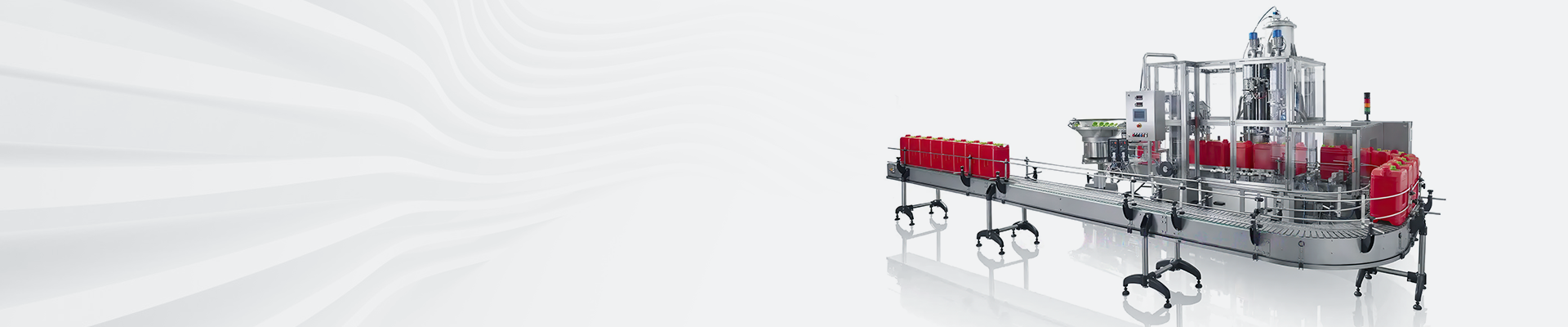
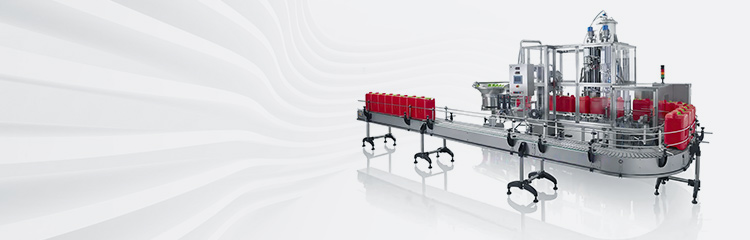

Summary:The flour multi-feed pneumatic conveying system is to realize the specific requirements of the material required to be stored for several days before the mixing process proposed by the enterprise through the multi-storage tank, and at the same time achieve the purpose of continuous feeding. The system greatly improves the degree of automation of the enterprise, but because the pneumatic system itself has the disadvantage of large energy consumption, if the system conveying process parameters are not designed properly, it will produce very high energy consumption. Therefore, from the perspective of economic benefits of enterprises, it is very important to study the energy consumption of the system. In order to rationally design the parameters of the pneumatic conveying system, this paper analyzes the effects of the mixture ratio of fuel and gas, the pneumatic conveying speed and the diameter of the pipeline on the energy consumption through orthogonal experimental design method, and concludes that the mixture ratio of fuel and gas and the pneumatic conveying speed have the most significant effects on the energy consumption. The influence of pipe diameter is relatively small, which provides a theoretical basis for further regression analysis of system energy consumption and optimization of process parameters.
Pneumatic conveying is a modern conveying method which is flexible, easy to operate, occupies less land, and has a good future. Like mechanical conveying, pneumatic conveying is a widely used material conveying method. These advantages meet the requirements of modern logistics engineering and material handling technology, and the transportation form is more mechanically perfect, so it is often used by the food processing department with its environmental protection, health, safety and other characteristics. However, pneumatic conveying is not a perfect conveying technology, in addition to some superior to the characteristics of mechanical conveying, the power required in the operation process is larger, more gas consumption, power consumption index is higher, and its consumption reduction problem is the focus of research in various countries. There are many factors affecting energy consumption, equipment structure, operating conditions, conveying process parameters, material characteristics, etc., all affect the change of energy consumption." In this paper, the energy consumption of the flour multi-feed pneumatic conveying system was studied, and the transport process parameters of the system were analyzed by orthogonal experimental design, and the primary and secondary relationships among the mixture ratio of fuel and gas, the pneumatic conveying speed and the diameter of the pipeline were found out.
