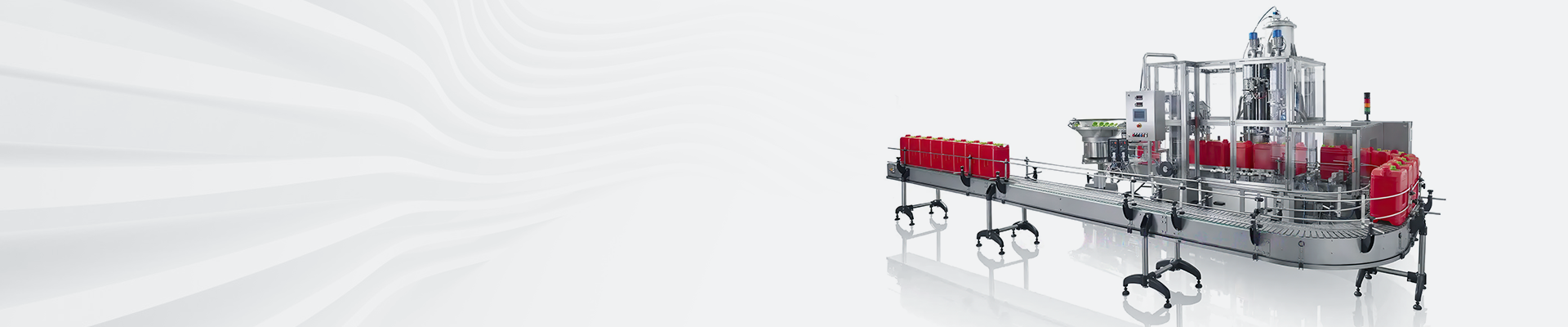
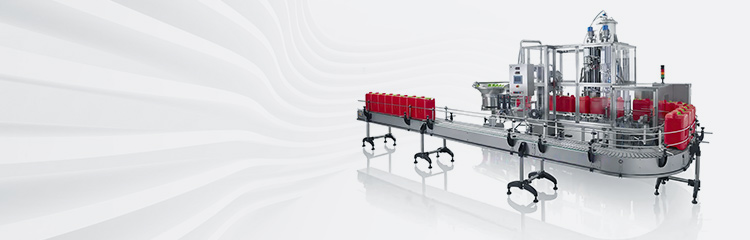

Summary:The automatic batching control process is a multi-input and multi-output system. It consists of a two-level computer control network composed of PLC and electronic scales. It connects field instruments, control computers, PLCs, frequency converters, etc. through field buses. It has high intelligence and fast processing speed. device of.
Automated dosage system is a very important process in the production process of fine chemical plant, and the quality of dosage process is very important to the quality of the whole product. Automatic batching control process is a multi-input, multi-output system, each batching and conveying production line is strictly coordinated automation control, timely and accurate monitoring and adjustment of material level and flow. The system consists of programmable controllers and electronic scales to form a two-stage computer control network, connecting field instruments, control computers, PLCs, frequency converters and other equipment with high intelligence and fast processing speed through the field bus. In the batching production process, the main material and auxiliary materials in a certain proportion with the electronic scale to complete the measurement of the material conveyor, PLC is mainly responsible for conveying equipment, weighing process for real-time control, and complete the system failure detection, display and alarm, while the frequency converter output signals to regulate the speed of the belt conveyor role.
Batching composition
The automatic dosage system adopts "EVOC" industrial computer produced by Advantech Industrial Control Group, with remote data acquisition module, and follows the industrial 485 protocol composition, which ensures the system reliability and advancement from the hardware. After the microcomputer system is started, the feeder is started according to the pre-stored working formula (want to weigh the value), and the material is fed to the weighing hopper, at this time, the weighing module will change the weight to the ADAN module, and then transmitted to the microcomputer. When the set value is reached, the microcomputer issues a command to turn off the feeder and start the discharger to discharge the material to the receiving equipment, thus ending a basic weighing and batching process. The batching machine consists of electronic scale batching, numbered as 1#, 2#, 3#, 4#, 5#, of which 1# to 4# is a group, 1# is the main material scale, the other three are auxiliary material scale. When there is no need to add auxiliary materials, 5# electronic scales work alone to convey the main material. The system has two functions of constant flow and proportioning control. For constant flow control, the electronic scale automatically adjusts the belt speed according to the amount of material on the belt to achieve the set flow requirements. Take the main scale (1#) system process flow to analyze.
