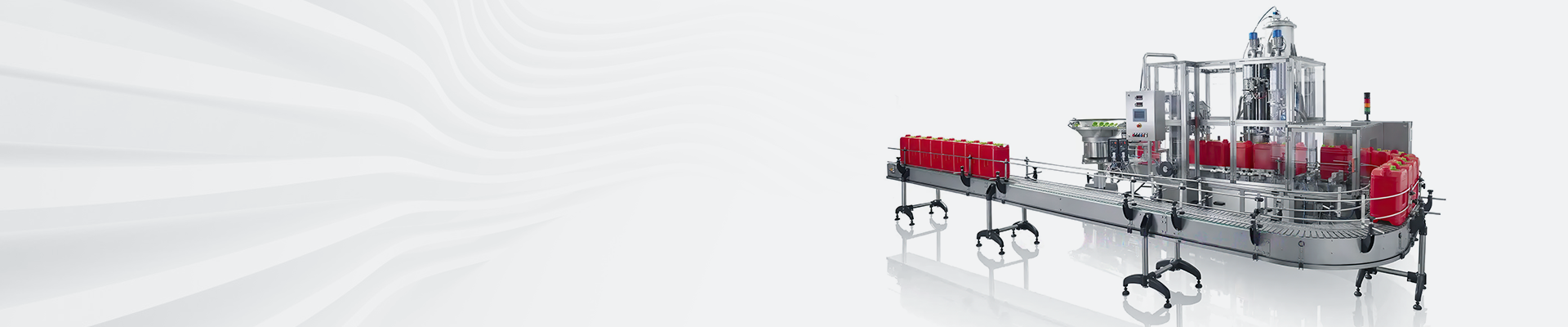
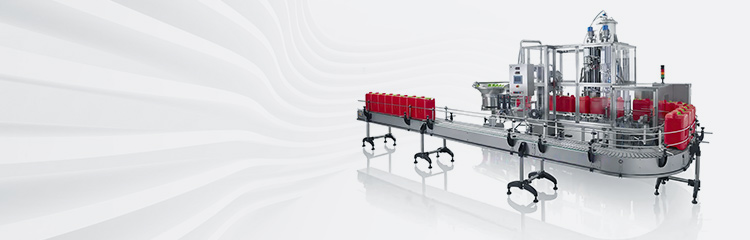

Summary:The batching system records time sampling data and events in the database through WinCC, and can reflect the historical records of temperature and pressure in the form of trend curves.Equipped with complete monitoring functions.
Dosing system structure
The automatic feeding system adopts German Siemens S7-300PLC programmable controller, distributed I/O ET200M and industrial computer (loaded with WinAC and PROFIBUS-DP adapter card CP5611) to constitute the DCS automatic dosage system, and PROFIBUS-DP of the automatic dosage system serves as the The automatic dosage system PROFIBUS-DP is used as the network platform of equipment control layer; WinCC and MPI network are used as the platform of human-machine interface and system maintenance (network programming and human-machine interface standby station) in the monitoring layer; Ethernet is used as the network platform of data management, production and equipment management layer.
One of the four S7-300PLC programmable controllers as the lower to achieve all the signal acquisition, arithmetic, regulation, respectively: temperature control, traction control, pressure control, and auxiliary control of the current unit, S7-300 is characterized by: modularity, no-exhaust structure, easy to achieve the distribution of the operation is reliable, cost-effective. The industrial control machine is mainly installed with WinAC adapter and unit status monitoring, process data access, unit dosage control, and connected with the process control server and production planning server at the workshop level, so as to seamlessly connect with the MIS system at the plant level. Among them, CP5611 card is the communication interface card between S7-300 PLC and industrial control machine. At the same time, in order to facilitate the connection with the MIS system at the workshop level and the factory level, a D-LINK network card is installed in the WinAC controller (industrial control computer), which is connected to the process control server, the production planning server and the workshop server at the workshop level via Ethernet.
