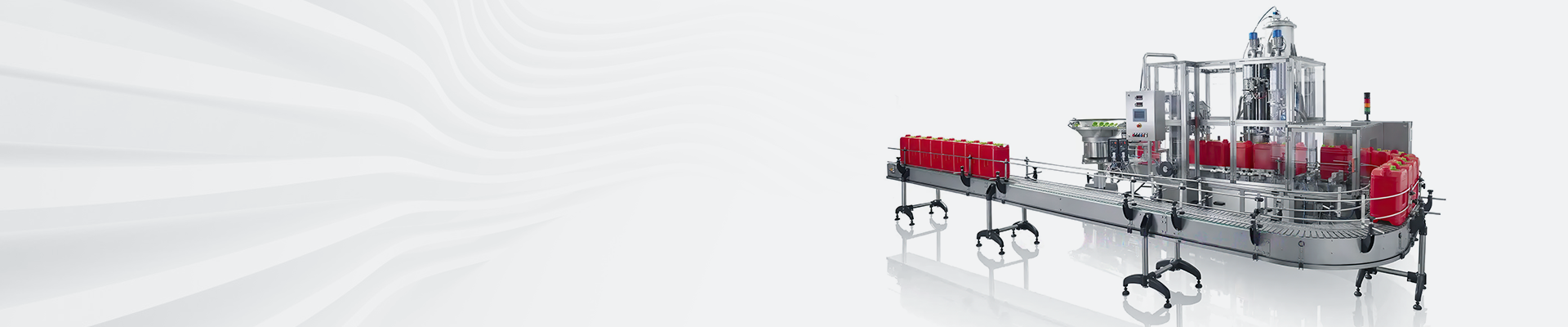
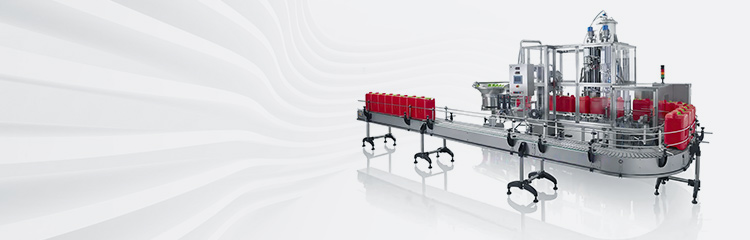

Summary:The batching system is based on PROFIBUS-DP field bus control as the core of metering production. It performs a reasonable proportion of various materials and realizes automatic batching through an open, digital, two-way transmission, and multi-branch communication network that connects field equipment and reactors. control.
Dosing mixing tank is the core of metering production, but also an important part of the entire paint production process, a reasonable proportion of various materials, is the key to improve the mixture of materials. The original dosage workshop of mixing kettle adopts distributed process metering and dosage system based on PROFIBUS-DP fieldbus to realize microcomputer automatic dosage. PROFIBUS fieldbus is an open, digital, bi-directional transmission, multi-branch structure communication network applied in production site to connect the intelligent on-site equipments and the reactor kettle weighing and dosage and realize the fast communication between automatic dosage system. It can realize the fast communication between automatic batching system.
As a result of the technical reform project, the new paint tanks should also use this batching plant, so that the load increases, from the outdoor raw material silo, pipeline spiral to the indoor frequency converter, raw material tank metering and batching are not able to meet the requirements, and so based on the fieldbus control based on the expansion of its transformation, upgrading, and the establishment of a high-performance reaction kettle automatic dosage system.
1 dosage composition principle
Batching workshop existing 9 pipe spiral (1 brace a 9 brace), 1 brace, 3 brace, 7 brace, 8 brace, 9 brace rotary motor rated power 2.2kW, rated current 5.0A, 2 brace, 4 brace, 5 brace, 6 brace motor rated power 3.0kW, rated current 6.8A, the motor drives the pipe rotation, the layer of material is uniform, the faster the motor rotation, the greater the flow of material, the higher the ratio, and vice versa, the higher the ratio, the higher the ratio, the higher the ratio, the higher the ratio, the higher the ratio, the higher the ratio, the higher the ratio, the higher the ratio, the higher the ratio, the higher the ratio, the higher the ratio, the higher the ratio, the higher the ratio, the higher the ratio, the higher the ratio, the higher the ratio. The faster the motor rotates, the higher the material flow rate and the higher the proportion, on the contrary, the slower the motor rotates, the smaller the material flow rate and the lower the proportion. Each motor is driven by a frequency converter, and the frequency of the frequency converter is controlled by PLC through PROFIBUS-DP field bus. PLC calculates the actual flow rate of each material according to the load and instantaneous flow rate of each material collected automatically and compares it with the set value to complete the closed-loop adjustment.
According to the field experience, the spiral only retains the weighing primary weighing instrument, canceling the secondary indicator, which is converted by PLC; canceling the speed sensor, which is converted by the frequency converter. The signal of weighing resistance bridge is input into PLC template after isolation, amplification and linearization. This expansion and remodeling increased 2 propped, 3 propped, 9 propped complete sets of screw and frequency converter. Among them, 9 props for two-way rotation, two-way measurement, two-way frequency conversion speed control, two-way control.
2 dosage composition
This set of batching system adopts distributed structure, which is composed of batching control level and process monitoring level. The cost-effective SIEMENSPLC is chosen as the main control station, which is connected to the distributed on-site batching system through PROFIBUS-DP field bus to form a batching machine, and the process monitoring and operating station adopts configuration software to monitor the batching system in real time.
