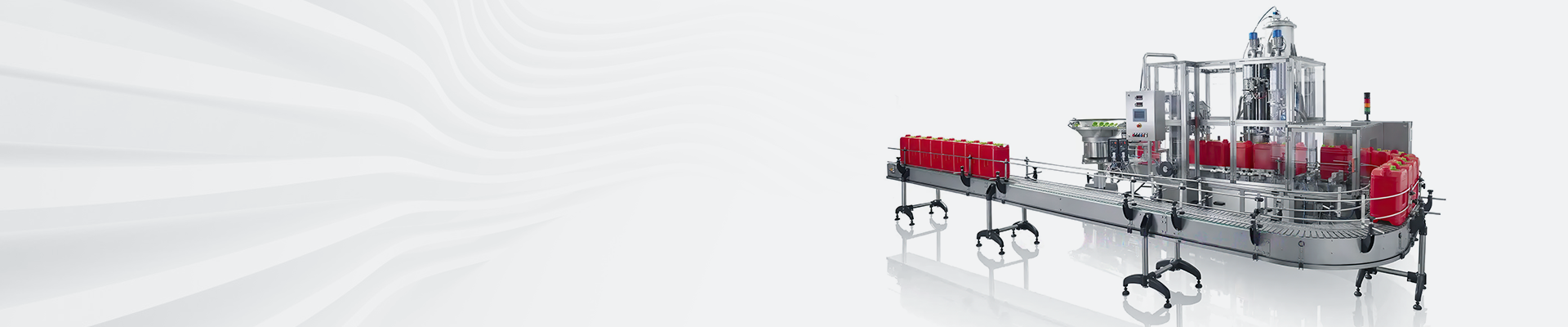
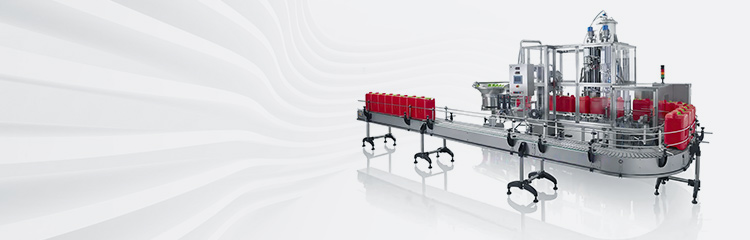

Summary:The batching machine control system is designed using Siemens TIA V13 software platform and PROFINET industrial Ethernet. The batching machine is mainly composed of Siemens 1516FPLC, G120 frequency converter, and TP700 human-machine interface.Realize automatic control and complete various operations such as feeding, dispensing, and calibration.Interlock control is adopted for each valve to avoid accidents such as material leakage caused by misoperation.
With the development of modern industrial technology and the acceleration of urbanization, the mixing and stirring technology has also been developed rapidly. But how to control the mixing process and quality is still a major problem to be solved. How to accurately control the material mixing ratio, mixing time, reduce the turbulence generated in the mixing process and mixing power, etc., still need to be solved by constantly optimizing the technical means. This study aims to use advanced Siemens industrial control technology to solve the related problems in mixing and blending, and to optimize and precisely control the mixing process. The use of Siemens high-end S7-1500 PLC, frequency conversion technology and PROFIBUS industrial Ethernet technology based on bus standards to achieve the mixing mixing device mixing process and quality optimization, improve the quality of the mixing mix, to achieve the relatively ideal quality and effectiveness of the mixing mixture.
1 Batching machine system composition
The mixer is mainly composed of mixing system, feeding part, discharging part, control cabinet, frequency conversion motor, frequency converter, weighing and dosing system and control operation panel. Using Siemens 1516F-2PNDPPLC to control the material proportion, using the output of the G120 frequency converter to control the motor speed, the operation control panel intuitively shows the motor speed, process, the whole system can display and control the production process of a variety of materials mixing and blending process.
2 batching machine control and communication design
2.1 Control design of batching machine
In the production process, according to the formula of the material added through the weighing control system measurement, the resulting signal input to the Siemens 1516F-2PNDPPLC, PLC according to the formula to control the weight of different materials and feeding order, feeding is completed, through the inverter motor to drive the mixing system for mixing. PLC and frequency converter are used to control the speed of mixing to realize the control of product quality. The frequency converter adopts G120 frequency converter with PROFINET industrial Ethernet port.
