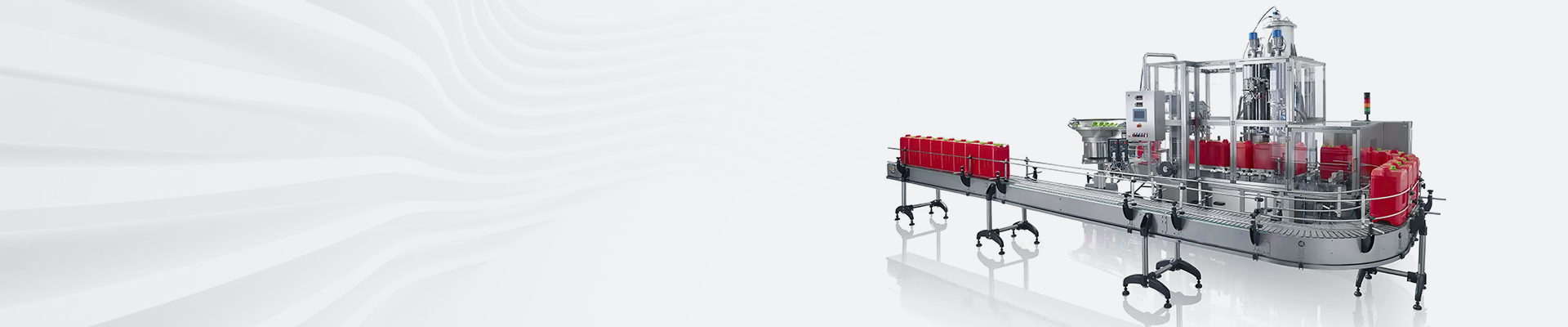
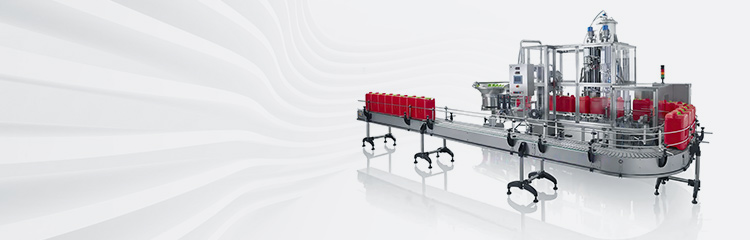

Summary:OMRON programmable controller in the production of wood-based panels, dosage system with a programmable controller as the control core, with level sensors and actuators for the volumetric method of glue dispensing, to achieve automatic glue dispensing control, to stop when the corresponding set value. It is controlled by a three-phase frequency conversion motor driving a water pump, and the feed of hardener, water and ammonia is controlled by a cut-off solenoid valve, and the control system has to provide corresponding electric power driving and controlling power for the motor and solenoid valve. All kinds of raw materials are set up a measuring cylinder, measuring cylinder is equipped with a probe to detect the liquid level. There are two liquid level probes in each of the two glue metering cylinders, one probe is used to set the glue level when dispensing glue in the surface layer, and the other one is used to set the glue level when dispensing glue in the core layer.
1.Preface
The processing of man-made boards mainly includes wood drying, glue dispensing, hot pressing and other processes. Good or bad glue distribution directly affects the quality of wood-based panel, if the raw materials of the various components of the distribution is not reasonable, will lead to a decline in the quality of wood-based panels, resulting in cracking, degumming and other serious product quality problems, which directly affects the economic interests of the wood-based panel factory. With the continuous development of computer technology, a variety of control engineering to automation and intelligent direction, the manufacturers of wood-based panel factory on a variety of raw materials proportioning accuracy put forward higher requirements, which requires the dosage system in the control of higher requirements of automation and intelligence, the traditional rely on the experience of the wood-based panel dispensing can not meet the requirements of the production of this paper describes the use of OMRON PLC, combined with external relays, contactors and other components, and then the use of OMRON PLC. This paper introduces the use of OMRON PLC, combined with external relays, contactors, air switches and sensors to form a volumetric glue dispensing control system.
2. Volume method of automatic glue dispensing system introduction
Volumetric glue dispensing of artificial boards are dispensing raw materials: glue 1, glue 2, curing agent, water, ammonia, paraffin, six raw materials are in liquid state. Due to the different requirements of the surface layer and core layer of artificial board on the proportion of each component, to be configured separately, in the surface layer mixing tank for the surface layer of glue, core layer mixing tank for the core layer of glue. Glue, paraffin feed by three-phase frequency conversion motor driven pump control, curing agent, water, ammonia feed by the cut-off solenoid valve control, feeding system for the motor and solenoid valve must provide the corresponding power drive and control power. All kinds of raw materials are set up a measuring cylinder, measuring cylinder is equipped with a probe to detect the liquid level. Two liquid level probes are set in each of the two glue metering cylinders, one probe is used to set the glue level when dispensing glue on the surface layer, and the other one is used to set the glue level when dispensing glue on the core layer. Paraffin, ammonia, curing agent, water metering brief each set 3 liquid level probe, two of which are used for the surface layer and core layer glue level setting, the other for the maximum allowable level setting.
