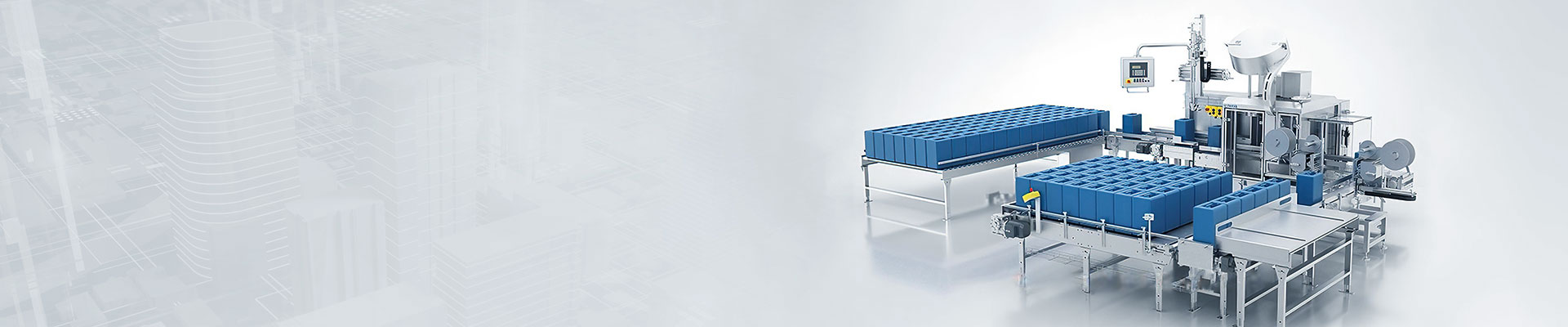
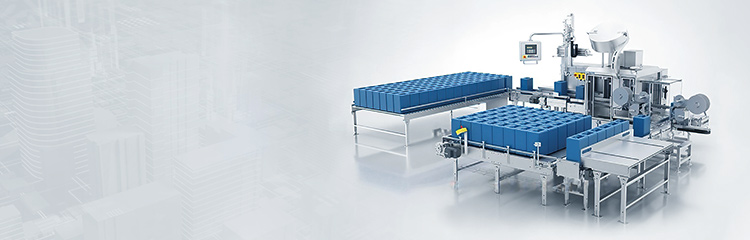
Weighing and mixing system integrates automatic control technology, computer technology and communication technology as a whole, with advanced technology, complete functions, the control unit is mainly a touch screen, PLC as an auxiliary control system, the man-machine interface displays the proportioning parameters (formula) and monitoring and recording of real-time data. According to the weighing fast and slow with an advance amount, when the detection of the weight to reach the set value, will subtract the advance amount, the control instrument will close the feed valve. The amount of advance can be corrected manually or automatically, so that the control reaches the set target value for each dosage accuracy.

Weighing and mixing system has the advantages of short process flow, high weighing accuracy, high reliability, highly flexible equipment layout, and greatly reduced plant height than the traditional powder Weighing system. According to the different positions of the weighing equipment in the powder vacuum weighing system, a variety of additive scales and subtractive scales can be composed to meet the different requirements of customers.
Mixing scale consists of feeding station or material storage bin, vacuum doser weighing device, PLC controller and other components, which can complete the automatic feeding and dosing of single material fixed weight dosing or multiple materials with different formula dosing. Widely used in medicine, food, chemical, battery materials, building materials, metallurgy, feed processing and other industries.
Powder mixer applied to two materials automatic weighing and dosage as an example to illustrate the working principle of the powder vacuum weight-bearing system. Material A, B were stored in two bins, powder vacuum weighing system began to work, the vacuum pump start, material A bin bottom spiral discharge valve A to reach a certain weight, the spiral stops, the discharge valve A closed, the remaining materials in the pipeline continue to be sucked into the weighing hopper, sucked after the net weighing of the material in the scale A weight is exactly the weight of the set. At this time, the screw discharge valve B at the bottom of the material B bin opens, the screw starts, the material B is sucked into the weighing hopper, when the material B in the scale reaches a certain weight, the screw stops, the discharge valve B closes, and the remaining material in the conveying pipe continues to be sucked into the weighing hopper, and after sucking clean, the weight of the material B in the scale is exactly the set weight. The vacuum pump stops.
The weighing control system has the advantages of short process flow, high weighing accuracy, high reliability, highly flexible equipment layout and greatly reduced plant height than the traditional powder weighing and feeding system. According to the different positions of the weighing device in the powder vacuum weighing system, a variety of additive scales and subtractive scales can be composed to meet the different requirements of customers.
Product Features:
The weighing system adopts computerized full-automatic control with high precision and speed without guarding;
Centralized control system is convenient and reliable, with intuitive display and fault alarm system.
Can be equipped with a printer to print the shift output and related data;
All pneumatic components are imported ingredients to ensure reliable operation of the system;
Maintenance and convenient, small footprint
Technical parameters:
Automatic dosing 3~4 kinds of materials per hour output of 10T~15T/hour, dosing accuracy ≤ 0.5%.
Automatic packaging scale hourly packaging output: 12~15T/hour, packaging accuracy: 0.2%.
Power supply voltage: 380V 50HZ; power consumption: 3KW/hour
Gas source: 0.5Mpa Gas consumption: 0.6m3/hour