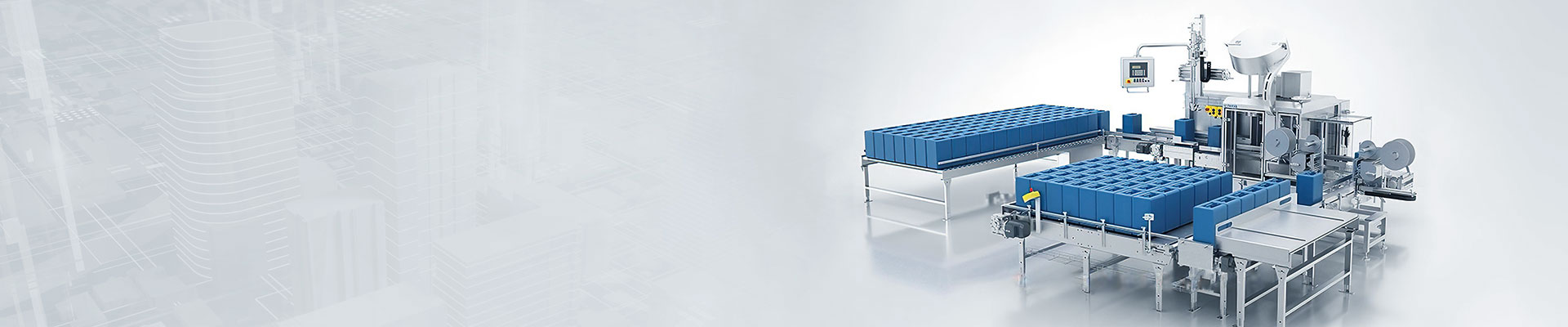
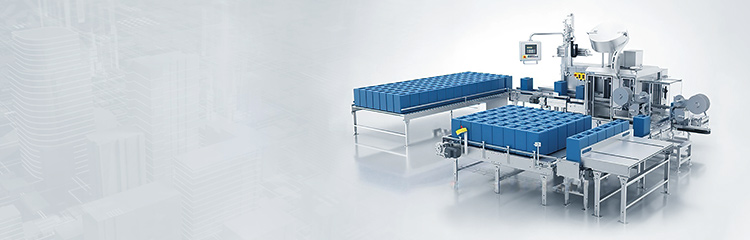
The weighing system of garbage truck realizes garbage identification, and the system dynamically collects the information of electronic license plate of garbage can during the process of garbage lifting. Realize the automatic identification function of garbage can weighing and metering, and merge the automatically collected weighing data information into the weighing management system.

The Electronic scale of garbage is mainly designed for urban garbage metering, and a new Weighing system is designed. The electronic scale adopts high-precision AD acquisition integrated circuit and high-speed microprocessor, and uses dynamic sampling technology and fuzzy algorithm to realize dynamic calibration and dynamic weighing. Compared with the traditional garbage metering device, it saves time for users and improves efficiency.
Moreover, the electronic scale has high precision, accurate measurement and stable performance, and can be used as a measuring instrument. The measurement accuracy reaches the standard of * * * scale, which controls the loading weight from the source and reduces the tedious work of weighing again after loading.
Non-inductive weighing, the weighing process does not need to stop, and high-precision weighing is realized in the process of overturning and lifting the trash can;
The weighing sensor dynamically weighs in the whole process, with quick response and fast and efficient weighing;
The weighing accuracy can reach 3%;
Adapt to a variety of trash can specifications, automatically identify large and small barrels and weigh them;
The weighing of garbage truck can obtain various data such as total weight, net weight of garbage, tare weight of garbage can and so on, which can be switched freely;
Single/double station independent bucket number accumulation function;
Statistical function of total cumulative weight of garbage collected and transported in a single day;
Can automatically identify the identity information of trash cans and associate it with the weight data of garbage collection and transportation;
Can realize vehicle fuel consumption information management;
Photographing and video monitoring functions of vehicle working process;
4G network remote data communication function;
BD/GPS dual-mode positioning function;