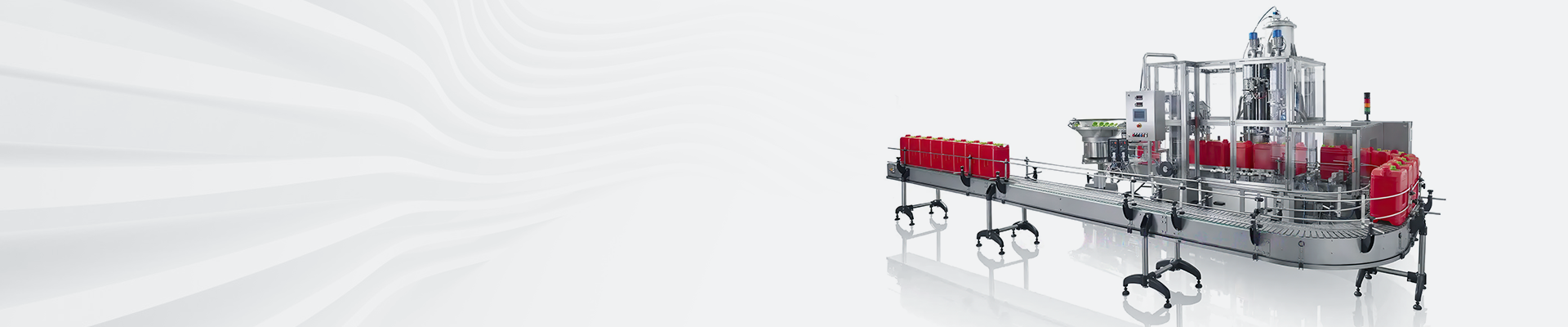
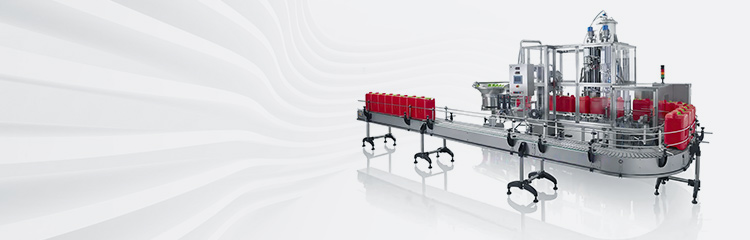

Summary:The batching system performs logical control on the motors, valves, etc. in the system (controlling the amount of each additive added) according to the set parameter requirements.It accepts control signals from other parts to achieve linkage, or sends its own weighing data to the main control computer for processing in a timely manner.
PVC resin in the processing to add a variety of additives to improve the performance of PVC, in order to adapt to the processing and product performance needs. In the production of plastic doors and windows profiles generally to add: heat stabilizers, processing modifiers, impact modifiers, lubricants, light stabilizers, fillers and colorants. The addition of these additives is 0.1% to 10% of the PVC resin, but they each play a very important role, it can be said that one is indispensable, and changes in the amount of addition to the processing and final product performance has a great impact. Therefore, not only in the ingredients to be weighed accurately, but also in the mixing process to be mixed evenly to achieve consistency of the material.
1 material preparation
PVC material preparation process mainly includes batching, hot mixing, cold mixing, transportation, storage. The method has artificial dosing, artificial transportation of small-scale production and automatic dosing, automatic transportation of large-scale production. In recent years, China's hard PVC profile extrusion industry has entered a period of rapid development, the scale of enterprises continues to expand, the annual output of 10,000 tons of enterprises, such as the use of manual dosing of traditional material handling methods have been unable to meet the needs of mass production, material handling automation has become a common way to use.
Dosing is the first process of mixing. The key to dosing is a "quasi" word. In the plastic door and window profile production of large-scale modern enterprises, dosage technology, most of the computer-controlled multi-component automatic weighing and measuring system. More widely used is the weighing measurement method, according to different weighing methods, can be divided into batches of cumulative weighing, loss-in-weight weighing and flow process material continuous weighing three ways. The batch cumulative weighing and mixing process requires a batch of material mixing mode of work is very harmonized, the most suitable for PVC mixing, so in the production of PVC profiles used more. Batch totalization weighing.
Weighing control system including hopper scale, load cell and computer control system, is the core of this system, the main functions are: to reduce the electrical signal of the weighing module to the mass value displayed on the screen and input into the computer; according to the requirements of the set parameters of the system, such as motors, valves, etc., for logic control (control of each kind of additive to add the amount). Accept other parts of the control signal to achieve linkage, or its own weighing data in time to the main control computer for processing.
