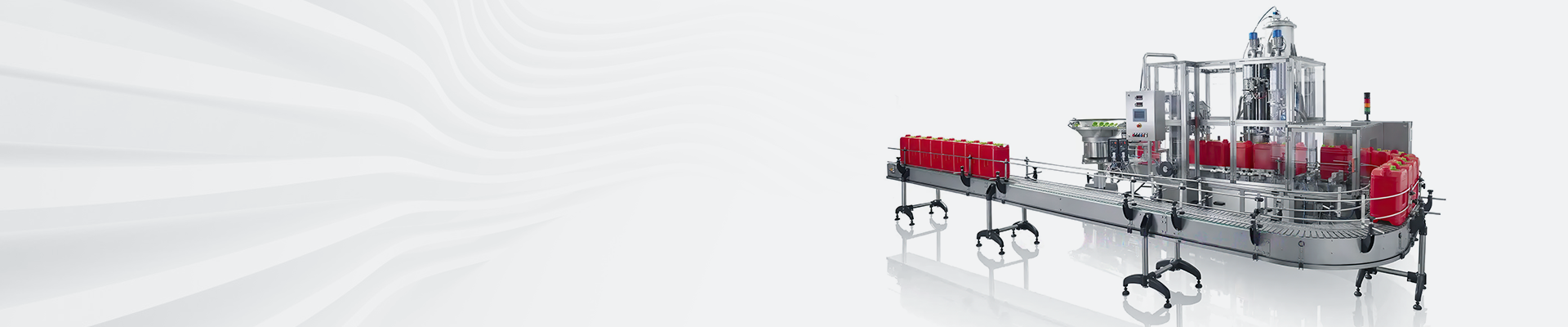
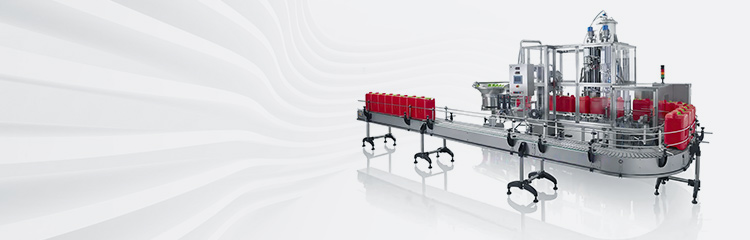

Summary:The automatic batching control system mainly consists of a feeding system, a storage system, a conveying system and a weighing control system.The double-tube pneumatic conveying of carbon black can ensure the conveying air pressure and speed. The inner rubber tube can reduce the breakage of carbon black caused by conveying and can resist carbon black erosion. The bag filter can effectively control the flying of carbon black during conveying.The weighing control system can complete the weighing and feeding of carbon black, oil and rubber.Its feeding system adopts the structure of microcomputer and PLC, which reduces the complexity of the system.The software adopts a full Chinese interface and is very convenient to operate.
Carbon black is one of the important raw materials for tire production, its density is small, the amount of large and easy to pollute the environment, so carbon black storage and delivery has become the focus of attention of many tire factories and equipment manufacturers, large-capacity compactor is also only with advanced compactor automatic dosing control system (hereinafter referred to as the mixing machine) supporting the use of in order to give full play to the effectiveness, especially in the production of radial tires, the mixing machine has been an indispensable key Batching equipment.
The structure of the mixer is mainly composed of feeding system, storage system, conveying pipeline, weighing control system and feeding system.
1、Feeding system
Feeding system consists of unpacking bucket, carbon black tanker, bag filter, induced draft fan and so on. The unpacking hopper adopts double-side feeding structure, which can be fed in two directions at the same time. The unpacking hopper will automatically add the carbon black powder from the carbon black tanker to the carbon black pressure conveying tank. The bag filter can effectively avoid the carbon black flying and improve the working environment.
2、Storage system
The storage system consists of large storage silo, bag filter, induced draft fan, balance valve, screw feeding device, storage hopper, etc. Carbon black sent by the conveying system is sent to different large storage silos for storage according to the models. When conveying the carbon black, the induced draft fan will automatically open and control the carbon black flying through the bag filter, the balance valve will automatically open to balance the pressure in the big storage silo, the screw feeding device at the bottom of the big storage silo will send the carbon black to the storage hopper to wait for further conveying to the weighing system, and the balance valve will be automatically closed after the conveying is finished. The large storage silo is designed with 3 levels of control: high, medium and low. When the material level is in the low level must be added, in the high level must stop adding material.
3、Conveying system
Conveying system is composed of gas source, pressure conveying tank, distribution valve and double pipe conveying pipeline. After the carbon black is sent to the pressure conveying tank by unpacking hopper, compressed air will be sent to the tank to blow the carbon black up, so that the carbon black is in the floating state. When the pressure in the pressure conveying tank reaches a certain value, keep the pressure for 2-3min, then open the unloading valve, and at the same time open the compressed air valve on the conveying pipeline, under the action of compressed air, the carbon black is conveyed along the conveying pipeline to the storage tank. In order to ensure constant conveying pressure, there will be compressed air of the same pressure supplemented to the conveying pipeline at certain intervals, which can ensure the conveying speed. The conveying pipeline is a double-pipe structure, the inner pipe is made of flexible rubber material, which can resist the erosion of carbon black and reduce the crushing rate of carbon black particles when conveying carbon black at high speed. The outer pipe is made of hard aluminum alloy, which can bear certain pressure.
