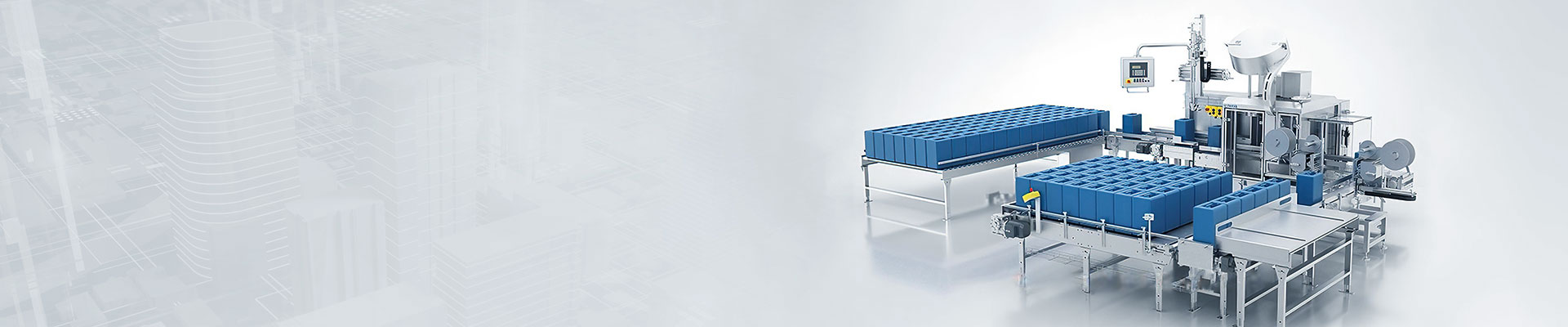
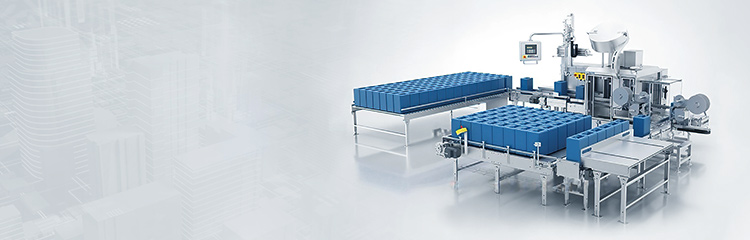
The overall composition of the dosage system is that the host and the slaves (including the virtual host) are connected via serial bus, and the virtual host and the slaves are also connected via serial bus, constituting the master-slave microcomputer dosage of the dual-bus structure, the host realizes the control of the dosage through the serial president, and the virtual host realizes the control of the dosage through the serial bus after obtaining the right to control the system, and the host mainly completes the control of the process, real-time display and alarm, and provides data storage. The host mainly accomplishes the functions of process control, real-time working condition display and alarm, data storage, report printing, recipe optimization and management consulting.

The automatic dosing system is a kind of high production efficiency, high precision and fully automatic dosing auxiliary machine system developed for rubber, feed, food, pharmaceutical, chemical and other industries. The system has the function of fully automatic weighing and distribution of powder (carbon black, etc.), granule (paraffin, etc.), oil and other materials according to the required production formula, which can be adapted to different specifications of 75~150L refiner, mixer, extruder, etc., and is mainly applicable to the production of large and small material formulas, smartly storing production formulas, recalling production formulas at any time and storing production data, which can help product quality tracing. The batching equipment can continuously and automatically complete the following operations for powder, granule, block and bulk materials in various industrial production environments: full-automatic weighing of trace substances, full-automatic dosing and full-automatic conveying and controlling. Its stable and reliable performance, intelligent and accurate, will greatly improve the efficiency of the industrial production of trace substances Dosage system, at the same time completely eliminated the trace substances of manual weighing and dosage, feeding the error rate may occur. Additives trace component computer dosing and adding system can improve feed additives trace component dosing accuracy and dosing and weighing efficiency, completely overcome a variety of human error, to avoid a variety of feed additives dosing and weighing and adding accidents, and greatly reduce all kinds of economic losses due to the micro-component dosage and weighing, and can significantly improve the production efficiency of the feed mill, to realize the feed additives trace component dosage, weighing and adding safety, high quality, clean and safe. It can significantly improve the production efficiency of feed mills and realize the safety, high quality, cleanliness and high efficiency of feed additive micro-component dosing, weighing and adding. The traditional mixing process is to weigh the ingredients manually, put them into the mixing unit, and the mixed materials are carried to the extruder manually, which is suitable for small factories with only a few lines. For large-scale production plants, this method has many disadvantages:
1. Manual batching, easy to make mistakes. Weighing and batching is a mechanical and boring repetitive action, workers are easily fatigued, and the wrong material, resulting in fluctuations in the product qualification rate.
2. Labor intensity, high labor costs.
3. The related chemical raw materials are hazardous to the operator's health.、 4. The advantages of weighing and dosage system are:
1. The automatic dosage system controlled by computer improves the accuracy and efficiency of dosage, and reduces the chemical hazards to the operator.
2. Pipeline conveying reduces the labor cost and improves the production efficiency, and in addition, the materials are conveyed in the closed pipeline to avoid the pollution of the environment of the workshop by the dust.
3. Other functions of the Weighing system:
1, real-time display of the dosage status;
2, with dosage statistics, traceable;
3, can save the formula, adjust the range function;
4, with operating records query, easy to trace responsibility;
5, with operating privileges;
6, with real-time reports, alarms; automatic dosage system is mainly applicable to large and small material formula production, intelligent storage of production formulas, call at any time the production of formulas, storage of production data, etc., to help product quality traceability. Automatic dosage system process characteristics:
1. Reduce the contact opportunity between workers and chemical raw materials, greatly reduce the number of workers, reduce labor intensity, improve the health protection of workers.
2. Avoid the influence of human factors on the dosage operation, to ensure the stability of product quality, improve the product quality of the factory and efficiency.
3. Automatic dosage system according to the characteristics of the raw materials, the use of different feeding mechanisms and control algorithms, improve the dosage The automatic dosage system adopts different feeding mechanism and control algorithm according to the characteristics of raw materials to improve the dosage efficiency and meet the production requirements.
4. The automatic dosage system adopts Feeder speed control technology to meet the minimum dosage of raw materials and precision requirements.
5. The control system automatically saves the record of each weighing and the batch number of raw materials used to realize the traceability of the quality.
6. Reliable control devices and professional mechanical processing ensure the stability of the system; the abnormal alarm function ensures the reliability of the dosage.
7. The operation can complete a batch of dosage just by pressing the button. Batching technical parameters:
1. Batching capacity: 6~50 kinds of materials, applicable to a variety of formulas;
2. Single material distribution capacity: 50g~200kg;
3. Storage bin capacity: 1~20m3;
4. Dosing accuracy: ±1g, 2g, 5g, 10g, 20g;
5. Dosing speed: 5 to 30 minutes a batch, a batch of 10 barrels (the number of barrels can be set);
6. Power supply of the control system: AC220V 50Hz; 7. Power supply of the control system: three-phase AC380V 50Hz; 8. Input air pressure: ≥0.35Mpa;