2.2 Communication and configuration design of batching machine system
(1) Communication design of batching system
The automatic batching system adopts bus type network topology. PROFINET field bus is used for communication interconnection. The signals of on-site equipments such as weighing module, travel switch and contactor are connected to the IO module of 1516F-2PNDPPLC with PROFINET communication interface by adopting the principle of proximity. The inverter motor is connected to the G120 inverter, and the PLC, HMI and inverter are connected to the same PROFINET bus network.
(2) Hardware configuration of measuring and batching system
Using TIA Botou V13 software for hardware configuration design, set up a S7-1500 control station, select CPU module 1516F-2PN\DP (6ES7315-2FJ14-0AB0), the power module PS3075A (6ES7307-1EA01-0AA0), digital module DI16\DO1624VDC\ 0.5A (323-1BL00-0AA0), analog metering module AI4/A028BIT (334-0CEO1-0AA0) for the configuration, add industrial Ethernet bus PROFINET, TP700 human-machine interface and G120 inverter (with PN network interface control unit and power module).
3 batching machine control system software program design
3.1 batching machine G120 frequency converter parameter setting
Utilize Botou V13 development platform to set the parameters of G120 inverter. Set P10 = 1 (into the fast debugging mode) P15 = 6 (fieldbus PROFINET for communication), P922 = 352 (PZD6/6 control word) P10 = 0 (end of the fast debugging), according to the motor nameplate to set the benchmark parameters. Set P2051 communication content. p2051.0r2089 (status word 1), p2051.1r633 (frequency feedback) p2051.2r68 (actual current), p2051.3r80 (actual torque), p2051.4r2132 (alarm number), p2051.5r2131 (fault number).
Table 1 Parameterization of the frequency converter of the batching plant
Parameter address/description/parameter
P2000/base frequency/1400.00
P2001/Reference voltage/380
P2002/baseline current/0.3
P2003/Regular torque/0.41(9.55*power/speed)
P2004/Regular power/0.06
(1) Communication data port design
Communication data selection PZD6/6, the address corresponds to: PIW256-PIW266PQW256-PQW266, PIW256 for the status word, PIW258 frequency feedback, PIW260 actual current, PIW262 actual torque, PIW264 alarm number, PIW266 fault number, PQW256 for the control word, PQW258 frequency set value, PQW260-PQW266 standby (where all set and feedback values are 16#0-4000 numbers, which must be converted during writing and reading).
(2) Inverter communication control word command and setting
Stop: W#16#047E, start: W#16#047F, reverse: W#16#0C7F reset: W#16#04FE
Setting of inverter parameters: modify P10=1, modify P15=6 (fieldbus PROFINET with two safety function macros), modify P922=352 modify P10=0.
3.2 PLC program design of batching machine
The feeding system needs to fulfill the functions of feeding, mixing and unloading of two kinds of materials. Through the solenoid valve on and off to control the entry of materials, weighing module by monitoring the weight of the feed to control the amount of feed input. After pressing the start button, the solenoid valve A is energized and opened, the first material begins to enter the container, when the material reaches the pre-set weight, at this time the solenoid valve A is de-energized and closed. And solenoid valve B energized on, the second material into the container, when the weight of the material reaches the preset value, the solenoid valve B de-energized off, and at the same time start the motor stirring. The rotation time of the motor is controlled by presetting the mixing time.
3.3 Mixer control system human-machine interface program design
Through the design of human-machine interface (HMI) system can intuitively, real-time, clearly display the operating status of the batching machine, and can quickly set and control the relevant parameters of the device. According to the needs of the device and control, the design of the mixing device automatic operation interface and parameter setting interface, start and stop records, historical alarm records and so on.
4 Conclusion
Adopting Siemens PROFINET industrial Ethernet communication technology for the batching machine control system realizes the interconnection of on-site equipment, improves the operation efficiency of the equipment, reduces the system failure, and lowers the maintenance cost of the equipment, and adopts the HMI human-computer interface monitoring to improve the human-computer interaction capability of the system, facilitate the monitoring of the equipment by the technicians, and design the practicality, safety and high efficiency of the batching machine.