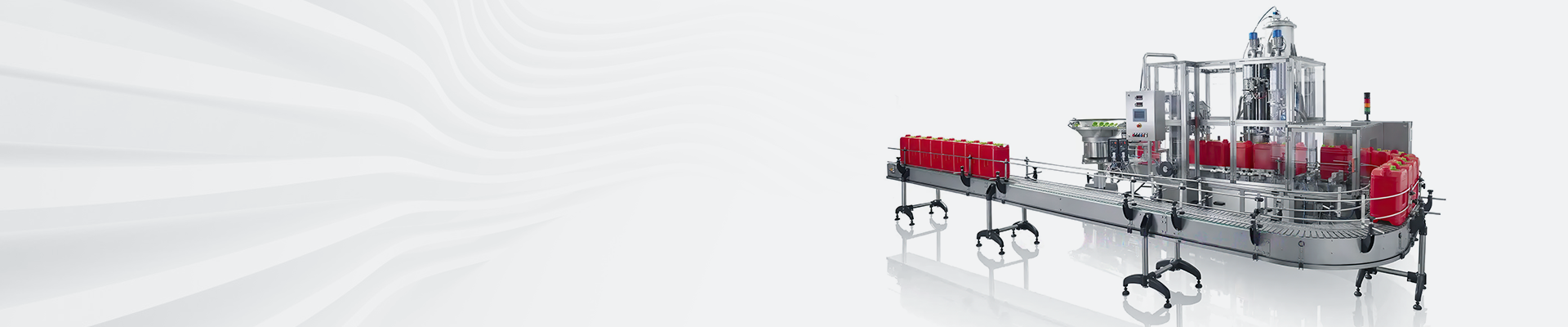
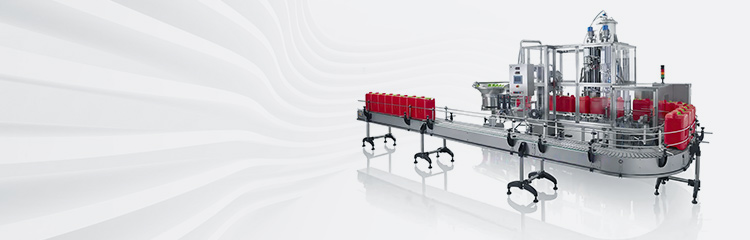
摘要:动态配料系统通过集成接口导入ERP,可和物资库存管理动态系统集成,自动读取数据扣除可用数量,同时可指导现场作业配料。
在治金企业中,配料质量控制的优劣直接关系硅铁电炉能否冶炼出合格的产品。只有配料系统精确地将电炉所需物料按一定的比例配比好装入原料仓中,通过运料皮带将配好的原料加入炉内,才能满足硅铁正常生产的需求,因此上料系统在整个电炉冶金系统中尤为重要“。目前硅铁配料机主要存在的问题是:系统可靠性差,配料精度低,缺少对生产过程的实时动态监控,以及对生产数据的管理能力不足。因此结合成熟的PLC控制技术、变频调速技术、组态软性监控技术、通讯技术来设计新型配料控制系统,不仅可以提高配料精度和稳定炉况,也大大减轻了岗位工人的劳动强度,增产降耗,对保障硅铁生产线的稳定运行和提高生产效率都有重要的现实意义。
1硅铁配料工艺及生产流程
治炼硅铁的特点是必须加工处理大量的原料,按照一定的比例称量,混合后形成均匀料,而配料的质量很大程度上决定着生产的技术经济指标2。配料中所采用的主要原料有木屑(1物料仓)、硅石(2物料仓)、精煤(3物料仓)、石油焦(4物料仓)、钢屑(5物料仓)等,其配料过程整体上可以分为5种物料的定量给定、称重、布料、混合料输送和卸料等4个主要生产环节,涉及生产设备有:5个物料仓、5个料斗秤、5台振动给料机、5条布料皮带机、1条水平运料皮带机、1条大倾角皮带机、落和卸料装置等。本喂料系统采用“单料单秤”的称量方式,各台秤可同时进行称量,统一布料,称量精度高,配料速度快。
硅铁配料的工艺流程是,先按照配方将硅石、精煤、钢屑及辅料分别称量,等称量结束时,系统检验是否满足布料条件,如给料电振机停止,运料皮带已启动等。如果满足布料条件,则系统按规定顺序开始布料,使各种原料的料头对齐,分层平铺在水平运料皮带机上,混合料经大倾角运料皮带机送入炉顶的分料仓,打开分料仓底端的卸料闸门,最终将混合物料送至矿热炉内。经过一定延时后,系统开始配下一批原料。
2硅铁投料系统的构成
本系统采用上位工控机和下位机PLC构成的两级控制系统。上下位通过ETH-iBUS以太网转换模块进行TCP/IP通讯。PLC与现场称重仪表和给料、布料和输送等变频器采用MODBUS协议通讯。
上位工控机完成整个工艺过程的集中管理利用组态软件实现配料过程进度的动态监控和对系统中各个装置的工作状态实时监控,并可以对配料数据,报警记录和故障进行打印等。
下位机通过MODBUS通信协议实现PLC与称重仪表、变频器的实时数据交换,完成配料数据的处理、计算以及配料过程的控制。由于PLC接受的是通讯信号,无需进行模拟量转换计算,不会增加多余误差;PLC对配料设备进行直接控制可降低系统故障风险,真正实现了集中管理、分散控制的目的。
在配料过程中,PLC不断从称重仪表读取重量值,与设定的配方和程序相比较,作出判断,控制给料机的启停和快慢给料。加料完成后,开始启动运料皮带和布料电振机进行布料、混合料输送。
配料机的硬件设计
要保证配料的精度和快速性,必须根据工艺要求、所需配制物料的特性等因素进行综合分析,首先选择合理的称量方式和生产线的结构形式,然后正确选择称重传感器、称量仪表以及设计合理的总体控制方案并综合考虑其他相关因素,这样才能设计出精度高、成本低、符合要求的自动配料系统。
3.1硬件设备选型
为了满足硅铁配料生产自控系统的设计要求,选用西门子公司SIMATICS7-200PLC和高性能研华工控机构成自控系统,根据设计要求,本系统所选用的主要硬件产品如下。
1)上位工控机。研华工控机:双核2.16G,内存2G,硬盘500G,22x2.54cm液晶显示器。
2)下位PLC的模块配置。由于投料系统的PLC与现场称重仪表和变频器用MODBUS现场总线通讯,故没有模拟量的输入和输出,减少相应的IO点,故选用西门子S7-200系列PLC即可实现控制功能。
