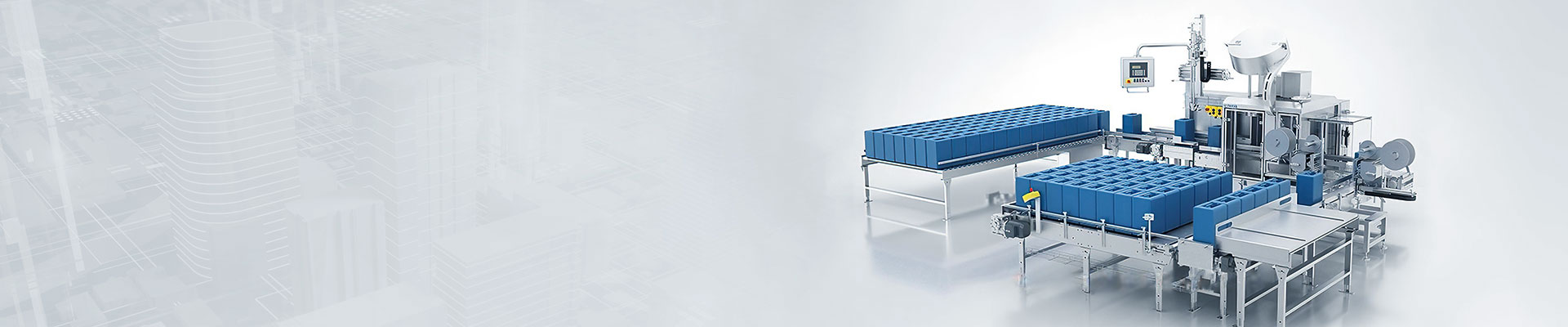
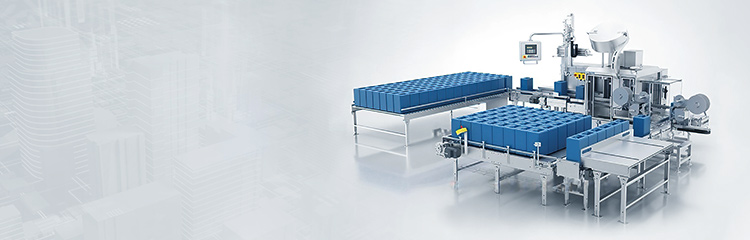
The batching production line consists of two computers as the human-machine interface of the whole system to complete all system parameter setting, process monitoring and data recording. The other one is the slave station, relying on the main station, responsible for the data setting and process monitoring of the post ingredients. The main station communicates directly with the Siemens S7-300 PLC system, the automatic control of the front proportioning and the balance of the rear proportioning. The front dosing control system adopts a sealed junction box on site, which is dustproof and moisture-proof to ensure reliable signal transmission and realize continuous location detection.

The weighing Feeder consists of a two-level computer control network composed of a programmable controller and a spiral scale, which is connected to the weighing instrument, control computer, PLC, frequency converter and other equipment with high intelligence and fast processing speed through the field bus. PLC mainly undertakes the system fault detection, display and alarm, and at the same time output signals to the inverter, the inverter completes the role of adjusting the speed of the screw machine. The screw conveyor weighs the instantaneous flow rate, and the upper computer gives the set flow rate. There is some deviation between the two in real-time measurement. The most widely used PID regulation in industrial control is used for actual flow control. According to the flow deviation, the control quantity is calculated by using proportion, integral and differential. The speed of spiral scale is adjusted by frequency converter, and the quantity is adjusted so that it is equal to the set value.
The feeding system is composed of silo (or tank, tank, etc.), support body, weighing module, weighing instrument and so on. The silo and the support body are the mechanical force transfer reset system between the weighed object and the conversion element, including the granary that accepts the load of the said object, the force transfer reset mechanism, the limiting device, etc., which are the main bearing components of the weighing type electronic material level meter and play the role of bearing the weight of the object. The silo and force transfer mechanism are responsible for accurately transferring the weight of the object to the metering module. The weighing module (primary instrument) is located between the silo and the support body, and converts the weight of the object to the corresponding millivolt electrical signal according to a certain functional relationship, which is output to the weighing control instrument (secondary instrument) through the junction box signal cable. After processing, the instrument directly displays the weight data of the object and converts the weight data into a standard signal of 4~20mA or 1~5V, or transmits it to the control terminal by RS-232, RS-485, Modbus/Profitbus/Hart. The weighing control instrument can also be preset at different weight values to achieve relay output to control the automatic addition and subtraction of materials.
The feeder hardware adopts Siemens S7300 series and ET200 modules, and adopts Siemens STEP7 series and WINCC series. According to the process requirements, the proportioning control is carried out in a certain proportion, and the feeding system is given according to the material level information of each material reaction tank. Ingredient control can be proportioned according to the weight and chemical composition of the raw material. The weight ratio is to control the screw and the feeding device under the raw material reaction tank. According to the flow rate of the weighing screw and the feeding device, the PLC sets the ratio and the total feeding amount of the raw material, and considers the relationship between the sequence of the raw material reaction tank. Through the communication of the upper computer, the flow rate of the equipment under each reaction tank is set. After the system is started, the weight signal and speed signal are sent to the secondary weighing instrument. By amplifying A/D conversion, the instantaneous flow rate and cumulative amount are calculated and displayed in the on-site weighing instrument. The weighing display transmits the signal to the PLC metering module. The PLC analog input module collects the weight signal and speed signal of the weighing screw and the feeding device, and performs self-tuning operation according to the parameters set by the user.