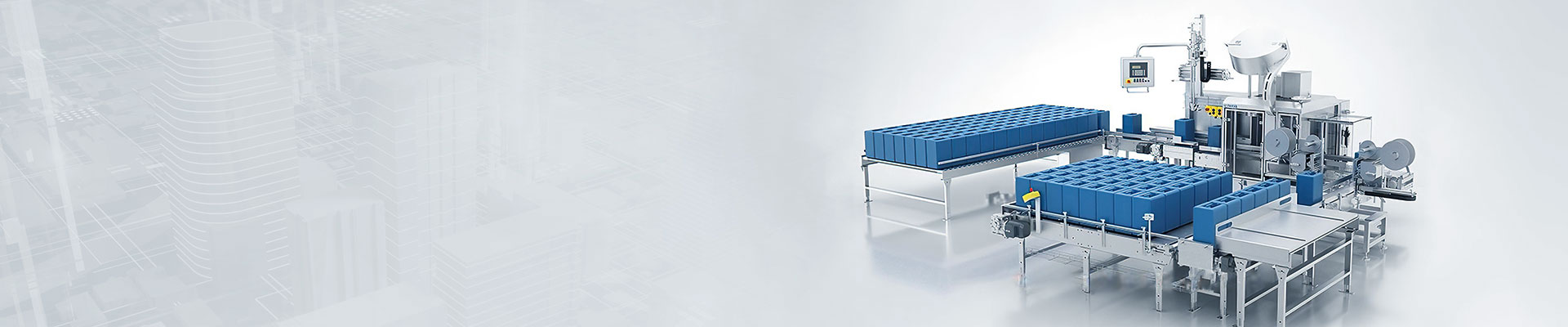
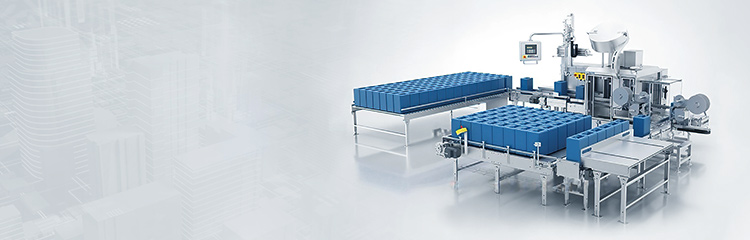
The batching control system integrates material storage, quantitative feeding, weighing, sealing and conveying, and the whole process is controlled by the microcomputer in the process of PLC control. The upper computer uses the upper computer connection command to monitor the operating status and data area content of the lower computer, read the internal status of the PLC and the real-time data of the weighing instrument in the upper computer, and display it on the upper computer. The weighing system is mainly composed of storage bin, feeding device, weighing device, conveying device, electric control cabinet and microcomputer control system, which can complete the automatic feeding of different ingredients of various materials.

In order to ensure the measurement accuracy in various environments of reactor weighing, linear compensation, zero compensation and temperature compensation are generally added to the strain gauge bridge of reactor weighing, as well as anti-corrosion treatment of the sensor surface. At the same time, in order to ensure the accuracy of remote excitation of the sensor, two wires are usually output from the excitation ends of the strain gauge to the weight transmitter or the weighing terminal, which is used to calculate the loss compensation of the excitation voltage in the long line transmission. The three pressure Weighing modules installed at the bottom of the reactor transmit the weight signal of the reactor body to the junction box. The junction box is connected in parallel with the signal of each weighing module, and the Angle difference can be adjusted according to the load condition of each weighing module. The weight signal after collection is sent to the weighing terminal or weight transmitter, which processes the weight signal into the corresponding weight data.
The weighing instrument inhales the sucked material into the hopper scale through negative pressure, weighs it and transfers it to the hopper, waits for the timing and waiting time. The PLC gives the control signal to close the feed motor, open the outlet of the hopper scale, and send the raw material to the high-mixing tank. The high-mixing motor starts the raw material to heat up in the high-mixing tank until the purpose of mixing is achieved (during the synthetic mixing process). The thermocouple converts the temperature signal value of the high mixing tank detected in real time into A digital signal through the internal A/D converter, and transmits it to the PLC. When the high mixing tank reaches the set temperature, the PLC sends out a control signal, opens the discharge port of the high mixing tank, and sends the material after high temperature chemical combination into the cold mixing tank.
The Batching system receives the status information from all other control modules through the CAN bus, and uploals it to the computer through its 232 serial port, receives the control commands from the serial port of the computer, and transmits them to the related modules connected to the bus through the CAN bus. The control functions of mixed charging are interrelated, responsible for all weighing control of the Electronic scale, and equipped with the same number of weighing modules. Formula content and weighing control parameters can be received from the computer; Receive and execute the start, pause, warehouse change and other charging orders issued by the computer; Receive weight data from weighing instruments; Depending on the formula, weight and control parameters, the feed agitator in each silo is driven for start, stop, fast, slow and pointing operations, and the scale door is driven open and closed under specified conditions to complete the weighing process, which can be equipped with the same number of weighing modules. If there is a scraper under the scale, the start and stop control of the scraper will be completed; Upload actual weighing results and alarm information.