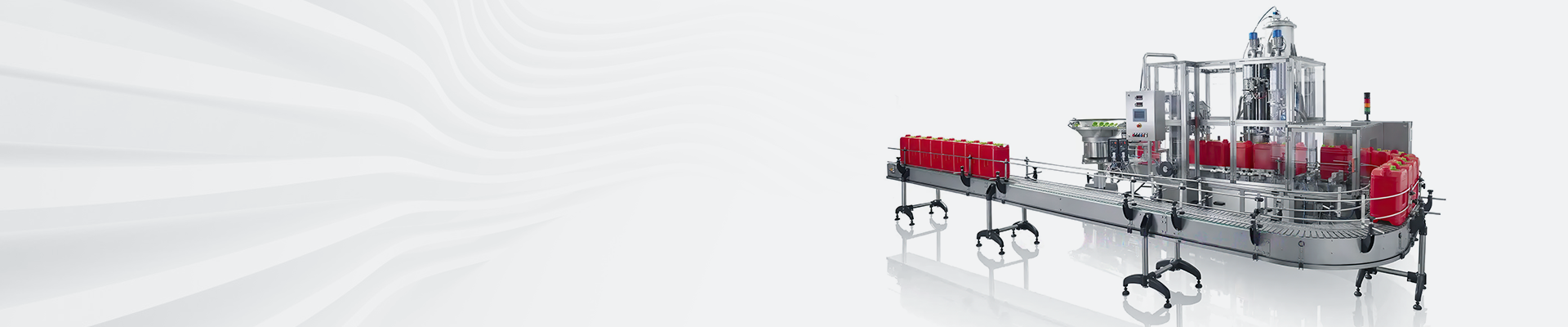
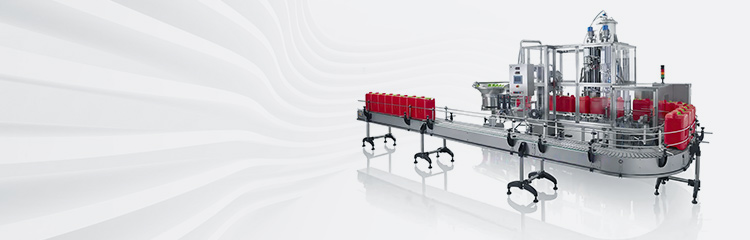

Summary:Abstract: A set of weighing control system of silicon carbide powder mixing device is introduced. The basic structure of the system, the hardware composition of the computer batcher and the control program module are given, and the working principle of the self-made D/A is described. The self-made D/A uses the existing 8155 chip counter in the system to convert F/V, eliminating the special D/A. The practice shows that the system has the advantages of fast batching speed, high precision, strong anti-interference ability, real-time report processing, warehouse management and so on.
0 Preface
Silicon carbide is a good sealing material for mechanical industry. In the production process, raw materials should be mixed according to a certain ratio first. According to the requirements of a factory, a set of automatic mixing control system is designed in this study and has been put into production. Practice has proved that the system has fast batching speed, high precision, static error <±0.1%, dynamic error <±0.2%, strong anti-interference ability, and has real-time report processing, warehouse management and other functions. It is a comprehensive system integrating automatic control and information management. This research focuses on the composition of the whole batching control system, the hardware composition of microcomputer batching controller, and the working principle of the control program module and self-made D/A.
1 System Composition
The feeding system takes the computer batching controller as the core, and controls other equipment to complete batching 2. The raw materials fall into the hopper scale from the silo driven by the skewer, there are 6 ways, respectively conveying different materials. The speed of skewer operation is adjusted by the frequency conversion governor according to the output voltage of the batching controller. In actual batching, the formula and batch of batching are set through the batching controller keyboard, the batching weighing instrument automatically selects the required bin, sends instructions to drive the winch motor, and makes the material fall into the weighing bucket. The weighing signal is output through the weight sensor on the weighing bucket, and the frequency conversion governor is controlled by the batching weighing display to adjust the winch speed and control the feed amount. Make the end value with sufficient precision. At the end of the dosing, the door is automatically opened, and the material enters the mixer for mixing. The dosing controller automatically calculates the mixing time, and releases the finished material when the mixing is finished.
2 Component hardware of the batching controller
The hardware of the computer proportioning controller is composed of three tension weighing modules in the weighing system, which are connected in series to improve the output sensitivity, and three independent power supplies are used. Since the performance of the power supply, the post-amplifier and the A/D converter directly affect the control accuracy, the LM399 high-precision voltage regulator, the ICL7650 instrument amplifier, the ICL7109 low-drift A/D chip are used in the weighing system, and the external reference is used with high stability, thus ensuring the accuracy in the entire linear measurement range. Because the 80C31 I/O interface line is limited, the 8155 is extended, because the 8155 internal has 256BytesRAM, 22-line I/O interface, which not only expands the storage, but also expands the I/O; At the same time, 8155 internal timer is used for F/V conversion to complete D/A function, making full use of 8155 chip. In order to prevent the interference of the backward channel into the CPU system, the input/output interface of the 8155 and the outside world are all photoelectric isolation, and the PA and P of the 8155 are used. The port is used as an output line to drive the skein selector switch, P. The mouth is used as an input signal for the position limit of the electronic weighing bucket and the mixer door. The display part uses a 0.5 hour digital tube, which is divided into two rows, the upper row shows the current amount of ingredients, and the lower row shows the error or cumulative value of ingredients. Keyboard is mainly used to input formula and various parameters, in order to save hardware lines, LED display and keyboard are dynamic scanning structure.
3 System software design
The program software of the feeding system adopts a modular structure and is scheduled by the main control program. The main modules are: Display and keyboard function scanning module, data acquisition module (collect A/D data, digital filtering, etc.), control algorithm module (complete dynamic accuracy control and overcome "return air" interference), output control and D/A output module, keyboard function processing module, software timing module, alarm module. 4 Self-made D/A working principle This system uses 8155 internal timer for F/V conversion to complete the D/A function and control the frequency conversion governor.
The square wave signal with a frequency of about 2kHz is connected to the input end of the timer, which is used as the input signal of the timer, and the output adopts photoelectric isolation. CA3140 is used to increase pulse amplitude and convert negative pulse to positive pulse. R and C constitute an integral circuit, which is used to filter out higher harmonics, so that the output end can get a stable DC level. Using the continuous pulse signal control mode 6 of the timer, the pulse width is the half period of the input signal, and the frequency of the pulse is determined by the timing constant T of the timer, that is, the output signal can be modulated by the timing constant T.
It can be seen that the output voltage V is only related to V and T, and has nothing to do with the integrating components R and C. The accuracy of R and C components does not affect the output voltage, which is its advantage. However, when the output voltage of the timer is relatively low, the voltage after RC integration is the pulsating voltage, and the amplitude of the pulsating voltage is related to the RC time constant. The larger the RC is, the smaller the pulsating amplitude is, but the D/A conversion time is longer. Therefore, RC should be reasonably selected in practical application. In addition, the higher the frequency of the input signal, the smaller the pulsation, but increasing the frequency fashion should consider the limit of the optocoupler transmission frequency.
5 Closing remarks
The batching system has been applied in the batching of SIC powder, which greatly improves the batching precision and the stability of product quality. The practical operation shows that the system is easy to use, flexible and has a good development prospect. At the same time, the control principle described in this study can also be applied to other industrial machinery.