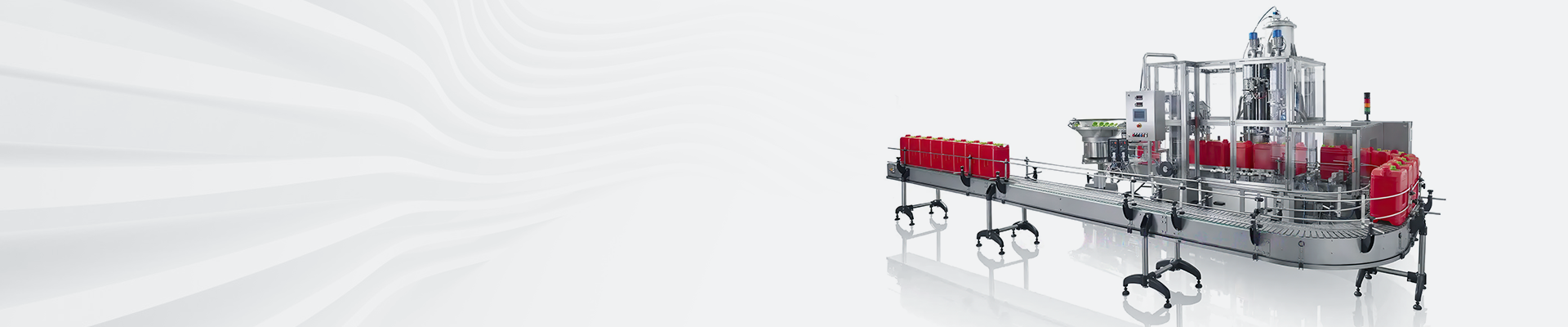
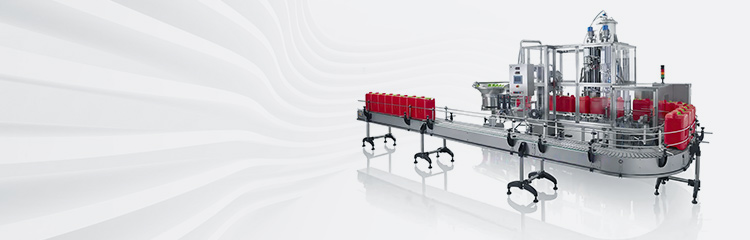

Summary:Automatic complete sets of mechanical, electrical, computer integration system, the system is mainly used in the production of polyethylene film blowing workshop, its function is to distribute in a few hundred meters of more than 10 to do the film workshop in the automatic preparation of the production of raw materials (PE pellets) according to their own formula, and the preparation of raw materials automatically transported to the need of extrusion and blowing film machine.
In recent years, China has promoted plastic greenhouse planting and agricultural film mulching technology in rural areas, making polyethylene plastic film production into the leader of the entire plastic industry, but the degree of automation of the equipment used in China's polyethylene plastic film production line is low, especially the two important production processes in the film blowing production of raw materials and feeding, the widespread use of manual feeding and semi-automatic feeding. The amount of labor of the workers is too large, and the accuracy of the ingredients is low. Although there are also manufacturers producing automatic feeding machines in China, this equipment is expensive, and an automatic feeding machine can only feed a extrusion film blowing machine (hereinafter referred to as the extrusion machine), so the use of manufacturers are very few. The existing feeding method also has two common drawbacks: first, the batching equipment and raw materials occupy more production sites. Second, the raw materials need to be manually transported from the warehouse to the production site. According to the production characteristics of multiple extruders in the plastic film production industry are often concentrated in one or two workshops, the author proposes a new centralized raw material distribution scheme.
