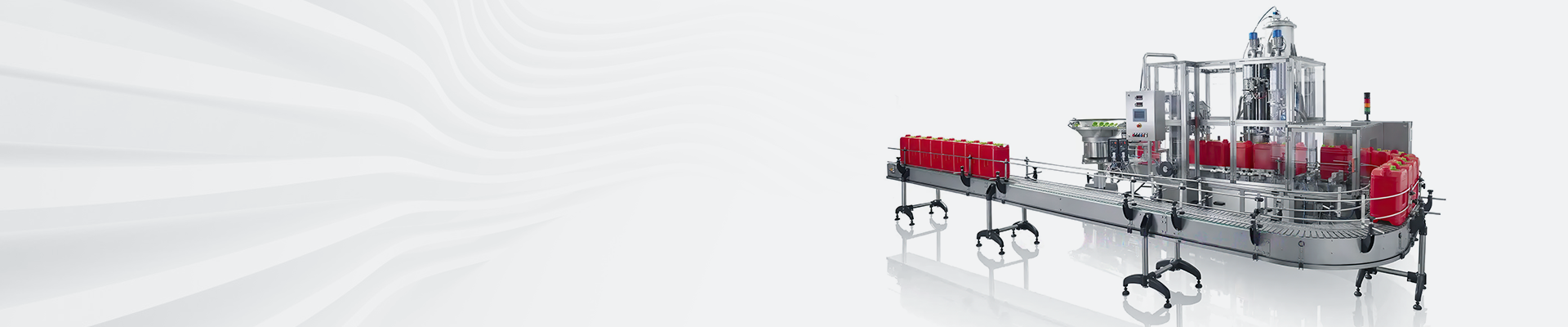
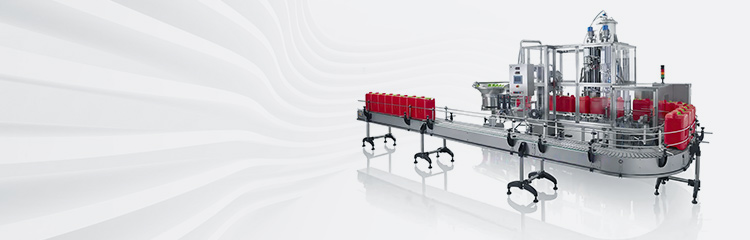

Summary:The automatic batching system realizes fully automatic control of multi-formula and multi-material batching, which must be completed by PLC and uses weighing modules for communication.Each weighing module corresponds to a set of sensors of a weighing bucket to implement a weighing unit.
1 Preface
Weighing module is called the heart part of weighing control system and electronic balance. The rapid development of science and technology, the weighing module made by the weighing and batching systems and electronic scales have been widely used in all walks of life, to achieve the rapid and accurate weighing of materials. Especially with the emergence of microprocessors, the degree of automation of industrial production processes continue to improve, weighing module has become a necessary device in the process control, from the previous can not be weighed large tanks, hoppers and other weight measurement, as well as crane scales, automotive scales and other measurement control, to the mixing and distribution of a variety of raw materials feeding systems, production processes in the automatic detection and control of powder and granular body feed, etc., are applied to the weighing module. Weighing Modules
Weighing electronic material level meter solves the inherent problem of inaccurate measurement caused by uneven surface dust of solid materials, widely used in petrochemical, plastics, cement, medicine, feed, food, metallurgy, light industry, building materials, environmental protection and other industries, to achieve the upper and lower limits of the level of the material alarm and control.
2 weighing material level meter composition and working principle
Material level meter is a container of solid material height (weight) of the changes in real-time detection of the primary instrument. Usually output 4-20mA or 1-5V standard signal and secondary instrumentation or computer system connection can also be connected through RS-485 or Modbus/Profitbus/Hart fieldbus with the calculation system. The material level meter is also known as material level transmitter, material level controller, material level meter, material level meter and so on.
