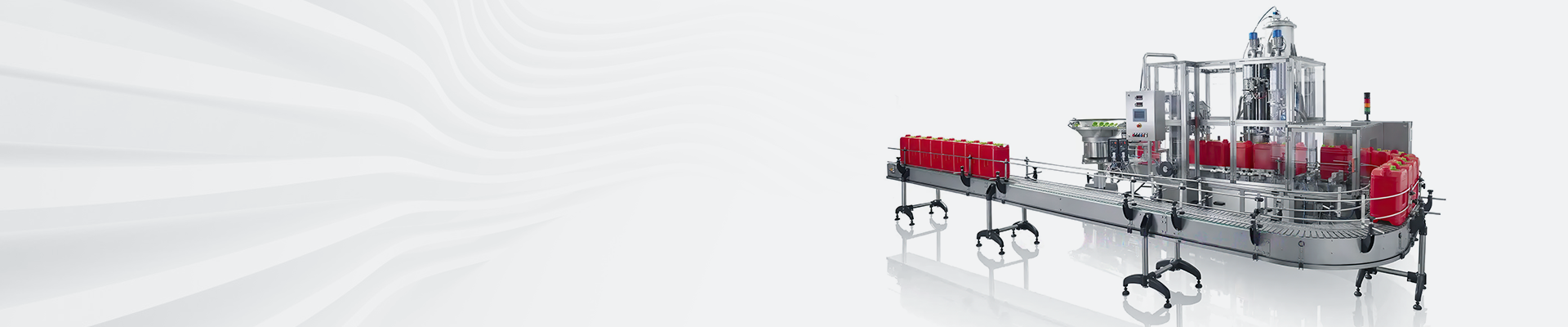
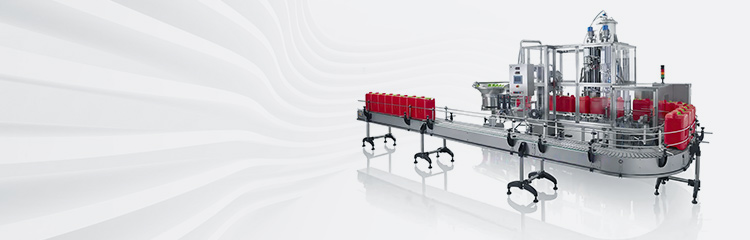

Summary:The dynamic batching system is imported into ERP through the integrated interface and can be integrated with the dynamic system of material inventory management. It can automatically read the data and deduct the available quantity, and can also guide the batching of on-site operations.
1 Ferrosilicon batching process and production flow
Refining ferrosilicon is characterized by the need to process a large number of raw materials, in accordance with a certain proportion of weighing, mixing to form a uniform material, and the quality of the ingredients largely determines the production of technical and economic indicators.2. The main raw materials used in the batching of wood chips (1 material silo), silica (2 material silo), coal (3 material silo), petroleum coke (4 material silo), steel chips (5 material silo), etc., and the process of its batching overall The batching process as a whole can be divided into four main production links such as quantitative feeding of five materials, weighing, fabrication, mixing material conveying and unloading, etc., which involves the following production equipment: five material silos, five hopper scales, five vibrating feeders, five fabrication belt conveyors, one horizontal material conveyor belt conveyor, one large-inclination belt conveyor, and falling and unloading devices, etc. The feeding system adopts the "feeding system" principle, which is the most suitable for the production of coal, petroleum coke and steel chips. The feeding system adopts the weighing method of "single scale for single material", each scale can weigh at the same time, uniform fabric, high weighing precision and fast batching speed.
The process flow of ferrosilicon batching is that silica, fine coal, steel chips and auxiliary materials are weighed separately according to the formula, and when the weighing is finished, the system will check whether the conditions of fabrication are met, such as the feeding vibrator is stopped and the material transportation belt is started, etc. If the conditions of fabrication are met, the system will check whether the conditions of fabrication are met, and the system will check whether the conditions of fabrication are met. If the fabric conditions are met, the system starts to fabricate in the specified order, so that all kinds of raw material header alignment, layered in the horizontal material conveyor belt machine, the mixture of material through the large inclination angle conveyor belt machine into the top of the furnace bins, open the bins at the bottom of the unloading gate, and ultimately will be sent to the mixture of materials in the mineral heat furnace. After a certain delay, the system begins to match the next batch of raw materials.
