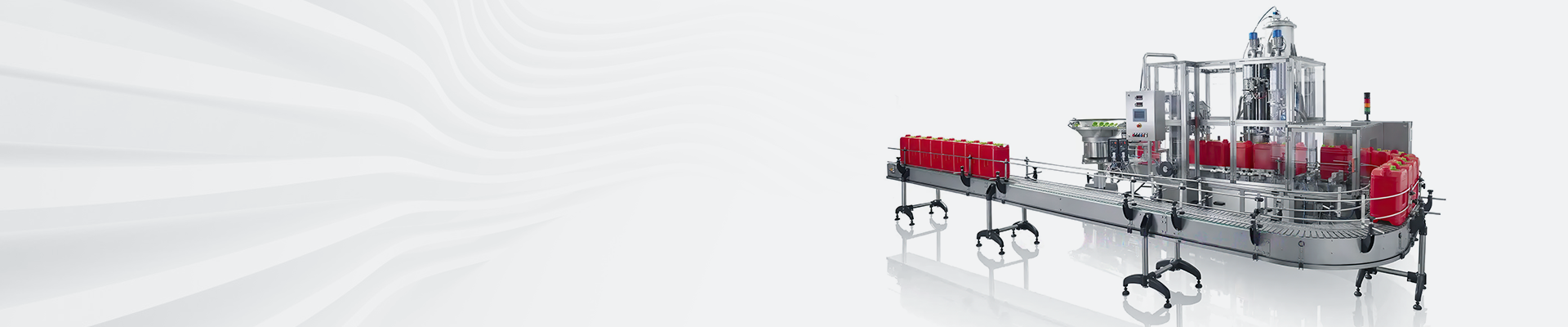
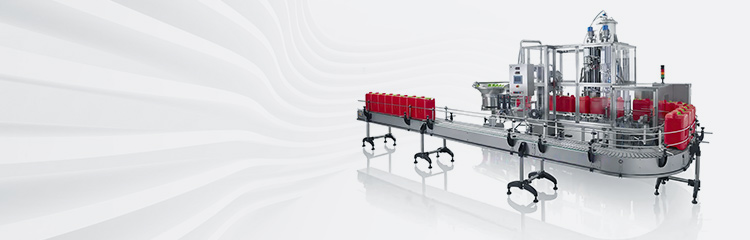

Summary:The batching system enables the on-site workstation to complete the collection and control of on-site pressure, temperature, flow, valve opening, etc., and completes signal processing, sequence control, control algorithm, PID adjustment and fault diagnosis in the on-site station.
Generally in the raw material feeding system, mixing and batching, powder made of distribution control room, respectively, set up on-site control workstations, central control room, engineer station, operating station, and on-site control workstations connected through the communication bus to form a network. The automatic dosage system program is characterized by decentralized control, centralized operation and centralized management. The automatic dosage system is highly reliable, easy to operate and maintain, which is convenient to realize centralized command, scheduling and management of the whole plant, and is conducive to the improvement of the output and quality of the products.
The thermal parameters of the whole production process are automatically detected and controlled, and the starting and stopping of some electrical equipment are automatically controlled. Each on-site workstation completes the acquisition and control of various analog signals (pressure, temperature, flow, valve opening, etc.) and various switching signals (motor, position and material level, etc.) on site, and completes the signal processing, sequence control, control algorithm, PID adjustment and fault diagnosis, etc. in the on-site station.
The main screen and function of automatic batching machine can display various screens on the screen of engineer station and control operation station, and the screens mainly include:
① Analog schematic diagram of the whole production line, which can show the actual status of each important equipment and the direction of process flow;
② process screen, sub-section of the process simulation screen, which can display the process flow, dynamic parameters and equipment operation status, and issue an alarm for abnormal conditions;
③ Real-time trend screen, displaying the trend of dynamic parameters in the current few minutes, and the time can be set arbitrarily;
④Control group screen, adopting the form of simulating the conventional instrument, clustering the relevant regulators on one screen, which is convenient for operation and observation;
⑤ Adjustment screen, the control object is the regulating circuit, including regulating parameters, initialization, starting, stopping, and realizing manual/automatic non-perturbative switching;
(6) Alarm summary screen, displaying all alarm information, making it easy for the personnel concerned to check the operation and operation of the equipment in the previous period of time;
(7) Historical trend screen, displaying the running trend of important parameters in the past few days, providing analytical data for technicians to solve the problems of automatic process dosage system or equipment;
(8) Report screen, according to the user requirements of the automatic dosage system of important information into electronic reports. Each screen can be switched, the operator can monitor and supervise the production situation of the main workshop in the whole plant at the operation station, operate, modify the parameters and start and stop some equipments related to the automatic dosage system, etc., and print the alarm information and all kinds of production reports randomly. The engineer station can configure, program, debug and maintain the whole automatic batching system, and can modify the program online without affecting the operation of the whole automatic batching.