Weighing level meter consists of several major parts, such as silo (or tank, trough, etc.), support body, weighing module, weighing instrument, etc. Among them, silo and support body are the main parts. Among them, the silo and the support body is the mechanical force transfer reset system between the weighed object and the conversion element, including the grain bin that accepts the load of the weighed object, the force transfer reset mechanism, the limit device, etc., which is the main load-bearing part of the weighing electronic material level meter and plays the role of bearing the weight of the object. The silo and the force transmission mechanism are responsible for accurately transferring the weight of the object to the weighing module. The weighing module (primary meter) is located between the silo and the supporting body, which converts the weight of the weighed object into the corresponding millivolt electrical signal according to a certain functional relationship, and outputs it to the weighing control meter (secondary meter) through the signal cable of the junction box. After processing, the instrument directly displays the weight data of the weighed object and realizes the conversion of the weight data into 4-20mA or 1-5V standard signals, or transmits them to the control terminal by RS-232, RS-485, Modbus/Profitbus/Hart. The weighing control instrument can also be pre-set at different weight values to realize relay output to control the automatic addition and subtraction of materials.
3 Weighing Module Selection
Weighing module in the selection of many factors to be taken into account, the actual use of the main factors from the following considerations. Secondly, the sensitivity of the weighing module, the maximum number of divisions, the minimum calibration index value and so on are also the indicators that must be carefully considered in the selection.
3.1 Use of the environment
Weighing module is actually a quality signal into a measurable electrical signal output device. First of all, we must consider the actual working environment in which the sensor, this point for the correct selection of sensors is critical, related to the sensor can work properly and its safety and service life, and even the reliability and safety of the system. In general, high-temperature environments, such as heavy modules caused by the melting of coating materials, weld joints open, structural changes in the stress of the elastomer and other issues; dust, moisture on the sensor caused by short-circuit effects: in the corrosive environment will cause damage to the sensor elastomers or short-circuit phenomenon; electromagnetic fields on the sensor output will produce interference. The corresponding environmental factors to choose the corresponding weighing module to meet the necessary weighing requirements.
3.2 Number and range of load cells
The selection of the number of weighing modules is based on the purpose of the weighing system, the number of points to be supported by the carrier (the number of support points should be determined according to the principle of coincidence of the geometric center of gravity of the carrier and the actual center of gravity). Generally speaking, there are a few support points on the selection of several weighing modules load cell range selection can be based on the weighing of the maximum weighing value, the number of sensors selected, the weight of the scale body, the maximum bias load can be generated and the dynamic load factors to determine a comprehensive evaluation. Generally speaking, the closer the range of the sensor is to the load assigned to each sensor, the higher the accuracy of its weighing. However, in actual use, because the load loaded on the weighing module in addition to the object to be weighed also exists in the carrier self-weight, tare, bias load and vibration impact and other loads, so the selection of the weighing module, we must take into account a number of aspects of the factors, to ensure that the safety and life of the sensor.
3.3 Installation of the weighing module
The installation method of weighing module mainly depends on the type of weighing and installation space to ensure proper installation and safe and reliable weighing; on the other hand, the manufacturer's suggestion should be considered. For the sensor manufacturer, it generally specifies the force of the sensor, performance index, installation form, structural form, elastomer material and so on.
3.4 Accuracy level of weighing module
The technical indexes of the accuracy level of the weighing module include nonlinearity, creep, repeatability, hysteresis, sensitivity, etc. When choosing the weighing module, it should not be blindly selected. In the selection should not blindly pursue high-grade sensors, should consider the accuracy level and cost of electronic scales. In general, the total accuracy of the selected sensor for the nonlinearity, non-repeatability and hysteresis of the sum of the three indicators of the root mean square value is slightly higher than the accuracy of the scale.
4 weighing level meter on-site installation, commissioning
This paper introduces the installation of various large and medium-sized feeding systems using pressure-type weighing module as an example.