4、Weighing control system
The weighing control system is divided into three parts: carbon black weighing and feeding, oil weighing and feeding and rubber weighing and feeding.
(1) Carbon black weighing and feeding
Carbon black weighing and charging consists of day storage hopper, bag filter, balance valve, charging screw, central bag filter, recovery screw, carbon black weighing module, carbon black calibration scale and discharge turnoff and other parts.
Carbon black is transported to the day storage hopper through the conveying system to wait for weighing, when it starts weighing and charging, the charging valve at the bottom of the day storage hopper opens, and the charging screw moves to transport the carbon black powder to the carbon black weighing scale (when transporting the carbon black, the central bag filter adsorbs the fluttering carbon black on the filter bag of the bag filter in order to prevent fluttering and contamination of the carbon black). After the carbon black weighing is finished, the disk valve of the carbon black weighing scale opens, and the carbon black is unloaded to the carbon black calibration scale along the charging pipe to calibrate the accuracy of the weighing. After checking is completed, the discharge valve of carbon black checking scale opens, and the carbon black is sent to the refining chamber of the refining machine through the pipe through the discharge fork.
Spraying anti-adhesive and anti-corrosion chemical paint inside the hopper not only makes the carbon black discharging smoothly and prevents the carbon black from adhering to the inner wall, but also effectively prevents the carbon black from corroding the hopper and prolongs the service life of the hopper.
In view of the large-capacity refiner mixer dosing cycle is short, high production efficiency, weighing the characteristics of the large volume, between the carbon black weighing and feeding system set up an intermediate calibration scales hopper (sensor-type), this configuration can effectively solve the transition and storage of large-capacity carbon black to shorten the cycle of dosage and charging, while at the same time can be weighed many times to ensure the accuracy of the weighing and charging of the mixing of the special requirements of the process, and the carbon black unloading process of secondary monitoring, shorten the refining cycle. At the same time, it can be weighed several times to ensure the weighing precision and the special process requirements of mixing, and it can monitor the unloading process of carbon black twice to shorten the refining cycle.
Because of the small density of carbon black, easy to fly, easy to clog in the pipeline when weighing and unloading, so there is a connecting device between the weighing hopper and the intermediate hopper. The connecting device is closed when weighing in the hopper and opened when unloading to ensure that the carbon black is discharged quickly and efficiently. The hopper weigher adopts 3-point support and suspension sensor, which can ensure the weighing accuracy by the uniform force at 3 points. The weighing sensor adopts S-type sensor, which can effectively reduce the influence of eccentric force on weighing. Discharge fork has an inlet and two outlets, one outlet is connected to the refiner, the other outlet is connected to the outside world, in the manual calibration weighing scale, the carbon black can be unloaded into the container in order to manually weighing.
(2) Oil weighing and charging
Oil weighing and feeding is composed of oil scale, intermediate storage hopper, oil injection pump and oil pipeline. Oil in the oil scale weighing, unloading valve open, oil unloaded to the middle of the storage hopper for temporary storage, at this time the oil scale can continue to weigh the next batch of oil. The oil injection pump will start to inject the oil in the intermediate hopper into the refining room through the oil injection port of the refiner, meanwhile, the equipment will select the corresponding oil injection pump according to the different oil injection methods and choose the appropriate pressure to inject into the different oil injection holes of the refiner.
(3) Rubber weighing and charging
Rubber weighing and charging consists of rubber supplying machine, rubber scale and feeding belt. The lump rubber is weighed directly on the rubber scale and then put into the refining chamber of the refiner through the feeding belt. Sheet rubber is fed to the rubber scale by the rubber feeder, and then fed to the refining chamber.
5、Feeding system
The control part of the dosing machine is composed of PLC and ten upper computer, which is a two-stage control; PLC adopts advanced bus control mode, and there are remote workstations under it, which are divided into powder system workstation and rubber and oil system workstation. Each workstation will be their respective signals and data collected back to the PLC system, the system unified control. Microcomputer control and on-site equipment connected by cable, changing the previous situation that all connections must be received in the control room, reducing the amount of cables and bridges in the installation process, saving investment, while also enhancing the system's ability to resist interference, and greatly facilitates equipment maintenance and repair. All signals are transmitted by digital means, with high precision and reliability.
Control software based on the windows platform using VB programming, full Chinese interface, menu-based human-computer dialogue, dynamic graphics management and open management, the operation is very convenient. It can monitor the parameters such as process formula, time, power, temperature, pressure and speed of refiner, optimize the mixing and network function. The unique touch screen rubber scale terminal allows for on-site modification of recipe settings, replacing the main control room for pre-machine operation and dynamic monitoring of production.
Conclusion
The automatic mixer dosing system, put into use in the factory, can maximize the efficacy of the refiner, improve product quality and production efficiency. Due to the use of airtight carbon black double tube pneumatic conveying, completely solved the carbon black in the transportation, storage and use of the process of leakage and flying brought about by environmental pollution, reduce the waste, greatly improve the working environment of the refining workshop, has a good economic and social benefits.