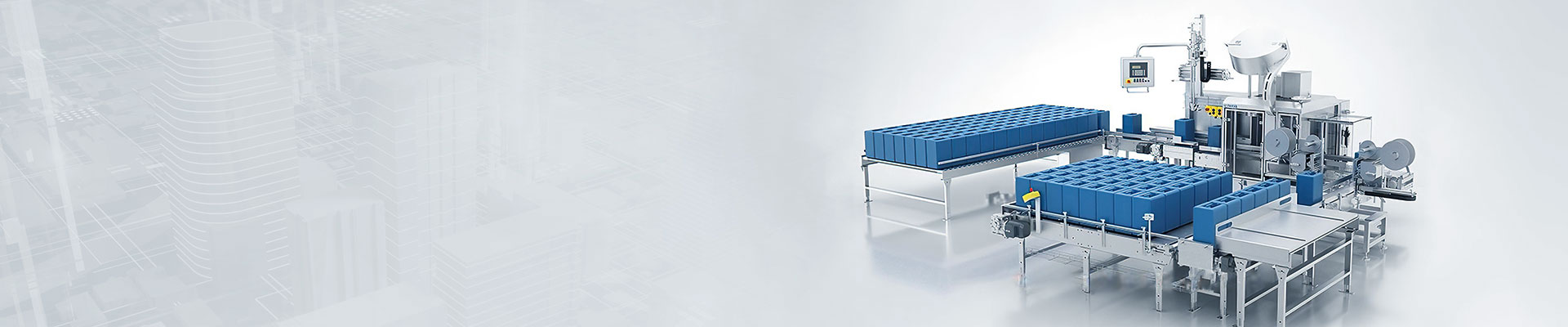
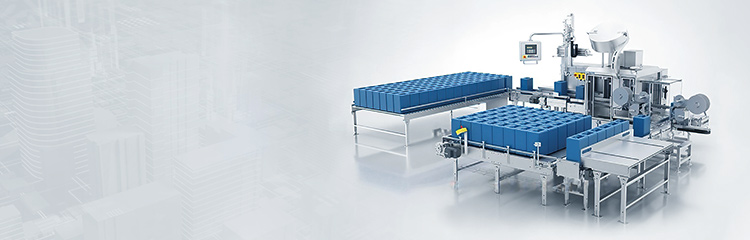
The reactor control system controls the dosing according to A certain proportion, at the same time gives the feeding system according to the material level information of each reaction tank, sets the relationship between the ratio of raw materials and the arrangement sequence of the total feed quantity meter, sets the weight of the equipment under each reaction tank through the communication of the upper computer, and sends the weight signal and speed signal to the weighing instrument after the weighing system is started. Instantaneous flow and accumulation are calculated and displayed in the field weighing instrument. Self-tuning operation is carried out according to the parameters set by the user. If there is a deviation between the set value and the current value, the PLC analog module will adjust according to the need.

Weighing of reaction kettle is a very important process in the production process of fine chemical enterprises, which consists of Weighing system. The dosage machine is under the control of the general control microcomputer system, and the liquid raw materials are put into the reaction kettle and stirred to form the formula raw materials. Mainly complete the weighing of the main material and various ingredients, proportioning, mixing and blending of ingredients, and then grouped and categorized filling. It realizes the measurement of symmetrical weighing and filling.
The dosing system adopts DCS centralized control mode, and selects Siemens S7300 PLC to constitute the data acquisition and control system, which is modularized design and economical and practical. The human-machine interface monitoring software adopts the leading configuration software "Configuration King" in the field of industrial control in China, which has the advantages of good openness, easy maintenance and secondary development. All process control data and equipment operation status of the system can be centrally managed, recorded in real time, and printed and consulted at any time, which consists of computer, cabinet and peripheral equipments (weighing kettle, pneumatic control valves, conveying pumps, etc.).
The dosage control system consists of a computer as the human-machine interface of the whole system, which is set as the master station to complete all the system parameter setting, process monitoring and data recording; another weighing touch control instrument is set as the slave station, which takes the master station as the backing, and is in charge of the data setting and process monitoring of the post-dosage dosage. The master station communicates directly with Siemens S7300 PLC system and automatic touch control instrument. Sealed junction box is adopted on site, which is dustproof and moisture-proof and ensures reliable signal transmission. Adopt special industrial process touch control instrument, through the RS-485 bus and the central control room to realize communication, both independent control, but also can realize PLC on-line control of each valve position and unloader position signal detection, the use of load cells, with no contact, anti-interference, anti-dust, moisture-resistant characteristics. The silo level adopts heavy hammer type material level meter, which can realize the continuous silo level detection.
The automatic Dosage system has the functions of human-computer interaction, communication, display and storage, printing, etc. It also has data and graphic display, status monitoring, data input, information storage and other function screens related to operation. It can realize real-time process data monitoring, simulation display of process flow, real-time data record checking, system operator authority setting, process parameter setting, setting alarm of running process events and switching between manual and automatic control. Field control instrument real-time display of flow, load, totalized value, temperature, etc.. Temperature indication through the field temperature display instrument, pressure indication through the field pressure display instrument and motor current through the field display instrument is transmitted to the centralized display in the control room. The frequency converter regulation is equipped with automatic switching switch and communicates with the main control computer.