中央处理单元:CPU226;扩展模块:EM221数字量输入2块,EM223数字量输入输出1块通讯处理模块:大连德嘉国际电子有限公司ETH-iBUS以太网转换器1块。
3)称重传感器。本系统选择的是型悬臂梁式称量模块,量程为1000kg。每个称重斗采用3块计量模块并联组秤方式(通过接线盒汇集)来实现称重目的。
4)称重仪表。系统采用称重仪表(带MODBUS通讯接口RS485),对称重数据进行高速高精度A/D转换,将ms信号直接转换成数字信号,采用标准的MODBUS协议将称重信号传输至PLC,由PLC进行数据处理、计算和控制。
5)变频器。系统选用浙江海利普电子科技有限公司的HLP-NV系列多功能、高性能矢量变频器进行精确调速,以保证配料过程的高速度和高精度。
3.2电气控制系统
电气控制系统由PLC控制柜、电气控制柜以及就地操作箱等组成。电气控制柜为PLC控制柜、现场操作箱、现场设备、室内照明等提供电源,并集中管理。电气控制柜正面为动力控制回路,包括电源开关、熔断器、接触器等,背面为给料变频器和接线端子。就地控制箱安装在现场设备附近,可以对单台设备独立启停,控制面板上面有“就地/远控”转换开关,启动按钮,停止按钮和指示灯。
配料系统的软件设计
根据对称重混料机工作流程的分析,PLC程序设计采用结构化编程方式3,把整个程序划分为主程序、通信子程序、配料子程序、布料子程序、输送子程序、配料算法子程序和故障报警子程序等几部分。系统分为手动/自动两种运行模式,自动控制方式又包括单步和连续方式;手动操作主要在系统调试、维修时或者PLC发生故障时使用
主程序调用不同的子程序实现总体功能。上位机把配料数据及启动信号传给PLC后开始执行配料应用程序。配料过程中,通讯子程序不断读取称重系统的数据;给料变频的启停和快慢配料由配料子程序控制;混合料输送过程通过调用布料子程序和输送子程序来实现。硅铁4.1配料程序设计
当系统满足所有设备为“远控”状态;布料过程已结束,称重斗为空;配料参数设置合理;加料变频无故障信号等条件时,系统开始配料。
在进行自动配料时,当物料快配料目标值远小于设定值时,PLC发出高速指令,使振动给料机工作在高频状态,物料快速落入称重斗,减少给料时间,以提高进料效率,同时在上位机上实时显示物料的净重;当物料达到设定的快配料目标值时,变频器切换到较小的振动频率,慢速振动给料,以减小物料下落时的冲击,提高称量精度。当达到停机重量值时,PLC向变频器发出停机信号,加料电振机停止,等空中余料完全落下后,完成一个批次的配料周期。、
4.2混合料输送程序设计
称重混合机在整个混合料输送过程中要求运料皮带正常运行,否则物料会堆积在皮带上导致皮带跑偏。输送系统启动顺序是:先启动未端的大倾角运料皮带,再启动始端的水平运料皮带。2条皮带都正常运行后开始混合料输送过程,为了使物料在运料皮带上混合均匀,要依次启动1~5"布料变频器。
根据实际情况,通常会连续配若干批料,由于加料和卸料过程的时间很短,完成1次配料后,运料皮带不停机。当完成本次配料任务后,可上位选择停止运料皮带。与启动顺序相反,先停止水平运料皮带,经延时后停止大倾角运料皮带。
4.3配料控制系统的通讯设计
4.3.1上位工控机与PLC通信
本称重控制系统的S7-200PLC和上位机监控软件WinCC之间的通信是通过ETH-iBUS以太网转换器实现的。ETH-BUS通过RJ45双绞屏蔽网线与WinCC直接连接(即不用PCAccess或OPC方式)。它能够用winCC自带的驱动(TCP/IP)连接S7-200,减少了因使用OPC而带来的通信不稳定性。WinCC中的I,Q,M,DB1外部变量与S7-200中的I,Q,M,V变量一一对应,使用非常简单,填完PLC和工控机的P地址即可使用。同时在S7-200编程软件MicroWin4.0中,通过ETH-iBUS实现程序上传下载、在线调试及监视功能。
4.3.2PLC与仪表变频器通信
