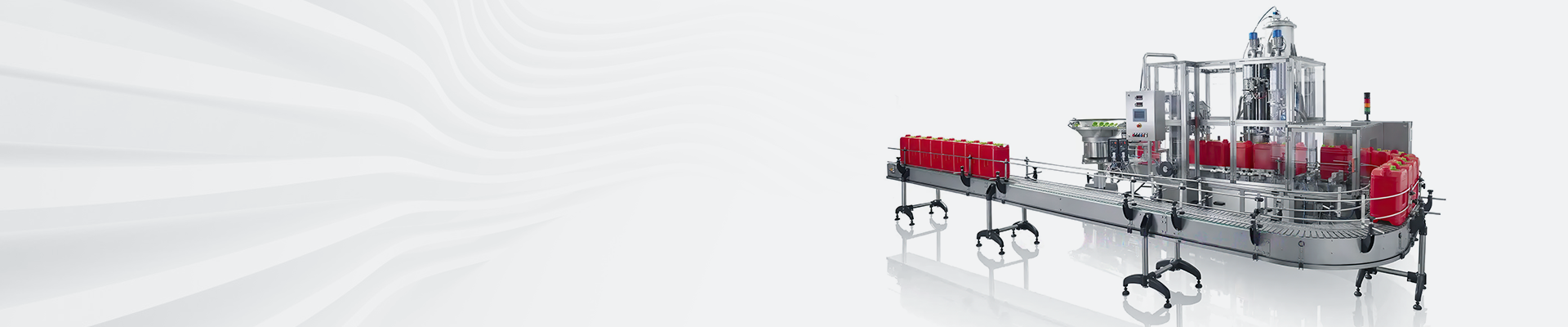
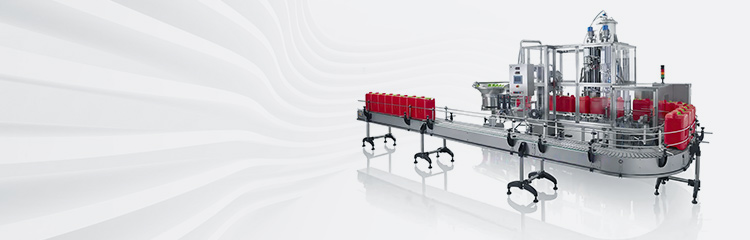

Summary:The weighing batching machine can display the changes in each weighing bin, the operation of the equipment and the status of the equipment through dynamic graphics, record and archive the data changes of each batching.
At present, many pharmaceutical companies mainly focus on the application of advanced technology and equipment to control the production process, the development of a variety of mixing, stirring, molding, packaging equipment, but in the dispensing - weighing link, but was ignored. Most of the enterprises still use the traditional manual material extraction and weighing method, low efficiency, poor precision, and easily due to human error caused by the duplication of an ingredient or omission phenomenon.
Some pharmaceutical factories use simple mechanical operation, but it is difficult to meet the requirements of high precision of pharmaceutical ingredients.
Another part of the enterprise in order to strengthen the dosage operator responsibility, to be able to carry out the responsibility of traceability, the implementation of electronic signature system, such as Rockwell automation system regardless of the operator into or out of the electronic signature can be automatically executed. However, this method can only be an afterthought.
The implementation of this program I design a weighing accuracy, lower price, and can ensure quality and safety of the automatic batching machine to meet the needs of small and medium-sized enterprises.
1 batching machine overall program design
After a comparison of several program arguments, the main work process: mixing machine by 10 raw material barrels (respectively, containing the ingredients of the formula), 10 collector barrels (a combination of ingredients) composed of the ingredients of the code, and will be affixed to the bar code on the raw material barrels by the bar code reader to identify, if it is a prescription ingredient, the PC opportunity to display the number of ingredients, then the material can be taken as needed. If it is a non-prescription ingredient, it will refuse to open the lid and take the material. Repeated pickups will also be rejected by the control system. If the weight is correct, the tank will be opened and poured automatically, and if the weight is too poor, the system will refuse to pick up the material.
This not only reduces the workload of personnel, but more importantly, completely avoids human error. The equipment can be well suited to our national conditions to meet the new production requirements of the pharmaceutical industry.
