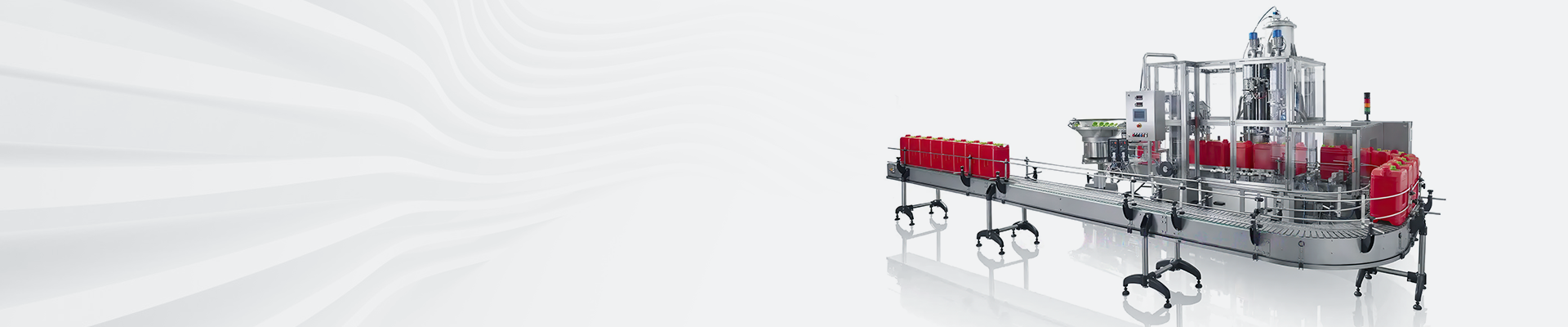
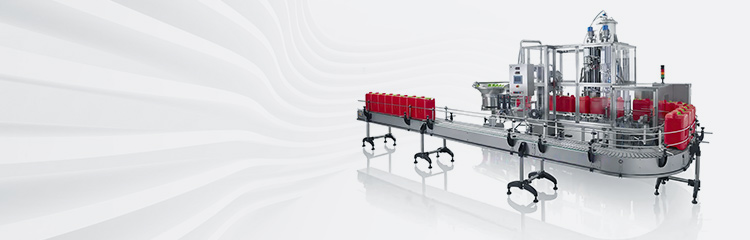

Summary:The batching system adopts S7-300 and ET200 as the control, data calculation, storage and management of the whole batching to realize centralized monitoring and decentralized control. It consists of feeding system, weighing system, mixing and conveying system and central control system. Through the central control system, each sub-system will be integrated intelligent control to achieve the purpose of energy saving and consumption reduction.
At present, the vast majority of domestic PVC resin manufacturers use DCS system to realize polymerization automation control, which mainly includes formula management, fully automatic charging control, polymerization reaction control, monomer recovery control, drying feed control and chain protection control. Batching of 60,000t / a micro-suspension method of PVC paste resin device using YOKOGAWA company's dosage of centralized dosage control system to achieve automation control. The following describes the process control process and control program of the device.
1 Process flow
Vinyl chloride micro-suspension polymerization is to use oil-soluble azo compounds and organic peroxides as initiators, and pre-mixed with vinyl chloride, emulsifiers, pure water, and then mechanically dispersed into a stable dispersion with droplet diameter of 1~2μm, and then polymerized. The micro-suspension method PVC paste resin plant of the dosing equipment is divided into 2 production lines, each with 5 polymerization kettles, sharing 1 set of dosing, homogenization and recovery equipment. The production process is divided into chemical preparation, homogenization, heating, polymerization, recovery, drying and other stages according to the process, which is automatically controlled by DCS system.
2 Control system composition and function
2.1 System hardware composition
The metering and feeding system adopts FIO standard field control station (KFCS), whose CPUs are 1:1 pairwise redundant, with dualized Vnet/IP network and power supply. Each CPU and Vnct/IP communication card of the system is equipped with self-diagnostic function and fault alarm function, which is convenient for debugging and maintenance.
