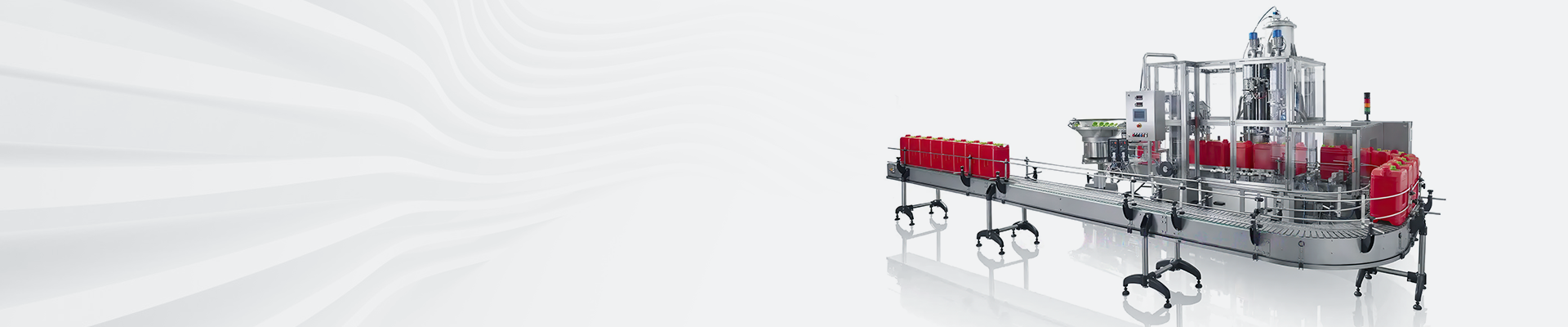
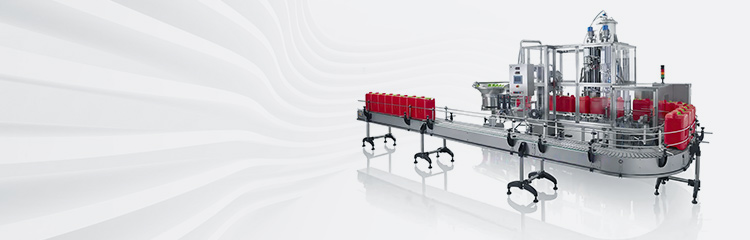
摘要:反应釜自动配料系统采用PLC技术,具有回路控制、逻辑控制、监控、计量等功能。实现原料流量的连续稳定控制;顺序启停和联锁控制;数据的实时监视;计量系统对进行在线计量。计算机网络与实时数据库的支持,保证反应釜配料生产过程的控制、运行和管理。
反应釜配料是树脂生产流程中对原料进行处理的重要工序。该过程中,原料等原料被输送到反应釜中进行混合、研磨后形成生料浆。生料浆的各项工艺指标直接影响着最终树脂产品的质量。目前的反应釜配料过程基本停留在自动化程度低,依靠人工操作的水平上,从而导致生产效率低,能源消耗大,生料浆的各项工艺指标合格率低,成为制约树脂生产的瓶颈。
为解决这一问题,根据反应釜配料过程的工艺特点和技术要求,本文采用西门子公司的S7-300PLC设计并开发了反应釜配料过程的自动投料系统。根据上料系统的功能和要求对硬件平台进行了设计和选型,并采用Step-7系统开发了逻辑控制程序、连续控制程序,采用MCGS系统开发了监控画面。本文所设计和开发计量配料系统可以应用在实际的树脂反应釜配料过程中,取代现有的人工操作方式,因此可以提高生料浆产品质量,并节能降耗,为企业创造更多的效益。
1自动配料系统的硬件设计
反应釜配料过程采用PLC自动配料技术,具有回路控制、逻辑控制、关键工艺参数的监控、计量等功能。回路控制实现原料等原料重量的连续稳定控制;逻辑控制实现关键配料设备的顺序启停和联锁控制;关键工艺参数的检测与显示实现过程数据的实时监视;计量系统对各种物料的重量进行在线计量。通过控制系统软件和监控系统软件提供的强大组态功能,计算机网络与实时数据库的支持,保证反应釜配料生产过程的控制、运行和管理。
根据反应釜配料过程的工艺流程及混合系统的功能要求,系统中共有65点数字量输入(DI)和20点数字量输出(DO),20点模拟量输入(AI)和17点模拟量输出(AO)。
采用西门子S7-300PLC,同时还需扩展模块。扩展模块包括3个SM321(32点数字量输入),1个SM322(32点数字量输出),3个SM331(8通道模拟量输入),3个SM332(8通道模拟量输出)。
反应釜配料中包括多个原料质量的控制回路,以原料重量控制回路为例,该控制回路的电气和仪表设备主要包括PLC,变频器,密度计和称重模块等。
2称重控制系统开发
称重控制系统软件包括各种逻辑控制程序、各种重量控制程序以及监控画面等等。逻辑控制和连续控制程序采用SiemensS7-300PLC中的Step7系统开发。监控画面采用组态系统软件MCGS系统开发。
逻辑控制程序主要完成原料泵、各种给料皮带秤的启停控制和相关设备的联锁保护等功能。
重量控制程序完成各种原料重量的手动和自动控制,使各种原料的实际重量准确、稳定的跟踪相应的设定值。
监控画面主要有两方面的功能:一是监视设备的状态,包括设备的运行、停止和故障等;二是控制设备的状态,包括设备的启停、参数的设定等。通过对监控画面的操作,可以使操作员随时对现场生产过程进行操作指导及控制。
2.1逻辑控制程序
以原料泵为例,启动和停止程序,启动条件:变频器处于自动控制,变频器已交流合闸,变频器没有故障,电机没有故障。
停止条件:液泵处于自动控制方式。自动停车条件:变频器故障或电机故障。
2.2连续控制
连续控制是指各种原料的重量控制回路,主要包括5个原料重量的回路控制。
2.3监控画面的开发
根据配料功能要求,本文采用MCGS系统开发了多个监控画面,不仅具有丰富的功能,同时具有良好的人机互动性,典型的监控画面。为反应釜配料过程的主监控画面。通过该画面可以全面的掌握整个配料过程中各个设备的运行情况,并可以切换到其他画面上完成相应的功能。为反应釜系统的监控画面,在该监控画面中不但可以通过按钮对相应的设备进行启动和停止,还可以对物料的给定值进行设定。
3结论
本文采用西门子公司的S7-300PLC设计并开发了反应釜配料过程的配料系统,包括硬件设计和称重系统开发等。该系统通过逻辑控制部分完成对条件的判断及设备的启停顺序控制、实现联锁保护功能,保证设备的安全运行,延长其使用寿命。通过连续控制对各种原料的重量进行控制,保证被控变量准确稳定的跟踪设定值。过程监控部分保证监控画面的直观性、友好性,操作员可以方便地实现过程监控、重要参数的记录及显示、异常情况的处理等,达到人机优势互补的目的。该自动配料机可以取代传统的人工配料生产方式,提高了生料浆各项工艺指标的合格率,降低了配料成本,实现了自动配料,从而提高了企业的竞争力。