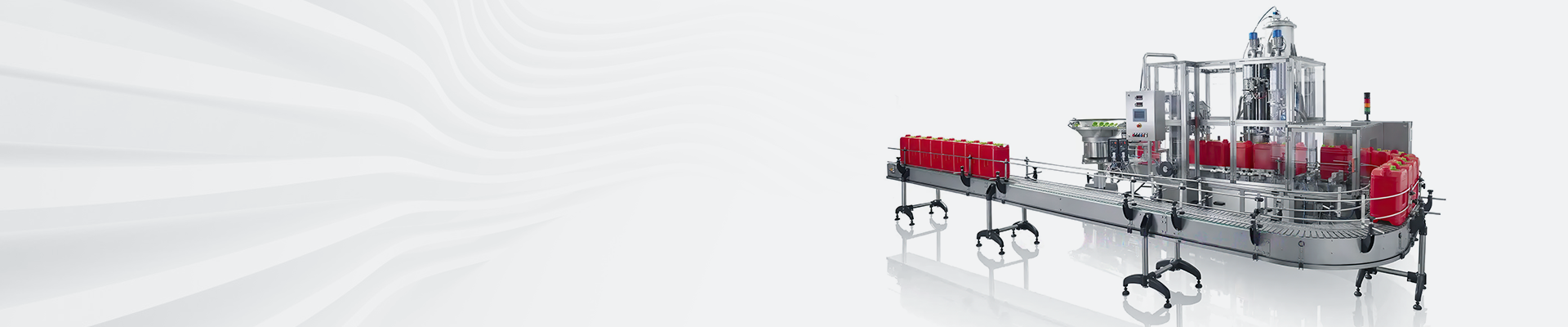
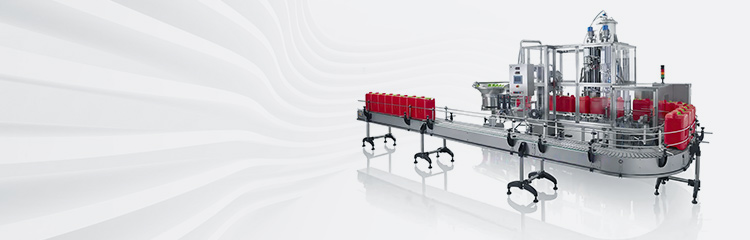

Summary:The weighing mixer adopts a PLC-based distributed control system as the overall control plan. The main links of feed production are analyzed and a control plan is given.A batching mixing control system based on PLC was designed, the system hardware design and software control process were given, and the fuzzy PID control of the batching system was studied.
Feed industry is an extremely important key link in the agricultural industry chain connecting planting, breeding and agricultural by-product processing industry. As one of the emerging industries of the world economy, it has developed rapidly in a relatively short period of time, and has been highly valued by governments and businesses feed processing production line control is mainly characterized by sequential control of processing equipment and testing devices, and this sequential control is where the advantages of PLC control.PLC control is the current industrial process control is very widely used in the control mode, the use of PLC control can greatly improve the degree of automation of production. PLC control can greatly improve the degree of automation of production. Programmable controllers and PC communication with the host computer to achieve the overall optimization of the production process to ensure normal production and management level.
1 feed production process
Mixing system generally includes the receipt and cleaning of raw materials, crushing, batching, mixing, granulation, finished product packaging and storage and dust removal and fire and other systems, each production link is an independent production section.
2 PLC-based overall control program design
Each system in the weighing and mixing machine is relatively independent, the automation of feed production, including the automatic control of the entire system and the automatic control of each process and the automatic control of individual equipment.
Among them, PLC is responsible for controlling the operation of field equipment and obtaining its operating status and fault information, sensing system to collect field information data computer using network communication to obtain data for storage and management, dynamic display of the process, equipment operating status, production data, alarm information, and generate various types of production reports. Its core control component PLC, the use of modular programming ideas, separation of subsystems and relatively independent of the internal functions, and the functional blocks in accordance with the feed production system process flow through together to form the entire system of centralized control, and through the network to achieve the production management and remote monitoring command system.
3 dosage mixing system design
3.1 Dosing and mixing process program selection and control system determination
The dosing process is a key link in the feed production process, and its dosing accuracy directly affects the quality of feed products. Mixing feeding system to realize the two or more materials according to a certain ratio of automatic quantitative added to the mixer, after mixing to meet the predetermined requirements of the process of automatic discharge.
Through the comparison of the advantages and disadvantages of common dosage mixing technology program, choose the multi-material weighing mixing technology show. That is, all the measured material according to its physical properties or weighing range for grouping, each group with the corresponding measuring device to achieve the measurement operation, so as to economically and accurately complete the entire dosage process.
Multi-feed hopper weighing mixing process can significantly shorten the mixing time of the feed, significantly increase the output, combined with the feed production situation, the mixing process is selected as a multi-feed double weighing simultaneous dosage process.
The automatic feed batching system consists of PC, PLC, feeder, hopper, weighing module and actuator.