On the production line, the parameters and quantities to be controlled are:
Traction motors: These include pre-traction motors, post-traction motors, tension control motors, and six lava motor pumps. The pre-traction motors, post-traction motors and tension control motors are controlled by the D/A module of the traction control PLC, which provides analog input signals for the MicroMaster420 inverter, which then controls the operation of the three-phase asynchronous motors, and at the same time controls the starting and stopping of the motors by the relay input/output module.
Temperature control: The continuous salt bath cable vulcanizing unit monitors a total of 32 points of temperature signals and also controls 10 industrial electric furnaces to heat and melt inorganic materials. Vulcanization tube installed by the thermocouple and temperature transmitter, the temperature signal of 1800 ~ 2200 ℃ will be converted into a standard 0 ~ 10V signal, ready for PLC AI module acquisition, while using the relay output to start the non-contact power module switch, so that the electric furnace energized to heat up the temperature, and at the same time, real-time monitoring of the temperature of the molten salt, constituting a temperature closed-loop dosage system, which adopts a PID control method of the current of the electric furnace.
Pressure control: rubber through the rubber extruder unit mechanism on the cable, after traction before the motor, after the motor and tension control motor with the cooperation of the lava vulcanization tube, vulcanization tube in the lava more or less determine the size of its pressure. There are 20 pressure sensors and transmitters installed on the wall of the tube, and their output signals are collected by the AI module of the pressure control PLC.
In the continuous vulcanizing unit, there are also many digital meters and electrical switch states that need to be collected and controlled in real time, so the collection and control of these quantities is done by the auxiliary control PLC.
Real-time monitoring of unit signals, cabinet temperature signals (to prevent individual relays from short-circuiting and causing fire), humidity signals, smoke level and other signals is required in the electrical control cabinet, so the new distributed I/O product ET-200M from SIEMENS is used as the cabinet's on-site monitoring unit.
The basic configurations and modules for the four in-place control units are:
Power supply module: PS307-lK, 120/230VAC, 24VDC/10A;
CPU318-2: 512K byte I/0 expandable to l024 points. The 2nd Profibus-DP interface can be set. It completes the real-time monitoring monitoring of operating status parameters, real-time logic judgment, CPU318 has four kinds of operation options: RUN-P, RUN, STOP and MRES operation mode;
Analog input module: SM331 (8 inputs). It converts the analog output of temperature and pressure transmitters into digital signals and sends the digital signals to the control unit of PLC for PLC to make logical judgment of state parameters;
Digital input module: SM321. 2 16-channel inputs, 1 32-channel input, to complete the motor running status monitoring and PLC motor batch self-starting automatic dosage system operation, debugging status monitoring side, the motor running status signals through the motor operating circuit in the contactor auxiliary contact connected to the module;
Digital output module: SM322 (8-channel output). Accept the instruction of PLC control unit, complete the motor drive signal output, drive the motor operation circuit through the export intermediate relay, complete the motor batch self-start;
Analog output module: SM332 (AO2x12-bit), mainly provides 0~10V control signal to the inverter to control the operation of three-phase asynchronous motor in real time.
Distributed IO using ET200M, including the following components: power supply PS307, Profibus module ET200M, digital inputs, digital outputs, analog inputs.
The PLC uses four frames, three in the RTU signaling cabinet, one of which is a spare expansion frame; the other is in the operator's console, connected via the IM361 expansion, which simplifies wiring and greatly improves reliability.
Dosing implementation strategy
1、Temperature control strategy
Cable rubber vulcanization temperature, pressure by the melting of organic materials and as a carrier to achieve, and the melting of molten salt by the industrial furnace control, real-time control of the current of industrial circuits also realize the real-time control of temperature. Temperature control using PID regulation, when PID regulation, proportional regulation reflects the size of the deviation of the automatic dosage system, as long as there is a deviation exists, the proportional regulation will produce control to reduce the deviation. Differential regulation produces control effect according to the change trend of deviation, and it can improve the dynamic response speed of automatic batching system. Integral regulation produces control effect according to the change of deviation integral, which has hysteresis effect on the control of automatic dosage system and can eliminate static error. Increasing the integral time constant can improve the static accuracy, but the integral effect is too strong, especially in the automatic dosage system deviation will make the automatic dosage system overshoot a large amount, and even cause oscillation. Therefore, in this automatic dosage system, we adopt the following temperature control strategy to form an intelligent dosage system
When the actual temperature is lower than T1, full power heating is used to speed up the response.