1. Mission and overall design
The main task of the raw material feeding system is to mix and feed, and to reduce the production, installation, operation and maintenance costs of the system as much as possible under the premise of ensuring the production amount and formula accuracy and system reliability. The idea of system design is as follows: ① a set of large self-developed batching machine is used in the raw material warehouse to concentrate on the preparation of raw materials needed for all extrusion machines. This allows all extruders to share a set of batching machines to reduce system cost and improve equipment utilization, while also eliminating raw material handling. ② The positive pressure thin phase pneumatic conveying method is used to blow the prepared raw materials through the conveying pipeline to the hopper of the extrusion machine where they should be. The pneumatic conveying scheme has the characteristics of low production and installation cost and energy consumption, and easy maintenance. (3) Due to the large scale and complex structure of the feeding system, its components are distributed in the workshop and warehouse, and to complete its automatic control, there are many and scattered signals and control parts that need to be detected. Therefore, it is necessary to use the advanced real-time computer network control scheme of fieldbus to complete the control of the whole system. The pneumatic feeding system consists of two subsystems: mechanical electrical and computer control.
2 Mechanical and electrical subsystem
The mechanical and electrical subsystem mainly consists of the batching system and the feeding system.
2.1 Feeding system
The feed control system is composed of several feeding machines with the same structure and a barrel-shaped mixing chamber. Each blanking machine is composed of a frequency converter, a feeder motor and a rotary hopper feeder, and the blanking machine is responsible for taking material from a bin at a fixed rate. When dosing, different feeding machines take materials from different silo at different speeds at the same time, and put them into the mixing chamber, the proportion of dosing is achieved by the different feeding speed ratio of different feeding machines, and the length of feeding time will determine the amount of dosing.
2.2 Feeding system
The feeding system is composed of two Roots blower units, meaning feed pipes and several branch feed pipes, pneumatic two-branch reversing valves (hereinafter referred to as branch valves) and a number of cyclone separators. One of the two fans is a backup fan, and each Roots blower unit includes a Roots blower, a typhoon electromechanical machine and a fan control cabinet, whose task is to generate compressed air flow required for pneumatic conveying. The fan outlet is connected to one end of the mixing chamber, and the total material delivery pipe is connected to the other end of the mixing chamber. The feeding system and part of the fan unit and the total feed pipe can be installed in the raw material warehouse. The total feed pipe from the raw material warehouse is connected with an independent branch valve, which can form two branch feed pipes respectively to two workshops. Similarly, n+1 branch feed pipes can be formed with n branch valves, and these branch pipes are equipped with 1 branch valve at the location (hopper) of each extruder in the workshop. When selected to feed to a extrusion machine, the relevant branch valve is played in the corresponding direction, so that the material can only lead to the extrusion machine and can not go to other locations, so that the fan will mix the air mixture in the mixing chamber through the various links of the feeding channel to blow to the corresponding cyclone separator, after separation, the material reaches the corresponding extrusion machine hopper.
2.3 Characteristics of raw material preparation and conveying system
It should be noted that the volume of the barrel-shaped mixing chamber is limited, and there is no agitator in it, and the raw materials from each feeder to the mixing chamber are blown away directly without stirring, and while feeding, they are transported. Although the raw materials are not stirred in the distribution process, the clever design method makes the raw materials go through the mixing, the mixing of the turbulent flow in the blowing process, and the random mixing when the raw materials fall into the hopper of the extrusion machine, and the uniformity fully meets the requirements. When it is necessary to feed a extrusion machine, it is not necessary to determine the preparation amount in advance, in the process of matching and sending, the system can stop distribution at any time according to the specific situation, such as the hopper has been full or there is an urgent task.
3 Computer control subsystem
The computer control subsystem is a real-time computer network system that connects dozens or even hundreds of computer sites responsible for the measurement and control of field equipment by fieldbus. Its composition and structure are shown in Figure 2. We developed a kind of fieldbus technology with certain universality in bli. The use of this technology makes the structure of the control system most simplified, and can adjust the scale of the system according to needs, saving the number of hardware and investment, installation and wiring costs and maintenance costs, and improving the accuracy and reliability of the system.