After the system is energized, the belt drive motor starts to rotate and the microprocessor controls the motor speed according to the current operation. The material in the hopper falls in the drop zone and is transported by the belt to reach the weighing zone, where the material on the belt is weighed by the electronic scale. The weighing module outputs a voltage signal according to the magnitude of the force applied, which is amplified by the transmitter and outputs a metering level signal proportional to the weight of the material. This signal is sent to the interface of the host computer, after sampling and converted into a flow signal, the current flow value is displayed on the host computer. At the same time the flow signal is sent to the PLC interface, and the upper computer set a variety of dosage for comparison of the given value, and then adjust the operation, the control volume sent to the frequency converter to change the output value of the frequency converter, thereby changing the rotational speed of the drive motor. Adjust the feeding quantity to make it equal to the set value and complete the automatic batching process.
The flow is the amount of material traveling on the belt in a certain time. The electronic scale weighs the instantaneous flow rate, and the upper computer gives the set flow rate, both of which are deviated in real-time measurement. In the actual control of the flow of the most widely used in industrial control PID regulation, according to the flow deviation, the use of proportional, integral, differential calculated control amount for control. In the production process for automatic adjustment, based on the flow measurement of the main ingredient components, according to the requirements of the production process through the host computer to set out the total flow and the main and auxiliary ingredients ratio parameters, according to the formula proportion of the rest of the auxiliary materials mixed. Flow metering control is a combination of metering deviation and frequency conversion speed control, which has the advantages of simple structure, good stability, reliable operation and convenient adjustment.
Batching control process
When the batching starts to work, start the batching machine. First of all, the system program is initialized, the batching ratio is set through the upper computer or touch screen, and the material in the hopper is checked. If there is no material, feed the material to the hopper, start the batching line, weighing and real-time measurement by the electronic scale, the CPU calculates the real-time flow rate and cumulative flow rate. If there is a deviation between the set flow rate and the actual flow rate, the regulator compares the deviation between the set value and the actual flow rate according to the system control requirements, and then changes the output signal by PID regulation to control the frequency converter to regulate the speed of the conveying motor, so as to realize the constant flow rate control. According to the proportion of each auxiliary material at the same time mixed and measured, and added according to the recipe process requirements.
The core of dosing accuracy is the compensation of the fall and accumulated error of the air material, and its control methods include the automatic correction method of fall, fixed value compensation method, point movement compensation method and over-measurement deduction weighing method.
(1) Automatic correction method. Drop correction method is less affected by the mechanical structure, the drop is more stable in the case of the choice of control methods, can be used alone, can also be used with a variety of other control methods. The control method is as follows: the initial value of the fallout is preset manually first, and then a learning algorithm is used to find a suitable fallout value, from which control algorithms are born such as iterative self-learning control algorithms, fuzzy control algorithms, fuzzy adaptive control algorithms, and control algorithms based on the prediction function.
(2) Fixed-value compensation method. The constant value compensation method is a drop correction method proposed for the control mechanism is stable and the material is uniform. By setting the fixed value in the upper computer, it realizes that when the dosage stops, the material on the scale is within the set error range. This kind of control because of the need for precision control mechanism and accurate weighing mechanism, many users require high, the application surface is small, and for the system can not automatically adapt to the production process of fallout changes, the actual application is less.
(3) point compensation method. Point compensation is the most widely used domestic error compensation control method. Weighing instruments are usually close to the target value when using point compensation can improve the control accuracy, point compensation contact time between 0.3s ~ 0.5s optimal.
(4) Excessive weight deduction method. Excessive buckle scale control method is to take the material over the scale to feed the early closure of the door, will be a certain amount of material left on the scale control method. This control method can ensure that the weighing of each plate are stabilized, to prevent the uneven proportion of single plate materials, resulting in the overall quality of the product unqualified phenomenon. However, the early closing time by the degree of material thickness and equipment and electrical mechanism response speed, it is difficult to achieve the accuracy of the over-measurement deduction weighing, and at the same time the degree of damage to the mechanism is also unavoidable.
PLC dosage hardware settings
The main and auxiliary material scales in the system by the programmable logic controller (PLC) and the host computer to achieve two-level control. Now take 1 # ~ 4 # four electronic scales PLC control analysis as an example, each electronic scale has a belt drive motor, two material level sensors, a speed sensor, a weighing module, a frequency converter, which constitute the controlled object. Motor start, stop by the switching control, PLC digital output signal as a frequency converter control terminal input signal, modulated by the frequency converter output high-frequency pulse to the belt drive motor. The material level sensor detects the presence or absence of material in the hopper, and the speed sensor measures the speed of the motor. The system requires 8 digital input signals, 25 switching input signals and 24 switching output signals, with a total number of I/O points of 57. The dosage weighing module is in fact a device that transforms a mass signal into a measurable electrical signal output. The weighing module takes into account the actual working environment in which it is located. This point is crucial for the correct selection of the weighing module, and is related to the ability of the weighing module to work properly, as well as to its safety and service life, and even to the reliability and safety of the entire scale. Environment to the weighing module caused by the impact of the following aspects:
(1) High temperature environment causes melting of coating materials, weld cracking, and structural change of elastomer internal stress on weighing module. For the weighing module working in high temperature environment, high temperature sensor is often used; in addition, it must be added with heat insulation, water cooling or air-cooling and other devices.