Artificial batching is the method used in small and medium-sized factories. Since the batching process is a very important production link and the accuracy of batching is directly related to the normal production and the quality of the products, each factory has formulated the corresponding operation process and quality control measures according to its own actual situation.
Artificial batching process should pay attention to:
(1) The personnel must be trained and qualified before taking up the job. Training should include skills and professional ethics training. Personnel should be kept relatively stable.
(2) The accuracy of the weighing system must be carefully checked before each operation, and measurement appraisal should be carried out regularly.
(3) Make preparations before operation, including inspection of various auxiliaries, opening packages, neat yardage, preparation of holding bags as well as preparation of hygienic and environmental protection instruments and tools for use.
(4) The operation should be carried out in accordance with the specified operating procedures and operating procedures. For example: the use of several ingredients each responsible for 1 to 3 kinds of additives flow operation method, which first weighing and then weighing, weighing accuracy should be strictly in accordance with the operating procedures.
(5) The operation process should be mentally concentrated, no chatting or doing other things.
(6) Strict inspection system of the quality of the ingredients, there should be a person responsible for piece-by-piece inspection, unqualified shall not be sent to the mixing process. Generally adopt the method of checking the total weight, the total weight of the checking should be within the permissible range.
(7) Pay attention to the hygienic environment, ventilation and lighting conditions of the operation site. Pay attention to the health of the batching personnel.
2 mixing process
Mixing process is the PVC resin and heat stabilizers, modifiers, lubricants, fillers, color and other additives mixed with the process of homogenization, the use of equipment is mainly high-speed kneader, cooling mixer. The process is not complicated, but the quality of mixing often affects the normal production and product quality. The process of mixing is to rely on mechanical force on the material, resulting in mutual friction, shear force to make the material refinement, heating, some additives melt, coated in the surface of the PVC resin.PVC resin in the shear, friction under the action of the refinement, the temperature continues to rise, the surface presents a fluffy, porous additives adsorbed on the surface to achieve uniformity; further increase in temperature, the surface of the particles melted, the density of particles increased.
Mixing process is carried out in the high-speed mixer, high-speed rotation of the impeller with the help of the surface and material friction and the side of the material thrust so that the material along the impeller tangential movement. At the same time, due to the role of centrifugal force, the material is thrown to the wall inside the mixing chamber, and rise along the wall, rising to a certain height, due to the role of gravity, and then fall back to the center of the impeller, and then thrown up again. As the impeller rotates at a high speed, the material transportation speed is very fast, the rapid movement of the particles collide with each other, friction, so that the agglomerate broken, the material temperature rises accordingly, and at the same time rapidly cross-mixed, these effects promote the uniform distribution of components and has been melted into a liquid state of the absorption of the additives. High-speed mixer mixing efficiency is high, the time used is much shorter than the Z-type kneading machine, usually a mixing time of only 8 ~ l0min, the temperature of the material with the mixing friction rises very quickly, after 8 ~ 10min temperature rose to 120 ~ 140 ℃. Generally through the control of material temperature to control the mixing time, the discharge temperature control at 125 ~ 135 ℃. After the material reaches the temperature, it is quickly put into the cooling mixer. Material into the cold mixer, in the slow rotation of the role of the mixing paddle, can be radial and part of the axial mixing, so that contact with the cooling jacket of the cold material and away from the cooling surface of the hot material to carry out effective heat exchange, reduce the temperature of the material. Material temperature drops to below 45 ℃, can be discharged from the discharge port.
The volume of the mixer should generally be more than twice as high as the mixer. This ensures the continuity of the mixing process, in order to facilitate the acquisition of uniform dry mix. Dry mix preparation process should be strictly controlled process parameters. At present, some manufacturers tend to pay attention only to the quality of raw materials, formulations, as well as extrusion molding process process control, and for the blending process is not enough attention. The actual production of many product quality fluctuations, are due to the dry mix preparation process control is not strict or unreasonable.
Mixing process should pay attention to the following issues:
2.1 Preparation of raw materials
The main component of dry mix PVC resin should have uniform granularity, appropriate relative molecular mass range, the internal should be porous, the quality should be in line with national standards, should use loose resin. The water content of the resin must meet the production requirements, otherwise it will increase the difficulty of drainage at high speed mixing. All kinds of additives, especially lead salt stabilizer and soap stabilizer particles should be very fine, the content of active ingredients should be stable and in line with the standards of first-class products. The water content of the additives should be low, otherwise it should be dried beforehand.