Various components of the pick-up error is less than 0.01g, to achieve a high degree of weighing accuracy, and can be regularly calibrated.
The mixer is overall electromechanical integration equipment: mechanical part: raw material cylinder turntable and collector cylinder turntable are supported by mechanical structure, with starting, braking and positioning devices; weighing mechanism, including the design of the calibration weighing part. Each part of the action is powered by a cylinder. Automatic control part: the starting and braking of the turntable, the identification of raw materials, opening and sealing the lid, weighing, pouring and calibrating are all completed by the control system. The mechanical part and the control part form a good cooperation with each other, and the action is accurate.
2 Mechanical part of the main structure design
Raw material barrel turntable and aggregate barrel turntable structure is similar, only to the raw material barrel as an example of its structural design.
2.1 Raw material barrel turntable structure
The lower end of the solid shaft is suspended arrangement, the friction Yang force is reduced, the whole set of weighing control system is flexible and free running. Starting cylinder solenoid valve to accept automatic control signals to promote the rotation of the rotary axis, and ultimately make the cylinder rotation, turn to the pickup position before the implementation of about 5 ° braking and accurate positioning. In order to facilitate the transportation, disassembly and maintenance [many parts of the detachable connection.
2.2 Starting device design
Adopting overrunning clutch structure, the clutch drives the main shaft to rotate when starting; the main shaft does not move when returning to the position, which not only realizes the conversion of linear motion to rotary motion, but also meets the intermittent rotation at an interval of 36° in order to pick up materials.
2.3 Positioning mechanism design
The turntable should be accurately positioned to stop after 36° so as to scan the barcode and accurately pick up materials.
2.4 Minimum diameter design of rotating shaft
The rotating shaft is supported on the sleeve by the bearing, the upper end is connected to the step outer shaft by the key, the lower end is installed with overrunning clutch, braking device and positioning device, the rotating shaft has to bear the sum of the rotational inertia of 4 parts, which are the step outer shaft, the drum and the medicine, the outer extension beam and the rotational inertia generated by the shaft itself. Considering the safety coefficient, the minimum diameter of the shaft is designed as 40mm. and because the capacity of raw material barrel is larger than the aggregate simple, so the raw material machine meets the requirements, the aggregate machine must also meet the requirements.
3 Automatic control part of batching machine
In many automatic control program, selected the programmable controller (PLC) control knowledge, through the preparation of the program, to achieve the control requirements. According to the analysis of the control object can be seen: the number of input points for 17 points output points for 7 points.
The control of the machine for the switching control, and the required number of IO points is not much, so choose a general small machine can be S. Selected FX1N-40MR type PLC, its host IO points for 24/16.
The electronic balance is the JH2102 electronic precision balance produced by Shanghai Tianpu Analytical Instrument Co. The balance features: high accuracy (can be accurate to 0.01g), in the poor use of the environment can also achieve the requirements of precision weighing, can be tare weight. Merologic series barcode scanner MS1690 barcode scanner.
4 prototype test analysis
4.1 test purpose
The machine's startup sensitivity, positioning accuracy and reliability, are part of the mechanical structure and control program to ensure that, and after a trial test, to achieve satisfactory results. Therefore, the main item of the test is the weighing accuracy, that is, to detect whether the weighing error can be controlled within 0.01g. This is also a small dosage of formulated drugs pay more attention to the problem.
4.2 Test method
Use the JA5003N electronic precision balance with higher weighing accuracy (reading accuracy: 0.001g, weighing range: 500g) to detect the mass of each portion after weighing, and calculate the weighing error each time. Analysis of the test results shows that, regardless of the size of the sample, the average error is <0.01g, within the control range, to meet the design requirements.
5 Conclusion
This topic has completed the design, prototype preparation and test work of the accurate weighing dosage machine.
It mainly solves the problems of over taking or omission of ingredients and over weight due to manual operation in the process of drug dispensing. It plays a role in guaranteeing the quality and safety of drugs.
Popularization and application: This equipment has the function of high-precision weighing, and it can be applied in other industries that need high-precision dosing, such as the dosing of automobile tires.