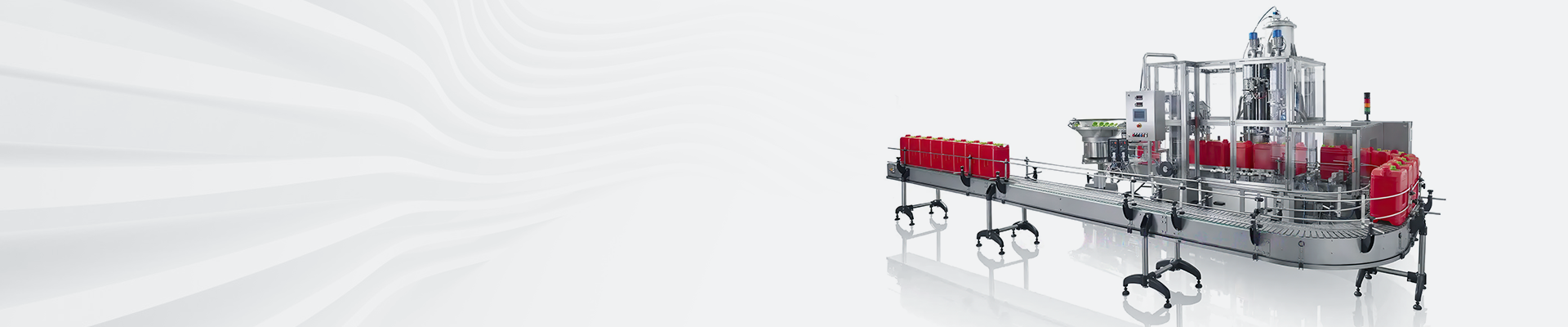
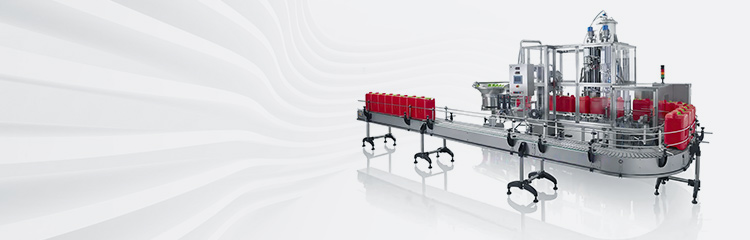

Summary:The batching system adopts a composite control of weight proportional feedforward control and fuzzy self-tuning PID cascade control. The frequency converter is used to control the driving motor speed of the metering pump, thereby adjusting the dosage of the metering pump, realizing automatic batching, and completing the coordination with the monitoring center. Various communication functions.
Paint is an important process in paint treatment, the automatic dosing system determines the operation effect of the subsequent process and the quality of the final factory paint. The effect of paint mainly depends on the accuracy of the paint dosage. As the paint process itself is a complex physical and chemical process, it is difficult to accurately establish a mathematical model of the reaction process, which brings difficulties to determine the paint dosage online. Automatic dosage system is the basic liquid arrives at the most basic and main process ring of the paint manufacturing process. Correct weighing and dosage, as required by the process recipe, is the basis for ensuring that the required amount of liquid control is available for the production of paints. If the liquid control volume is not up to standard, or if there are unavoidable small deviations in each metering placement, the deviations must be controlled within acceptable limits or the performance of the final product will be affected. The use of existing industrial electronic scales or general metering is prone to deviation metering due to the presence of the human factor, the poor repeatability and accuracy of metering, and the difficulty of open manual operation to ensure good process hygiene. Therefore, the operation mode of automatic liquid supply and weighing and mixing dosage is the best way. In recent years the production technology of the paint industry has been improved and updated. With the introduction of the Paint Safety Act, the requirements for paint safety have also increased. The working mode of automatic weighing and mixing and dosing is gradually applied and popularized.
1 weighing and dosing working principle
Batching system mainly consists of data collection equipment mainly engaged in electrical automation, weighing instruments, variable execution equipment and other components. Data acquisition equipment mainly includes weighing module, flow current detector and turbidity meter and other instruments and meters, and the analog signals collected by them are processed and sent to the corresponding weighing instruments. Each weighing instrument executes the corresponding control algorithm to get the control quantity, and this control quantity is controlled by the variable execution equipment metering pump to control the paint. Liquid supply weighing and mixing batching system consists of storage reaction tank, material supply system, mixing equipment, conveying equipment and control system. Main functions: reception and storage of liquids (in bulk or in iron drums), distribution and mixing of different liquids and deposited liquids, distribution to intermittent or continuous weighing and batching tanks. It is suitable for the mass production of coating companies that need liquids. This batching equipment produces metering and high efficiency, solves the heavy physical labor of customers carrying liquids manually, saves labor, solves the deviation of liquids in the carrying process and the waste of residual liquids in the opening process, saves the storage of the reaction tanks, uses the space reasonably, and sets up the saving point and the use point flexibly. The automatic dosage machine is controlled by programmable controller, which can continuously store, use and dispense liquid without manual control. It adopts the compound control strategy of weight-proportional feed-forward control and cascade control. The metering pump with double adjustment of frequency and stroke is selected, and its precise control principle of mixing volume is as follows.