The operation process of the system is that the raw material formula data are first transmitted from the upper computer to the lower PLC, and then controlled by the PLC[. Various kinds of feed ingredients are distributed into the corresponding batching silo for storage through the top of silo conveying equipment and distributor. The ingredients are fed to the hopper scale by the feeder in sequence respectively during dosing. Raw materials with large ratios (>20%) are sent to the large hopper scale; raw materials with small ratios (5%-20%) are sent to the small hopper scale for weighing. The weighing module detects the quantity of each material and transmits the signal to the weighing controller to control the feeding of the feeder, thus controlling the dosing of each material. When all the materials in the silo are weighed and dosed according to the set recipe requirements and reach the specified cumulative quality (quantity of each batch), the PLC opens the material door according to the control program and puts the materials in the hopper scale into the mixing chamber of the feeder for stirring and mixing. Mixing machine to achieve a predetermined mixing time, that is, the mixing uniformity to meet the requirements, under the control of the PLC, the material door opens out of the material, send the material to the buffer bin, fall into the finished product scraper-type conveyor, sent to the entrance of the bucket elevator lift to the mixing silo storage, to the next process.
3.2 Hardware design of dosage mixing system
The upper computer selects a brand-name machine with standard RS232C communication white, printer interface, this system requires high control accuracy, according to the number of input and output signals, the lower computer selects a Mitsubishi FX~-80MR PLC and two FXN-16EX expansion unit, and selects SC-09 programming cable as the connecting line of the computer and PLC communication. In the whole feeding system, the load cell is a very critical component, how accurate it is, directly affects the accuracy of the system's dosage. This system selects resistance strain type weight sensor, its accuracy meets the requirement of dosage, it should be one level higher than the dosage accuracy.XSB-A type weighing display and control instrument is a kind of multi-purpose instrument, with fast speed and high accuracy, it owns a lot of special performance which is very suitable for the application of weighing display and control.
3.3 Software design of batching and mixing system
The computer transmits the corresponding formula and production process parameters to PLC according to the production process, PLC controls the frequency converter to start the batching winch according to the formula parameters and the feeding order, and the weighing signal is detected by PLC.
Feeding system working sequence: after weighing is completed, when there is material in the feeder, the hopper scale door is closed; when the feeder discharges and closes the door in place, the hopper scale door opens. After the hopper scale door opening time arrives, the residual material on the hopper scale will be detected, when the residual material exceeds the limit value, the system will alarm and the hopper scale door will not be closed when it is lower than the limit value, the hopper scale door will be closed. When the hopper door closes in place, if the scheduled batch is not completed, the dosage continues and a signal is sent to add premix and grease. After the premix is added and the answer reset is completed, the doser starts the mixing timer and after the mixing time is reached, the mixer opens the door to discharge the material according to the material level in the buffer hopper. The dosage machine will open the door and the door will be closed automatically when the door opening time is reached. After the next batch of material is dropped, a new round of cycle will be started. This system adopts modular program design method, whose central idea is to divide a complex application program into several relatively independent program modules according to the overall function. This control system, according to the program to complete the function is mainly divided into three program modules:
(1) Feeding and weighing module completes the raw material discharging as well as weighing signal acquisition from each bin according to the recipe parameters and feeding sequence to ensure that each raw material is within the tolerance range. After the feeding stops, from the screw feeder to the hopper scale, there is still a part of the raw material to fall into the hopper scale, we need to take this part of the material into account, the program with the "retention" on behalf of this value. Retention is based on the enterprise production experience data, through the test to select the optimal value to determine.
The frequency converter is set to multi-speed frequency, and the frequency converter is controlled by the output point of PLC. When the feeder is dosing, PLC controls the feeder motor to run in the high-speed section of the frequency converter, and when the amount of raw material is approaching (feeding amount - retention amount), the feeder motor is controlled by the PLC output point to run in the low-speed section of the frequency converter for slow dosing. Feeding process, PLC will be the amount of raw materials and (feed amount - retention) real-time comparison, within the tolerance for qualified, stop feeding; close to the lower limit of the tolerance, should be carried out inverter low-speed section of the feeding; greater than the upper limit of the tolerance for the overdifference, the alarm.
(2) Weighing door metering module controls the weighing bin door to open and close in logical sequence, so that the current batch of dosage is completed successfully.
(3) Mixer door module realizes the logic control of buffer bin door and mixing door, so that the dosage will complete mixing and stirring according to the set time.
In the program design, the whole program is divided into several functional modules to realize separately, and the PLC works through the main program to call each subroutine to complete the corresponding function respectively.
Fuzzy control of dosage system
Due to the changes of process parameters, material properties, fallout, etc., the model of dosage system has non-linearity and time-varying nature. In order to improve the influence of fallout and other factors on the accuracy, the prediction of fallout and the approximate control of batching quantity can be used to improve the batching accuracy. According to the characteristics of repeated batch weighing in feed mills, fuzzy adaptive compensation control of spatial material quantity using a large number of existing weighing error data can ensure that the material error fluctuates within the minimum range.
4 Control principle of fuzzy PID
The dosing controller receives the control flow data from the host computer as a given, compares it with the actual detected flow, and through the fuzzy PID control method, calculates the corresponding output (0~5V voltage or 4~20mA current) to control the frequency converter, so as to control the rotational speed of the motor, and make the flow of the dosed raw materials reach the given value.
5 Conclusion
The application of PLC technology to the traditional feed production line modernization technology transformation research, the development of the overall control program, combined with weighing module technology, communication technology and fuzzy control technology and other related knowledge, theoretical research and practical demonstration, designed a set of PLC as the core of the control, by the PC and PLC composed of the upper and lower computer of the control system. Practice has proved that the system runs reliably, the accuracy basically meets the requirements, and fully adapts to the requirements of modernized production management of enterprises.