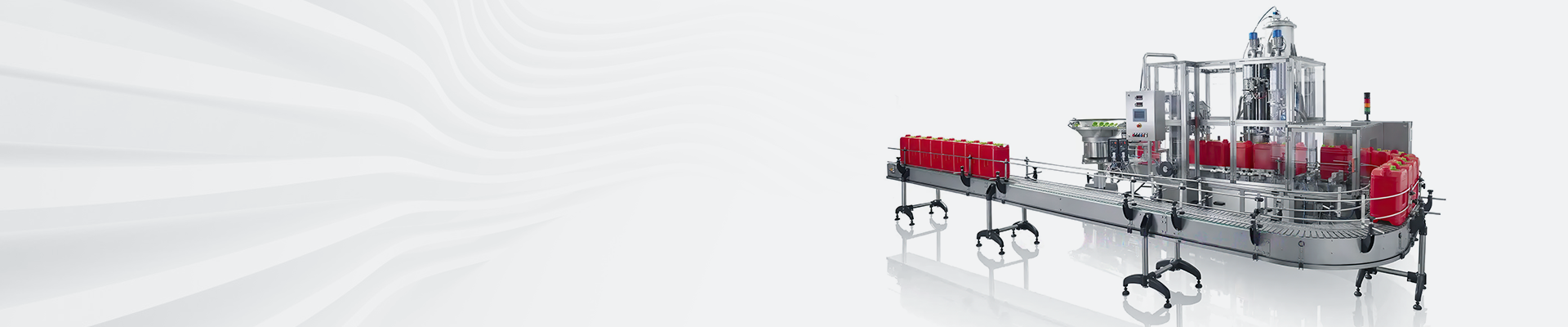
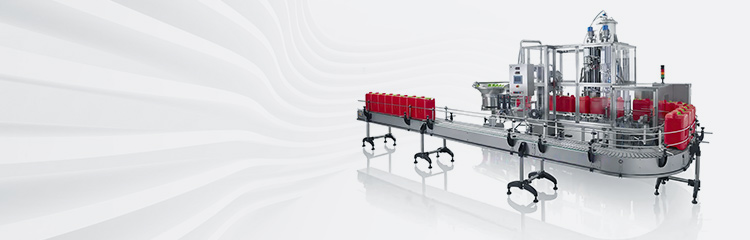

Summary:The polymer adopts advanced computer control technology and network technology as well as weighing and batching system hardware and reactor configuration, network configuration, communication, data sharing and other functions.
Polymer polymers using advanced computer control technology and network technology and weighing micro-materials system hardware and reactor composition, network configuration, communication, data sharing and other functions. After the system is put into operation, the whole weighing and dosing to realize automatic operation, and equipment operation is stable and reliable, greatly improving the production efficiency, reducing the operation of the staff, fully meet the needs of production.
I. Hardware Configuration
The weighing and feeding system consists of two levels, L1 level with PLC as the basic level, the production process for planning, setting, interlocking control; L2 level under the dosing table to realize automatic dosing. The automatic dosage system adopts centralized/distributed structure, which consists of 3 sets of Quantum controllers and 3 sets of Siemens industrial microcomputer monitoring stations to form a centralized/distributed control system, with 1 set for loading and 2 sets for feeding. Adopting MB+ network, a series of TSXMomentum is connected to the CPU processor to realize data acquisition and control of field equipment. Ring Ethernet is used to realize the sharing between PLCs and between PLCs and monitoring management level. TCP/IP protocol is used for transmission between monitoring station and server.
Software Function
1、Software configuration
The control software of weighing and batching machine consists of 3 parts: loading system, feeding system and alloy fine-tuning system after furnace. Programming software adopts Concept2.5, combining ladder logic LD control and function block FBD, defining fixed algorithm and frequently used logic into DFB block, which can be called at any time when needed. The monitoring software adopts the Client/Server structure of dual redundant network version MonitorProV7 and single board VIJEOLOOK, realizing the operation and monitoring with friendly interface and providing vivid and fast fault diagnosis system information guidance function.
2、Key Technology
(1) Accurate weighing technology
Weighing feeder from the field equipment interlock signals and load cell signals through the MB + network leads QuantumPLC, after the CPU calculations to directly control the site of the vibrating feeder. On-site weighing hopper part, the pressure head adopts 0.5 level weighing module, the weighing signal enters TSXMomentum through ISPMomentum metering module from the field bus, and then the signal is transmitted to the CPU remotely through MB + communication to complete the interlocking of the weighing and the accurate control of the vibrating feeder frequency.
(2) Token transfer mechanism between feeders
Token transfer mechanism between vibrating feeders. The weighing command controls the start of the first feeder, and the start of the subsequent vibrating feeders is controlled by the token. When the given value = 0, the vibrating feeder does not run, and directly outputs the token to the next vibrating feeder; when the given value > 0, the vibrating feeder runs according to the requirements, and outputs the token to the next vibrating feeder after weighing.
(3) Feeder speed conversion operation
Automatic weighing of the accuracy that can be achieved is the key to weighing and batching system, for this reason, the main circuit of the vibrating feeder adopts frequency converter to control the vibrating feeder first high-speed, then low-speed operation, from large to small indirectly control the flow of material. At the same time cited the weak vibration value, fall value, strong vibration speed, weak vibration speed concept, so that the vibrating feeder in the moment of stopping the flow of material as small as possible, in order to improve the accuracy of weighing.
(4) Self-healing ring network technology
Weighing mixer using dual-fiber protected fiber optic switches and optical fiber as the transmission medium to form a self-healing ring network, when a single fiber failure downstream node interface circuit to achieve the ring back, such as when the left side of the optical receiver no signal, the right side of the optical transmitter to select the same side of the optical receiver data forwarding. This self-healing function ensures that the continuity of the ring can still be maintained in case of failure.