①Cascade control loop: the turbidity control loop of the sedimentation tank is the main loop, and the flow current closed-loop control loop is the secondary loop. The flow current closed-loop control loop is the main control means. That is, on-line monitoring of the flow current value of the original paint after mixing (SCD) - and & potential positively related to the essence of the paint parameters, only this parameter can accurately determine whether the mixing amount is appropriate, so that the amount of mixing can be adjusted within a few minutes.
②Weight Proportion Feedforward Control Loop: In order to improve the response speed of the metering pump when the weight of the original paint changes drastically, a weight proportion feedforward control loop has been added. The specific realization method is to set up a weighing module in the original paint dosing equipment, which is used to obtain the weight of the original paint, and adjust the stroke length of the metering pump by changing the proportion coefficient of the stroke regulator, so that the response time is greatly shortened to only a few seconds.
2 dosage hardware design
The dosage of the lower computer using the S7-200 series, CPU model 224XP, making full use of the weighing instrument signal acquisition, A/D conversion, fuzzy control program execution, control signals sent, communication and other functions of the paint weighing and dosage for automatic control.
The PLC collects manual/automatic push-button switch signals via digital input module EM221 (8 digital inputs, input voltage rated at 24VDC) and decides whether to execute the automatic control program. Analog input module EM231 (4-channel analog input, range 0 ~ 20mA, resolution of 12 bits) to collect the module output 4 ~ 20mA current signal, the output control signal sent to the positional servo mechanism, so as to adjust the length of the stroke, so that it is in the range of 0 ~ 100% of the change; EM231 to collect the turbidimeter and the flow of current detector output of the 4 ~ 20mA standard current EM231 collects the 4~20mA standard current signal output from turbidity meter and flow current detector, and transmits the standard current signal to CPU to execute the serial control program. The calculated control signal is controlled by the analog output module EM232 (2-channel analog output, range. ~20mA, with 11-bit resolution at full scale) outputs 4~20mA current signals, the
The upper computer is mainly used to monitor the paint dosage and to provide corresponding parameters for the manager to adjust the specific state of the controlled object. Considering the economy, the upper computer uses ordinary PC and inserts the MPI communication card into its PCI slot, connects the PLC and the communication card with the MPI cable and adopts the MPI protocol to realize the communication between the PLC and the upper computer with the transmission rate of 187.5kbit/s. The upper computer can be connected to the PLC by the MPI cable, which can realize the communication between the PLC and the upper computer with the MPI protocol, the transmission rate of 187.5kbit/s.
3 dosage software design
3.1 Control algorithm design
The batching control system consists of computer, cabinet and peripheral equipment (front batching scale, rear batching scale, material level machine). The dosage monitoring system consists of two computers as the human-machine interface of the whole system. One of them is the master station, which accomplishes all the system parameters setting, process monitoring and data recording; the other one is the slave station, which takes the master station as the basis and is in charge of the data setting and process monitoring of the post-batching system. The master station communicates directly with the Siemens S7300 PLC system, the front dosage scale and the rear dosage scale. The front dosage control system adopts sealed junction box, which is dust-proof and moisture-proof, and can ensure reliable signal transmission. The former dosage scale adopts special industrial process controller, which communicates with the central control room through RS-485 bus, and can be controlled independently or realized PLC on-line control. With the purpose of adjusting the stroke of the metering pump proportionally to the weight, since the stroke is proportional to the weight of the original paint, the PID series control program is adopted. In order to improve the dynamic performance and anti-interference ability due to changes in paint quality.
3.1.PID equipment
The automatic batching system adopts Siemens S7-400PLC as the lower computer. the PLC communicates with two EM200 sub-stations and 12 sets of Siemens MM440 inverters to collect and process the field data and simple control. the PLC communicates with the upper computer using CP443 Ethernet module to exchange the system operation data.
The configuration system uses configuration dosage to design the following configuration interfaces: home cover, login interface, equipment operation interface, dosage setting interface, recipe interface, real-time data interface, report interface, system diagnostic interface and so on.
Based on the self-tuning control rules of PID parameters, combined with the technical knowledge and experimental operation experience of the engineering designers, the table of conforming control rules is established.
