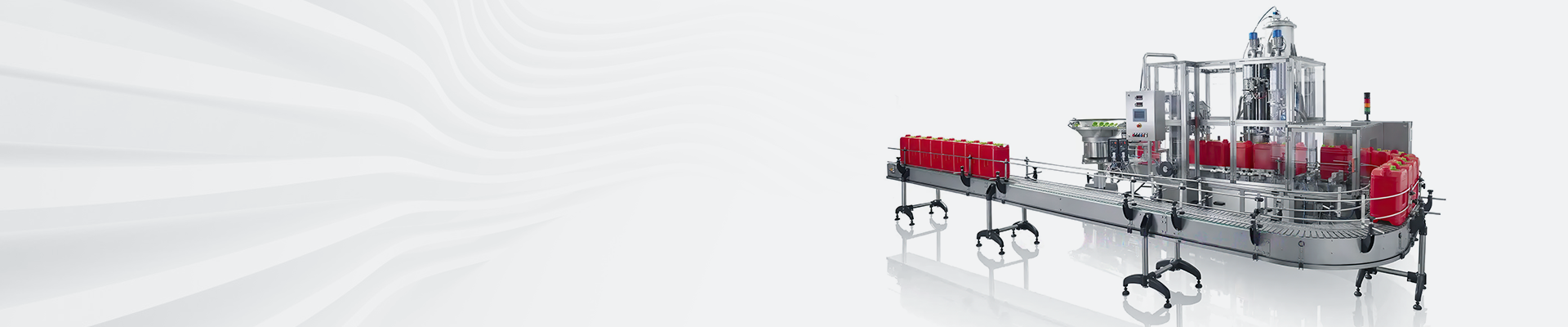
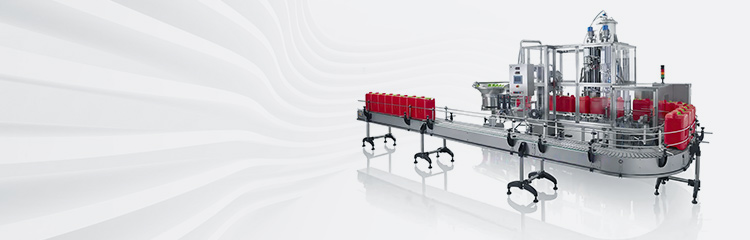
摘要:称重配料系统LK系列PLC对现场称重仪表的数据信息进行采集和处理,通过PID调节,控制变频器的频率和用水阀门的开度设定,联锁控制个阀门、泵、电机,实时显示输出状态。
薄膜是一种重要个工业原料。随着现代工业的发展,薄膜生产的自动化水平越来越高。本文基于LK系列PLC开发出薄膜称重配料系统。LK系列PLC不仅能实现复杂的逻辑控制、顺序控制和定时控制,而且还具有抗干扰能力强、可靠性高、体积小、编程简单、开放性好等特点。上位监控系统采用组态软件开发。通过本系统的应用,大大提高了薄膜配料控制过程的稳定性和可靠性,从而保证系统运营的经济性、合理性和高效性。
薄膜配料工艺介绍
薄膜投料系统工艺主要包括配料计量和上料过程。
(1)配料计量过程
根据称量要求,控制每次薄膜给料器出料至反应釜的时间,从而控制进入反应釜的薄膜重量。然后根据薄膜和溶剂的配比要求,控制每次溶剂给料器出料至反应釜的时间,从而控制进入反应釜的溶剂量。这样完成一次称量过程。最终完成规定的每次烧制需要进行的称量次数。
(2)上料过程
每次计量完成后,控制卷扬机及附件运动,把薄膜和溶剂的混合料运至反应罐。薄膜上钟帽打开后,混合料通过反应罐输送器进入薄膜进行搅拌。
薄膜喂料机的控制程序包括小车上料、配料、称重、输送、出料、温度等控制部分,以及电机电流、温度、压力、流量等模拟量的显示报警。其中配料称重和上料控制是本系统的控制难点和重点。供料系统和消化系统的每条线都可以联锁或者独立进行操作。
3薄膜配料设计
薄膜称重配料机以公司LK系列PLC为控制核心,包括执行机构、声控报警、称重仪表系统等部分,主要控制提升机、分级机、皮带秤、破碎机、下料器、螺旋、阀门等元件。在中央控制室设置操作员站和工程师站,并联网至总控室,以便对全厂进行系统监控与管理。
薄膜配料分为操作员站和工程师站,并通过以太网连接。操作员站的置与工程师站相同,只是部分功能受限。上位机画面模拟现场的立体化动态工艺流程,可以根据需要对阀门、皮带秤、物料、用水等进行设定,并显示温度、流量、电流、控制元件状态等信息。液位采用比例棒图及字符数据,并辅以直观的立体图的形式显示各仓实际液位。阀门及泵的控制也是根据实际进行操作,并有相互连锁关系。每个仓的信息每10毫秒内采样一次,并实时显示各种信息。在系统中分别设置各种报警,使工作人员能够方便快捷地查询各种信息。
薄膜配料上位机操作系统采用公司的进行开发,实现对PLC控制站的监视与控制。为了保证系统的可靠性,本系统采用两台PC机互为备份,并实现数据库同步,确保监控系统的不间断运行。
4薄膜称重配料的特点
基于LK系列PLC的薄膜配料具有如下特点:
配料控制系统采用公司LK系列PLC。LK系列PLC主要针对中大型或对可靠性要求高的自动配料系统,产品设计借鉴了公司DCS产品的成功经验,在恶劣的工作环境下仍然可以保证长时间可靠的工作。LK系列PLC还通过了UL和CE两大国际认证。
LK系列PLC运算速度高达0.013us,逻辑控制容量大,支持SD卡程序下装,支持LD、ST等多种语言混合编程。LK编程软件中带有增量PID功能块,通过配置参数就可以很方便的实现PID运算功能。PLC实时采集高精度的模拟信号,采样周期只有10ms。再通过以太网传送至上位机。
计量配料系统通过PID调节,控制变频器的频率和用水阀门的开度设定,联锁控制个阀门、泵、电机,实时显示输出状态。
数据处理及计算能力强,模拟量输入信号通过A/D转换,实现超限检查、最大最小值的计算、流量及累计流量计算等功能。画面显示整个工艺流程及控制控制环节,包括各种采信号的趋势图、棒图、数据表格等。工程师站和操作员站画面相同,只是部分功能操作员站受限。显示内容包括开关状态、泵的运行停止及故障状态,动态显示测量值。
通过上位机可以方便的查询和统计历史数据,并可以保存历史数据。根据历史数据,可以预测相关量的趋势曲线。根据用户的需要,可以提供报表。根据需求可以进行分级管理,操作员站、工程师站和总控室均可通过以太网进行连接。可以进行详细的操作记录,使管理更加科学和有效。