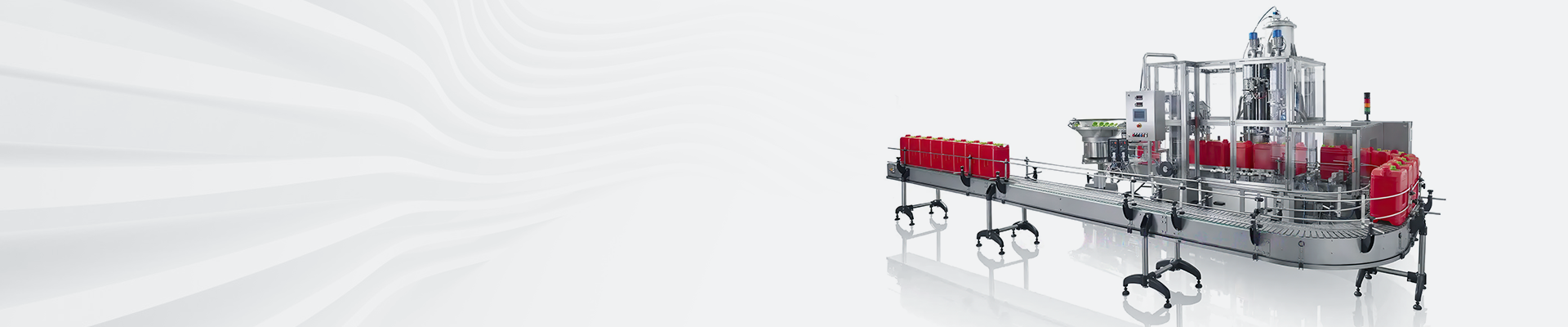
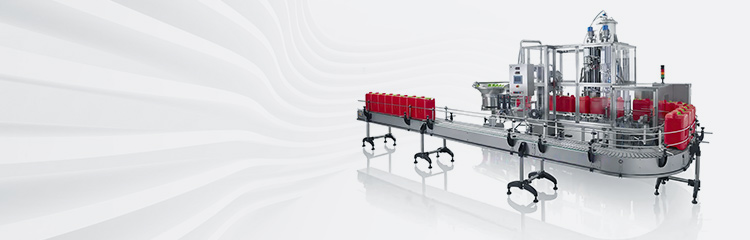
摘要:配料系统利用称重仪表实现了批量加料自动控制,组成批量控制网络,实现各车间批量加料配料之间的连锁功能,并用上位机实现对整个加料的远程监控和管理。
工矿企业中经常需要对大批量物料进行动态称重,以满足生产工艺中对配方的要求。常见的称重方式有皮带秤,斗式秤等。皮带秤采用连续进料方式,重量变化不大,可以实现边称边调节进料量以及事后补偿的技术,对时间响应的要求不高;而斗式秤是间歌进料,重量累积增加,物料不足可以补充,但物料过量后不易取出。因此,斗式秤对控制精度和实时性要求较高。
1系统分析
实际中要求对多台料斗秤组成的称群进行物料称量和控制物料仓,每台秤称量范围为50~500kg物料盛装于物料仓中,物料仓和称量斗之间安装振动筛,由振动筛控制进料量,当物料重量达到目标值时停振动筛,记录静态称量的物料重量,并根据生产需要打开底部仓门卸料,由运输带将物料送到窑内嫩烧,然后重复上述称重和下料过程。从上述过程可看出,物料重量最终由精度较高的静态称量值给出,用该值与目标产量之间的差异来衡量称量的精度。但系统需要在进料过程中动态称量,以便能及时停止振动筛,而且斗式秤过称量后不能在本次调整,所以其动态称量精度重为重要。投料系统中动态称量存在如下难点:
1)物料流量大。由于物料的密度、颗粒大小、流动性不相同,所以各台秤的进料流量也不相同,范围在8~23kg/s之间,最快几秒种即可达到目标产量,对测量和控制实时性要求较高。
2)物料不规则冲击。物料从振动筛上落下进入称量斗时具有一定的下落速度,物料冲击振荡形成一系列虚假的重量传递给传感器,称重传感器采集的瞬间信号不能真实反映物料重量。由于物料大小不一,其下落冲击是随机的。很难估计,并且随着物料落差的减小,单位质量物料冲力也会减小。这些特点使得系统无法精确建立冲力和重量的对应关系。
3)下料时间滞后。当关闭振动筛后,由于振动筛的惯性。下料不会立即停止,仍有一些物料继续进入称量斗,造成下料过冲,因此设计过程中必须考虑下料过程的时间滞后特性。
4)电磁干扰。现场有风机、提升机、皮带机、振动筛、卷扬机等设备,必须采取措施减小电网波动及电磁干扰给重量信号及数据采集带来的影响。
针对上述问题,我们在系统实现部分给出解决方案。
2系统设计与实现
上料系统大致分为称量模块部分、信号调理部分、信号采集、处理部分和显示记录部分。其中信号采集、处理部分和显示记录由PCI数据采集卡、工控机及显示、打印外设完成。
本喂料系统为机电一体化的计算机控制系统,共控制六台料斗秤。每台秤除一路重量信号外还有其他如监测仓门状态和位置、控制和监测变频器、控制和监测运输带、自动手动模式切换等数字输入输出量。对于重量信号的采集。对称安装三个计量模块支撑称量斗,将重量信号用加法器合并为一路重量模拟信号,这样既可避免由于物料在称量斗中堆积位置不同造成的重量信号差异,又无须对三个称重传感器是否在同一水平面作精确调节,减轻了日后维护负担。
工控机配以数据采集卡组建系统,这种方式相对于嵌人式系统和PLC还具有界面友好、开发周期短、维护更新方便、价格低廉等优点,而且工控机性能稳定,电磁兼容性和抗尘性能都满足工业应用需求。为保护工控机以及外设免受线号输入线上意外高压电的损害,应选取在输入和系统总线之间有隔离保护的数据采集卡。
配料机还需控制振动下料筛改变下料流量,选取变频器控制电机转速方式,可方便快捷地改变电机转速。
