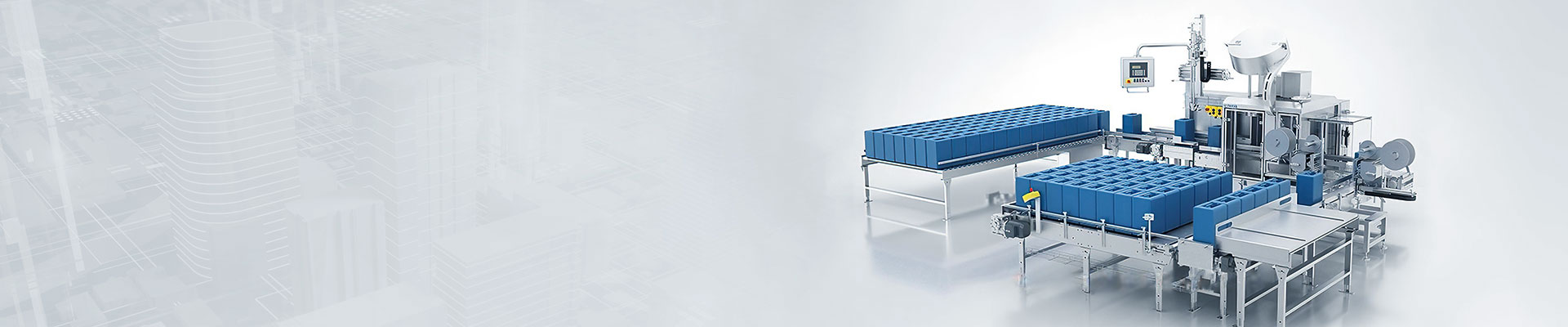
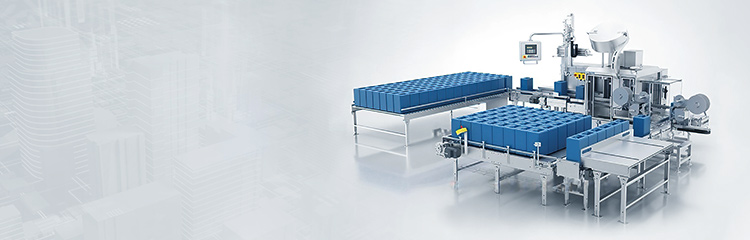
Powder batching system consists of industrial control computer, control software, system power supply and distribution and on-site inspection and control. Computer constitutes the center of control and management, can operate in general industrial environment, the field of primary signal after conversion, amplification into a standard 4 ~ 20mA signal to OPTO22RTUMUX control machine, the weighing module to send industrial control machine to collect data, scale conversion, filtering and processing with the given value sent to the PID function block operation, respectively, sent two ways to regulate the value of the output of the D / A conversion, all the way! Adjust the frequency converter speed of feeding screw to control the feeding quantity, and adjust the opening degree of electric regulating valve to control the flow of materials, so as to achieve the purpose of feeding materials accurately according to the proportion.

The metering and feeding system includes feeding station, feeding device, batching bin, etc. The raw and auxiliary materials are determined according to the process formula, and the raw and auxiliary materials are identified; the main raw and auxiliary materials are put into the storage bin directly through the dust-free feeding station according to the varieties and quantities required by the operation plan, and then moved to the batching station through the elevator, or the raw and auxiliary materials are put into the dust-free feeding station, and then sent to the metering and Weighing system fixed in the batching station through the vacuum conveyor. The feeding system is mainly composed of pneumatic feeding system and pneumatic weighing system.
The feeding system is mainly composed of pneumatic conveying negative pressure suction blower and suction pneumatic conveying equipment device system with unique wear-resistant parts structure, materials, extend the service life of the suction blower, the use of high-pressure fan generated by the negative vacuum pressure as the conveying power, the material will be sucked into the conveying pipeline, the use of material and gas separator will be separated from the material and gas, and then after the separation of the material in the gravity of the role of the material, the material will be discharged into the receiving bin with electric locking air valve. After separation, the material is discharged into the receiving bin by electric locking valve under the action of gravity, and the equipment is operated safely to minimize the occurrence of safety accidents and at the same time to reduce the operating cost of enterprises. The system enables the materials to realize rapid and uniform mixing under the action of airflow, avoiding the abrasion, dust and energy consumption problems brought about by mechanical mixing in traditional mixing equipment.
The automatic mixer introduces airflow into the mixing chamber through compressed air or other gases. The airflow forms a high-speed rotating gas-solid two-phase flow inside the mixing chamber, which generates strong airflow power. Powdery or granular materials to be mixed are put into the mixing chamber through the inlet. The material forms a suspended state under the action of airflow and is rolled into the airflow. The kinetic energy and hydrodynamic effect of the airflow make the material stay suspended in the mixing chamber, and continuously circulate upward, downward or in the airflow. The speed and direction of the airflow can be adjusted to control the suspended state of the material. Under the action of the airflow, collision, friction and diffusion are produced between the materials, thus realizing the homogeneous mixing of the materials. The materials continuously rise, fall and circulate in the airflow, which makes different particles mix with each other and achieves the effect of uniform mixing. The mixed materials form a uniform suspension state in the mixing chamber, and are discharged from the mixing chamber through the discharge port.