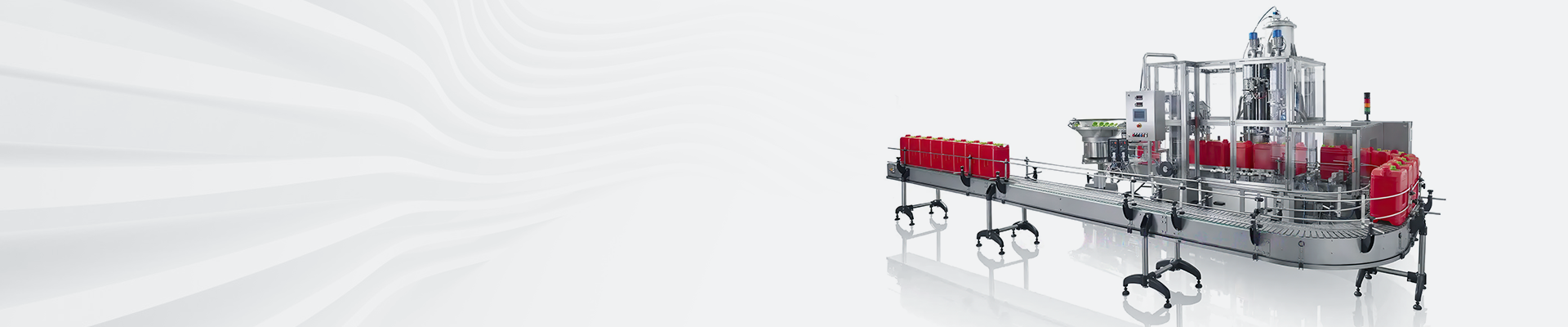
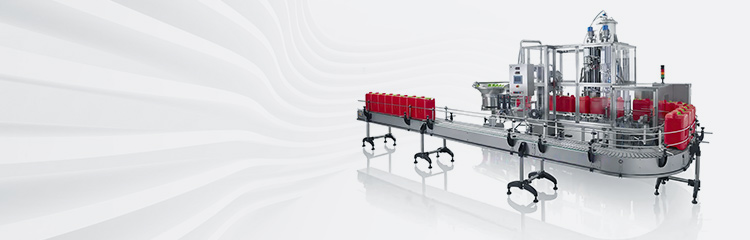

Summary:The control scheme and implementation method of the automatic vacuum filling and fine coating system based on ccink bus communication. The automatic filling system uses the high-precision weighing module and the interrupt function of the PLC to realize online precise liquid spraying and complete the dynamic and accurate output of the material weight, including The sensing, spraying, calculation and compensation links were included, and a preliminary analysis was conducted on the rapid response and energy saving issues of the related vacuum system.
1. Introduction
Automatic vacuum fine coating filling system consists of two parts, namely: vacuum feeding system, carrier filling fine coating and moving system. These two parts of the equipment is independent of each other, electronic control and drive equipment is far away from each other, in the logic of the two separate devices can be used as separate control; but all the equipment and to work together, communication. Therefore, the cclink bus communication is used to signal the decentralized system to realize the coordinated control of the whole system.
2.System realization
The general purpose of the fine coating vacuum automatic filling system is to realize the catalyst coating of the automobile exhaust gas filter core, and the control difficulty of the system is the fast production beat as well as the high precision of the control of the catalyst coating thickness. The whole system can be subdivided into vacuum supply system and carrier filling and moving system.
2.1 Vacuum supply system
The vacuum supply system consists of a 250L reserve vacuum tank and two 90L on-site vacuum tanks, the power drive consists of two Siemens MX440 inverters and two B0SCH vacuum pumps, the controller adopts Mitsubishi FX2N PLC, the vacuum detecting parts are vacuum detecting sensors set in the reserve vacuum tank and the on-site vacuum tanks, and the opening or closing of the vacuum pipes is realized by the PLC controlling the pneumatic ball valves. The opening or closing of vacuum pipeline is realized by PLC controlling pneumatic ball valve.