2 ferrosilicon feeding system composition
The system adopts the upper industrial computer and the lower machine PLC composed of two-stage control system. The upper and lower bits communicate via TCP/IP through ETH-iBUS Ethernet converter module, and PLC communicates with on-site weighing instruments and frequency converters for feeding, cloth and conveying using MODBUS protocol.
The upper computer completes the centralized management of the whole process and uses the configuration software to realize the dynamic monitoring of the progress of the dosage process and the real-time monitoring of the working status of each device in the system, as well as the printing of the dosage data, alarm records and faults, etc. The lower computer communicates via MODBUS Ethernet converter module.
The lower computer realizes the real-time data exchange between PLC and weighing instrument and frequency converter through MODBUS communication protocol, and completes the processing and calculation of batching data as well as the control of batching process. As PLC accepts communication signal, no analog conversion calculation is needed, which will not increase the extra error; PLC directly controls the dosage equipment to reduce the risk of system failure, which really realizes the purpose of centralized management and decentralized control.
In the process of dosage, PLC constantly reads the weight value from the weighing instrument, compares it with the set formula and program, makes a judgment, and controls the starting and stopping of the feeder and the fast and slow feeding. After the dosage is completed, the start of the transport belt and the cloth electric vibration machine for the cloth, mixing material delivery.
Hardware design of batching machine
To ensure the accuracy and rapidity of dosage, it is necessary to make a comprehensive analysis according to the process requirements, the characteristics of the materials to be prepared and other factors, firstly, choose a reasonable weighing method and the structural form of the production line, and then correctly select the weighing sensor, weighing instrumentation as well as the design of a reasonable overall control program and comprehensive consideration of other relevant factors, so as to design a high precision, low cost, and comply with the requirements of the automatic dosage system.
3.1 Hardware selection
In order to meet the ferrosilicon batching production automatic control system design requirements, the selection of Siemens SIMATICS7-200PLC and high-performance Advantech industrial control machine constitutes an automatic control system, according to the design requirements of the system selected the main hardware products are as follows.
1) Upper industrial computer. Advantech industrial computer: dual-core 2.16G, 2G memory, hard disk 500G, 22x2.54cm LCD monitor.
2)Module configuration of lower PLC. As the PLC of the feeding system communicates with the on-site weighing instrument and inverter with MODBUS field bus, there is no analog input and output to reduce the corresponding IO points, so the control function can be realized by selecting Siemens S7-200 series PLC.
Central processing unit: CPU226; expansion module: EM221 digital input 2 blocks, EM223 digital input and output 1 block communication processing module: Dalian Dejia International Electronics Co., Ltd ETH-iBUS Ethernet converter 1 block.
3) Load cell. This system selects the cantilever beam type weighing module with a range of 1000 kg. each weighing hopper adopts 3 pieces of measuring modules in parallel group weighing mode (through the junction box pooling) to realize the purpose of weighing.
4) Weighing instrument. The system adopts weighing instrument (with MODBUS communication interface RS485) to perform high-speed and high-precision A/D conversion of weighing data, directly convert the ms signal into digital signal, and transmit the weighing signal to PLC by standard MODBUS protocol, and then PLC carries out data processing, calculation and control.
5) Inverter. The system selects HLP-NV series multifunctional and high-performance vector frequency converter of Zhejiang Hailip Electronic Technology Co., Ltd. for accurate speed regulation to ensure the high speed and high precision of the batching process.
3.2 Electrical control system
The electrical control system consists of PLC control cabinet, electrical control cabinet and local operation box. The electrical control cabinet provides power supply for PLC control cabinet, on-site operation box, on-site equipment, indoor lighting, etc. and centralized management. The front side of the electrical control cabinet is for the power control circuit, including power switch, fuse, contactor, etc., and the back side is for the feeder frequency converter and wiring terminals. The local control box is installed near the field equipment, which can start and stop the single equipment independently, and there are "local/remote control" switch, start button, stop button and indicator light on the control panel.
