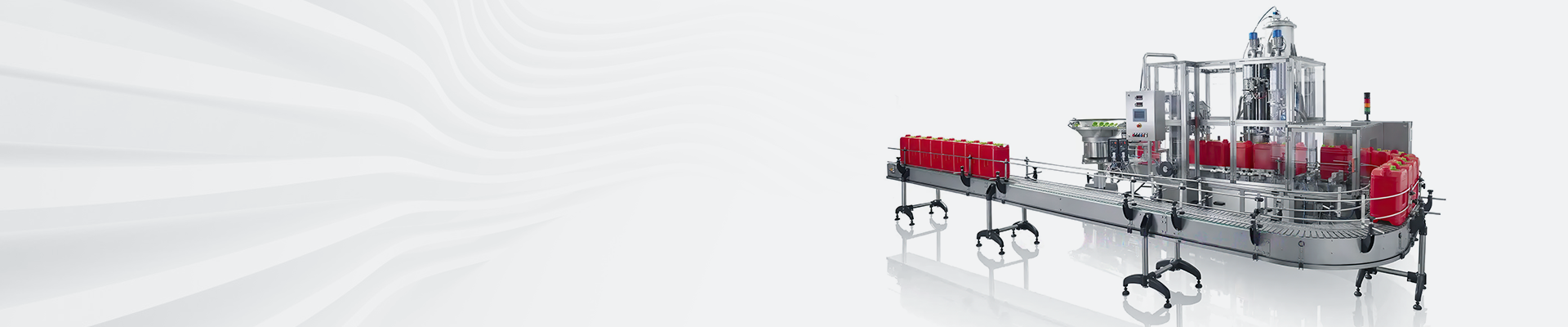
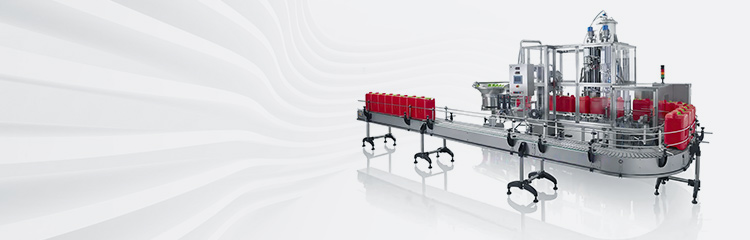

Summary:The batching system takes PLC as the core. Through the control of frequency converters, variable frequency motors, electromagnetic regulating valves, unloading valves, mixers and other batching equipment, the feeding control batching equipment is required to be able to adjust in a timely manner according to the amount of material used. , realizing automatic control of quantitative mixing of materials.
Sintering is one of the important links in iron and steel production, including raw materials, batching, mixing, sintering and finished products and other subsystems. Among them, the batching process determines the raw material proportion of the sintered ore, which has an important influence on the quality of the finished sintered ore and even the blast furnace running and the quality of the iron. The batching system has high requirements on the control system, and it is difficult to control the production process effectively by using single-loop instrumentation control in the past. In this paper, PLC is used for the control of the batching system, and better results have been achieved.
1 batching system process requirements
In the sintering system, the dosing system is very critical, its main function is to calculate, allocate and control the amount of raw material slots in accordance with the sintering production demand for a variety of materials, so as to ensure that the material balance of raw materials and sintered minerals meet the requirements of the chemical composition of the finished ore. In the dosing process, the main process requirements of the control system are as follows.
(1) Realize single start-stop and linkage start-stop of each feeder, belt scale and aggregate belt, and realize fault interlock;
(2) Control the ratio of the amount of material discharged from each batching chute;
(3) Calculation of raw material proportion. Calculate the flow rate setting value of each ore tank according to the total amount of material discharged and the proportion of each ore tank;
(4) Flow calculation. According to the weight detection value of the belt scale belt speed detection value, to calculate the average flow rate of materials in a certain period of time and the average flow rate as a feedback value for PID regulation;
(5) Troubleshooting. The actual production of high-frequency faults (such as clogging, belt slippage, motor overload) and so on to set sound and light alarms. Requirements for the automatic start of the vibration motor on the hopper when the blockage occurs, and should be automatically stopped after resuming the material. If the material is blocked for a long time (more than the set time value after starting the vibration motor), the air cannon should be started automatically to clear the blockage;
(6) system hot standby. Requirements for the system host computer has a hot standby function, that is, each host computer can simultaneously monitor the system's PLC;
(7) Printing reports. Manual printing and automatic printing of reports at regular intervals, including the Times, Shift Reports, Monthly Reports and so on.
