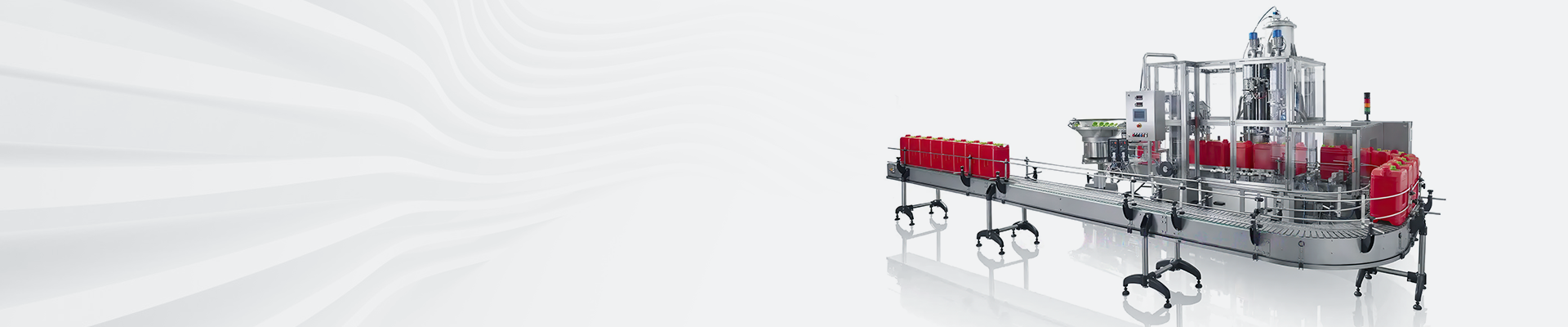
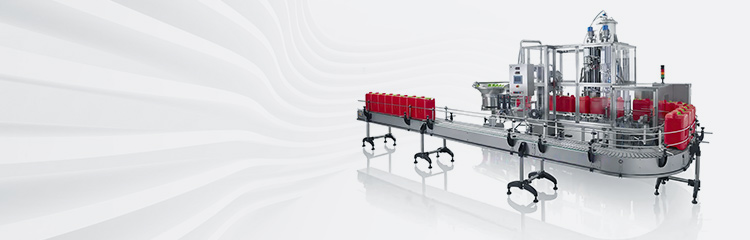

Summary:The reactor weighing and batching system realizes the management and control of on-site production, data viewing analysis and historical records, viewing of all data in the production process, and an overall understanding of the entire production.
Reaction kettle weighing refers to the heating device required to realize the expected physical changes in the process of batching, processing of raw materials or manufacturing of finished products. At present, China's reaction kettle industry has a large consumption of heat transfer oil, serious waste, and there is a general problem of high energy consumption. This is mainly due to the greater labor intensity of workers, backward means of regulation, it is difficult to ensure the ideal dosage conditions. Therefore, improving the automatic batching system and control level has great potential for energy saving.
Weighing feeding system is also known as the reactor base automation, the size of the batching machine according to the reactor type, reaction tank size, generally including electrical automation, batching automation and cooling automation. For large-scale step heating reactor, the above system is indispensable; for small-scale heating reactor, heat treatment reactor, electrical automation content is very little, mainly automatic dosage system using PLC and related temperature control instrumentation, to meet the process of automatic dosage requirements, but also saves the cost of the project, but also to complete the process parameters of the collection, control and communication functions. Therefore, the automatic weighing and feeding system established by connecting PLC and temperature control instrument table with the upper computer is the most feasible way at present.
This solution adopts the configuration king software as the upper software, the bottom connects the PLC, temperature control instrument meter, sensor and so on to form the feeding system, for the characteristics of the reactor industry, with the report, temperature control curve as the core, optimize the production control of the reactor, in order to achieve the optimization design of energy saving and emission reduction.
2.Automatic batching demand
The reaction kettle can be divided into 5 categories according to the industry usage (refer to the classification of "Reaction Kettle Manual"): resin reaction kettle, special reaction kettle for paint, special reaction kettle for polyester, special reaction kettle for glue and special reaction kettle for laboratory. According to the application: in the dosage workshop, there are electric heating kettle, self-control kettle, polymerization kettle, magnetic kettle, vacuum kettle, horizontal kettle, mixing kettle and so on for stirring and mixing, and there are blending dosage kettle, stainless steel kettle and compartment kettle and so on; in the mixing workshop, there are all kinds of heating kettles for resin or raw materials to be heated before dosage, and there are heating kettles for iron powder in powder workshop, and so on. In the powder workshop, there are heating kettles for iron powder, etc. Reaction kettle industry reaction kettle subtypes, the site production environment is generally more complex than a variety of production processes are also different, for the production management focus is also very different, but for the reaction kettle production of automatic dosage system requirements are more urgent.
According to the current production of dosage process summarized in the general process flow:
According to the kettle feeding machine production process, control needs are mainly the following aspects
1) According to the technical requirements of the process, to comply with the principle of high reliability, economy and simplicity.
2) The whole operation process can realize remote monitoring, control and management by computer to realize high quality, low cost, stable and reliable operation.
3)Require perfect report function. It can conveniently set up shift report, daily report, monthly report and yearly report, completely record the production project information, provide complete equipment operation data record and display (flow control, pressure control, vacuum degree of the equipment, etc.), real-time report displaying all kinds of operation information in the operation of the project, and historical report querying the history conditions for the parameters of the production process. Provide graphical display and trend curve display of data, provide real-time display and historical display of data alarms, and be able to generate reports in the form of.
(4) weighing mixer can complete the kettle temperature measurement and automatic control, can be set for different production materials, different temperature control process and record. In the reactor production process, the need to achieve the set temperature of the real-time settings, while monitoring the feedback temperature signals, in the form of a curve on the control of the synchronization of the refreshing, able to intuitively show the temperature control process. Therefore, the control is required to realize the combination with the temperature control instrument. Through the temperature control control report to transfer the set parameters to the temperature control instrument table, temperature control by the temperature control instrument table for temperature control, to realize the configuration monitoring.
(5) The product batch management function, batch management refers to the product from the raw material input to the delivery of the entire manufacturing process, the implementation of scientific management strictly according to the batch. Most of the production materials of the reactor are required for quality traceability, and the quality of the finished product is widely reflected in the flow of processes, so batch management is a very common requirement. Such as resin dosage of a reactor times, for the metal content of the quality requirements; heat treatment of a reactor times, for the hardness and organization requirements. In the automatic control system, the system is required to be able to produce detailed batch records for the production process of different materials, in order to facilitate the quality of the later traceability; able to provide detailed experience production process for different production materials.
(5) Requirements for feeders with alarm functions, can carry out real-time alarm prompts, can realize the sound alarm notification, remote information alarm notification prompts, can store and query the historical alarm information. Can view and modify the alarm parameters of each system variable in the control process.
(6) Realize man-machine dialogue, can modify process parameters, and display temperature, time and other main parameters, can be combined with the temperature control instrument to realize the PID parameter adjustment, and can be run in the system PID parameter setting and calculation.
(7) It can realize the dynamic simulation display of the working state of the reactor, which can intuitively display the current production and operation state of the reactor, as well as the current values of various control parameters on the reactor body.
(8) It can provide client remote data access function. Through the client tool, it can monitor the operation status of remote equipment through the network to ensure that the remote equipment is running normally. The real-time, historical and alarm data can be released in an integrated way in the Internet network or LAN, so that users can realize browsing in IE.