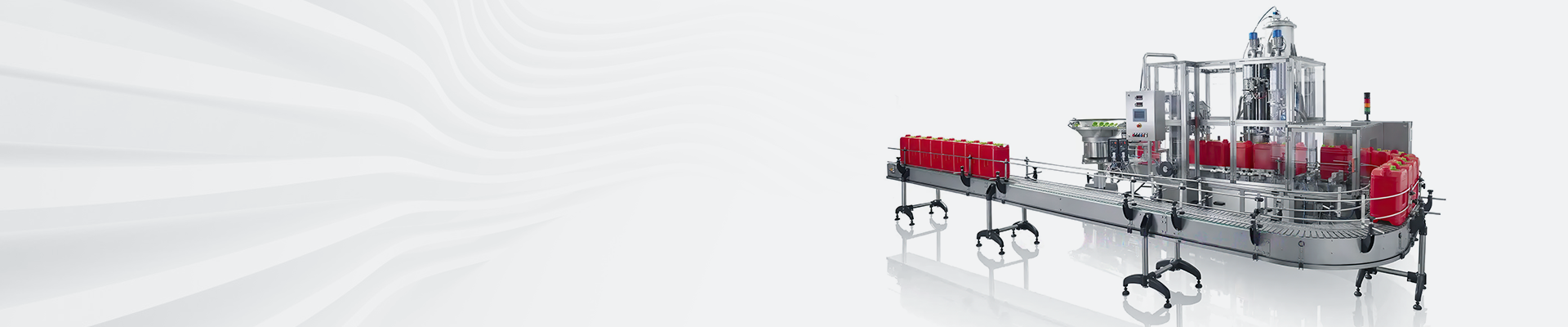
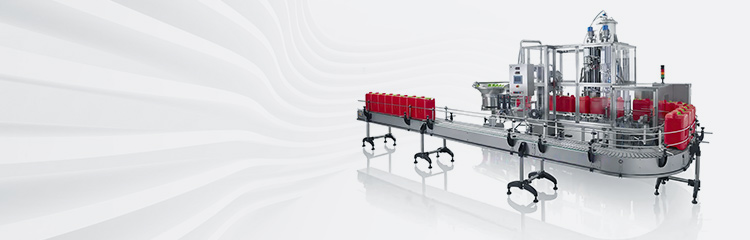
摘要:配料系统以PLC为核心,通过对变频器、变频电机、电磁调节阀、下料阀、搅拌机等配料设备的控制,在给料时要求给料控制配料设备能够根据用料量的大小来适时调节,实现了对物料的定量混合搅拌的自动控制。
0引言
烧结是钢铁生产中的重要环节之一,包含原料、配料、混料、烧结和成品等子系统。其中,配料过程决定了烧结矿原料配比,对成品烧结矿的质量乃至高炉顺行和铁水质量有着重要影响。配料系统对控制系统的要求高,过去采用单回路仪表控制,难以有效地控制生产过程,本文采用PLC进行配料系统的控制,取得了较好的效果。
1配料系统工艺要求
在烧结系统中,配料系统非常关键,它的主要功能是按照烧结生产对各种物料的的需求量来计算、分配、控制各个原料矿槽的下料量,从而保证原料的物料平衡和烧结成品矿的化学成分符合要求。在配料过程中,对控制系统的主要工艺要求如下:
(1)实现各个给料机、皮带秤和集料皮带的单机起停和联动起停,并实现故障联锁;
(2)控制各个配料矿槽下料量的配比;
(3)原料配比计算。根据总下料量和各个矿槽的配比来计算每个矿槽的流量设定值;
(4)流量计算。根据皮带秤的重量检测值皮带速度检测值,来计算一定时间段内的物料平均流量并以此平均流量作为反馈值来进行PID调节;
(5)故障处理。对实际生产出现频率较高的故障(如堵料、皮带打滑、电机过载)等设置声光报警。要求出现堵料时自动启动料斗上的振动电机,恢复下料后应自动停止。如果长时间(启动震动电机后超过设定时间值)堵料,则应自动启动空气炮清堵;
(6)系统热备。要求系统上位机具有热备功能,即每台上位机可同时对系统的各PLC进行监控;
(7)打印报表。人工打印和定时自动打印报表,包括时报、班报、月报等
(8)断电电保护。断电电后重新上电时,系统进行初始化复位,确保各台设备均处于停机状态,防止出现人身事故或设备事故。2配料控制系统
2.1系统组成
自动配料系统的上位机和PLC通过MPI或以太网进行连接,下位机采用SIEMENS公司的SIMATICS7可编程控制器,上位机采用研华工控机(IPC)。
投料系统配置的软件部分包括STEP7编程软件和SIMATICWinCc人机界面监控软件。STEP7用于PLC编程、调试和程序监控,而SIMATICWinCc则用于编写和运行人机交互界面。
2.2控制原理
称重模块对称量区域内的物料重量进行检测,输出与重量成正比的直流毫伏信号,然后通过直流毫伏变送器变换为4~20mA直流信号,并送到模数转换(A/D)模块。利用编码器测量皮带秤电机转速,并将输出的转速信号送入PLC。假设某一时刻皮带秤有效称量段中的物料重量为W,皮带的线速度为V,有效称量段的长度为工,则该时刻物料瞬时