(2) Dust, humidity on the sensor caused by short-circuit effects. In this environment, the weighing module with high sealing should be used. Different weighing modules are sealed in different ways, and their tightness is very different.
(3) In the corrosive environment, such as humidity, acidity and weighing module caused by elastomer damage or short circuit and other impacts, should choose the outer surface of the plastic spraying or stainless steel cover, corrosion resistance and good sealing of the weighing module.
(4) The influence of electromagnetic field on the sensor output signal disorder. In this case, the shielding of the weighing module should be rigorously checked to see whether it has good antimagnetic ability.
(5) Flammable and explosive not only cause thorough damage to the weighing module, but also give a great threat to other equipment and personal safety. Therefore, weighing modules working in flammable and explosive environments put forward higher requirements for explosion-proof performance: explosion-proof weighing modules must be used in flammable and explosive environments, and the sealing cover of such weighing modules should not only take into account its airtightness, but also take into account the strength of the explosion-proof, as well as water-proof, moisture-proof and explosion-proof cable lead-outs.
CPU and input/output module selection
SIMATICS7-300 of Siemens belongs to modularized small PLC system, and a wide range of individual modules can be combined to form a system with different requirements.
According to the number of I / O points of the system controlled object and process requirements, scanning speed, self-diagnostic functions and other considerations, the choice of SIEMENS S7-300 series PLC's CPU315-2DP. CPU315-2DP is the only CPU template with a fieldbus (PROFIBUS) SINECL2-DP interface with 48KB RAM, 80KB load memory. It has 48 KB of RAM, 80 KB of load memory, which can be expanded with a memory card to a maximum of 512 KB, and can be expanded with a maximum of 1024 digital or 128 analog points. According to the counted I/O points, a DC 32-point and a 16-point SM321 digital input module and a 32-point SM322 relay output module are selected.
Inverter selection and its function setting
Mitsubishi provides the technical parameters of FR-A540 series inverter when matched with the company's standard motor. Using Mitsubishi's standard motor, 1 # belt machine rated power 2.2KW, 2 ~ 4 # belt machine rated power 0.4KW, rated voltage 380V, rated current 5A, speed 1420r/min, speed range of 120 ~ 1200r/min. Mitsubishi FR-A540 frequency converter comes with PID adjustment function, according to the requirements of the dosage production process for PID control.
PLC software design
STEP7 is the programming language used by Siemens S7-300 series PLC, which is a kind of language that can be run in general-purpose microcomputer and programmed in WINDOWS environment. Through the STEP7 programming software, not only can it be very convenient to use ladder diagrams and statement tables and other forms of offline programming, and through the adapter cable can be sent directly to the PLC's memory for execution, but also in the debugging operation, you can also monitor the program on-line each input and output or status point of the on and off situation, and even on-line modification of the value of the variables in the program, the debugging work is also a great convenience.
STEP7 divides user programs into different types of blocks. Program blocks are divided into two categories: system blocks and user blocks. User blocks include: OB = Organization Block, FB = Function Block, FC = Function, DB = Data Block. The main program can be placed in an "organization block" (OB), while subroutines can be placed in a "function block" (FB or FC).
In this system, the main task of PLC is to accept the input of external switching signals (buttons, relay contacts) and digital signals generated by sensors, to judge the current system status and to output signals to control the contactors, relays, solenoid valves and other devices in order to complete the corresponding automation control tasks. In addition, another important task is to accept the control commands from the industrial control machine (host computer) to carry out automatic dosage control.
The automatic dosage program has 7 "blocks" such as OB1 and FC1 to FC6, etc. OB1 is the main program, which calls FC1 to FC6 and other function blocks in turn through 6 "CALL" call statements to organize the whole program. The assignments of the six function blocks in the program are as follows:
FCl is responsible for starting the system and setting the operation mode; FC2 is responsible for stopping the system; FC3 is responsible for metering pump and metering pump proportioning control; FC4 is responsible for fault and accident handling control; FC5 is responsible for automation control of frequency converter; FC6 is responsible for indicator display control.
Conclusion
PLC replaces the traditional mechanical transmission and huge control appliances to realize the automatic control of electric. Through the frequency conversion speed regulation of the belt motor, it achieves energy saving and improves the batching accuracy. The batching system adopts PLC control scheme, which greatly improves the batching precision, facilitates the microcomputerized control of metering, realizes networked production management, and achieves good economic benefits through the commissioning and use.