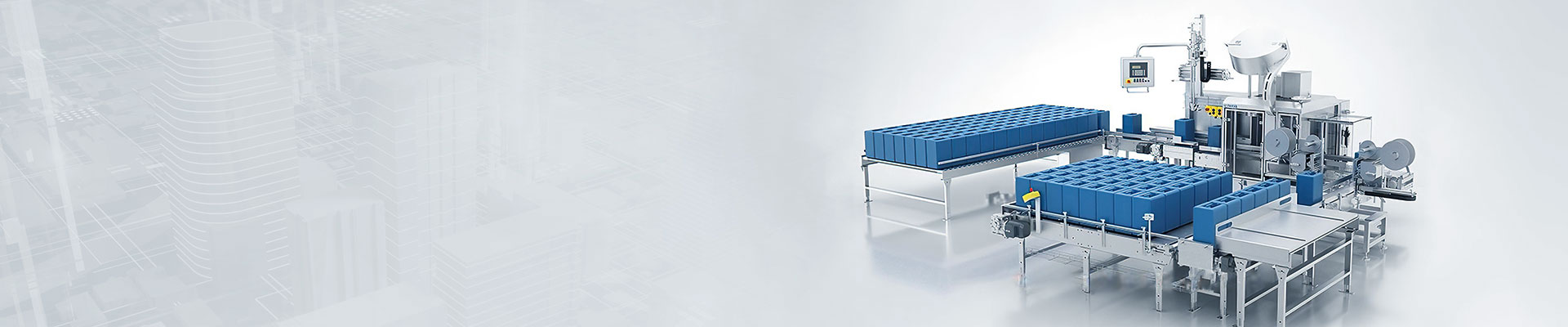
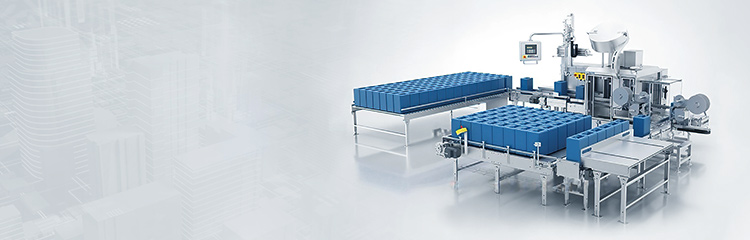
The batching and weighing system is realized by using fuzzy adaptive PID control. The parameters of the controller are adjusted online to track the given input, accelerate the adaptive process and reduce the tracking error. Through the microcomputer to connect a number of weighing feeder, can be used for bin batching, at the same time batching materials can be up to 9 ~ 12, to carry out a variety of materials continuous batching, based on the structure of the bucket scale, can directly carry out the weight calibration, through the weighing hopper each moment test calculated the actual discharge amount, and then closed-loop adjustment, so as to achieve a higher control accuracy.

The dosing system mainly completes the weighing and proportioning of the main material and various ingredients, and after mixing and blending the ingredients, it carries out group classification and filling. It realizes the measurement of the Weighing system, adopts DCS centralized control mode, selects Siemens S7-300 PLC to constitute the data acquisition and control system, and adopts the domestic leading configuration software "Configuration King" in the field of industrial control for the human-machine interface monitoring software, which has the advantages of good openness, easy for users to maintain and secondary development. It has the advantages of good openness, easy maintenance and secondary development. All process control data and equipment operation status of the system can be centrally managed, recorded in real time, and printed and consulted at any time. The structure and function of feeding system is composed of computer, cabinet and peripheral equipment (weighing reactor, pneumatic control valve, transfer pump, etc.).
The control unit of the feeding system is mainly a 10-inch touch screen (equivalent to 10 weighing instruments), PLC as an auxiliary control system, computer human-machine interface displaying the proportioning parameters (formula) and monitoring and recording real-time data. In automatic control mode, by clicking the "Start" button of automatic dosage in the screen or the "Start" button of the control cabinet, the weighing instruments will open the weighing valves of 10 scales according to the set recipe. If the system detects that the dosage valve of a scale is not closed, an alarm occurs and the system enters the pause state. Each scale has an advance quantity according to the weighing speed. When the control instrument detects that the weighing weight reaches the set value, the advance quantity will be subtracted and the control instrument will close the feeding valve. The advance amount can be corrected manually or automatically, so that the control instrument can control the dosage scale to reach the set target value every time the dosage accuracy.
The raw materials are put into the feeding system in a certain order, and the weighing instrument turns on the mixing and heating at the same time. This control process is accomplished by the temperature control meter and PLC. The temperature control meter controls the upper temperature limit and the heating is controlled by the PLC. The automatic batching has two control modes: fixed order and programmable. In the fixed-order mode, the order of discharging all kinds of raw materials is fixed and cannot be changed. In programmable mode, the feeding order of all kinds of raw materials can be set artificially according to the recipe on the human-machine interface.
In the interface of recipe process, the real-time display can show the instantaneous flow rate of the former dosage scale, the proportion of the recipe, the weighing and dosage status, the material level, the valve closing signal, the temperature of the pot, the current of the motor and so on. In the interface there are other operations, such as automatic / manual control buttons, automatic weighing of single and continuous switching buttons, material buttons and reset buttons.