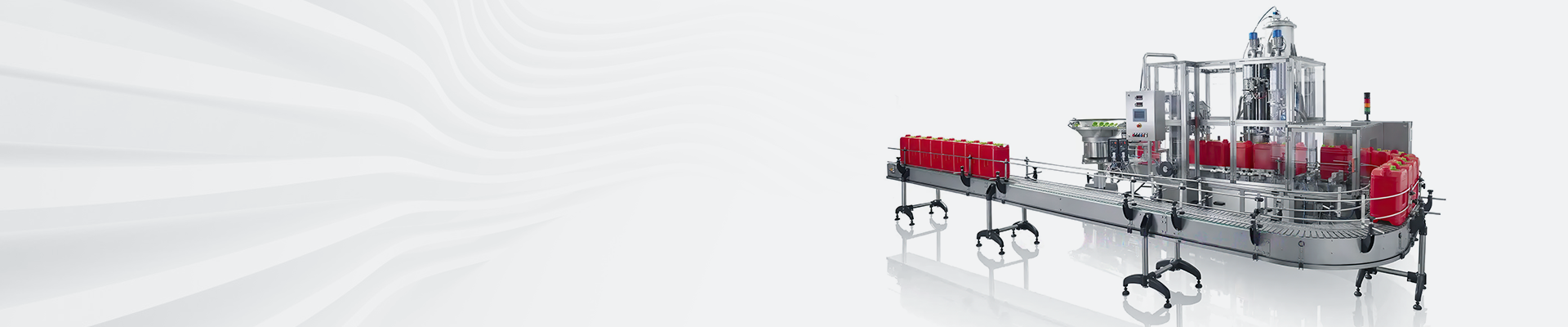
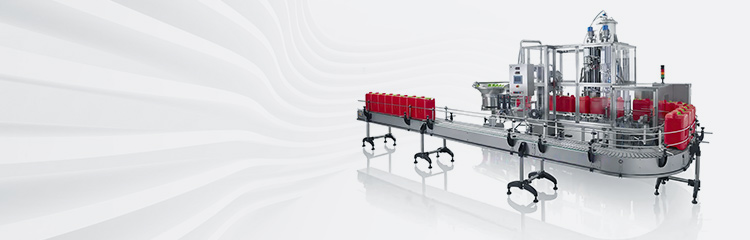

Summary:The check bracket of the hopper scale ensures the stiffness of the carrier, the bearing capacity of the foundation (including the structure), and the linearity, sensitivity and stability of the weighing instrument. Ensure the accuracy, reliability and so on of the load cell. Among them, the linearity, sensitivity, stability of the weighing display instrument and the accuracy of the weighing sensor are particularly important: the accuracy of the measuring instrument is the most important performance of the quality and characteristics of the measuring instrument, and the day of any measuring instrument is to get accurate and reliable measurement results, the essence is to require the indicating value closer to the true value.
1. Question raising
In recent years, with the continuous improvement of the degree of industrial automation, but also with the continuous improvement of product quality requirements in the production process of the industrial economy, some special and accurate weighing instruments are required in some key processes, especially in the coal industry, large weighing instruments have been developed from weighing several "tons to hundreds of tons. Individual places have hundreds of tons of load. At the same time, the rapid development of railway transport, 60~80t/ car freight train maximum transport volume has reached 3000~4000t. So dozens of tons, hundreds of tons, even hundreds of tons of automatic, rapid, measurement of large coal mine hopper scale also emerged.
At present, the main calibration method of the relevant hopper section of the coal industry is to load the standard weight to the hopper scale sensor through the hopper scale body, so that the output signal of the sensor of the hopper scale on the weighing display instrument shows the same weight as the standard weight of the loaded coal. There are many problems to be solved in the calibration of mine and Sichuan hopper scales.
(1) The standards of county-level metrological verification units where some coal mines are located
(2) The depth of the joint profiling method is related to the scale of the geological body, the difference of electrical properties and electrochemical properties, the size of the power supply field and the conduction range.
(3) The test is carried out in the case of a single electrical electrochemistry, but the actual survey environment is much more complex, and various interference factors affect the parameter record of the receiving system, so it affects the reasoning and judgment of the technical personnel on the results.