(8) Power failure protection. The system is initialized and reset when power is restored after power failure to ensure that each device is in the shutdown state to prevent personal accidents or equipment accidents.2 Dosing control system
2.1 System composition
The upper computer and PLC of the automatic dosage system are connected through MPI or Ethernet, the lower computer adopts SIMATICS7 programmable controller from SIEMENS, and the upper computer adopts Advantech industrial computer (IPC).
The software part of the feeding system configuration includes STEP7 programming software and SIMATICWinCc human-machine interface monitoring software. STEP7 is used for PLC programming, debugging and program monitoring, while SIMATICWinCc is used for writing and running human-machine interface.
2.2 Control principle
The weighing module detects the weight of materials in the weighing area and outputs a DC millivolt signal proportional to the weight, which is then converted into a 4~20mA DC signal through a DC millivolt transmitter and sent to the analog-to-digital converter (A/D) module. The encoder is used to measure the rotational speed of the belt scale motor, and the output rotational speed signal is sent to the PLC. assuming that the weight of the material in the effective weighing section of the belt scale at a certain moment is W, the linear speed of the belt is V, and the length of the effective weighing section is work, the instantaneous flow rate of the material is F = 1/Lx.
Flow rate is F = 1/LxWxV according to the formula, can be calculated at each sampling moment of the instantaneous amount of material in a slot, and further calculated for a period of time the average amount of material in this slot. Compare the obtained average discharging volume with the given value of discharging volume set by the operator, and then carry out PID regulation operation to get the control volume, and finally output 4~20mA DC signal through digital-to-analog converter (D/A) module, which will be sent to the speed adjustment terminal of the inverter, and control the inverter to change the output frequency and other parameters, so as to change the speed of the motor of the disk feeder, thus controlling the discharging speed.
2.3 Software Design
STEP7 series instruction system is powerful, there are rich control instructions and operations, control instructions, data types including integer, real number type, etc., so that the program control program is written more flexible and convenient. In order to facilitate the operator's understanding and monitoring, the main program of the control software is written in ladder diagram, and the sub-programs are written in ladder diagram or SCL language. In the process of program writing follow the structured, modular principles based on the independence of the function of the division of subroutines, the function of the relatively independent part of the function is written as a function (FC) or function block (FB), and try to avoid contact between them. The main program is to call each subroutine, according to different conditions to complete the corresponding function.PLC control program mainly includes.
(1) Main program;
(2) Sequence control;
(3) Flow calculation;
(4) Proportioning calculation;
(5) PID regulation;
(6) Troubleshooting.
In addition, the CPU will automatically call the fault routine subroutine during power-on reset to complete the power-on protection. In the dosing control program, the digital filter subroutine in the flow calculation plays an important role in the actual production. Due to the characteristics of the disk feeder itself, the instantaneous value of the discharging flow rate will always fluctuate, often resulting in a large change in the instantaneous flow rate. If the instantaneous flow rate is used directly as the feedback quantity for PID regulation, it will lead to fluctuations in the regulation process, which is not easy to be smooth, and in serious cases, oscillation or even dispersion may occur. Therefore, we through the digital filter subroutine for a period of time to take the average of the sampling value of the amount of material to calculate the average of the material during this period of time, and use this as the feedback value.
In the upper computer, WinCc is used to write the control interface, which mainly accomplishes the functions of parameter setting, modification, monitoring and recording.
2.4 Operation effect
During the operation period, the batching system is in good working condition. After calibration test, the system measures accurately, each disk feeder adjusts fast, and the control precision meets the expected requirements. Production practice shows that, under the condition that the material state (particle size, moisture, etc.) meets the requirements, the feeding accuracy of concentrate powder reaches plus or minus 1.5%, and the feeding accuracy of the rest of the materials reaches plus or minus 1%, which is able to satisfy the requirements of sintering batching process well.
After a period of operation, the system has proved to be simple and intuitive to operate, and reliable in performance.
During the operation period, the working condition of the batching system is good. After the calibration test, the system is accurate in measurement, and the adjustment speed of each disk feeder is fast, and the control accuracy meets the expected requirements. Production practice shows that, under the condition that the material state (particle size, moisture, etc.) meets the requirements, the feeding accuracy of concentrate powder reaches within plus or minus 1.5%, and the feeding accuracy of the rest of the materials reaches within plus or minus 1%, which is able to satisfy the requirements of sintering batching process better. After a period of operation proved that the system operation is simple and intuitive, reliable performance.
3 Conclusion
The feeding system can achieve better results in terms of precision, stability and some other control system quality indexes, especially in the automatic tracking of total amount of dosage and balance control of material in the ore tank, which plays a good role in ensuring normal working conditions and improving product output and quality.