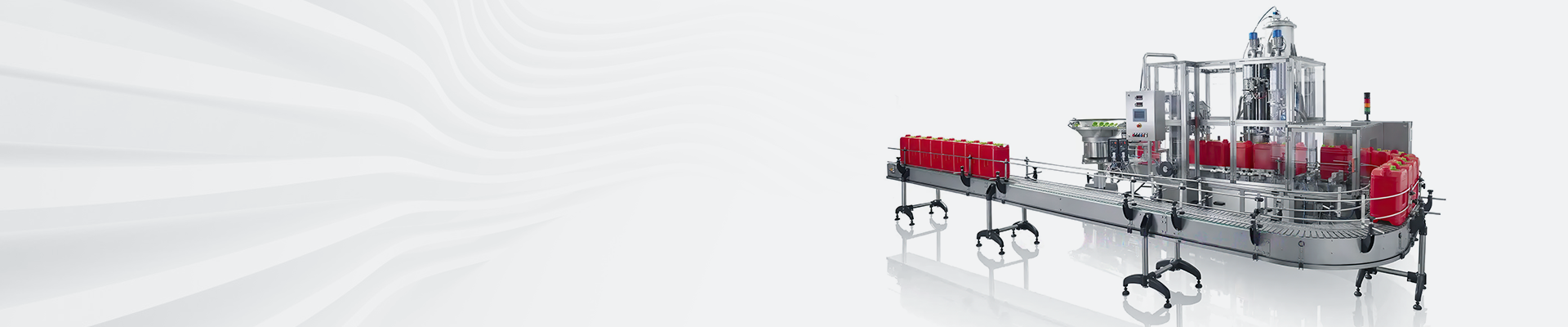
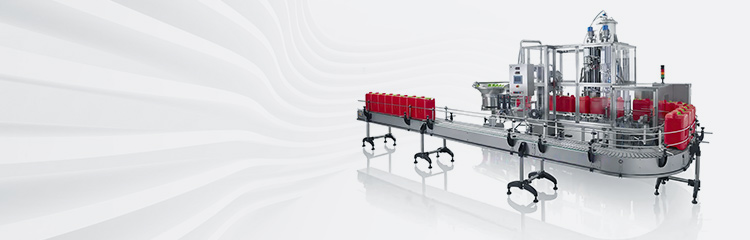
摘要:配料系统基于PROFIBUS—DP现场总线控制为计量生产的核心,对各种物料进行合理的配比,连接现场设备和反应釜的开放式、数字式、双向传输、多分支结构的通信网络实现自动配料控制。
前言
配料混合罐是计量生产的核心,是整个涂料生产过程中的重要环节。各种材料的合理配比是改善混合材料的关键。混合釜原配料车间采用基于PROFIBUS-DP现场总线的分布式过程计量配料系统,实现微机自动配料。PROFIBUS现场总线是应用于生产现场连接智能现场设备和反应釜称重配料的开放式、数字化、双向传输、多支路的通信网络,可实现自动配料系统之间的快速通信。
由于技改项目,新建的油漆罐还需要配料车间,增加了负荷,室外原料仓库和管道螺旋至室内变频器和原料罐的计量配料无法满足要求。因此,在现场总线控制的基础上,对其进行了扩展和升级,建立了高性能的反应罐自动配料系统。
1配料组成原理
配料车间有9根螺旋管(1根支架和9根螺旋)。1支撑、3支撑、7支撑、8支撑和9支撑的旋转电机的额定功率和额定电流分别为2.2kW和5.0A,2支撑、4支撑、5支撑和6支撑的电机的额定功率和额定电流分别为3.0kW和6.8A。电机带动管道旋转,料层均匀。电机旋转越快,材料流量越大。每台电机由一台变频器驱动,变频器的频率由PLC通过PROFIBUS-DP现场总线控制。PLC根据自动采集的负载和瞬时流量计算出每种物料的实际流量,并与设定值进行比较,完成闭环调节。
根据现场经验,螺杆只保留称重仪表一次称重,取消二次称重显示,由PLC转换;取消速度传感器,通过变频进行转换。称重电阻电桥的信号经隔离、放大、线性化后输入PLC模板。在此次产能扩建中,增加了2支撑、3支撑和9支撑的成套螺杆和变频器。其中9项支持为双向旋转、双向计量、双向变频调速、双向控制。2配料构成
该配料系统采用分布式结构,由配料控制级和过程监控级组成。选用性价比较高的SIEMENSPLC作为主控站,通过PROFIBUS-DP现场总线与分布式现场配料系统相连,组成加药机,过程监控操作站利用组态软件对配料系统进行实时监控。
自动配料系统控制级包括主控制站、1撑一9撑螺旋变频器、嘲站。其中嘲站、2撑、3撑、9撑变频器为这次改造所增加。根据工艺需要,主控制站数字量输入模板选用16路AC220V,32路DC24V两种类型,数字量输出模板选用32路DC24V;低压电器系统选用性能可靠的OMRON继电器;7台变频器采用SIEMENS公司的MMV440,配置PROFIBUS—DP接口板选件。包括主控制站在内的所有PLC及变频器直接与现场的各类装置(如传感器、电动机、电气装置等)相连,实现9条管道螺旋的模拟信号检测及电动机的变频控制,E'IP.00站实现对扩容后的两条匀煤和外滚煤滚筒的电气控制、2撑、3撑、9撑螺旋实物流量控制,特别是9撑螺旋的双向计量与双向变频控制,另外,还实现了多条共用管道和高压电机的启停、联锁等信号的采集和控制。
