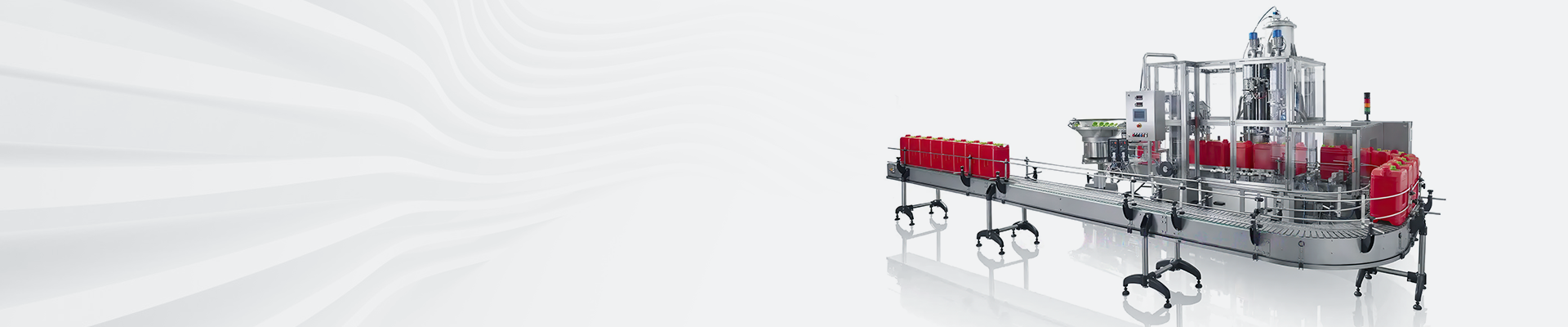
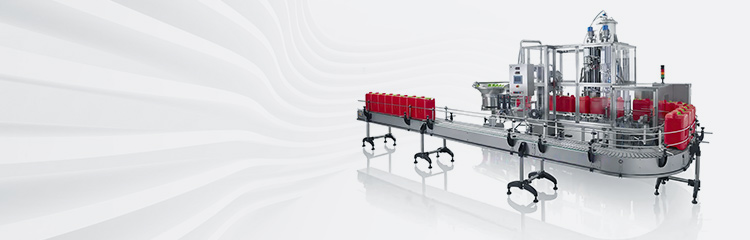

Summary:The automatic batching system of the reactor adopts PLC technology and has functions such as loop control, logic control, monitoring, and measurement.Realize continuous and stable control of raw material flow; sequential start-stop and interlock control; real-time monitoring of data; and online measurement by the metering system.The support of computer network and real-time database ensures the control, operation and management of the reactor ingredient production process.
Reactor dosing is an important process for handling raw materials in the resin production process. In this process, raw materials and other raw materials are transported to the reactor for mixing and grinding to form raw slurry. The process indexes of the raw slurry directly affect the quality of the final resin product. The current kettle dosing process basically stays in the low degree of automation, relying on the level of manual operation, which leads to low production efficiency, energy consumption, the raw slurry of the various process indicators of the qualification rate is low, and become a bottleneck to restrict the production of resin.
In order to solve this problem, according to the process characteristics and technical requirements of the reactor dosing process, this paper adopts Siemens S7-300 PLC to design and develop the automatic feeding system of the reactor dosing process. According to the functions and requirements of the feeding system the hardware platform was designed and selected, and the Step-7 system was used to develop the logic control program, continuous control program, and the MCGS system was used to develop the monitoring screen. The metering and dosing system designed and developed in this paper can be applied in the actual resin reactor dosing process, replacing the existing manual operation method, so it can improve the quality of raw slurry products and save energy and reduce consumption, creating more benefits for the enterprise.
1 automatic dosage system hardware design
Reactor dosing process using PLC automatic dosing technology, with loop control, logic control, monitoring of key process parameters, measurement and other functions. Loop control realizes the continuous and stable control of the weight of raw materials and other raw materials; logic control realizes the sequential start-stop and interlock control of the key dosing equipment; detection and display of key process parameters realize the real-time monitoring of the process data; metering system carries out on-line measurement of the weight of various materials. Through the powerful configuration function provided by the control system software and monitoring system software, the computer network and real-time database support to ensure the control, operation and management of the kettle batching production process.
According to the process flow of kettle batching process and the functional requirements of the mixing system, there are 65 points of digital input (DI) and 20 points of digital output (DO), 20 points of analog input (AI) and 17 points of analog output (AO) in the system.
A Siemens S7-300 PLC is used, and expansion modules are also required. The expansion module includes 3 SM321 (32-point digital inputs), 1 SM322 (32-point digital outputs), 3 SM331 (8-channel analog inputs), and 3 SM332 (8-channel analog outputs).
The reactor dosage includes several control loops of raw material quality, taking the raw material weight control loop as an example, the electrical and instrumentation equipment of this control loop mainly includes PLC, frequency converter, densitometer and weighing module.
2 Weighing control system development
The software of weighing control system includes various logic control programs, various weight control programs and monitoring screens. Logic control and continuous control programs are developed by SiemensS7-300PLC in Step7 system. The monitoring screen is developed by the configuration system software MCGS system.
The logic control program mainly completes the functions of starting and stopping control of raw material pumps, various feeding belt scales and interlock protection of related equipment.
The weight control program completes the manual and automatic control of the weight of all kinds of raw materials, so that the actual weight of all kinds of raw materials accurately and stably tracks the corresponding set value.
The monitoring screen has two main functions: one is to monitor the status of the equipment, including the operation, stopping and malfunctioning of the equipment; the other is to control the status of the equipment, including the starting and stopping of the equipment and the setting of parameters. Through the operation of the monitoring screen, the operator can guide and control the on-site production process at any time.
2.1 Logic control program
Take the raw material pump as an example, start and stop the program, start conditions: the frequency converter is in automatic control, the frequency converter has been AC closed, the frequency converter is not faulty, the motor is not faulty.
Stop conditions: liquid pump is in automatic control mode. Automatic stop conditions: inverter failure or motor failure.
2.2 Continuous control
Continuous control refers to the weight control loop of various raw materials, which mainly includes the loop control of 5 raw material weights.
2.3 Monitoring screen development
According to the functional requirements of dosage, this paper adopts MCGS system to develop a number of monitoring screen, which not only has rich functions, but also has good human-computer interaction, typical monitoring screen. Typical monitoring screen is the main monitoring screen of the dosage process of the reactor. Through this screen, you can fully grasp the operation of each equipment in the whole dosage process, and can switch to other screens to complete the corresponding functions. It is the monitoring screen of the reactor system, in which you can not only start and stop the corresponding equipments by buttons, but also set the given value of the material.
3 Conclusion
This paper adopts Siemens S7-300PLC to design and develop the dosage system of reactor dosage process, including hardware design and weighing system development. The system completes the judgment of the conditions and the start-stop sequence control of the equipment through the logic control part, realizes the interlock protection function, ensures the safe operation of the equipment and prolongs its service life. The weight of various raw materials is controlled through continuous control to ensure that the controlled variables accurately and stably track the set values. The process monitoring part ensures the intuitiveness and friendliness of the monitoring screen, so that the operator can conveniently realize the process monitoring, recording and displaying of important parameters, handling of abnormal situations, etc., and achieve the purpose of complementing the advantages of man and machine. This automatic batching machine can replace the traditional manual batching production method, improve the qualification rate of all process indexes of raw slurry, reduce the cost of batching, and realize automatic batching, so as to improve the competitiveness of the enterprise.