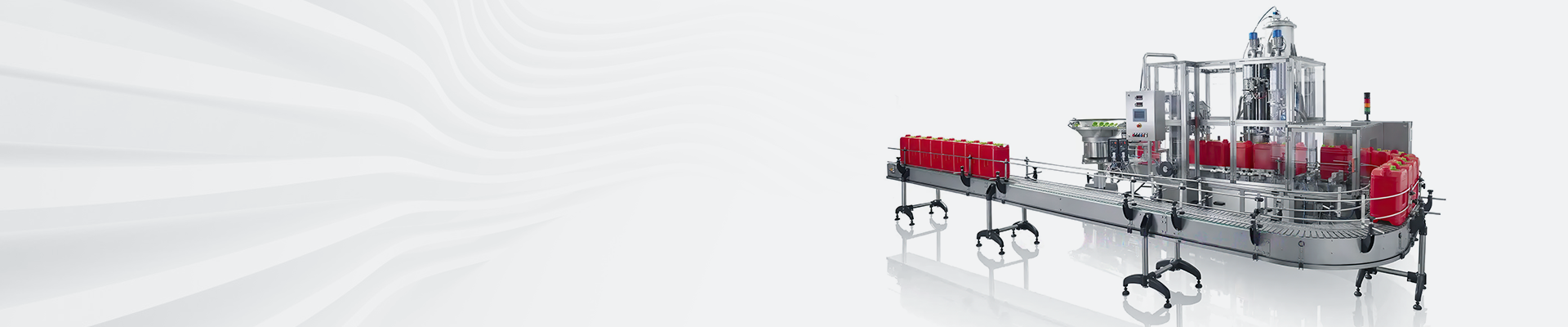
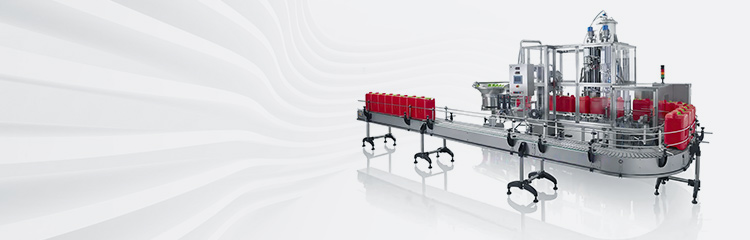

Summary:The weighing and batching machine adopts the functions of high, medium and low speed switching of frequency converter, tare and zero tracking, out-of-tolerance processing, fault diagnosis and other functions.Algorithms such as predictive control of production conditions and cumulative error compensation greatly improve the accuracy and stability of material production control.
1 Preface
In the chemical industry, metallurgy, building materials, ceramics, food, feed and other industrial fields, there are many products are made of a variety of raw materials according to a certain ratio of mixing, through the physical or chemical processing and obtain. Therefore, in the production process of these products, the proportioning accuracy of each material has not only become one of the important factors affecting product quality, at the same time, it is also an important factor to avoid waste and improve production efficiency. Therefore, how to improve the control precision of industrial mixer is very important.
In the last decade or so, China has been developing rapidly in batching control, and its application is also very wide. At present all feeders are controlled by microcomputer, according to the weighing method, it can be roughly divided into several categories such as nuclear scale, belt scale, bucket scale, loss-in-weight scale and so on. Nuclear scale is based on the principle of the measured material absorption of radiation for weighing, is a high-tech and high-precision weighing equipment, but because of its high cost and serious pollution of the environment and only used in a few occasions. Belt scale by the pressure weighing module on the flow through the weighing body of the belt machine on the material weight of the feeling and access to the flow of materials, low cost, but due to the impact of belt motor vibration, the accuracy is very low, generally difficult to achieve more than 1% accuracy, this type of scale is mostly used in a number of places that do not require a high degree of accuracy, such as cement batching. Bucket scale is the weighing equipment with the longest history of use in industrial batching, with simple structure and low cost, but most of them are no longer used because of low accuracy. Loss-in-weight is the latest development of a new technology, the popularization of the use of domestic history is only a decade of history, it can achieve a high degree of accuracy. Its working principle is very simple, that is, through the conveying equipment first to the weighing hopper to provide the required amount of material P, as well as the additional amount of material AP and then discharge until the weighing hopper of the remaining material AP until the weighing hopper due to the weighing method can overcome the material impulse, transmitter zero drift and other factors caused by error, and close to the static measurement, so the accuracy is very high, it can be achieved more than 0.1 percent. At present, this weighing method is widely used internationally, especially in the glass industry. This paper mainly discusses how to improve the accuracy of loss-in-weight scale dosage control, in which the first part briefly describes the principle of loss-in-weight scale dosage control, the second part describes how to improve the control accuracy from the software, the third part describes how to improve the on-line weighing accuracy by adopting the method of multiple AD conversion coefficients, and the fourth part gives the control examples and their application effects.
2 Basic principle of loss-in-weight batching control system
Loss-in-weight scale on the batching line is composed of silo, loading electric vibration machine, hopper scale, discharging electric vibration machine and three tensile force measuring modules. The dosing process is, first through the feeding vibration machine to the weighing hopper material supply, at the same time, the loss-in-weight scale on the material on-line measurement until it reaches a certain value, to stop the feeding process. However, the discharge loss-in-weight measurement is carried out. That is, the material is continuously discharged onto the belt conveyor by means of an electric vibrator. In the process of discharging, the computer samples and calculates the amount of discharged material according to a certain sampling period, and when the given amount of discharged material is reached the discharging process stops and a dosage process is completed.