Perform fuzzy inference and defuzzification steps. According to the designed fuzzy control rule table, apply the fuzzy inference synthesis rule to calculate the fuzzy control quantity.
3.1.2PID algorithm
PID adopts the incremental PID algorithm commonly used in engineering. PLC is the core of paint mixing and dosing, and the program design adopts a modular and functional structure, which is convenient for maintenance and expansion. The software is mainly composed of the following modules:
Initialization program, used to set the initial value of each register, counter, PLC working mode, communication mode and other parameters;
Fault detection subroutine, which automatically detects and alarms the faults of various valves, pumps and other power equipment; According to the acquisition subroutine, it collects analog data from various channels and carries out filtering, averaging and other processing;
ADC interrupt program, A/D conversion of the collected analog quantity;
Fuzzy self-tuning PID control subroutine, send the converted data to the fuzzy self-tuning PID control subroutine, and the calculated control quantity is sent to the PID weighing instrument as the setting value of the PID weighing instrument;
PID control subroutine, the calculated control quantity is used to control the rotating speed of the driving motor of metering pump through frequency converter, so as to regulate the dosage of metering pump and realize automatic painting;
Letter subroutine, to complete a variety of communication functions with the monitoring center.
3.3 Upper unit configuration software
This weighing and batching system adopts KINGVIEW 6.51 software development to monitor and control the paint process through KINGVIEW, and the control program and algorithm are configured on PC. The program is divided into five parts: main control interface, real-time curve display, historical curve survey, report output and weighing and batching system alarm. 3 levels of authority password settings are used, i.e. operator, technician and system administrator, to realize different levels of authority. The operator can control the starting and stopping of the equipment and use the software but cannot modify the parameters; the technician can modify the control parameters of the dosage; and the dosage administrator can modify all the dosage functions. the PLC program consists of three parts: the main program part, which is responsible for the selection of manual/automatic processing flow, the judgment of entering the subroutine of the level processing, the processing of displaying the alarm lamps and the control of the alarms in various fault states; two subroutines, which are responsible for the selection of the manual/automatic processing flow, the judgment of entering the subroutine of level processing, and the control of the alarm lamps in various fault states. cycle; there are two subroutines, which are liquid level processing and automatic operation. Among them, the liquid level processing subroutine is mainly responsible for judging the height of the liquid level in the reaction tank by comparing the collected liquid level information with the set value, and the liquid level signal will determine the opening and closing status of the material pump. When the collected input value exceeds the maximum set liquid level, the liquid level signal will determine the opening and closing status of the material pump.
4 Batching Simulation
According to the algorithm model established earlier, the dosage system was simulated using Simu-link and Fuzzy toolbox in Matlab and compared with conventional PID series control. At the beginning of the simulation, the weight of the original paint is 1500m'/h, and all the various control algorithms are able to stabilize the amount of paint at 350iyh after a certain adjustment time, but the performance of the dosage system has different advantages and disadvantages. From the simulation results, it can be seen that compared with the conventional PID series control and the fuzzy PID series control, the latter has a smaller overshoot and a shorter regulation time than the former. In the paint volume stabilization after a certain moment to change the weight of the original paint, in this selection of the beginning of the moment after the 300th s regulation of the weight of the original paint for 2570m3 / h, a variety of control algorithms after a different regulation time can still be made to stabilize the paint volume in the last 600I / h, the dosage regulating performance is also divided into advantages and disadvantages. From the simulation results, it can be seen that, compared with the feed-forward control without weight ratio and with weight ratio, the regulation time of the latter is obviously shortened, and the amount of paint can be adjusted in time with the change of the weight of the original paint. In order to prove the reliability of the above conclusions, the weight of the original paint is changed again after the paint quantity is stabilized, and the weight of the original paint is selected to be 1070m'/h in the 600s, and the various control algorithms can stabilize the paint quantity at 250I7h, which leads to the same conclusions in terms of the performance of dosage regulation.
5 Conclusion
The weighing and dosage system takes S7-200PLC as the core of processor and ordinary PC as the upper computer to realize the monitoring and parameter management of paint process. This not only realizes the automatic control function, but also has the functions of real-time monitoring, data analysis, printing reports and so on. The control algorithm adopts the composite control strategy of weight-proportional feedforward control and fuzzy self-tuning PID serial control, which plays the advantages of PID and fuzzy control as well as serial control, and combines the perturbation control and deviation control, and has the features of high control accuracy, strong adaptability and good robustness, which can be well adapted to the control requirements of the real production process. It is guaranteed that the turbidity of the ex-factory paint is controlled below 1NTU, the paint treatment effect is good, and the amount of mixing is saved, which achieves a good economic benefit.