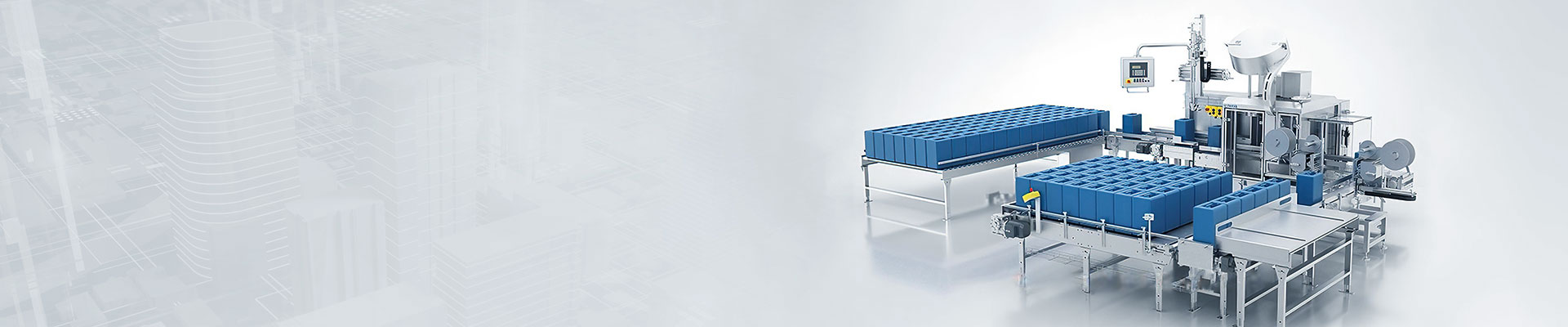
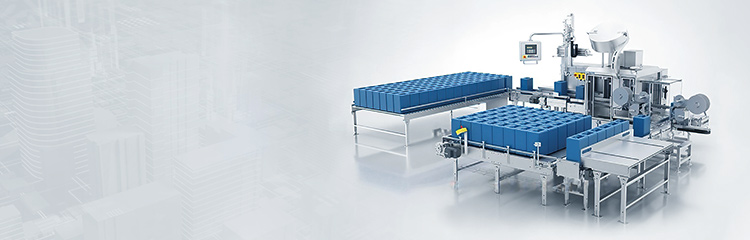
Automatic batching system is a complete set of automation equipment to realize dynamic weighing and batching control through electrical control management and visualization man-machine software configuration. The electrical control part of the system adopts Siemens PLC, which is programmed and controlled according to the production requirements; the software adopts man-machine configuration, which is used to control the weight and flow of the materials loaded into the weighing hopper through the monitoring system and the PLC program according to the technological requirements so as to realize accurate measurement and batching. The software adopts man-machine configuration. With strong stability and high cost performance, the system can provide accurate measurement data and control means for production control and management of various industrial sites.

Weighing and Dosage system with integrated use of communication, PLC and WinCC technologies, which organically constitutes a system of control circuits, PLCs (lower unit), industrial control computers (upper unit) and all kinds of electrical equipment, and realizes real-time data communication between them. Through the electrical control management and visualization man-machine software configuration, it realizes the complete set of automation equipment for dynamic weighing and dosage control. The electrical control part of the system adopts Siemens PLC, which is programmed and controlled according to the production requirements; the software adopts man-machine configuration, which is used according to the technological requirements, through the monitoring system and the PLC program, to carry out the weight and flow control of the materials loaded into the weighing hopper, so as to realize accurate measurement and dosage. The system has strong stability and high cost performance, and can provide accurate measurement data and control means for production control and management of various industrial sites.
Batching system is based on a pre-established formula will be a variety of raw materials orderly, quantitative mixing and related processing to form the required products, batching production is an important and necessary part of industrial production, batching product quality directly affects the subsequent production can run normally, the existing batching through the local detection instrument control combined with on-site manual monitoring, to realize the realization of automatic and visual batching industrial control system. The dosage system pumps are used to realize the raw materials.
Dosing system pump is to realize the raw material pump on/off, thermal protection and fault alarm function. The system has a total of material pumps and solvent pumps, respectively, for the reactor and additives reaction tanks for discharging. The control principle of each pump is basically the same, and the control circuit of the material pump is analyzed here:
(1) material pump control hand / automatic state switch (2 positions: manual, automatic), here for the normally open contacts, its normally closed contacts as the pump control hand / automatic state switching PLC input signal. Through the intermediate relay to contact respectively control 1 ~ 4 material pump manual / automatic state switching. When BSBO normally open contact is closed, the pump control is in manual state; when BSBO normally open contact is disconnected, the pump control is in automatic state. Through the switch BSBO and relay KB1 ~ KB4 can realize the material pump hand / automatic state unification, will not appear some pumps in manual state, some pumps in automatic state.
(2) BSB1 is the button to turn off the pump, BSB2 is the button to turn on the pump, BHL1 is the indicator for pump off status, and BHL2 is the indicator for pump on status. Manual state, press the BSB2, ZJ01 wire packet power, and through its own normally open contacts to achieve self-locking, then the BKM1 wire packet power, BKM1 normally open contacts closed, open the pump successfully, at this time the BHL2 light; when you press the BSB1, ZJO1 wire packet loss of power, and immediately shut down the pump, at this time the BHL1 light. Under automatic state, PLC controls the pump state by controlling the state of output relay BYKA1.
(3) The dosing pump control is in manual state or in automatic state, if there is an emergency or abnormal condition, the pump can be shut down immediately by rotating BSBO.
(4) Thermal relay BFR1 mainly plays the role of circuit overload protection. When the circuit overload, BFR1 action, the pump immediately stop running, BFR1 normally open contacts closed, normally closed contacts open, BGZ1 wire packet power, BKM1 wire packet loss of power, the main circuit is in a state of disconnection. At the same time, the normally open contact of BKM1 and the normally open contact of BGZ1 are sent to PLC as the No. 1 pump operation and fault signals respectively, and the host computer communicates with PLC through Ethernet and displays the status of the pumps in real time in the WinCC process interface of the host computer software. Once the pump operation is faulty, PLC can also make the electric bell in the alarm circuit to sound the alarm bell.