2.1大流量物料称量物料流量大要求对重量信号的采集频率和传输率高,采用了研华公司生产的基于高速PCI总线的PCI-1713型32通道模拟量采集控制卡。该卡实现12位高速A/D转换采样率可达100KS/s,为保护PC以及外设免受线号输人线上意外高压电的提害在输人和PCI总线之间提供了2500V(DC)的直流光离保护。对于本系统将PCI-1713设置为单端输人内触发工作模式增益代码设置为16,即相应的输入信号电压范围为0-10V。采用PCI-1713卡达到了1ms/channel的采样周期,控制周期为128ms左右,比普通皮带秤的1s控制周期大大提高。模拟量重量信号采集通过驱动对PCI-1713进行操作本系统中PCI-1713模拟量输入采用多通道中断触发方式,使用FIFO并使用用户缓冲区。采样数据先依次存放于FIFO第一半和第二半缓存中,FIFO半满时产生一个中叫,然后将此半缓存的数据向用户缓存区传送,以供后续处理并防止在Windws多任务操作系统下进行高数数据采集时丢失数据,同时新数据继续填充下一半缓存,可实现高速实时数据采集。在此基础上,进一步对振动筛的工作模式进行了设置。让控制振动筛的李频器能在软件系统的控制下工作于高速和低速两种模式,在低速模式下降低下料流量提高控制精度。
2.2数据处理方法由于物料不规则的冲击,称量斗振荡,导致软件界面上显示的实时物料重量数值忽大忽小异常跳变,而且其他大功率设备启停造成的电网波动也会产生类似干扰。针对此问题,在数据处理部分对数据进行了中位值平均滤波法,这种方法是中位值滤波法和算术平均滤波法的综合。即首先对-个采样周期内得到的N个数据按大小排序,然后别除前m个和后,个数据,最后求出中间(N-Tn)个数据的平均值作为最终采样值。该方法可除偶然脉冲扰,适当调整m值可调整输出值大小偏向。在本系统中一个数据采集周期采集到64个重量信号.将前16个和后16个数据别除,取中间32个数据平均值为重量信号值。运行结果发现该措施同时解决了不规则冲击和电磁干扰问题。下料过程中软件界面上显示的实时物料重量值逐渐平稳增长。即使大型机械启停造成电网剧烈波动也没有出现跳变现象。
2.3时间滞后处理方法为解决时间滞后问题。我们采取了基于模糊控制的设置预留冲量的方法,其基本算法为:开始下料时开变频器为高速,振动下料筛快速下料,物料以较大的流量进人称量斗,当称量斗中物料重量值大于目标产量减去慢速预留冲量时,则开变频器为低速状态,振动下料筛慢速下料。物料以较小的流量进人称量斗:当称量斗中物料重量值大于目标产量减去停止预留冲量时。则关闭变频器,振动下料筛停止下料,下料筛的过冲量会补足当前物料重量与目标产量的差值:这一控制流程如图3所示。这样。快慢两速下料以及设置预留冲量的方法解决了由于时间滞后特性造成的下料过冲问题。预留冲量的大小可根据目标重量以及物料性状的不同在软件操作界面上设置。
实际调试过程中我们发现,振动筛高速开50H2,低速开20H2,则高速目标设为设定值减去10倍预留比较合适,振动速度太低则下料耗时,太高则下料速度过快难以控制。
3结果和讨论
自动配料系统实际运行半年共一万多条实际下料数据,3号称和6号称由于称量时每次目标产量都较小,且物料常常结块,时间滞后特性对下料的精度控制造成较大影响,称量误差较大。其余各台称均达到自动称量准确度2.0级。如果增加对过冲量的截留装置将大大提高本系统的可控性和称量精度,但这也会使称体机械部分重为复杂。另外系统使用时如果目标产量改变或物料性状发生改变,需要人工对预留冲量值进行适当增减。在实际使用过程中我们发现缺乏经验的操作人员对该值的设置有时不当,造成称量误差较大。因此我们考虑在人工干预预留冲量的基础上增加自适应控制预留冲量算法,以降低预留冲量设置的恰当性对操作人员经验的依赖。