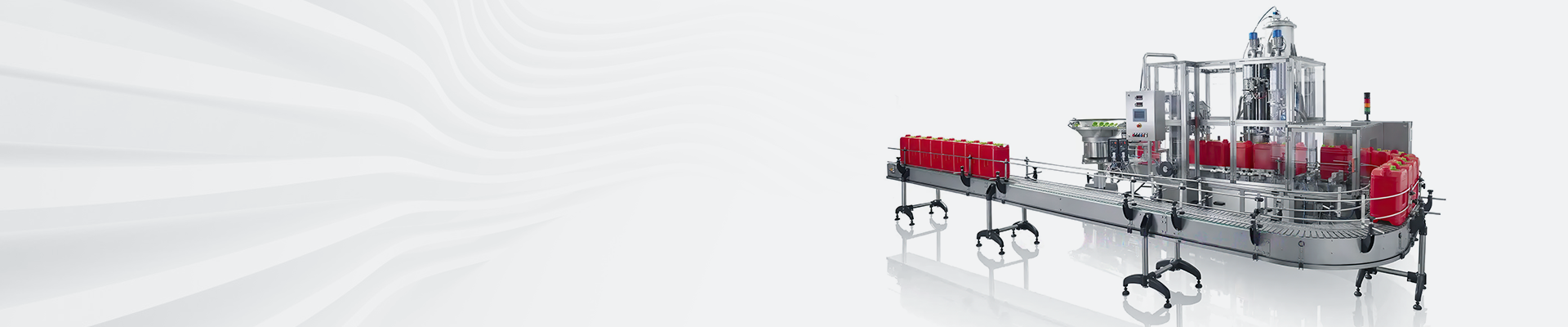
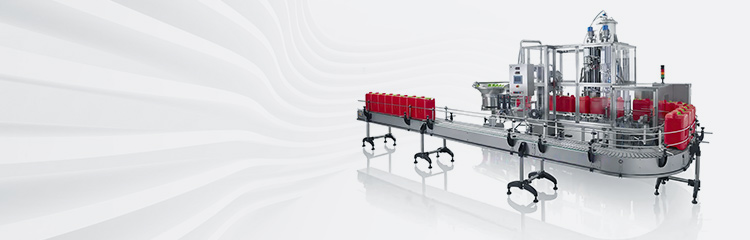
摘要:配料系统实现现场工作站完成对现场的压力、温度、流量、阀门开度等采集和控制,并在现场站内完成信号处理、顺序控制、控制算法、PID调节和故障诊断等。
日产2000吨以上化工厂已全部采用中央配料系统。聚氨酯厂及部分小化工厂尚未采用该自动投料系统。中央喂料系统构成分为3个或4个层级:管理层级、操作层级、控制层级、设备层级。管理层级主要功能是信息收集、优化决策、资产管理等;操作层级主要功能是工程师岗位操作;控制层级主要完成各类控制;设备层级主要实现各设备的工艺参数检测转换与配送。
一般在生料上料系统、混合配料、粉料制成等配电控制室,分别设现场控制工作站、中央控制室、工程师站、操作站,与现场控制工作站之间通过通讯总线连接构成网络。该自动配料系统方案的特点为分散控制、集中操作、集中管理,自动配料系统可靠性高,操作简便,可维护性强,便于实现全厂集中指挥、调度和管理,有利于提高产品的产量和质量。
整个生产过程的热工参数实现自动检测与控制,部分电气设备的启停实现自动控制。各现场工作站完成对现场的各种模拟量信号(压力、温度、流量、阀门开度等)、各种开关量信号(电机、位置和料位等)的采集和控制,并在现场站内完成信号处理、顺序控制、控制算法、PID调节和故障诊断等。
自动配料机主画面及功能在工程师站和控制操作站的屏幕上可显示各种画面,画面主要有:
①整条生产线的模拟示意图,能显示各台重要设备的实际状态和工艺流程走向;
②过程画面,分工段的工艺模拟画面,可显示工艺流程、动态参数和设备运行状态,对异常情况发出报警;
③实时趋势画面,显示动态参数在当前几分钟内的趋势,时间可以任意设定;
④控制组画面,采用模拟常规仪表的形式,把有关的调节器集聚在一幅画面上,便于操作和观察;
⑤调整画面,控制对象为调节回路,包含调节参数、初始化、启动、停止、实现手动/自动无扰切换等;
⑥报警汇总画面,显示所有报警信息,便于有关人员对以前一段时间内的设备运行和操作情况进行查对;
⑦历史趋势画面,显示重要参数在过去数天内的运行趋势,为技术人员提供分析数据,以解决工艺自动配料系统或设备存在的问题;
⑧报表画面,根据用户要求将自动配料系统的重要信息转换为电子报表。各画面之间可以切换,操作员在操作站可对全厂主要车间的生产情况进行监测与监视,操作、修改有关参数和启停有关自动配料系统的部分设备等,可以随机打印报警信息和各种生产报表。工程师站对整个自动配料系统进行组态、编程、调试和维护,可在线修改程序而不影响整个自动配料的运行。
各配料的检测与控制
①生料、粉料混料机的检测与控制检测生料配料秤的压力、速度、运行状态;检测库底配料皮带运行状况;检测磨机入口处:轴瓦温度、轴瓦油压、冷却水流量;检测磨机出口处:轴瓦温度、轴瓦油压、冷却水流量;检测减速机油温或轴温、磨机功率、磨机出口处负压、旋风收尘器压差、选粉机电流;实现配料设备的顺序启停控制;检测磨音,改变经验控制,减少空磨与饱磨工况。振动检测,根据电动机型号和功率的不同,安装检测位置不同,粉料磨主电机振动传感器安装在减速器上,磨尾出口袋除尘风机、选粉风机则安装在轴承座上。磨机主轴瓦温度监测和油池、油温监测与控制,保护了轴瓦,避免了电动机频繁启动,节约能源。控制磨机压差、减少磨机振动。选用变频调速皮带秤作为给料计量设备,不需要振动给料机,减少故障点,保证称重配料系统长期稳定运行;完成单秤的定量给料控制,多秤的比例跟踪控制,提高配料系统的计量控制精度,使出磨生料质量达到生料配料系统的工艺要求。磨机产量根据磨机自动配料系统工况进行优化调节。过程画面显示全部检测工况,供操作管理人员进行有效决策。