西门子S7-200的编程软件专门为ModbusRTU通信开发了指今库,极大地简化了ModbusRTU通信的开发,以便于快速实现相关应用。通过ModbusRTU主站指令库,使得S7-200可作为ModbusRTU中的主站设备集成到Modbus网络中,以实现与Modbus从站设备(仪表变频器)的通信。
S7-200CPU2262个RS-485通信接口(Port0和Port1)分别作为ModbusRTU主站,采用总线型拓扑连接,其中称重仪表从站与PLC上Port0口通信,变频器从站与PLC上Port1口通信,这样可以减轻单通信接口传输数据的负担,增强系统ModbusRTU通信的稳定性。
从Step7-Micro/Win的Modbus指令库中调用ModbusRTU主站初始化和控制子程序,在CPU的V数据区中为库指令分配存储区。设置Modbus主站设备的通讯参数,完成主站的初始化,并启动其功能控制
从MODBUS指今库中调用ModbusRTU主站读写子程序MBUSMSG,设置相关参数,完成发送一个Modbus请求。从而实现称重仪表、变频器的相关数据(重量、频率等)的读写任务。
5上位机监控画面设计
根据配料监控系统的工艺要求,使用监控软件WinCC6.2设计出相应的用户管理,操作流程配方管理,参数设置,报表查询,数据管理和故障报警等画面,对现场设备的运行状况进行实时的显示,并能对现场设备进行控制,共同完成配料控制系统的状态监控和操作管理6,下面个绍部分画面的设计功能。
5.1主画面
启动WinCC,用户登录完成后可进入配料主画面。该画面不仅展示了系统的整个工艺流程动态显示配料设备的远控信号、运行信号、故障信号,实时显示称重仪表的数据、变频器的运行频率,还能对配料设备进行控制。画面设有自动和手动两种操作模式,手动模式下,配料系统的所有设备可以单独启动和停止,不受其它设备的影响,通常这种方式只在调试时使用。自动模式下配料,只需点击“配料启动”按钮,系统按照设定好的配方自动完成配料、布料、输送等功能。
5.2配方管理
该画面主要功能是完成配方的新建、保存、查看、应用和删除等。用户可以根据需要保存配方,每个配方需有唯一的编号才能存入数据库,否则保存失败,并提示已有相同的配方号配方应用:在历时配方中找到所害的配方数据后,输入配方号码点击“应用”按钮,配方数据即传入配料控制器中。历时配方查询:用户输入查询的时间段,系统自动导出该时间段内的所有配方记录。
5.3系统参数设定
配料控制系统中需要操作人员设定的参数主要有5台秤的快投重量值,提前停机重量值,变频器的运行频率和布料时间等。使用过程中比较稳定的参数,用户还可以保存到数据库中,方便下次设定参数。
5.4故障报警
监控软件对系统运行过程中出现的故障情况有自动记录的功能,操作人员能够通过故障查询窗口浏览冬个时期系统的故障情况。出现故隆时还能帮助维护人员查找故障点和原因。
5.5数据报表
报表画面提供了方便的可视化操作界面,用户只需要在画面上设定好查询条件,然后点击查询按钮,就可实现对数据的访问操作。根据项目要求,本系统可以通过时间段和班次两种条件来查询历时配料数据。查询的记录则直接在表格MSFlexGrid控件中显示出来,方便用户进行查看。也可将查询的数据导出到Excel电子表格中去,并充分使用Excel的数据分析功能,创建日报表和月报表,为相关生产管理部门提供可靠的生产分析与决策依据。
系统运行情况
从2018年2月投入运行以来,系统运行稳定、操作方便、控制精度高,减少了原材料消耗,提高了生产率,实现了硅铁炉的自动化配料。生产运配料误差正值表示实际配料量超出目标设定量的误差值而负值则表示实际配料量低于目标设定量的误差值。
配料初期硅石的配料误差较大,经过调整给料变频器的频率和不断修正快投重量值、停机提前量,使配料误差逐渐缩小在允差范围内。满足了工共对配料精度的要求。
本控制系统是结合成熟的PLC控制、变频调速组态监控、通讯技术和合理控制算法设计出的新型配料控制系统,解决了传统配料系统存在配料精度不高、系统稳定性差等问题。系统在恶劣的环境下能长期、稳定地运行,具有高可靠性和良好的抗干扰性。实践表明,该系统有较高的性价比,具有很好的推广价值。