The change of the material in the weighing hopper is sent to the computer through the load cell through AD conversion and computer processing for display, and based on this, the loading and unloading electric vibration machine is controlled.
The accuracy of the dosage control mainly depends on the performance of the weighing module, transmitter, electric vibration machine and controller as well as the control algorithm. As this dosage control method is only interested in the cumulative amount of material changes, and the flow of material changes in the requirements are not high, as long as the electric vibration machine and the controller's output capacity to meet the requirements and more stable on the control accuracy will not have a worthwhile consideration of the impact of the weighing module and transmitter is the key factor affecting the accuracy, it should be used to select high-precision and high-stability weighing module, and the use of multiple weighing modules (choose) Therefore, high precision and high stability weighing module should be selected, and multiple weighing modules (3 weighing modules can be selected) should be combined in parallel. The circuit should also use advanced integrated circuit amplifier, in order to achieve ideal measurement results.
In addition to the selection of good performance of the hard equipment, but also must use reasonable control algorithms and control software in order to further improve the accuracy of the dosage.
3 control algorithms and software design ideas
Loss-in-weight scale dosage control is a non-continuous process, it is required for the production of a variety of materials to a given ratio of batch preparation control algorithms are relatively simple, to complete a batch of material preparation can be by the material, static measurement, coarse flow of materials, fine flow of materials, static measurement and static
Compensation and other processes. In the batching, assuming that the demand for a certain material is P, in order to carry out weightlessness measurement, the amount of feeding should be greater than P, set R as the excess amount of feeding, then the amount of feeding should be P + R. At the same time in the feeding, the computer constantly detects the amount of feeding until the amount of feeding for P + R until the end of the process of feeding and enter the process of static measurement, which is designed to eliminate the dynamic measurement error and the hopper inertial jitter caused by measurement interference, so as to obtain a static compensation process. The purpose is to eliminate the dynamic measurement error and the measurement interference caused by the inertia jitter of the hopper, so as to obtain an accurate feeding measurement value. The discharging process is an important factor affecting the dosage accuracy. If the flow rate of discharging is too large, it is easy to cause large error: if the flow rate is too small, although it will meet the requirement of accuracy, it will increase the dosage time, which is not allowed by the production. In order to solve this contradiction, the combination of coarse and fine flow should be used in the feeding mode, coarse flow to improve the dosage speed of fine flow to ensure accuracy.
Assuming a sampling period of 20ms set the coarse flow for each sampling period x AD code (take 23) fine flow for each sampling period y AD code (y generally take 0.2). The underflow is set to P-3X to ensure that the amount of coarse flow underflow does not exceed the given dosage amount P. Due to the existence of control errors, the coarse flow underflow process is stopped by static measurement, the actual underflow measured value of PmP-Pm is approximately equal to 3x, with P-Pm-1 as the fine flow underfeeding. After the end of the fine-stream discharging, after static detection, if the discharging quantity is less than P, then the fine-stream flow is used to carry out the fine-stream compensation for 1/adoption cycle, in order to improve the accuracy of the final dosage quantity. By analyzing the practice also proved that its control accuracy can
reach within one AD code. In the loading and unloading process, the computer has been constantly sampling the weight of the material, and once a certain weight value is found that requires a change in the electric vibration mode of operation, it immediately sends out a command to the electric vibration machine to turn on or off the electric vibration machine. Therefore, it can be seen that the shorter the sampling period, the more timely control of the vibration machine, and thus the higher the control accuracy. But the sampling period can not be arbitrarily short, because in order to overcome the random measurement error. Each material for each sample are a number of times AD conversion, in order to carry out digital filtering, and AD conversion is very time-consuming. Therefore, no more than 16 kinds of materials for the mixer sampling time to take 10-25ms is more appropriate
4 using multiple AD conversion coefficients for material detection
If there is no precision measurement, there is no way to talk about the control accuracy. And improve the measurement accuracy, on the one hand, from the hardware manpower. First of all, we must choose the excellent performance and stability of the measuring instrument, the requirements of the detection instrument should be high precision, linearity should be good. But any measuring instrument has a certain degree of nonlinearity, there is a certain degree of nonlinear error. But now the output of the detection instrument for AD conversion, often select a single AD conversion coefficient for data processing. In fact, the detection instrument is treated as an ideal linear instrument, which inevitably brings nonlinear error.
If the measurement range in the weighing instrument is divided into a number of intervals, in different intervals within the selection of different AD conversion coefficients, due to the local range of the interval of the linearity is necessarily better than the linearity of the entire measurement range, so in the different intervals of the selection of different AD conversion coefficients will make the measurement results more closely approximate the true value, so that you can overcome the nonlinear error to a considerable extent and greatly increase the accuracy of the measurement of the weightlessness. In the dosage, only the measurement accuracy of the feeding quantity P+R and the remaining quantity R in the hopper after discharging is the decisive factor affecting the dosage accuracy, while the numerical change from R to P+R is only used as the reference value for the control of the electric vibration machine, and does not have any influence on the dosage quantity. Therefore, if the detection system is calibrated at points P+R and R, the AD conversion coefficients of weight loss at these two points can be obtained. In the AD conversion calculation in the point close to P + R choose P + R point AD conversion coefficient, otherwise take R point AD conversion coefficient value. In addition, in the up and down material breaking point is static detection, this undoubtedly maximizes the two points sufficiently close to the interval of the measurement and calculation accuracy.