The control level of the automatic batching system includes the main control station, 1 brace and 9 brace screw inverters, and the mocking station. Among them, the mocking station, 2-, 3- and 9-props inverters are added for this remodeling. According to the process needs, the main control station digital input template selection of 16-channel AC220V, 32-channel DC24V two types of digital output template selection of 32-channel DC24V; low-voltage electrical system selection of reliable performance of the OMRON relay; 7 sets of frequency converters using SIEMENS MMV440, configure PROFIBUS-DP interface board options. DP interface board option. All PLCs and inverters, including the main control station, are directly connected to various devices on site (such as sensors, motors, electrical devices, etc.) to realize the analog signal detection of the 9 pipeline spirals and the inverter control of the motors, and the E'IP.00 station realizes the electrical control of the expanded two even coal and outer coal roller, the 2-support, 3-support and 9-support spirals in physical flow control, especially the 9-support spirals with bidirectional In addition, it realizes the collection and control of signals such as start-stop and interlock of several common pipelines and high-pressure motors.
The process control level (i.e. process monitoring and operating station) is not able to meet the requirement of fast communication after control due to the slow dosage speed in the past, so this renovation has upgraded the whole set of dosage equipment, which consists of a P4 Advantech industrial controller, and Advantech industrial controller carries out the point-to-point communication through the MPI interface between the C5611 communication card and the CPU315. Considering the reliability and the friendliness of the human-machine interface, the industrial controller adopts Windows software platform, and the upper computer adopts Fameview configuration software, which is responsible for monitoring and human-machine dialogue. The dosage system of the color mixing kettle of the suspending agent has the functions of monitoring the process, alarm recording, real-time trend, historical trend, report printing, etc. The operator inputs the formula of the dosage, modifies the formula, consults the process parameters, and monitors the production process through the monitoring operation. The operator can input batching formula, modify the formula, check the process parameters, and monitor the production process through the monitoring operation. Programming application software adopts STEPV5.2 to complete hardware configuration and lower computer software programming to realize all the process control, data acquisition, automatic adjustment, accident handling and alarm work.
3 dosage software realization
Because the original design software is not standardized enough, sometimes when the peripheral system is replaced, the model parameters are inconvenient to input, and the expansion and transformation of the software changes are relatively large, so the lower computer monitoring software complete set of re-development, the internal parameters, variables are unified, the interface is clear, and the design of the software is standardized, open and easy to expand the entire dosage and functional upgrades.
The focus of this set of software design is pipeline spiral control, that is, according to the dynamic weighing module of the instantaneous weight, measurement section, pipe speed (proportional to the motor speed), gravity coefficient and other parameters to calculate the instantaneous flow, and monitoring station set flow compared with the use of SIEMENS programming software STEF7 comes with the PID algorithm module (FB41) operation, calculated motor speed (that is, the value of the frequency converter output frequency, the range of 0.0 to 0.0). frequency converter output frequency value, range 050Hz), real-time tracking, closed-loop regulation. When each spiral starts to start and enters into regulation, the instantaneous value of the inverter is changed from the maximum value of 50Hz until the flow setting is satisfied. In the process of operation, sometimes to change the set flow rate value, the zero point of a spiral, coefficient, then need to recalculate, adjust.
4 dosage characteristics
Based on PROFIBUs-DP fieldbus communication network after the expansion and transformation of the mixing and dosing, the dosage tank metering and dosage functions are complete, and the automatic control of starting, stopping, interlocking protection, weighing and adjusting of a number of pipelines, spiral motors and drums has been realized.
The batching system mainly has the following functions:
1) It has two working modes: manual and automatic. Manually, each pipeline and spiral can be started, stopped, accelerated and decelerated by the operator according to the process requirements, and can also be electrically interlocked. Automatically, the upper computer of the system sends the given value according to the total flow and the proportion of each material, and starts, accelerates and decelerates the spiral motor automatically, and all the pipelines and drums can be opened and stopped by the logic interlocking control.
2) When the ratio changes, the internal PID regulator runs, the frequency converter changes steadily, and the speed regulation is smooth.
3) Cancel the spiral weight indicator and speed sensor, the mV signal of the load cell is processed and directly entered into PLC, which has the functions of signal calibration zero, automatic skin calibration and automatic adjustment system.
4) PROFIBUS-DP fieldbus has high-speed communication capability, which can quickly collect and transmit the field data and realize the signal without delay and distortion, and has powerful expansion capability.
5) In order to prevent clogging, all screw motors will be stopped immediately when the main collector is shut down; when the main collector is normally turned on, all the silos of the last operation (selected) will be automatically turned on with a delay in accordance with the batching system.
6) It has the totalization of consumed materials, all the animation of dosage action shows realistically, all the systems have reliable interlocking, high security, simple and convenient operation.
This set of metering and batching system has openness, standardization, interconnectivity, interoperability and rich hardware and software resources, so that the monitoring and operation station can be used as a monitoring station, displaying the monitoring screen, but also as an engineer's station, at any time, to call out the ladder logic diagrams, debugging programs, and find faults, convenient and fast.
5Effect
The expansion and transformation make full use of the openness of the fieldbus, in the dosage maintenance gap in the system docking and debugging, without affecting the normal production, after the transformation of the measurement of the dosage is more reasonable and standardized. After operation proves: PROFIBUS-DP fieldbus batching in hardware is reliable, anti-interference ability is strong, advanced technology, realize the mixing batching production process full automation. Adopting PROFIBUS-DP bus control realizes internal PID regulation and smooth speed regulation of frequency converter, which plays an important role of protection for the production of batching. PROFIBUS-DP reduces a lot of hard wiring, which makes the metering and batching simple, and reduces the failure rate and improves the batching as compared with the relay logic control. Compared with relay logic control, it reduces the failure rate and improves the dosage reliability and dosage accuracy, and the dosage control error of the system is reduced from the original 10% to about 1.5%-2%, which provides sufficient guarantee for the mixing of stable and high yield and improvement of the quality of mixed ore.