过程控制级(即过程监控操作站)因以前的配料速度慢,不能满足控制后的快速通讯要求,故这次改造进行了整套配料设备升级,由一台P4研华工控机组成,研华工控制机通过C5611通讯卡与CPU315的MPI接口进行点到点的通讯。考虑可靠性与人机界面的友好性,工控机采用Windows软件平台,上位机采用Fameview组态软件,负责监控和人机对话,助悬剂调色釜配料系统具有工艺流程监控、报警记录、实时趋势、历史趋势、报表打印等功能,操作人员通过监控操作输入配料配方、修改配方、查阅工艺参数、监控生产过程。编程应用软件采用STEPV5.2,完成硬件组态及下位机软件编程,实现所有的过程控制、数据采集、自动调节、事故处理及报警等工作。
3配料软件实现
由于原设计软件不够规范,有时外围系统更换时,型号参数不便输入,并且这次扩容改造时软件改动量比较大,所以将下位机监控软件全套重新进行开发,内部参数、变量统一,接口清晰,设计的软件规范、开放易于整个配料的扩充及功能升级。
本套软件设计的重点是管道螺旋控制,即根据动态称量模块的瞬时重量、测量段、管道转速(与电动机转速成比例关系)、重力系数等参数计算出瞬时流量,与监控站设定流量相比较,利用SIEMENS编程软件STEF7自带的PID算法模块(FB41)运算,计算出电动机转速(即变频器输出频率值,范围050Hz),实时跟踪,进行闭环调节。每台螺旋开始启动并进入调节时,变频器瞬时值均从最大值50Hz开始变化,直至满足流量设定。在运行的过程中,有时要改变设定流量值、某条螺旋的零点、系数,那么需要重新计算、调节。
4配料特点
基于PROFIBUs-DP现场总线通讯网络的混合配料扩容改造后,配料罐计量配料功能完备,实现了若干条管道、螺旋电机、滚筒的起、停、联锁保护、称量及调节的自动控制。
配料系统主要有以下功能:
1)具有手动和自动两种工作方式。手动时,每条管道、螺旋由操作员根据工艺要求来启、停、加速、减速,也可电气联锁。自动时系统上位机根据总流量、每种物料配比发送给定值,自动启动、加速、减速螺旋电机,所有管道、滚筒开、停均由逻辑联锁控制实现。
2)当配比改变时,内部PID调节器运行,变频器频率乎稳改变,调速平滑。
3)取消螺旋称重显示器和测速传感器,称重传感器的mV信号经处理后直接进入PLC,具有信号校零、自动校皮、自动调整系统的功能。
4)PROFIBUS—DP现场总线具有高速通讯能力,能快速将现场数据采集并传送,做到信号的不迟滞、不失真,并具有强大的扩展能力。
5)为防止堵塞,集料主管道停机的同时,立即停止所有螺旋电机;集料主管道正常开机时,按照配料制度,自动依次延时开启上次运行(选中)的所有料仓。
6)具有消耗料累计,配料动作全部动画显示逼真,所有系统之间都有可靠联锁,安全性高,操作简单方便。
本套计量配料系统具有开放性、规范性、互连性、互操作性及丰富的硬件和软件资源,使监控操作站既可作监控站用,显示监视画面,又可作工程师站,随时调出梯形逻辑图,调试程序、查找故障,方便而快捷。
5效果
本次扩容改造充分利用现场总线的开放性,在配料检修的间隙进行系统对接与调试,未影响正常生产,改造后计量配料更合理、规范。经过运行证明:PROFIBUS—DP现场总线配料在硬件上可靠,抗干扰能力强,技术先进,实现了混合配料生产过程全自动化。采用PROFIBUS—DP总线控制,实现了内部PID调节,变频器调速平滑,对生产配料起到了重要保护作用。PROFIBUS—DP减少了许多硬接线,从而使计量配料简单化,与继电逻辑控制相比,降低了故障率,提高了配料可靠性,配料准确,系统配料控制误差由原10%减少到1.5%-2%左右,为混合稳夺高产,提高混合矿质量提供了充分保证。