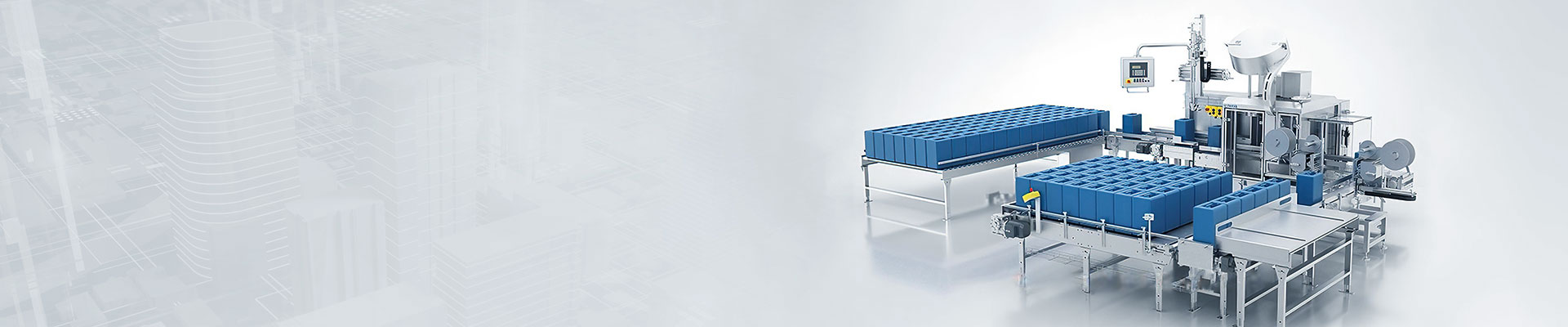
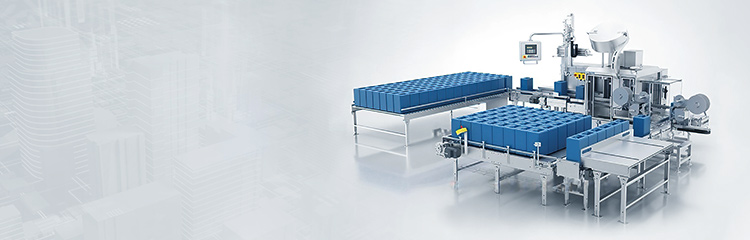
The automatic feeding system has very powerful functions to deal with the packaging process, set the target weight of any package, remove the tare automatically, correct the error automatically, and control the feeding actuator with multi-speed output and have the function of prohibiting the sampling time setting to eliminate the influence of the hopper vibration and rushing material on the metering accuracy, and the function of alarming for exceeding the difference in output, etc. It is equipped with a variety of communication interfaces to communicate with the upper computer, and is equipped with the corresponding operation software. It can be conveniently connected to the central control system of complete sets of production lines. Through the frequency conversion (service) control technology, running in the rigorous logic program of the programmable logic controller (PLC), so that the operation process becomes intelligent, reliable and stable; so that the manual operation becomes very simple.

Feeding system integrates computer technology, automatic control, communication technology and weighing technology into one, with perfect control function, centralized display and operation, convenient data processing, simple installation and maintenance, and easy system expansion. In the structure of the computer centralized control system to solve the "danger of centralized" problem, to achieve "centralized management of the danger of decentralized", to complete the data acquisition and process control to support a variety of communication protocols, to provide users with a variety of equipment support, colorful dynamic screen and the system's powerful features, so that you can easily operate with a strong scalability, easier integration with other systems, more effective protection of the user's investment. The redundant station utilizes two redundant CPUs, which improves higher availability and security. Based on the principle of one out of two, the switch automatically switches from the running system to the other in the event of a failure. Dual power supplies or industrial Ethernet communication modules can be provided and combined for each subsystem. Safe, reliable and advanced and practical system design chooses the mature and advanced distributed computer control system to decentralize the dangers and improve the reliability of the system under the premise of centralized management of information and scientific operation in the production process, collects all kinds of data on the site with PLC and transmits them to the central control room for centralized monitoring and management through high-speed network, and the mainframe of the central control room also transmits the control commands through the high-speed network to the The host of the central control room also transmits the control commands to the PLC measurement and control terminal through high-speed network to implement the decentralized management of each unit.
The mainframe of the automatic feeding system adopts an industrial PC as the upper computer (industrial computer, fully compatible with ordinary computers, more adaptable to harsh industrial environments) + PLC + weighing module (or weighing signal sampling board) + load cell + weighing actuator. It can contain measurement control host (host computer), weighing software (measurement software/control software), plc weighing control instrument, load cells, hopper scales which can be incremental and decremental; and most of the cases are controlled by frequency converters.
Weighing and feeding system will also take the upper computer an industrial computer, the lower computer - PLC programmable controller, powder dosage, liquid dosage, micro dosage and control system and other parts of the composition. This weighing and dosing control system is an automatic Weighing system with vacuum feeding, dosing screw quantitative dosing, weighing hopper automatic weighing and dosing, and cumulative weighing at the same time. It is suitable for accurate measurement of materials and automatic batching operation in the production process.
The automatic feeding system has the following advantages:
(1)The whole system adopts centralized structure, good openness, easy to expand, stable and reliable performance" structure mode: "upper computer + PLC system + solid dosage control instrument", the connection of each part of the equipment adopts RS485 field bus, simple and reliable structure.
(2) The weighing instrument adopts high-quality controller, which is characterized by high precision, high reliability and strong anti-interference ability. The load cell adopts high-precision weighing module. The weighing module is easy to install and maintain.
(3) The weighing and feeding system uses a powerful computer monitoring and management function, real-time collection, timely display of operating conditions and relevant data, the screen image is realistic, strong sense of dynamics; can automatically complete the system dosage process, the computer screen real-time display of the workflow of the weighing and dosage control system, the software is simple to operate, the screen is realistic.
(4) The product is highly reliable, the upper computer software is set up to protect the running password and important parameter password modification, and the user realizes hierarchical management, which can arbitrarily define the authority of personnel. Intelligent reporting software for production management to provide a large amount of data information, such as the list of dosage results, raw material consumption list, production volume list, the formula to use the results of the record, etc., according to time, formula and other production of shift reports, daily, monthly and annual reports and other statistical and printing functions.
(5) Accurate and timely response to faults, can automatically display or print the time, nature and location of the fault, and sound and light alarms; control mode can be divided into remote automatic, local automatic, local manual and local instrumentation control and other operating modes.