3.1 Computer system hardware
The RS485 fieldbus is used in the physical layer, and the transmission medium is hung on the bus with five types of twisted pair wire to communicate with each other, including two Advantech IPC and a number of self-developed intelligent measurement and control modules with 51 microcontroller as the core, which are connected by the fieldbus to form a whole that can communicate with each other and coordinate work. Two Advantech IPC machines are the upper computers in the system, one of which serves as the man-machine interface and completes tasks such as central main control and system task scheduling, and the other is a hot backup machine. Each of the two computers has an RS485 interface card to communicate with other sites. Other intelligent measurement and control modules are responsible for measuring and controlling the lower machine of each field device, and each lower machine is equipped with RS485 interface to connect to the network. There are four kinds of intelligent measurement and control modules as the lower computer.
(1) The feeder measurement and control module the feeder feeder is driven by the feeder motor to achieve rotary feeding, and the motor is driven by a frequency converter. A measurement and control module is designed, which can control the start, stop and output frequency (speed) of the converter, and detect the working state of the converter. In addition, it detects the rotation of the feeder by means of an photoelectric encoder installed on the feeder. Each feeder in the batching system is installed with 1 such module, which constitutes a group to coordinate the start and stop, ratio and discharge control of the batching system.
(2) The fan measurement and control module can not only control the start and stop of the fan through the fan control cabinet, but also detect the pipeline air pressure through the air pressure sensor installed at the fan outlet. Each of the two fans in the system uses one of these modules.
(3) The extruder measurement and control module is used to detect the hopper level of the extruder and control the local reversing valve to select the unloading position. One of these modules is installed on each extruder.
(4) Independent branch valve measurement and control module control The measurement and control module of this valve is not designed separately, and the third kind of measurement and control module is also used, because the third kind of measurement and control module can complete its function.
3.2 Software System
The software includes three kinds of lower computer software and upper computer software. The function of lower computer software is mainly to detect, control and network communication of local field equipment. The software of the upper computer includes the main control program, the human-computer Put interface program, the task scheduling program, the network communication program and various sub-programs. Limited by space, only the design idea of the master control program is introduced. The main control program is a real-time program with complex structure, and its overall control method is as follows: the main control computer obtains the material level status of all extruders collected by the measurement and control module of the extruder through the network, and generates a dynamic task table that can reflect the requirements and priorities of the ingredients feeding of each extruder according to the material level status and other related factors. According to this task table, the system further completes the batching feed of each extruder in order of priority. When the system decides to feed a certain extruder, the main control machine first issues a command to the fan measurement and control module to start the fan. At the same time, the corresponding valve opening and closing commands are issued to the measurement and control module of each extruder and branch valve, and the confirmation that the valve opening and closing are in place is obtained. Ensure that the channel of the corresponding extruder is smooth, and then take out the formula set by the operator for the extruder in advance, calculate the feeding speed of each feeder according to the formula proportion, and send to the feeding device measurement and control module, and then issue the command to start the feeding device to start the feeding device, by the feeding device measurement and control module to control the feeding device, and feed the mixing chamber at the same time according to their respective feeding speed. During this period, the master computer counts the blanking time, and obtains the running status of the blanking device collected by the blanking device measurement and control module. When the dosage reaches the requirement, it sends commands to each blanking device measurement and control module to stop blanking, and then completes the batching task.
4 Trial effect
A set of such a system was installed in Henan Yangkai Plasticizing Co., Ltd. to feed 20 extruders in 2 workshops within 180m, with 9 kinds of raw materials, 5t/h feed volume and 97% ratio accuracy. The system replaces all the feeding workers and feeding machines, reduces the loss of raw materials, eliminates the phenomenon of uneven mixing in semi-automatic feeding and manual feeding in the past, and improves product quality. The raw material distribution cost has been reduced from 30 yuan /t in the original semi-automatic and manual feeding to about 2 yuan/today.
Conclusion
The batching system will automatically mix raw materials in the warehouse to the film blowing machine, set raw material handling, mixing and conveying as one, can achieve 24h unmanned continuous feeding, using the system can greatly reduce production costs and improve product quality. In addition, although the system is designed for polyethylene film production enterprises, but as long as the production method is similar to such enterprises, it can also use this feeding method.