3. Rubber dispensing system control requirements
(1) The weighing control system can realize automatic control of glue dispensing and manual glue dispensing, and the glue dispensing process can be terminated at any time.
(2) Automatic control function: six metering cylinders feeding at the same time, stop when reaching the corresponding set value; when stop using any one of them, it will not affect the use of the rest of the metering cylinders; when the single metering cylinder does not reach the set value, it can be self-locking and can not be discharged; set up a permissible discharging switch, when the raw material level is in line with the requirements of discharging, the switch will open the discharging automatically; the surface layer/core layer dosage will be controlled by the selector switch of the surface/core layer; set up a start dosage button; set up a start dosage button, which is controlled by the selector switch of the surface/core layer. Set up a button to start dosage, press the button once for dosage.
(3) Manual control function: six measuring briefs can be fed individually, and the corresponding buttons must be pressed continuously when feeding; set the manual discharge switch to control the discharge or not; manual discharge and manual feeding interlock.
(4) Temperature detection and display: the temperature of the wax reaction pot is displayed and a switch signal is given for the temperature to reach the set value.
(5) Alarm function: independent control of subsidiary motors, sound and light alarm when any one of them is overloaded; sound and light alarm when the liquid level exceeds the specified value; discharge solenoid valve will be closed automatically when the liquid level of surface layer and core layer mixing tank is overfull; sound and light alarm when any liquid level of metering cylinder exceeds the highest liquid level.
4.Hardware configuration of glue dispensing system
In the process of volumetric glue dispensing, the input and output points are all switching quantities, the main PLC
Input and output points are switching, the main PLC are: the highest level of mixing tank, glue 1 level, glue 2 level, curing agent level, water level, ammonia level, paraffin level, feed overflow (the highest level), manual state, automatic state, core layer / surface layer selection, start automatic dosage, allowed to discharge, glue 1 manual dosage, glue 2 manual dosage, curing agent manual feed, manual feed, ammonia manual feed, paraffin manual feed, glue 1, no dosage, glue 2 not dosage, glue 2 manual feed, glue 1, glue 2, glue 2, glue 1, glue 1, glue 1, glue 1, glue 1, glue 1, glue 1, glue 1, glue 1, glue 1, glue 1, glue 1, glue 1, glue 1, glue 1, glue 1, glue 1 No dosage, no dosage of glue 2, no dosage of curing agent, no dosage of water, no dosage of ammonia, no dosage of paraffin, total 25 points. The 1st to 8th switching signals come from the converter. The 9th and 10th switching signals come from three switches, and the rest come from buttons.
The main PLC outputs are: glue 1 feed (with motor), glue 2 feed (with motor), curing agent feed (with solenoid valve), water feed (with solenoid valve), ammonia feed (with solenoid valve), paraffin feed (with motor), raw material into the surface layer mixing tank (with solenoid valve), raw material into the core layer mixing tank (with solenoid valve), alarm (with indicator alarm), control core layer dosage relay, total 10 output points. Output points. Since this system only involves switching control, we choose OMRON's small machine CPM2A, the number of I / 0 points for 60 points, for the box-type models.
Volume method of glue dispensing system adopts liquid level sensor to detect the liquid level, the resistance of the probe is sent to the liquid level detection circuit to control the opening and closing of the relay.
5. Software design of glue dispensing system
Software designers use the volumetric method, there are many bubbles in the feed, which will make the liquid level converter false action, that is, the actual feed is not yet full, and the liquid level converter detects the foam level rather than the actual level, so we feed the raw materials at the time of the second replenishment, that is, in the first time each feed is full of time delay, in the delay, the foam gradually disappears, which is when the liquid level sensor will be reset again. Delay time for replenishment, replenishment can greatly reduce the foam brought about by the dosage error. After the replenishment is full, each dosage feeder waits for permission to discharge. To allow discharging when discharging and open the timer, the timer time to discharging is completed, the end of the process of rubber dosing, return to the initial state and so on the next operation.
4.Conclusion
This paper introduces the glue dosing control system has been running in a wood-based panel factory, from the practical application of the effect, the system performance is stable, reliable, accurate ratio, reducing the loss of raw materials, has a high economic value.