The vacuum storage equipment consists of a vacuum reserve tank and a local vacuum tank to realize the physical reserve and deployment of vacuum. When the vacuum level of the local vacuum tank is insufficient, the corresponding ball valve opens, and the vacuum reserve tank is connected with the local vacuum tank, which realizes the quick replenishment of the vacuum level of the local vacuum tank. The size of vacuum directly affects the quality of the product, if the vacuum negative pressure is insufficient, the catalyst coating layer will be too thin resulting in scrap, so we should try to ensure that the vacuum of the reserve vacuum tank is high in order to effectively replenish the vacuum of the local vacuum tank at any time; however, when the vacuum of the reserve vacuum tank is large enough to reach a certain value, the high speed of the vacuum pump can no longer make the vacuum effectively reduced, but the increase in energy consumption is obvious, from the perspective of energy efficiency. From the point of view of energy efficiency, when the vacuum degree reaches 0.1 times the atmospheric pressure, one vacuum pump should be stopped, and only one standing vacuum pump should be kept for low-frequency operation; when the vacuum degree of the reserve vacuum tank suddenly decreases, the vacuum pump running at low frequency should be increased and the stopped standby vacuum pump should be started.
Every time the system starts, the operator needs to select the standing vacuum pump, and the starting and stopping of the standby vacuum pump is completely controlled by the program.
2.2 Carrier filling and moving system
The Carrier Filling and Moving System realizes the work station flow and filling and coating of carriers. Each carrier needs to go through five processing stations: loading station, empty carrier weighing module station, filling and coating station, secondary dosing module station, and discharging station. In order to achieve a high beat rate, each set of processing stations is a duplex station, i.e., each set of stations processes two workpieces at the same time. The movement of the carrier between each group of stations is synchronized by a circular carousel, which is transferred to the next group of stations immediately after each group of stations has been processed.
2.2.1 Feeding station
The feeding station is loaded by a robot. When the turntable allows loading, it sends the loading permission to the robot; when the robot finishes loading, it sends the loading completion signal to the turntable. In order to realize accurate and safe control, there is a diffuse reflection sensor on the turntable to detect the presence or absence of the carrier, the signal sent by the robot must be the same as the signal detected by the sensor before the system considers the feeding complete; otherwise, the system alarms.
2.2.2 Empty carrier electronic weighing station
The turntable rotates to transfer the empty carrier to the empty carrier weighing module station. After the system detects the workpiece in place by diffuse reflection sensor, it controls the electronic scale to lift the workpiece up to a certain height to measure the weight and store it in the PLC register. After weighing, the carrier is still put back to the rotary disk to be weighed.
2.2.3 Filling and coating station
The carousel rotates and moves the empty carrier to the filling station. After the system detects the workpiece in place by diffuse reflection sensor, it controls the lifting device to lift the workpiece to the mouth of the filling machine, and the vacuum funnel at the end of the vacuum system is synchronized with the lifting and fitting with the carrier: after all the actions are completed, the automatic filling machine's discharge port opens, and the vacuum system's ball valves 3# and 4# open, and the catalyst to be filled is pumped into the carrier by the vacuum funnel.
2.2.4 Secondary weighing station
The turntable rotates to move the filled carrier to the secondary electronic weighing station. After the system detects the workpiece in place via diffuse sensors, it controls the electronic scale to lift the workpiece, measure the weight of the filled carrier, and compare it with the original weight recorded in a register to determine the weight of the filled catalyst and to determine if the filling job is qualified. The pass of the product is stored in a register for production statistics and sent to the unloading robot for determining the unloading path. After weighing, the carriers remain in the weighing position on the rotary disk.
2.2.5 Unloading station
The carousel rotates and moves the filled carriers to the unloading station. After the system detects the workpiece in place by diffuse reflection sensor, it sends a discharging signal to the discharging robot; the discharging robot determines the discharging path of the workpiece according to the discharging signal as well as the qualified and unqualified signals, and then sends the qualified products to the next process, and the unqualified products are sent to the discharging roller conveyor.
2.3 Cclink communication connection
The vacuum supply system is far away from the carrier filling fine coating and moving system, and the operator works beside the carrier auto-filling machine, so it is necessary to monitor the vacuum supply system remotely. In order to simplify the site wiring and future maintenance and to realize convenient operation, a Cclink communication network was set up on site; the master station of the Cclink communication is the vacuum supply system, and the slaves are the carrier filling and coating and mobile systems; the slaves are connected to the human-machine interface, which can be used to set up and monitor the slaves themselves as well as the master station.
3.Conclusion
This paper describes the realization of a vacuum filling and coating system. The system has a simple communication structure, and the monitoring and setting of all the information of the whole system can be realized at one operating station, which is convenient for operation. Through the reasonable starting and stopping of the two vacuum pumps of the vacuum supply system and the frequency conversion setting, energy saving can be achieved under the premise of realizing the rapid replenishment of the vacuum degree.