Software design of dosing system
According to the analysis of the workflow of the weighing and mixing machine, the PLC program design adopts the structured programming method3, which divides the whole program into several parts, such as the main program, the communication subroutine, the dosage subroutine, the fabric subroutine, the conveying subroutine, the dosage algorithm subroutine and the fault alarm subroutine. The system is divided into two operation modes: manual/automatic, automatic control including single-step and continuous mode; manual operation is mainly used in system debugging, maintenance or when PLC failure occurs.
The main program calls different subroutines to realize the overall function. The host computer transmits the dosage data and the start signal to the PLC and starts to execute the dosage application program. During the dosage process, the communication subroutine constantly reads the data from the weighing system; the start/stop of the feeding frequency converter and the fast/slow dosage are controlled by the dosage subroutine; the mixing and conveying process is realized by calling the fabric subroutine and the conveying subroutine. Ferrosilicon 4.1 Batching program design
When the system meets the conditions that all the equipments are in "remote control" status, the fabrication process is finished, the weighing hopper is empty, the dosage parameters are set reasonably, and there is no fault signal of the dosage frequency converter, then the system will start dosage.
In automatic dosage, when the target value of material fast dosage is far less than the set value, PLC sends out high-speed instruction, so that the vibrating feeder works in high-frequency state, the material falls into the weighing hopper quickly, reduce the feeding time to improve the feeding efficiency, and at the same time in the real-time display of the net weight of the material on the upper computer; when the material reaches the target value of the fast dosage, the frequency converter is switched to the small vibration frequency, the slow vibration of the material to reduce the impact of the material falling, and reduce the impact of the material falling, and reduce the impact of the material falling, and reduce the impact of the material falling. When the material reaches the set target value of fast batching, the frequency converter switches to a smaller vibration frequency and feeds the material with slow vibration to reduce the impact of the falling material and improve the weighing accuracy. When the stopping weight value is reached, PLC sends a stop signal to the frequency converter, and the feeding electric vibration machine stops, waiting for the remaining material in the air to fall down completely, and then completes a batch of dosing cycle. The machine will stop when the remaining material in the air falls down completely,
4.2 Mixing material conveying program design
Weighing mixer in the whole mixed material conveying process requires normal operation of the transport belt, otherwise the material will be piled up in the belt, resulting in the belt run off. Conveying system start-up sequence is: first start the end of the large inclination of the material belt, and then start the beginning of the horizontal material belt. 2 belts are running normally after the start of the mixed material conveying process, in order to make the material in the material belt mixing uniformity, in order to start the 1 ~ 5 "fabric frequency converter.
According to the actual situation, usually a number of batches of materials will be continuously dosed, due to the feeding and unloading process time is very short, after the completion of a dosage, the feeding belt does not stop. When this dosage task is completed, the upper position can be selected to stop the material transportation belt. In contrast to the start-up sequence, the horizontal feeding belt is stopped first, and the large inclination feeding belt is stopped after a delay.
4.3 Communication design of batching control system
4.3.1 Communication between upper level industrial control machine and PLC
The communication between S7-200PLC of this weighing control system and WinCC of the upper computer monitoring software is realized by ETH-iBUS Ethernet converter. ETH-BUS connects directly with WinCC through RJ45 twisted shielded cable (i.e., it does not use PCAccess or OPC method). It can connect to S7-200 with the driver (TCP/IP) that comes with WinCC, which reduces the communication instability caused by the use of OPC. I, Q, M, DB1 external variables in WinCC correspond to the I, Q, M, V variables in S7-200 one by one, which is very simple to use, and can be used after filling in the P address of the PLC and the industrial control machine. At the same time in the S7-200 programming software MicroWin4.0, through the ETH-iBUS to achieve program upload and download, online debugging and monitoring functions.
4.3.2 PLC and instrument inverter communication
The programming software of Siemens S7-200 is specially developed for ModbusRTU communication, which greatly simplifies the development of ModbusRTU communication to facilitate the rapid realization of related applications. The ModbusRTU master instruction library enables the S7-200 to be integrated into a Modbus network as a master device in ModbusRTU in order to realize communication with Modbus slave devices (instrument inverters).
The S7-200CPU2262 RS-485 communication interfaces (Port0 and Port1) are used as ModbusRTU masters respectively, which are connected by bus-type topology, in which the weighing instrument slave communicates with the Port0 port on the PLC, and the frequency converter slave communicates with the Port1 port on the PLC, which reduces the burden of transmitting data from a single communication interface, and enhances system This can reduce the burden of data transmission from a single communication interface and enhance the stability of ModbusRTU communication of the system.