(4) It is suggested that a set of mathematical models and computer simulation programs should be formed through in-depth study of simulation tests to explore the regularity of the relationship between the electrical and electrochemical differences, the size of the power supply electric field and the conduction range of ap or nη curves and the scale and depth of geological bodies, so as to improve the accuracy of the joint profiling method to infer the scale, nature and depth of geological bodies.
Relatively speaking, some large enterprises with independent verification rights and responsibilities have more complete detection means, not only have a certain amount of tonnage weights, but also relatively stable alternatives.
(3) Coal mines are mostly located in remote areas with inconvenient traffic and complex terrain, and even if there is a sufficient amount of standard weights, the transportation, placement, installation, fixing, unloading and economic cost loss of weights are extremely difficult to solve.
(4) Due to the impact of structural design, installation position and space size, most coal mine hopper scales often fail to reach the minimum value of the calibration weight required by the standard, which affects the calibration effect and can not meet the requirements of the development of the production process.
2 Conditions for the accuracy of coal mine hopper scales
The conditions to ensure the accuracy of the coal mine hopper scale are: reasonable design and manufacture, normal use environment, through calibration and verification, and accurate transfer of quantity value.
Reasonable design and manufacture
To ensure the accuracy of the use of a set of coal mine hopper scales, it is necessary to ensure the quality of the four components of the hopper system, that is, to ensure the stiffness of the carrier; Ensure the bearing capacity and irregularity of the foundation (including the structure); Ensure the linearity, sensitivity and stability of the weighing display instrument; Ensure the accuracy, reliability and so on of the load cell. Among them, the linearity, sensitivity, stability of the weighing display instrument and the accuracy of the weighing sensor are particularly important: the accuracy of the measuring instrument is the most important performance of the quality and characteristics of the measuring instrument, because the daily purpose of any measuring instrument is to obtain accurate and reliable measurement results, and the essence is to require the indicating value to be closer to the true value.
The stiffness of the carrier
In the conventional design, the bearing capacity of the carrier should be considered according to the limit. For example, the coal mine hopper scale should take into account the situation of coal flowing out of the container when the coal feeding mechanism is out of control, which may cause a large local force of the carrier. In this case, the materials used in the structure of the carrier must be many. Therefore, usually on the basis of a reasonable selection of weighing sensors, the stiffness of the carrier is generally 1/600 to 1/1000.
The position of the standard
In the International recommendations of the International Organization of Legal Metrology (OML)R107 "Non-continuous Cumulative automatic Weighing apparatus" and R61 "Gravity automatic Loading weighing apparatus", both require that the bearer should be equipped with appropriate locations or facilities to facilitate the safe and reliable placement of specified weights or substitutes.
It is stipulated in the "Discontinuous cumulative automatic weighing apparatus" that the bearer of the weighing apparatus should be a device that facilitates the placement of the standard number of weights in the table.
As specified in the "Gravity Automatic Loading Weighing Apparatus", the bearer shall have a position or facility for placing the maximum weighing test weight or mass block so that the weight or mass block can be placed safely and reliably.
Correct transfer of quantity values
In JJG555-96 General Verification Regulations for Non-automatic Scales, two calibration and testing methods for weighing instruments used in trade settlement are described in detail. Of course, the calibration of coal mine hopper scales is also applicable. One is to use a sufficient amount of standard weights, but the error of the standard weight of the coal mine hopper scale should not be greater than 1/3 of the maximum allowable error of the corresponding rod weight; One is to apply a prescribed "substitute" that allows a small number of standard weights to be used in combination with the substitute.
Comparison of three calibration methods
Methodological compliance
(1) Standard weight method. The standard weight method is to use weight calibration to test the full measurement performance of the hopper scale under test, and the error of the weight used must be 1/3 of the maximum allowable error of the corresponding weight value of the hopper scale under test. However, for the verified hopper scale, the weighing accuracy of the maximum weight must be tested at the first verification, and the weighing test can be based on the actual use of the subsequent verification, if it is not tested to the maximum volume, at least to 2/3 of the maximum human weight.