Detection and control of each batching
Detection and control of raw material and powder mixer: detecting pressure, speed and operation status of raw material batching scale; detecting operation status of batching belt at the bottom of warehouse; detecting temperature of axle tile, oil pressure of axle tile and flow of cooling water at the entrance of mill; detecting temperature of axle tile, oil pressure of axle tile and flow of cooling water at the exit of mill; detecting temperature of oil of speed reducer or temperature of axle shaft, power of mill, negative pressure of mill at the exit of mill, pressure difference of cyclone collector and electric flow of powder separator; realizing the operation of batching equipment and the control of batching machine; and realizing the operation of batching equipment. The electric current of the mill; realize the sequential start-stop control of the dosing equipment; detect the mill sound, change the empirical control, and reduce the empty grinding and full grinding conditions. Vibration detection, according to the different motor models and power, the installation and detection position is different, the vibration sensor of the main motor of the powder mill is installed on the reducer, and the dust collector fan and powder selector fan of the mill tail outlet pocket are installed on the bearing seat. Mill main shaft tile temperature monitoring and oil pool, oil temperature monitoring and control, protects the shaft tile, avoids frequent motor startup, and saves energy. Control of mill differential pressure and reduction of mill vibration. Frequency conversion speed control belt scale is selected as the feeding and measuring equipment, which does not need vibrating feeder, reduces the failure points and ensures the long-term stable operation of the weighing and batching system; it completes the quantitative feeding control of single scale and the proportional tracking control of multi-scales, which improves the metering and controlling precision of the batching system, and makes the quality of the raw material out of the mill reach the technological requirements of the raw material batching system. The mill output is optimized according to the working conditions of the automatic mill dosing system. The process screen displays all detected conditions for effective decision making by the operator and manager.
② Mixing and feeding station detection and control of incoming frequency-controlled conveyor, mixer conveyor, bucket elevator, feed frequency-controlled conveyor, sealed belt scales, frequency-controlled pipeline pumps, pre-wetting machine, ball tray, ball conveyor belt and other equipment operating conditions; detection of blower left and right side oil temperature, power, wind pressure at the exit, air volume, valve opening; into the kiln wind, into the kiln wind pressure; detection of pulverized coal silo, silo material level; Detecting pulse dust collector flue gas temperature, pressure, flue gas composition; detecting the temperature of mixing and batching high temperature zone, temperature at the waist wind, cooling zone temperature; detecting the temperature of clinker out of the kiln, unloading speed, unloading volume; detecting the water flow of the ball pan, the material flow; realizing the sequential start-stop and fault-stopping control of the automatic ball batching equipment; real-time adjustment of the air consumption according to the calcination conditions (adjusting the opening of the control valve of the Roots blower); real-time adjustment of the air consumption according to the Polyurethane calcination thermal monitoring process, automatic material and water metering, proportional tracking control, long-term and stable to ensure the quality of pre-water into the ball, to achieve rapid calcination of small balls of powder process requirements, to achieve the purpose of improving clinker production, quality; a series of process flow charts and trend charts of the main parameters to give a timely production reports, graphic copies, to facilitate production management and accident analysis; the operator can be modified on-line. Parameters.
The weighing feeder adopts vertical hollow shaft motor to drive the screw directly, the motor is brushless DC motor, controlled by special brushless DC controller. After the intermediate transmission mechanism is omitted, all kinds of disturbances on the light rod act on the motor shaft without buffer, making the system susceptible to the influence of downhole working conditions (mainly the change of crude oil dynamic liquid level and the viscosity of crude oil). Screw pump drive in the controlled object changes and adjust accordingly, when the system parameters change, screw using a multivariable, nonlinear, time-varying system, the speed loop using fuzzy adaptive PID control to achieve. The screw adjusts the parameters of the controller online to complete the tracking of the given inputs, accelerating the adaptive process and reducing the tracking error at the same time. Through the microcomputer connected to multiple weighing feeder, can be used for silo dosing, while dosing materials can be as many as 9 to 12 kinds of materials, to carry out a variety of materials for continuous dosing, based on the structure of the bucket scale, can be directly calibrated by weights, through the weighing hopper of each instantaneous test to calculate the actual amount of discharged material, and then closed-loop adjustments, so that you can achieve a high degree of control accuracy, in general the cumulative accuracy of 0.5 percent. Because of the bucket structure calibration and maintenance is also much easier than belt scales, proving that in the raw material composition fluctuations in the single control of raw material CaO, Fe2O3 can not stabilize the value of the three rates of raw material, and further clarifies the concept of rate dosing. It reveals the defects of calcium and iron control, and puts forward the optimal callback method to ensure the qualified rate value under calcium and iron control, which maximally avoids the defects of calcium and iron control.
Weighing and mixing machine by the spiral feeder and a set of upper computer by the weighing module and weighing instrument and communication cable, the weight indicator also provides RS232, RS485 interface ADSL, GPRS, CDMA, fiber optic and other communications, the upper computer monitoring and control using Windows operation, programming software and configuration software control using the PID regulation of metering deviation and the combination of frequency conversion speed control, frequency conversion control in the The hardware setting, parameter setting and software design process. Multi-output each batching and conveying production line is strictly coordinated and controlled to monitor and regulate the material level and weight timely and accurately. A two-stage computer control system is composed of programmable weight indicator and metering module, which connects on-site weighing instruments, control field equipment, weighing feeder frequency converter, etc. through bus, with higher degree of intelligence and fast processing speed. In the process of batching production process, the main material and auxiliary materials according to a certain proportion with the completion of the conveyed materials for measurement. It mainly undertakes real-time control of conveying and weighing process, and completes fault detection, display and alarm, and also outputs signals to the frequency converter to adjust the screw speed.