When the actual temperature is in the range of [T1~T2], to avoid the integral saturation, the integral term is separated and PD control is adopted.
When the actual temperature is within the range of [T2~T3], PID control is used.
When the actual temperature is located in the range of [T3~T4], adaptive PID control is used.
When the actual temperature T>T0+ξ and in the sampling cycle, the temperature continues to rise, the relay is disconnected
In the sampling cycle, the temperature continues to fall, then the relay is turned on, and the other cases implement PID control. (The dead zone threshold value ξ is taken as 1℃ in this automatic dosage system). This control method not only considers the deviation of measured temperature and set temperature, but also considers the trend of measured temperature, which can reduce overshooting and fluctuation and has the effect of self-adaptation.
When the measured temperature is greater than T4, the fan power is turned on to force cooling. the selection of T1, T2 and T3 is:
T1=T0×87%, T2=T0×95%, T3=T0-20℃, T4=T0+20℃. (T0: set temperature)
3.2 Reliability design of automatic dosage system
3.2.1 Reliability measures for PLC outputs
PLC output metering module within the small relay contacts are very small, arc-breaking capacity is very poor, can not be used directly in the plant-level AC220V ~ 380V circuit, you must use the PLC to drive the external relay, using the contacts of the external relay to drive the DC220v load. At the same time more AC220V ~ 380V solenoid valve internal limit switch with its coil in series with the normally closed contacts, solenoid valve coil energized, the spool action, is to use the valve internal contacts to disconnect the circuit. In this case, to use a small relay with small contacts to transfer the PLC output signal.
Precautions for installation and wiring
Since this automatic feeding system PROFIBUS-DP to complete all the data communication, so the communication cable requires high reliability should be selected SIEMENS recommended and provided by the special cable.
Because of the automatic feeding system used in the high-power silicon controlled device, PLC should be away from strong sources of interference, PLC can not be installed with high-voltage appliances in the same switchgear cabinet, PLC should be away from the power line in the cabinet (the distance between the two should be greater than 200mm). PLC and PLC installed in the same switchgear cabinet inductive components, such as relays, contactor coils, should be connected in parallel with the RC arc-canceling circuit.PLC I / O lines and high-power lines should be routed separately, such as must be routed in the same trunk, the signal line should be shielded cable. AC and DC lines should use different cables, switching and analog I/O lines should be laid separately, the latter should be shielded. Different types of wires should be loaded into different cable ducts or cable troughs respectively, and make them have the largest possible spatial distance.
Dosing software design
Measurement and control software is the key core of this dosing control system, and it is also the difficult point. Including the upper computer measurement software and PLC control software 2 blocks, measurement software is mainly composed of human-machine interface program module, digital signal processing program module, database program module, etc., all using VisualC + + programming, in the control process, the main program can be read and write the relevant data in the database at any time through the DAO using the SQL query statement. After the end of production, the process can be elaborated data statistics operation, you can arbitrarily select the statistical start time and end time, the computer automatically classifies all the measurement data of the time period statistics. And can be visualized in the form of bar charts or pie charts, the relevant data can be backed up, deleted, exported, printed reports and other operations, in order to facilitate manufacturers to understand the product quality situation and take effective measures to improve the production process.
In the upper computer, WinCC as the human-machine interface WinAC system, weighing and dosage system through WinCC time sampling data and events recorded in the database, can be reflected in the form of trend curve temperature, pressure history. It has perfect monitoring function. Including equipment operating status, detection and implementation device operating status, network operating status, process parameters, fault diagnosis and localization, various types of alarm information, equipment / device status information and so on. At the same time, it is equipped with SQLServer2000 database service system, which is a data storage, processing, analysis and service center.