2.2 High-speed mixer to determine the amount of feed
High-speed mixer should be able to add the amount of material to ensure that the mixing temperature under the premise of maximizing production efficiency. When the volume of material for the mixer empty volume of 50% of the following, the friction heat is small, to reach the preset mixing temperature (such as 120 ℃), need more than l5min; charging volume accounted for 50% to 70%, to reach the temperature is only 8 ~ 10min; charging volume in 70% or more, the mixing effect deteriorates, and the speed of heating is no longer significantly improved, at the same time, the mixer motor current is too large.
Generally should be added to control the amount of mixing room in the empty volume of 50% to 70%. For example: the apparent density of PVC resin is 0.45; for 400L of high-speed kneading machine should be added 400 × 70% × 0.45 = 126kg PVC resin. In order to facilitate the operation generally add 4 bags (4 × 25kg) resin and with a variety of additives (20 ~ 30kg), the total weight of 120 ~ 130kg, more appropriate.
2.3 High-speed mixer discharge temperature selection
Research results show that the PVC resin particles in the strong mixing, material temperature below 50 ℃, PVC agglomerates of powder particles and larger particles are friction, impact, particle crushing becomes smaller, then the apparent density of dry mixes do not change much and the resin particles become smaller. Material temperature above 80 ° C to 120 ° C or so (with the formula and change), PVC resin particles expand (glass transition temperature near the coefficient of thermal expansion is larger), the particle size tends to be uniform, the average size of the particles and the average size of the unmixed PVC resin particles is similar; at the same time, due to the particles absorbed by the additives, the apparent density of the dry mix increases rapidly. Material temperature above 120 ℃ (specific temperature varies with the formula), the resin particle size decreases while the apparent density of the dry blend is still increasing, under the microscope can be seen in some of the particles or particles of the surface layer into a semi-transparent, indicating that the pores within the particles in the reduction, the internal structure tends to be close.
Resin particles become larger and more uniform, conducive to the flow of dry mixing materials, is beneficial to the transport; apparent density increases, is conducive to the increase in extrusion molding output and reduce the exhaust volume, is beneficial to improve the denseness of the product. At the same time, taking into account the material temperature above l00 ℃ is conducive to the elimination of water vapor in the material. So the general high-speed mixing temperature is set at 110 ~ 130 ℃.
The use of liquid stabilizers, while the material moisture content is very low, the hot mixing temperature can be set at a lower temperature range, such as 105 ℃, but not less than 90 ℃. The use of solid stabilizers or materials with a slightly higher moisture content, hot mixing temperature should be 120 ~ 125 ℃; additives containing processing modifiers to promote plasticization and internal lubricants, hot mixing temperature can be taken as the lower limit. Additives in the delayed plasticization, reduce friction of lead salts and external lubricants more, it is appropriate to take the upper limit. However, in practice, special attention should be paid to the temperature shown on the meter and the actual material temperature difference, which refers to the actual discharge temperature of the material, in the production should be often regularly correct the meter display, so as not to cause quality accidents.
2.4 high-speed mixing of various additives feeding order
Hard PVC formula has many components, the dosing order should be strictly controlled. Selected charging order should be conducive to the role of additives to play, to avoid undesirable synergistic effects of additives, but also conducive to improving the speed of mixing and dispersion. Stabilizers should be added to the resin, or with the resin at the same time added to the hot mixer, in order to mix with the resin early and evenly mixed in the mixing temperature to play its stabilizing effect. Soap stabilizers and internal lubricants should be added later, so as to melt and fully penetrate into the resin.
Wax lubricants should be added last when the material temperature is close to the discharge temperature (e.g., added at 85-100 ℃), so as not to interfere with the dispersion of other additives, so that the friction coefficient of the surface of the resin particles to reduce the friction of the lower rate of self-friction heat generation, and prolong the mixing time.
The filler has absorption effect on the additives, and the general dosage is large, it should be added before joining the external lubricant or together with the external lubricant. In order to add additives first in the resin to be dispersed, reduce the filler on the absorption of additives. At the same time, it can also reduce the wear and tear of the hot mixer.
Processing modifiers should be added before waxes are added and after stabilizers are added. Impact modifiers can be added to the hot mixer together with the resin, especially for modifiers with a tendency to thermal decomposition, such as CPE.Processing modifier ACR is a fine powder, in the mixing of dust is larger, and easy to be lost with the exhaust, so the general choice of high mixing late in the material at higher temperatures, viscosity is larger when added, to minimize the loss. Liquid additives should be added slowly during mixing. In short, the additives should be added in the order to maximize the effectiveness of additives to avoid additives between the phase of the elimination, to improve the complementary effect, so as to achieve the best results.