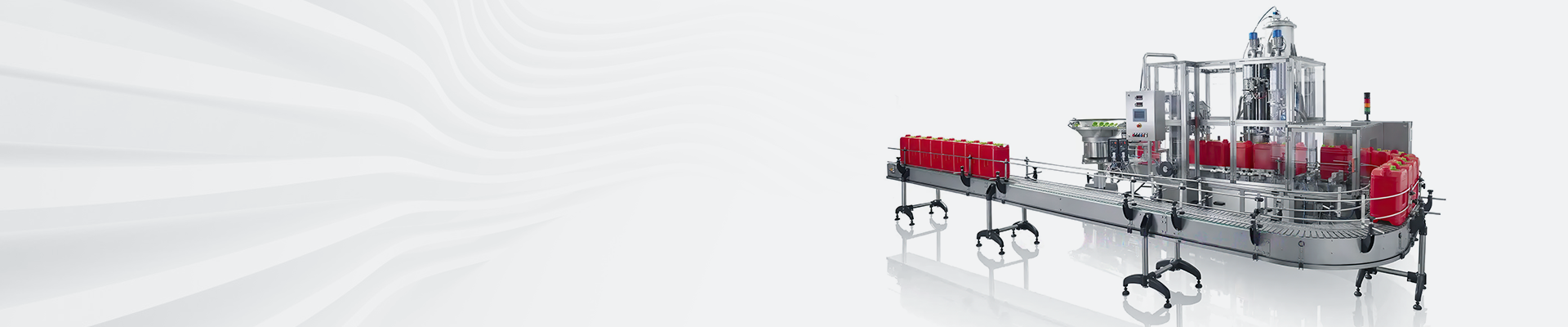
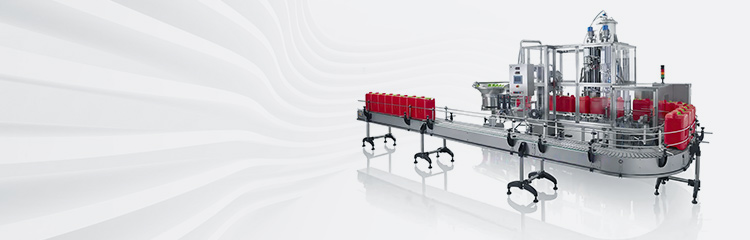

Summary:The LK series PLC of the weighing and batching system collects and processes the data information of the on-site weighing instruments. Through PID adjustment, it controls the frequency of the frequency converter and the opening setting of the water valve, interlocks the valves, pumps, and motors, and displays them in real time. Output status.
Film dosage process introduction
The process of film feeding system mainly includes dosage metering and feeding process.
(1) Batching and metering process
According to the weighing requirements, control the time of each film feeder to the reactor, so as to control the weight of the film into the reactor. Then according to the film and solvent ratio requirements, control each time the solvent feeder discharging time to the reactor, so as to control the amount of solvent into the reactor. This completes the weighing process. The final completion of the required number of times each firing needs to be weighed.
(2) Feeding process
After the completion of each measurement, control the movement of the winch and accessories, the film and solvent mixture transported to the reaction tank. After the bell cap on the film is opened, the mixture enters the film through the reactor tank conveyor for mixing.
The control program of the film feeder includes the control parts of trolley loading, batching, weighing, conveying, discharging, temperature, etc., as well as the display and alarm of analog quantities such as motor current, temperature, pressure, and flow rate. Among them, batching weighing and feeding control is the control difficulty and focus of this system. Each line of the feeding system and digestion system can be interlocked or operated independently.
3 Film batching design
Film weighing and batching machine with the company's LK series PLC as the control core, including actuators, voice-activated alarms, weighing instrumentation system and other parts of the main control of the elevator, classifier, belt scales, crusher, downcomer, screw, valves and other components. Operator station and engineer station are set up in the central control room and networked to the general control room for system monitoring and management of the whole plant.
Film dosage is divided into operator station and engineer station and connected through Ethernet. The setup of the operator station is the same as that of the engineer station, only some functions are limited. The upper computer screen simulates the three-dimensional dynamic process flow in the field, and can set the valves, belt scales, materials, water, etc., and display the information of temperature, flow, current, and the status of the control elements according to the needs. Liquid level adopts proportional bar graph and character data, supplemented by the form of intuitive three-dimensional diagram to display the actual liquid level of each bin. The control of valves and pumps is also operated according to the actual with interlocking relationship. The information of each bin is sampled once every 10 milliseconds and various information is displayed in real time. Various alarms are set up respectively in the system so that the staff can query various information conveniently and quickly.
The upper computer operating system of film dosage adopts the company's for development to realize the monitoring and control of PLC control station. In order to ensure the reliability of the system, the system uses two PCs as a backup, and to achieve database synchronization to ensure uninterrupted operation of the monitoring system.
4 film weighing and dosage characteristics
Based on LK series PLC film batching has the following characteristics:
The dosage control system adopts the company LK series PLC, LK series PLC is mainly for medium and large or high reliability requirements of the automatic dosage system, the product design draws on the success of the company's DCS products, in the harsh working environment can still ensure that a long period of time to work reliably, LK series PLC also passed the two major international certifications of UL and CE.
LK series PLC operation speed up to 0.013us, logic control capacity, support for SD card program loading, support for LD, ST and other languages mixed programming, LK programming software with incremental PID function block, through the configuration parameters can be easily realized PID operation function, PLC real-time acquisition of high-precision analog signals, the sampling period of only 10ms, and then transmitted to the host computer through Ethernet. The PLC collects high-precision analog signals in real time, with a sampling period of only 10ms, and transmits them to the upper computer via Ethernet.
The metering and dosing system controls the frequency of the inverter and the opening setting of the water valve through PID regulation, interlocking the control of valves, pumps and motors, and displaying the output status in real time.
Strong data processing and calculation ability, analog input signal through the A/D conversion, to achieve the over-limit check, maximum and minimum value of the calculation, the flow rate and cumulative flow calculation and other functions. The screen displays the whole process flow and control control link, including trend graph, bar graph and data table of various picking signals. The engineer station and the operator station have the same screen, only some functions of the operator station are restricted. The display includes switching status, pump running and stopping and fault status, and dynamic display of measured values.
Through the upper computer can easily query and statistics of historical data, and can save historical data. Based on the historical data, the trend curve of the relevant quantity can be predicted. Reports can be provided according to the needs of users. Hierarchical management can be carried out according to the needs, and the operator station, engineer station and master control room can be connected via Ethernet. Detailed operation records can be made, making management more scientific and effective.