流量为F=1/LxWxV根据式,可以计算出每一采样时刻某矿槽的瞬时下料量,并进一步计算出某一段时间内这一矿槽的平均下料量。将得到的平均下料量与操作员设定的下料量给定值进行比较,再进行PID调节运算,得到控制量,最后通过数模转换(D/A)模块输出4~20mA直流信号,送人变频器速度调节端子,控制变频器改变输出频率等参数,从而改变圆盘给料机电机转速,从而对下料速度进行控制。
2.3软件设计
STEP7系列指令系统功能强大,有丰富的控制的指令和运算、控制指令,数据类型包括整型、实数型等,使程控制程序的编写更加灵活、方便。为了便于操作人员理解和监控,控制软件主程序采用梯型图编写,子程序采用梯形图或SCL语言编写。在程序编写过程中遵循结构化、模块化原则依据功能的独立性划分子程序进行,把功能相对独立的部分编写为一个功能(FC)或功能块(FB),尽量避免它们之间产生联系。而主程序则对各个子程序进行调用,依据不同条件完成相应的功能。PLC控制程序主要包括:
(1)主程序;
(2)顺序控制;
(3)流量计算;
(4)配比计算;
(5)PID调节;
(6)故障处理。
此外,CPU在上电复位时将自动调用故障例行子程序,完成上电保护。在配料控制程序中,流量计算中的数字滤波子程序在实际生产中起重要作用。由于圆盘给料机本身的特性,下料流量的瞬时值会一直存在波动,经常造成瞬时流量的大幅度变化。如果直接以瞬时流量作为反馈量来进行PID调节,会导致调节过程产生波动,不易平稳,严重时可能发生震荡甚至发散。因此,我们通过数字滤波子程序对一段时间内的下料量采样值取平均值,来计算这段时间内的平均下料,并以此作为反馈值。
在上位机中采用WinCc编写控制界面,主要完成参数的设定、修改、监控和记录等功能。
2.4运行效果
运行期间,配料系统工作状况良好。经标定测试,该系统计量准确,各圆盘给料机调节速度快,控制精度达到预期要求。生产实践表明,在物料状态(粒度、水分等)符合要求的条件下,精矿粉下料精度达到正负1.5%以内,其余物料下料精度达到正负1%以内,能够较好地满足烧结配料工艺要求。
经过一段时间的运行证明,该系统操作简单直观,性能可靠。
运行期间,配料系统工作状况良好。经标定测试,该系统计量准确,各圆盘给料机调节速度快,控制精度达到预期要求。生产实践表明,在物料状态(粒度、水分等)符合要求的条件下,精矿粉下料精度达到正负1.5%以内,其余物料下料精度达到正负1%以内,能够较好地满足烧结配料工艺要求。经过一段时间的运行证明,该系统操作简单直观,性能可靠。
3结语
本上料系统在精度、稳定性及其他一些控制系统质量指标,尤其是配料总量自动跟踪、矿槽物料平衡控制方面,能够达到较好的效果,对保证工况正常,提高产品产量、质量发挥了良好的作用。