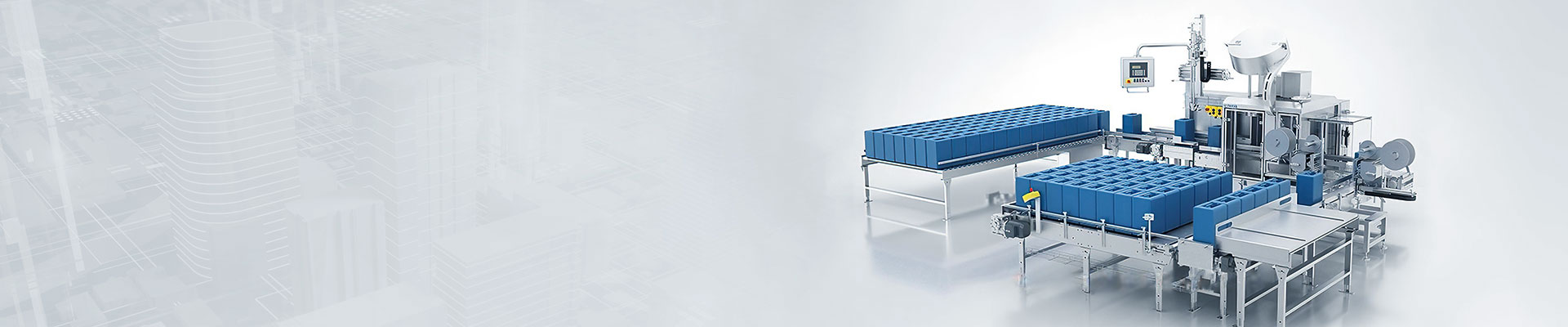
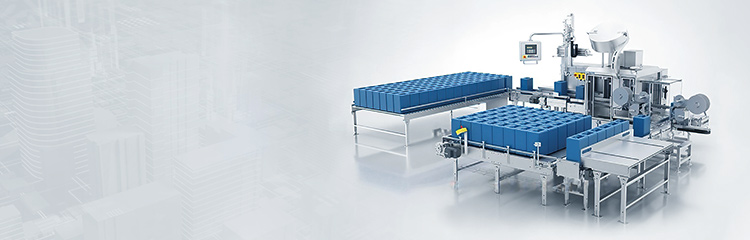
Plastic batching system can realize automatic weighing and feeding, flange connection to avoid dust leakage during mixing. The unique nitrogen supplement device can be used in chemical plants with high explosion-proof requirements. The vacuum pump creates vacuum through the separation container of the vacuum conveying equipment. The material is drawn from the feed port through the suction hose and suction port. The air is separated from the material in the filter bin of the separation vessel and the material is collected in the weighing bin.

Hopper scale as a metering control device for material ingredients, this is a metering equipment composed of barrel containers, bucket container is fixed on the weighing module as a whole, on the bottom of its side is installed a door that can be opened and closed by electromagnetic pneumatic valve, for regular quantitative discharge and feeding (when the hopper door is open, the material in the bucket scale is discharged, when the hopper door is closed, Material can be accessed from above via an electric vibrator or a spiral knife). Bucket scale has the advantages of simple structure, convenient manufacture, low failure rate and high batching precision, which can meet the requirements of batching production technology.
The feeding system is connected by 100M fast industrial Ethernet, the system network is redundant, and the power supply and main control unit of the field control station are redundant. In software design, on-site manual control, master control room manual control and master control room automatic control coexist, and set a variety of interlock protection. Each hopper is individually controlled, and the batching and feed controls are three separate sets of mixers. Even if one of the equipment fails, it will not affect the main control operation screen of the other two silos, and realize the manual and automatic interlock control of the supporting equipment such as kiln material weighing, batching, feeding, discharging and conveying.
According to the set weight and the proportion of the two ingredients, the single dosing time does not exceed 20s, after the dosing is completed, the first press to start, after 10s of delay, the feed truck begins to go down from the total stop position in the middle, the bottom stop feed switch, through mechanical linkage, after weighing the mixed feed into the feed, the feed every down once according to the action rule of 1 point cloth. The actions of batching, feeding, feeding, pouring and cloth are coordinated and automatically completed according to program control. Continue to cycle until the number of feeding is equal to the set batch, and stop at the middle total stop position.
The opening and closing of the hopper door is realized through the mechanical linkage of the feeding trolley. Using the relationship reflected by the weighing weight of the material when the hopper door is opened and closed, it is possible to know whether the hopper door is closed by judging the weight of the hopper before each discharge. Generally, there will be a large negative number when it is turned off. Compared with the feeding parameters set by experience, the weight of the tiger mouth is less than the feeding set value after the cart rises, which indicates whether the feeding process is normal. Once there is an anomaly, the feeding will be stopped and an alarm will be issued to prompt the operator to deal with the fault to avoid a large amount of material scattering and ensure the safety of the system feeding process.