1. Feed system design
When designing the material (flour) conveying system for food enterprises, in order to realize the specific requirements that flour needs a certain storage time and continuous feeding before the established processing technology (mixing) proposed by the enterprise, a set of multi-point feeding pneumatic conveyor is designed to store and feed flour through multiple storage tanks. During the feeding process, materials from multiple locations should be fed to a single fixed location. This is exactly in line with the advantages of suction (negative pressure) pneumatic conveying system, so the high pressure suction pneumatic conveying system is used, which is mainly composed of storage tank, feeder, feed pipe, bag filter, fan, ration tank, mixing tank and other components, the fan is located at the end of the system, when the fan is running, the material is sent to the bag filter, negative pressure is generated in the material conveying pipe. Each storage tank realizes alternating feeding of the system through the switch of the feeder. The whole operation process of the system is monitored by configuration software to achieve automatic control. As the pneumatic conveying itself has the problem of high energy consumption, this paper mainly studies the energy consumption of the system operation. Through orthogonal experimental design method, the main and secondary order of the influence of main conveying process parameters on energy consumption is analyzed, which provides a basis for further research on regression analysis and parameter optimization of system energy consumption, so as to better solve the problem of high energy consumption of the system, reduce energy consumption of enterprises and improve economic benefits.
2 Orthogonal experimental design
In the case of multi-factor and multi-level, in order to determine the importance of each factor and how to match each factor to achieve the best test index, it is necessary to carry out reasonable experimental design. Orthogonal test method is widely used in improving the yield and quality of products, reducing the consumption of raw materials and energy, improving the formulation of raw products and so on. In order to analyze the energy consumption of flour multi-feed pneumatic conveying system during operation, the key degree of its influence on energy consumption was found out.
2.1 Determination of influencing factors and factor levels
Based on the design of the flour feeding pneumatic conveying system, it can be seen that its energy consumption is reflected by the pressure loss of the pipeline, and the electric energy consumption of the fan mainly provides energy for the pressure loss of the system pipeline. Therefore, the system pressure loss is taken as an index to evaluate the energy consumption, and the three main factors affecting the pressure loss are as follows: The mixture ratio of fuel and gas, air conveying speed and pipe diameter are selected as the factors in the design of this experiment.
3 Analysis of energy consumption results and parameters
3.1 Energy consumption Results
In advance, a series of calculation methods required in the design process of the feeding system are created into a process parameter calculation tool only for this system. The input values in the tool are: mixture ratio of fuel and gas, conveying air speed, pipe diameter: the output value is: The pressure loss value of the whole system can be obtained by constantly changing the three input variables to obtain the corresponding output results. The whole process relies on the empirical formula calculation method for the calculation of pressure loss, and it does not need to build a large number of experiments to complete the data collection. Therefore, this method is economical, convenient and fast.
4 Conclusions
The purpose of flour storage at specific time and continuous feeding is realized through multiple storage tanks, but the energy consumption is too large due to improper parameter design during the operation of the system. In order to solve this problem, this paper makes a theoretical analysis on the factors affecting the energy consumption of the fan in the pneumatic conveying system. System pressure loss is taken as an index to evaluate energy consumption, and there are many factors affecting the system pressure loss. This study mainly analyzes the process parameters of the mixture ratio of fuel and gas, air transport speed and pipe diameter, and determines the test design scheme of three factors and four levels through the method of orthogonal experimental design, and finally concludes: The mixture ratio of fuel and gas has the greatest impact on energy consumption, followed by the air transport speed, and the pipe diameter has the least impact on energy consumption. This analysis conclusion provides a very useful theoretical basis for further study of the energy consumption of the system and optimization of process parameters, so it has a very important significance for improving enterprise benefits.