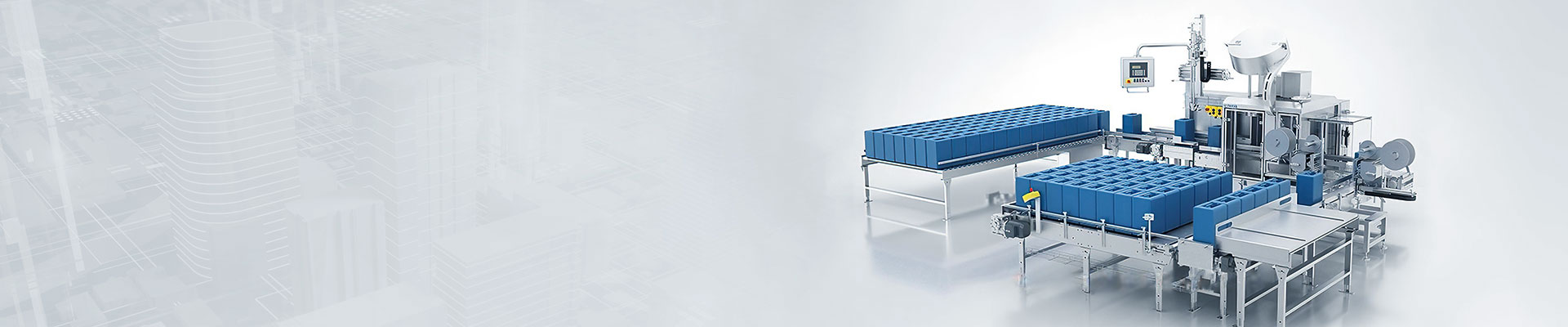
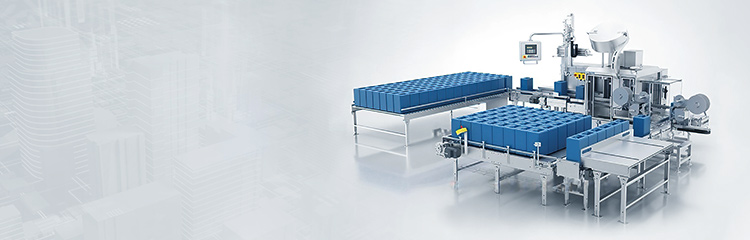
The automatic dosing machine is usually composed of a weighing module, a weighing body, a discharging mechanism, a feeding mechanism and a control system. The weighing module cooperates with the weighing transmitter, PLC and touch screen, and measures the weight through the weighing module under the scale frame to ensure the quality of raw materials on the silo. When the system is running, the weight data and speed signal received by the computer are converted into accumulated value and instantaneous flow after operation, and the data are transmitted to the work control machine, and the analog current signal is transmitted to the frequency conversion controller, and the frequency conversion machine properly sorts out the current, changes the rotation speed of the superior feeder, and then completes the calculation and configuration of raw materials.

Feeding system is a kind of production equipment which is used to automatically and accurately formulate different powder or liquid main materials and auxiliary materials according to a certain proportion in industry. It is usually composed of weighing control system, weighing instrument, PLC system and upper computer.
The automatic dosing machine consists of a variety of equipment, including raw material storage body, conveying body, weighing and batching body, dust removal body, material mixture and so on; According to the characteristics of the industry, the production process requirements and the specific material characteristics, the weighing methods such as "zero method" or "reduction method" can be reasonably selected, and there are various working modes such as single bucket, multiple buckets and multiple materials. The weight lost on the smaller surge hopper is bulk output, and the bulk bag polluter provides enough capacity to allow the main components to be transported at a lower rate and reloaded by the small-diameter flexible screw conveyor. In addition, that transportation by the weight-loss flexible screw conveyor is a secondary component, wherein the vacuum filter system equipped with manual dumping at any one or two dumping stations contain dust in the air. All flexible screw conveyors are discharged to a common shoulder-weight transition hopper, which is installed on a weighing sensor to confirm the accuracy of a batch of fed materials before passing through a rotating air lock to the above pneumatic pipeline.
Performance characteristics
1) The Batching system has the advantages of reliability, strong applicability, high weighing accuracy, high automation accuracy, stable quality and easy management.
2) Electronic weighing display design, high measurement accuracy, easy calibration and maintenance.
3) data processing: the batching system can automatically calculate and process the collected signals, thus automatically controlling the normal operation of the equipment.
4) Communication function, i.e. bidirectional data communication between industrial computer and PLC and instrument.
5) Monitoring function, which detects and monitors the instantaneous flow, daily accumulation, monthly accumulation, annual accumulation and other parameters in the batching process.
6) screen display, which can display the operation status of relevant control parameters in the batching process through computer monitor or weighing instrument.
7) Professional material handling ability, with the characteristics of raw materials measured by users, using various types of Feeders and inlet and outlet valves.
8) Friendly man-machine interface, which can be connected with various controllers to perform quantitative measurement or batching process control.
9) A variety of control modes can be selected, which can be controlled by PLC, man-machine interface, single chip microcomputer and industrial computer.
10) Rich experience in system integration, and all kinds of peripheral equipment can be planned and designed according to users' needs.
11) Reasonable site layout design can be configured according to the user's production and workshop environment.
System technical characteristics
1. System measurement accuracy: less than or equal to 1%
2. Static error: less than or equal to 0.5%
3. Dynamic cumulative error: less than or equal to 1%
4. Ambient temperature: instrument: -20℃ -50℃ Field equipment: -30℃ -60℃.
5. Relative humidity: 35%-80%