4.1 Field installation characteristics
(1) weighing module installation is difficult, the weight of the silo is relatively heavy, some even up to hundreds of tons. In the entire silo installation (including liner installation) welding is completed before the weighing module can not be installed.
(2) During the installation of the weighing module, the jacking technology is utilized to realize the jacking of the silo and complete the installation of the load cell.
(3) The installation process is simple, easy to implement the advantages of operation and installation accuracy.
(4) The use of "analog calibration method", debugging high precision, simple methods, applicable to meet the requirements of weighing measurement.
4.2 Installation process and key points
(1) Construction process
Weighing module installation location to determine a temporary support production and installation of a weighing module and accessories installation of an electrical circuit wiring check silo weighing module system simulation debugging a system calibration a put into trial operation information to organize the operation.
(2) the main points of the site installation
1) silo weighing module base elevation determination and temporary support seat installation
In the silo foundation installation is completed, the silo is not in place before (if the silo is in place after the four-point elevation measurement will be difficult), first of all, the need to install the weighing module 4-point position elevation, to determine whether the level of a horizontal plane. Generally recommended control of about 3 ~ 5mm. Produce temporary support height than the actual height of the weighing module 20mm high, so that the weighing module installation operation is convenient weighing module temporary support in the silo in place at the same time as the installation of temporary support does not require full welding, in order to remove the good later.
2) Installation of the weighing module in press type
Prerequisite for installation of weighing module: all welding work or work with strong current on the silo must be completed before the load cell can be installed.
Determine the position of the weighing module: Ensure that the 4 load cells on the silo are symmetrical and evenly loaded.
Place 4 jacks (the choice of jack type and specification is determined according to the weight of the silo) on the edges of the temporary support, start the jacks at the same time in 4 positions and slowly lift the silo up to a height where the temporary support can be taken out. Move the temporary support away from the position where the weighing module is installed, but make sure that the temporary support has a supporting effect on the silo.
Install the upper and lower bases of the weighing module and accessories (with flat washers and copper shims for adjustment), use the level meter to level the upper and lower bases of the load cell, the error should not be more than 2mm, the upper and lower bases of the weighing module will be fully welded, and the load cell will be taken out of the welded process. After the welding is completed, put the 4 positions of the weighing module into position.
Remove the temporary support and slowly unload the jacks in all 4 positions and slowly place the bins on the installed weighing module.
Connect the upper and lower kits reliably with a grounding wire.
After the sensor is installed in place, prohibit welding operation when the current flows through the sensor body.
3) Electrical system circuit debugging
Check the wiring weighing detection circuit wiring is correct, power circuit insulation is good.
Use precision multimeter to measure whether the output resistance value of the 4 sensors in the bin is balanced or not, if it is not balanced, adjust the precision potentiometer in the sensor compensation junction box, so that the output signal of the 4 weighing modules is balanced and the weighing system circuit is powered up.
4) System calibration (actual is subject to the instrument commissioning manual supplied with the weighing system)
Electrical zero calibration of the weighing module
Zeroing of bin tare
Calibration of weights
Weighing system simulation test
After the calibration of the weighing instrument is completed, the various application parameters of the actual demand are set, and the data records of the various test adjustments are organized and filed.
It should be emphasized here that in the process of installation, commissioning and use must also pay attention to safety and environmental measures. Any construction must follow its due industry norms and systems.
Conclusion
Weighing material level meter after actual research and practice in the project, compared with the traditional method, reduces the construction difficulty, reduces the labor intensity, shortens the construction period, saves the use of large cranes, saves the cost of construction machinery, and improves the economic efficiency. At the same time, it ensures the installation and commissioning accuracy of the weighing module, which is well received. Therefore, the use and commissioning process in the field must have a clear operational thinking, careful analysis, and actively summarize and accumulate on-site operational experience. If this is the case, you can greatly reduce the existing failure problems, can save a human amount of time for the field commissioning, for future maintenance to provide convenience.