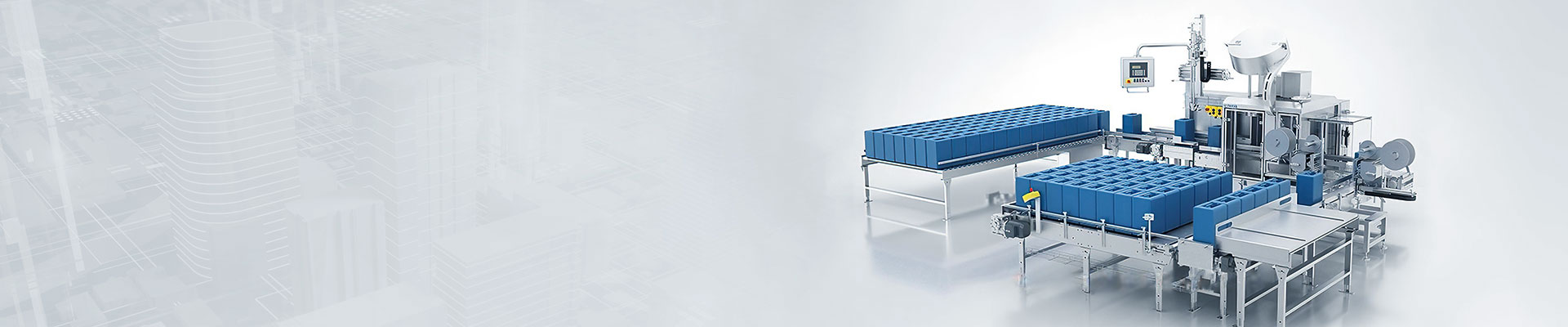
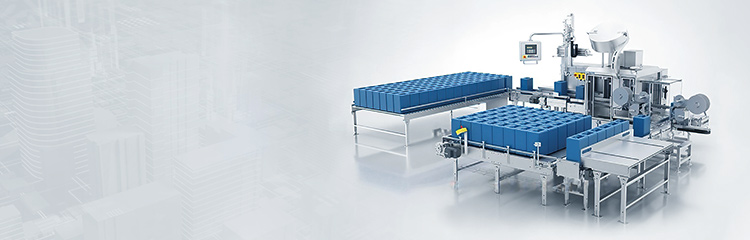
When the powder dosage system is refilled in the specified amount, the valve is closed to stop the addition of liquid, the stirring switch is activated, and the metering and dosage control starts to automatically add the material to the reaction tank according to the non-linear speed required by the dosage process, and then it flows from the silo to the dosage tank with the inlet pneumatic valve open, and the pump stops when all the material in the silo has flowed into the stirring tank. The weighing module monitors the flow rate of the solution injected into the dosing tank in real time and transmits the measured pulse range to the PLC, which calculates the weight of the solution and transmits the data of the total injected capacity to the host computer.

Weighing control system of powder conveying mainly rely on wind conveyor, compressor and other gas power equipment; liquid material conveying mainly rely on pumps, vacuum equipment or their own gravity; powder material conveying methods are hydraulic conveying, mechanical conveying and pneumatic conveying, the most commonly used in the industry is mechanical conveying and pneumatic conveying. Powder mechanical conveying equipment are screw conveyor, belt conveyor, bucket mixer and so on. Mechanical conveying of powders, in the joining point of the material and the discharge port, there are due to the gravity of the powder falling air disturbance caused by the dust raised, the formation of fugitive dust source (unorganized emissions). Mechanical conveying is generally shorter conveying distance, smaller conveying capacity, poor equipment containment, poor flexibility of deployment, high investment, dust pollution is more serious.
Powder process based on the fluidization theory established by the pneumatic conveying, become all kinds of powder in the various process units and equipment between the most commonly used way of conveying.
Pneumatic feeding system is powered by gas, in the closed pipe along the direction of the airflow through the sealed pipe to the powder material from one place to another device, is a specific application of fluidization technology. Widely used in fine chemicals, polymer materials synthesis and processing, battery manufacturing, food processing, metallurgy, cement building materials, coal-fired power stations and other sectors, is suitable for bulk material conveying a modern automatic Batching system, in many ways can replace a variety of traditional mechanical conveying and hydraulic conveying.
Pneumatic conveying has the following characteristics:
The particle size of conveyed powder can be from 1~104mm, and the density can be from 0.5×103~2×103kg/m3;
Flexible arrangement and long conveying distance;
For leakage-free conveying, no secondary pollution;
Energy saving and high efficiency;
Can be centralized conveying and recycling;
During the conveying process and at the conveying terminal, other process operations such as crushing, mixing, heating, cooling, drying (air drying, etc.), grading, etc., can be carried out at the same time, and even some chemical reaction processes can be carried out at the same time;
Suitable for computer control, high degree of automation;
The particles are easy to be broken; when the hardness of the material is high, the equipment is easy to be abraded;
Materials with much water content, adhesive or prone to static electricity in high-speed movement are not suitable for pneumatic conveying.
The type of pneumatic conveying:
According to the concentration of powder in the conveying pipeline, the pneumatic weighing and batching system can be divided into concentrated phase, semi-concentrated phase, dilute phase conveying system; according to the conveying pressure, it can be divided into positive-pressure system (press-feeding type) and negative-pressure system (suction-feeding type). Suction type pipeline pressure is lower than atmospheric pressure (working pressure of -0.04 ~ -0.08 MPa), self-absorption into the material, but must be unloaded under negative pressure, can be transported over a shorter distance, the main characteristics of the low (or bulk), multi-point to the high places, a point of delivery; pressure feeding system pipeline pressure is higher than atmospheric pressure (working pressure of 0.1 ~ 0.5 MPa), easy to unload, can be transported over a longer distance, but must be used to add material to the system, and can be transported over a longer distance. Longer, but must use the Feeder will be sent to the powder pressure pipe, positive pressure dilute-phase system in the material concentration is generally 5 to 10 kg / kg gas.
Dilute-phase conveying usually adopts higher gas velocity and lower solid-to-gas ratio, with solids content lower than 100 kg/m3 or solid-to-gas ratio (mass flow rate ratio of solids transported to the corresponding gas dosage) of 0.1 to 25 in the conveying process. Higher operating gas velocities (18-30 m/s). The conveying distance can be up to several hundred meters. The conveying gas is often air or nitrogen, and the power is usually provided by a Roots fan.
Dense-phase pneumatic batching control system is the use of compressed air to transport materials to the destination of a conveying method, solids content higher than 100 kg/m3 or solid-gas ratio greater than 25 conveying process. With higher air pressure pressure delivery. It is greatly superior to mechanical conveying, hydraulic conveying and other conveying methods in terms of environmental protection and energy saving. Concentrated phase conveying is divided into sending tank conveying and rotary valve conveying. The conveying gas often adopts air or nitrogen, and the power is generally provided by compressor, screw pump, etc., with low energy consumption.