②混合投料站检测及控制来料变频调速输送机、混合料输送机、斗式提升机、喂料变频调速输送机、密封皮带秤、变频调速管道泵、预湿机、成球盘、成球输送带等设备运行状态;检测鼓风机左右侧油温、功率、出口处风压、风量、阀门开度;入窑风量、入窑风压;检测煤粉仓、生料仓料位;检测脉冲收尘器烟气温度、压力、烟气成分;检测混合配料高温带温度、腰风处温度、冷却带温度;检测出窑熟料温度、卸料速度、卸料量;检测成球盘的水流量、料流量;实现成球自动配料设备的顺序启停、故障停车控制;根据煅烧工况实时调节用风量(调节罗茨风机控制阀的开度);根据聚氨酯煅烧热工监测过程,自动进行料水计量、比例跟踪控制,长期稳定地保证预加水成球质量,实现小料球快速煅烧的粉料工艺要求,达到提高熟料产量、质量之目的;以一系列的工艺流程图和主要参数的趋势图及时给出生产报表、图形拷贝,便于生产管理以及事故分析;操作人员可在线修改参数。
称重给料机采用立式空心轴电机直接驱动螺杆,电机为无刷直流电机,由专用无刷直流控制器进行控制。省去中间传动机构后,光杆上所受到的各种扰动无缓冲的作用在电机轴上,使得系统易受井下工况(主要是原油动液面的变化及原油粘度)的影响。螺杆泵驱动在被控对象的变化而作相应的调整,当系统参数发生变化时,螺杆采用一个多变量、非线性、时变的系统,速度环采用模糊自适应PID控制来实现。螺杆对控制器的参数进行在线调整,完成对给定输入的跟踪,加速自适应进程,同时减小跟踪误差。通过微机连接多台称重给料机,可用于料仓配料,同时配料的物料可以多达9~12种,要进行多种物料的连续配料,基于斗式秤的结构,能直接进行砝码标定,通过对秤斗各瞬间测试计算出实际排料量,再进行闭环调整,从而可以达到较高的控制精度,一般而言累计精度为0.5%。由于是斗式结构标定和维护也比皮带秤容易得多,证明在原材料成分波动时单控制生料CaO、Fe2O3不能稳定生料三率值,进一步明确了率值配料的概念。揭示钙铁控制的缺陷,提出了钙铁控制下保证率值合格的最佳回调方法,最大限度地避免了钙铁控制的缺陷。
称重混合机由螺旋给料机和一套上位机由称量模块和称重仪表及通讯电缆组成,称重显示器还提供RS232、RS485接口ADSL、GPRS、CDMA、光纤等通讯,上位机监控采用Windows操作,编程软件及组态软件控制采用PID调节计量偏差与变频调速的结合,变频控制中的硬件设置、参数设定和软件设计过程。多输出各条配料输送生产线严格地协调控制,对料位重量及时准确地进行监测和调节。由可编程称重显示器与计量模块组成一个两级计算机控制系统,通过总线连接现场称重仪表、控制现场设备、称重给料机变频器等,智能程度较高、处理速度快。在配料生产工艺过程中,将主料与辅料按一定比例配合,完成对输送的物料进行计量。主要承担对输送、秤量过程进行实时控制,并完成对故障检测、显示及报警,同时向变频器输出信号调节螺旋转速的作用。