Aiming at the process characteristics of the batching equipment, the batching machine is configured with 3 control stations, of which FCS0101 and FCS0102 realize the program control of polymerization line 1 and polymerization line 2 respectively, and FCS0103 completes the control of drying device and utility engineering.
The dosage control system is equipped with one engineer station and seven double-screen operation stations, which realize the configuration and monitoring functions respectively. The operating interface of the system view software is flexible and convenient, providing a large space for self-development. Users can complete the required special functions through the programming language provided by the system to improve the production operation and management level.
2.2 System program composition
Feeding system powerful, flexible configuration to provide CAE (computer-aided engineering), can be directly used controldrawing diagrams or fill in the form of software configuration, very simple and intuitive; and can provide virtual testing and simulation software to shorten the debugging cycle of the software.
PVC paste resin device DCS system needs to realize the control of
Functions mainly include conventional control, complex control, logic chain control and sequence control. The program should automatically complete the smooth control tasks at each stage according to the operator's instructions, and at the same time realize the accident processing of various abnormal working conditions. Among them, the use of smooth control table combined with a variety of conventional control, complex control to achieve the polymerization kettle recipe management, homogenization, reaction, recycling and atomization drying stage of the sequence control is the key part of the program. Shun control table of automatic batching system is a kind of software platform of Shun control with perfect function and convenient configuration, which is equipped with rich Shun control elements and different scanning methods, and with the help of connecting other function blocks and control process I/O and software I/O, it can automatically give the circuit, change the control method, output all kinds of information, call all kinds of calculations, and realize the sequential and interlocking control.
3 PVC paste resin polymerization device control program
3.1 Program processing of recipe data
First, the product grade of the production batch and the corresponding recipe parameters are determined. Recipe data is stored in the batch data setting block BDSET-1L, and the recipe data of each kettle is divided into two parts: chemical preparation, homogenization and cleaning part of the recipe data and the polymerization reaction part of the recipe data, the former is set up for each production line with one public recipe data block, and the latter is set up for each polymerization kettle with one recipe data block. Using the system's calculation block and the smooth control table software function to realize the recipe program processing. When the chemical preparation program of the polymerization kettle is started, the recipe data inputted from the screen is read and used for program control.
3.2 Control of feeding stage
In the micro-suspension polymerization process, polymerization before the use of high shear mixing of materials for homogenization, homogenization effect is the key to affecting the particle size distribution of the product, so in the process of dispersion of materials should be strictly controlled by a variety of materials to add the speed to ensure that a variety of materials at the same time into the dispersing tank dispersion and dispersion of the end of the completion of the formula set the amount of materials to join. In the homogenization process, the smooth control procedure should be strictly implemented in accordance with the process time sequence, and at the same time, it should be able to automatically deal with the sudden abnormal phenomena in the homogenization process.
The control program of homogenization process is a common program for each production line, and only one polymerization kettle can start the homogenization control program each time. The homogenization control program is mainly realized by the smooth control table, and the processes of vacuuming, adding different additives, cleaning, etc. are realized by an independent OC table with step numbers. The required control functions are realized through multiple calls to the common program of homogenization part, single-step execution, step-skipping, etc. 3.2 Temperature control of polymerization kettle One of the key points in the production process of PVC paste resin by micro-suspension method is the control of kettle temperature. The parameters in the program are set by the formula data, defined as follows: ① M3 is the polymerization reaction temperature control value, depending on the product model.
S1 is the jacket temperature setting value, which is adjusted according to the temperature curve of transition stage and jacket temperature.
M1 is the kettle temperature when jacket temperature is set to be automatically adjusted during temperature rise, which is calculated according to the kettle temperature rise rate, jacket temperature, kettle temperature and cooling water temperature. ④M2 is the kettle temperature when the series regulator is put into operation, generally M3-0.5℃. (1) Temperature rise stage. The transition stage of the warming process is the difficult control point. As the kettle temperature is close to the set reaction temperature, the exothermic reaction starts, so it is necessary to find the equilibrium point of heat absorption and exothermic, so that the kettle temperature can be smoothly transitioned to the constant temperature stage. The kettle temperature control of dosing equipment adopts the program of serial adjustment of kettle temperature and jacket temperature, with kettle temperature as the main adjustment parameter and jacket temperature as the secondary adjustment parameter.
