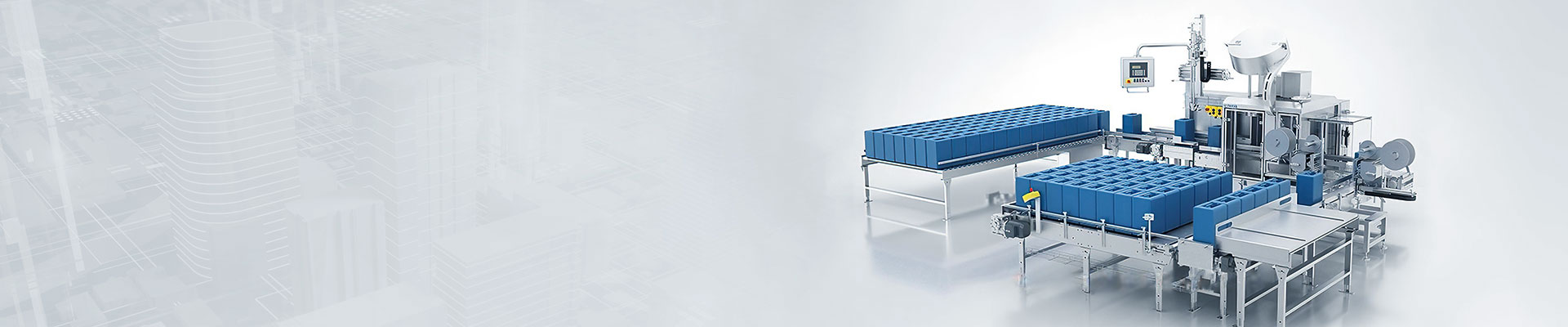
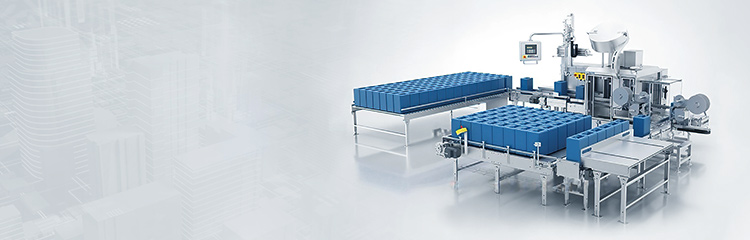
The dosage system and weighing instrument realize serial communication based on the development environment. The data from the weighing instrument is sent to the host computer in real time through the serial port, and the read data is intercepted and converted, and the weighing data can be displayed in real time on the operation screen, and at the same time, the weighing data can be stored in the database for querying and tracing the data, which is not only convenient to supervise the weighing process, but also to restrain the worker's operation. The upper computer software of automatic dosage system is designed with PLC program. The WINDOWS-based upper computer software has the functions of real-time process monitoring, overweight/overtime alarm, alarm processing, automatic data saving, querying historical data, printing formula and historical data. The feeding system adopts the rotating feeding basket installed on the screw to receive the materials, which effectively solves the problem that the feeding time in the whole production time accounts for too large a proportion in the dosing program of the lined-up dosing system. The weighing terminal from the signal to rotate to the receiving position is only 2 baskets apart, which is much faster than the receiving speed, and is conducive to improving the efficiency of the entire system. Sequential pick-up method, so that each recipe of small materials in a set order of cascade, so that the process personnel can easily identify the weighing of small materials and troubleshooting in parallel. The dosage weighing device adopts silo screw machine, the material flows to the mixer through the silo, each mixer has two weighing modules, and connected to the junction box, a speed weighing module, the signals through the junction box to the weighing instrument, and then by the dosage weighing instrument will be analog signals and pulse signals to the PLC, PLC processing output signals to the computer to monitor the operation of the PLC will be the computer commands to the weighing instrument for processing. The PLC will transmit the commands from the computer to the weighing instrument for processing. Batching scales and electrical interlocking, can be set from the computer flow, control to the dosage of dosage scales, can be switched through the "switch" button to switch the control, the frequency of dosage is the computer through the PLC to the frequency converter communication to control the output of the frequency converter, so as to change the rotational speed of the silo screw, in accordance with the required amount of dosage of dosage scales. The weighing flow setting at the weighing terminal is set by calculating the required value and outputting it to the PLC, then inputting it to the dosage weighing instrument and adjusting the frequency of the silo screw machine after PID calculation in order to achieve the required amount of material to be discharged.

The upper computer software of automatic Dosage system is designed with PLC program. The windows-based upper computer software has the functions of real-time process monitoring, overweight/overtime alarm, alarm processing, automatic data saving, querying historical data, printing formula and historical data.
The feeding system adopts the rotating feeding basket installed on the screw to receive the materials, which effectively solves the problem that the feeding time in the whole production time accounts for too large a proportion in the dosing program of the lined-up dosing system. The weighing terminal from the signal to rotate to the receiving position is only 2 baskets apart, which is much faster than the receiving speed, and is conducive to improving the efficiency of the entire system. Sequential pick-up method, so that each recipe of small materials in a set order of cascade, so that the process personnel can easily identify the weighing of small materials and troubleshooting in parallel.
The dosage weighing device adopts silo screw machine, the material flows to the mixer through the silo, each mixer has two Weighing modules, and connected to the junction box, a speed weighing module, the signals through the junction box to the weighing instrument, and then by the dosage weighing instrument will be analog signals and pulse signals to the PLC, PLC processing output signals to the computer to monitor the operation of the PLC will be the computer commands to the weighing instrument for processing. The PLC will transmit the commands from the computer to the weighing instrument for processing.
Batching scales and electrical interlocking, can be set from the computer flow, control to the dosage of dosage scales, can be switched through the "switch" button to switch the control, the frequency of dosage is the computer through the PLC to the frequency converter communication to control the output of the frequency converter, so as to change the rotational speed of the silo screw, in accordance with the required amount of dosage of dosage scales. The weighing flow setting at the weighing terminal is set by calculating the required value and outputting it to the PLC, then inputting it to the dosage weighing instrument and adjusting the frequency of the silo screw machine after PID calculation in order to achieve the required amount of material to be discharged.