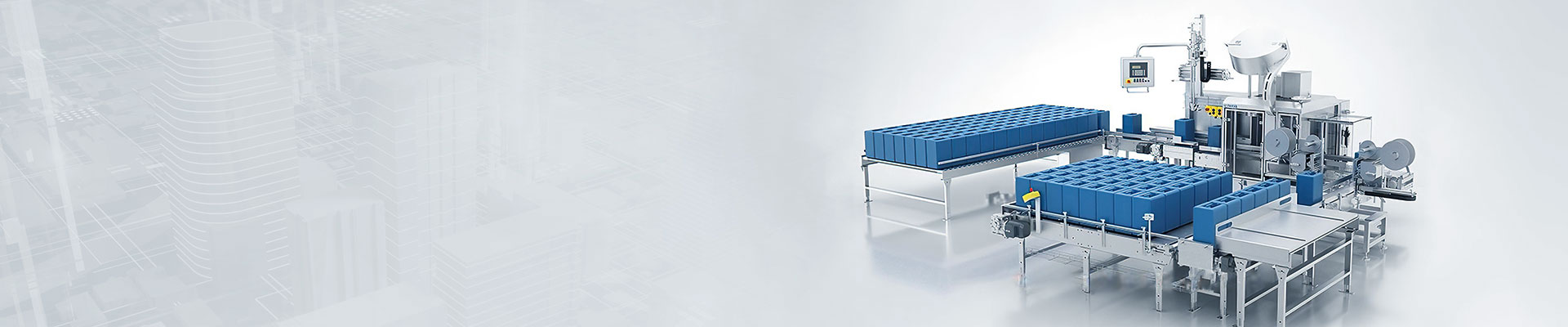
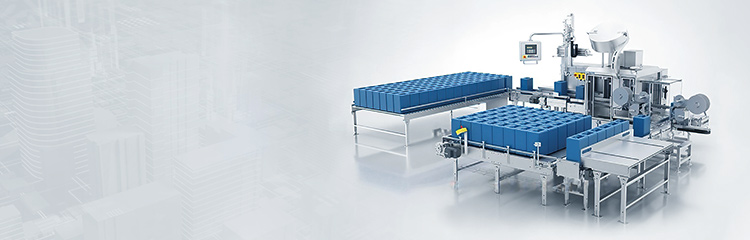
Weighing mixer for additives and pre-mixing unit, PLC as the main control of the unit, weighing module to collect the weight of the material in the mixer and should have the position (prompted when the material is lost). Limit switch, when the lifting action reaches the position, it should be signaled at the appropriate position. Analog output signal, 4-20mA to 4 valve switches to control the opening, with S type tension to collect the material position and close the valve when the weight reaches the required dosage weight. Has a communication circuit module whose function is to communicate with the console. The communication data is bi-directional and is required to receive information from the console about the specific gravity of the material and the weight distribution of each material mixer.

Weighing mixer for additives and pre-mixing device, PLC as the main control of the unit, weighing module to collect the weight of the material in the mixer and should have the position (prompted when the material is lost). Limit switch, when the lifting action reaches the position, it should be signaled at the appropriate position. Analog output signal, 4-20mA to 4 valve switches to control the opening, with S type tension to collect the material position and close the valve when the weight reaches the required dosage weight. Has a communication circuit module whose function is to communicate with the console. The communication data is bi-directional and is required to receive information from the console about the specific gravity of the material and the weight distribution of each material mixer.
Conveying system main equipment configuration
1) warehouse pump: warehouse pump by the warehouse body, plug valve, expansion joints, inlet valve, exhaust valve, air intake components and so on.
2)piping: connect the silo pump to the ash storage to realize long-distance transmission. It should have sufficient strength, smoothness and wear and corrosion resistance.
3)Companion gas pipeline:The pressure of the pipeline will drop gradually during the process of ash conveying, and it is necessary to make up the gas in the middle to maintain the normal pressure of ash conveying. So that the material is always in a suspended state.
4)Transmitter:Transmit system pressure, ash hopper material level, bin pump material level, etc., to realize the remote monitoring and adjustment of the ash delivery system.
5)Valve:Switching and isolation of silo pumps, pipelines, ash transmission electric field, ash storage, to realize program control.