In the warming stage, in order to avoid over-regulation and make the kettle temperature transition smoothly, the measures of changing the regulation law are adopted. Temperature rise program start, close the cold water valve V1, open the hot water valve V2 and jacket pump P, to the jacket into the deionized water preheated to 90 ℃, drive the kettle temperature to a fixed slope rate of uniform rise. When the kettle temperature reaches the value of M1, close the hot water valve V2, open the cold water valve V1, and set the jacket temperature control to automatic adjustment, with the set value of S1. Since the polymerization reaction has just begun at this time, and the system is transformed from heat absorption to exothermic, which is not in line with the heat that needs to be taken away from the jacket at the stage of thermostatic temperature, a weaker control mode is adopted, so that the water valve of the jacket is opened slowly, and the temperature of the jacket is adjusted according to the set value. Subsequently, due to the thermal inertia of rapid warming and reaction exothermic increase, the kettle temperature further rises to the value of M2, at this time, the kettle temperature control is set to automatic adjustment, the set value is M3, and the jacket temperature is set to cascade adjustment. When the kettle temperature reaches M3, the jacket control is strengthened, and the output of the main regulation is tracked rapidly, and the reaction thermostat control stage is entered.
(2) Normal reaction stage.
The average polymerization degree of PVC paste resin depends on the polymerization temperature, the higher the temperature, the smaller the average polymerization degree. The polymerization temperature has a great influence on the reaction time, low polymerization temperature is long reaction time. Polymerization temperature increases every 10 ℃, the polymerization rate increases three times. Therefore, the polymerization temperature must be strictly controlled so that its fluctuation range is within ±0.3℃ of the set temperature.
When the kettle temperature reaches the set kettle temperature of the constant temperature stage, that is, into the constant temperature stage, this process is a stable reaction period, the reaction process will release reaction heat, so the constant value of the series control, so that the chilled water valve in the role of the series control to find the reaction equilibrium point very quickly, the kettle temperature is maintained at the set value. The heat release during the whole reaction process is not uniform, and the peak period of reaction is different when the initiator ratio is different. According to the test data of the initiator and the practical experience of the production, the dosing equipment, by figuring out the changes of the exothermic quantity at different stages of the reaction, sets the main adjusting parameters into two different groups of PID parameters, automatically switches the PID parameters of the main adjusting controller with the use of the smooth control program, and uses the variable PID control to adapt to the changes of the working conditions and meet the requirements of the kettle temperature control.
At the same time, according to the characteristics of polymerization reaction exothermic, in order to react to the interference in time and control the fluctuation of kettle temperature within the permissible range, the dosage equipment imposes manual intervention at the same time of serial temperature control, i.e., when the kettle temperature rises and exceeds the set value of 0.1℃ or the kettle temperature falls and is lower than the set value of 0.1℃, the main regulator will intervene manually with the main regulator output value through the smooth control program, so as to enable the controller to make a quick reaction to the interference. to suppress the aggravation of deviation.
The above program controls the temperature of the polymerization kettle within the range allowed by the process, stabilizes the process parameters and improves the quality of PVC paste resin.
4 Conclusion
The use of automatic dosage system powerful function to realize the micro-suspension method of PVC paste resin polymerization reaction integrated control program, flexible use of the smooth control program, so that the polymerization temperature is basically controlled at the set temperature within the earth 0.1 ℃, so as to stabilize the process parameters, improve the quality of PVC paste resin. Since the system was put into operation, it has been stable, reliable and easy to operate, giving full play to the production capacity of the existing equipment. The polymerization system from feeding to discharging all realize automatic control, improve the output and quality of the product, simplify the field operation, reduce the labor intensity of the operator, and improve the production efficiency.