Call the ModbusRTU master initialization and control subroutine from the Modbus instruction library of Step7-Micro/Win, and allocate a storage area for the library instruction in the V data area of the CPU. Set the communication parameters of the Modbus master device to complete the initialization of the master and start its function control.
Call the ModbusRTU master read/write subroutine MBUSMSG from the MODBUS instruction library, set the relevant parameters, and complete sending a Modbus request. Thus, it realizes the task of reading and writing the relevant data (weight, frequency, etc.) of the weighing instrument and frequency converter.
5 Upper computer monitoring screen design
According to the process requirements of the batching monitoring system, use the monitoring software WinCC6.2 to design the corresponding user management, operation process recipe management, parameter setting, report query, data management and fault alarm screen, real-time display of the operating conditions of the field equipment, and can control the field equipment, and together to complete the batching control system status monitoring and operation management 6, the following part of the Introduction The design function of the screen is described below.
5.1 Main Screen
Start WinCC and enter the main screen of dosage after user login. This screen not only shows the whole process of the system dynamically displaying the remote control signals, operation signals and fault signals of the batching equipment, real-time displaying the data of the weighing instrument and the operation frequency of the frequency converter, but also controlling the batching equipment. The screen is equipped with two operation modes: automatic and manual. In manual mode, all the equipments of the dosage system can be started and stopped individually without being affected by other equipments, which is usually used only in debugging. In automatic mode, just click the "Batching Start" button, and the system will automatically complete the functions of batching, fabric and conveying according to the set formula.
5.2 Recipe Management
The main function of this screen is to complete the creation, saving, viewing, applying and deleting of recipes. Users can save the recipes according to their needs, each recipe needs a unique number to be stored in the database, otherwise the saving fails and prompts that there is already the same recipe number Recipe application: after finding the harmful recipe data in the time-honored recipe, input the recipe number and click "Apply" button, the recipe data will be transferred to the dosage controller. Historical formula query: user input the query time period, the system will automatically export all the formula records within the time period.
5.3 System parameter setting
The parameters to be set by the operator in the dosage control system mainly include the weight value of 5 scales for fast feeding, the weight value for early stopping, the running frequency of frequency converter and the fabric time. The user can save the parameters which are more stable in the process of using into the database, which is convenient for setting the parameters next time.
5.4 Fault Alarm
Monitoring software for the system during the operation of the faults occurring in the automatic recording function, the operator is able to browse through the fault query window in the winter period of the system's faults. It can also help the maintenance personnel to find out the fault point and the reason when there is a fault.
5.5 Data Report
The report screen provides a convenient visualization interface, users only need to set up the query conditions on the screen, and then click the query button to realize the access to the data operation. According to the project requirements, this system can query the calendar dosage data by two conditions: time period and shift. The queried records are displayed directly in the MSFlexGrid control for easy viewing. The query data can also be exported to Excel spreadsheets, and fully use Excel's data analysis function to create daily and monthly reports, providing reliable production analysis and decision-making basis for the relevant production management department.
System operation
Since it was put into operation in February 2018, the system has been running stably, easy to operate, with high control accuracy, reducing raw material consumption, improving productivity, and realizing the automated batching of ferrosilicon furnace. The positive value of the batching error of production transportation indicates the error value of the actual batching quantity exceeding the target set quantity while the negative value indicates the error value of the actual batching quantity lower than the target set quantity.
At the early stage of batching, the batching error of silica is large, after adjusting the frequency of feeding inverter and constantly correcting the value of quick casting weight and stopping advance, the batching error is gradually narrowed down within the tolerance range. The batching error is gradually reduced to within the tolerance range, which meets the requirement of batching accuracy of Gong Gong.
This control system is a new type of batching control system designed by combining mature PLC control, frequency conversion speed control, configuration monitoring, communication technology and reasonable control algorithm, which solves the problems of traditional batching system such as low batching accuracy and poor system stability. The system can run for a long time and stably under the bad environment, with high reliability and good anti-interference. Practice shows that the system has high cost-effective and has good popularization value.