(2) Standard weight replacement method. When the maximum weight of the hopper scale under inspection is greater than 1t, there are not enough standard weights to calibrate and test the full metering performance of the hopper scale, other constant loads are allowed to replace the standard weights, provided that there are at least lt standard weights, or standard weights of 50% of the maximum weight, the greater of the two should be taken. When the following conditions are met, the number of standard weights can be reduced instead of 50% of the maximum weight. If the repeatability error of the weighing device is not greater than 013e, it can be reduced to 35% of the maximum volume; If the repeatability error of the weighing device is not greater than 012e, it can be reduced to 20% of the maximum weighing amount; Repeatability error is determined by applying a load of approximately 50% of the maximum weight to the carrier three times.
A standard weight using 35% of the maximum weight needs to be replaced 2 times, and a standard weight using 20% of the maximum weight needs to be replaced 4 times. In the current tens of tons, hundreds of tons of large coal mine hopper scale is so popular, that is, the use of 35% of the standard weight to replace 2 times, but also requires a longer time and larger human and material resources. What's more, with the extension of the test time, some irrelevant errors will be brought to the weighing error. In addition, according to the above provisions, when there are only 10t standard weights below the county level measurement management department, in the calibration and detection of 50t coal mine hopper scales can not use this method.
Methods need to be explored
This paper mainly discusses the feasibility of superposition method to solve some problems in the process of calibration detection. In 1982, the working principle and implementation method of the stack standard machine to detect the load sensor was first proposed, and it was listed in 1989. According to the block diagram of the verification system of force measurement instruments, since the distribution and implementation of the superimposed large standard machine inspection procedures in 1992, the superimposed standard machine has been widely used in various sensor production units in the country. Since the superposition method can detect load sensors with higher accuracy than the weighing device, it can also be feasible to calibrate the inspection hopper scale. Just imagine, if the method of calibrating and testing a set of hopper scales with the superposition method is feasible, then the truck is not pulled by the standard weights, but by the hydraulic system and the calibration and testing structure. This is much better in terms of load capacity and transportation safety.
At present, there is a non-weight calibration method that can meet the requirements of the ore refining production site and production process for the calibration of the hopper scale. The main principle based on this method is the superposition comparison method: The calibration device is composed of frame, jack, standard sensor, supporting weighing instrument and accessories, etc. According to the principle of superposition comparison force measuring machine, the force value generated by the jack is simultaneously transmitted to the pre-calibrated standard sensor and the sensor of the field calibrated hopper scale through the mechanical frame. The weight shown on the weighing meter accompanying the standard sensor is the weight loaded by the sensor that is calibrated to the hopper scale. To calibrate and inspect the hopper scale on site. Adjusting the output of the jack is equivalent to changing the size of the load.
Of course, there are still some technical problems to be solved with the superposition method.
(1) The problem of calibration and detection structure. For off-load calibration detection, the detection structure is relatively simple, and for weighing detection, the detection structure is more complex and cumbersome.
(2) About the loading point problem. For off-load detection, the loading point is acting on the carrier above the load sensor; However, for the accuracy detection of each weighing point, the contact area between the detection point and the carrier will not be large, and the maximum is only acting on a line. It is impossible to have a large area of pressure on the carrier like the weight. It can be seen that the method of using superposition method to calibrate the accuracy of the hopper scale has much higher requirements for the stiffness and strength of the bearer than that of using the weight method.
(3) The stability of the force source. The stability of the force source is an important indicator to reflect the control performance of the system, and also relates to the measurement performance of the whole machine
The accuracy problem. In many places, a simple hydraulic jack is used as a force source, and the superposition method is used to detect the hopper scale. Because each cyclobenzyl is deformed under the action of external forces, the force acting on the force transmission system is elastic, so that a stable indication value is not read from the weighing display.
4 Closing remarks
There are many calibration and testing methods for electronic hopper bars in coal mine. How to select an accurate and effective calibration method based on the structural design of the hopper scale is particularly critical. It is worth mentioning that the superposition comparison method of non-weight calibration of hopper scale is unique in many calibration methods because of its convenient, fast and low cost. Maintenance personnel can also make their own non-weight calibration devices according to the field conditions, according to the superposition comparison method, so that the calibration work is more simplified. The future work can take this as the starting point, further in-depth and detailed research and discussion, so that the calibration and detection work of coal mine hopper scale is more simple, reliable and accurate.