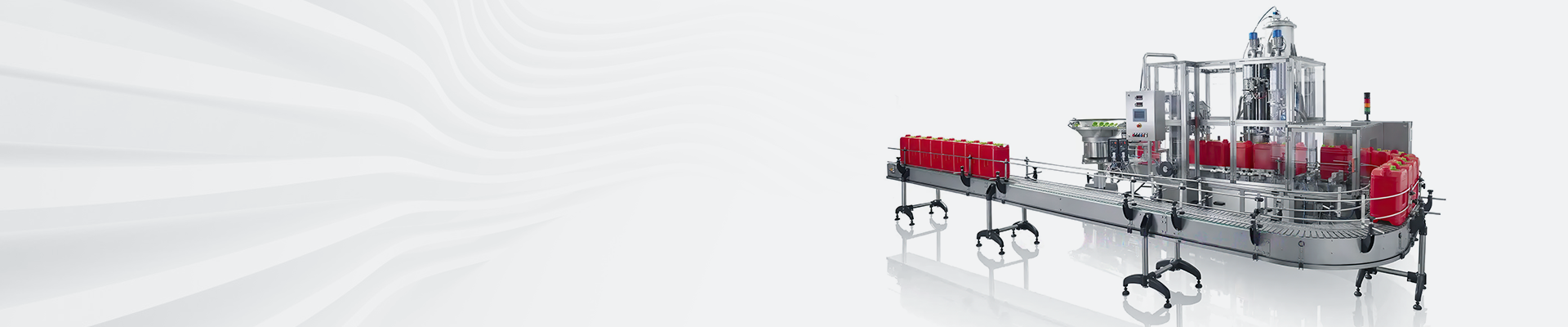
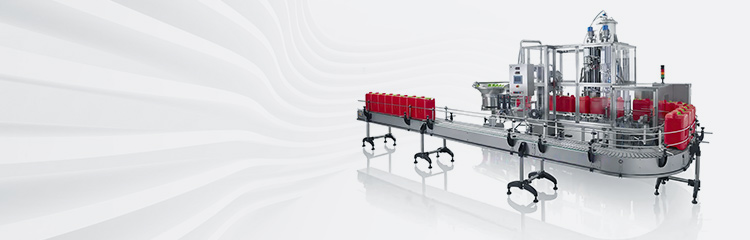

Summary:The weighing batching machine adopts a composite control of weight proportional feedforward control and flowing current paint stirring cascade control. The weight of the controlled batching is then entered into the electronic scale for repeated measurement.
I. Structural design and introduction of weighing and batching machine
Trimethyl has a strong corrosiveness to stainless steel in particular, so the storage and transportation mostly use T course plastic, porcelain, glass containers. With strong volatility, open placed will produce blue smoke, pollution of the atmosphere, while the respiratory system of the members of the harm. Based on these characteristics we have carried out special design and processing in the key parts of the scale body.
1. Selection of storage tank, weighing hopper and connecting pipes. The function of the storage tank is to transport the trimethyl chlorine from the ground to the platform for weighing. As the vacuum feeding method is used without feeding pump, considering the pressure resistance of the container and the characteristics of the material of TMHC, we choose the 2-ton enameled storage tank.
The requirements of weighing hopper and connecting pipe are light weight, convenient connection, easy welding and low price. After comparison, we choose polypropylene pipes. And according to the requirements of the T art of manufacturing a cone weighing hopper.
2. Soft connection mechanism. Weighing hopper inlet, outlet and pipe connection using soft connection. We choose four kinds of materials, which are polyvinyl chloride film, PTFE film, silk lining, poncho cloth. After one month immersion experiment, only PTFE membrane has elasticity, no lumps, hardening, erosion phenomenon. Therefore, PTFE is chosen as the soft connection material.
3. Fixing of weighing module and supporting mechanism of weighing hopper. The 4 hanging beam weighing modules of the dosage scale are connected to the base frame of the scale body by fixing bolts and reinforcing plates. The height of the weighing modules is adjusted by adjusting bolts and adding shims to ensure that the 4 weighing modules are on the same level. The support of the weighing hopper is realized by a pair of steel balls installed between the weighing module and the bowl of the weighing hopper, which can fully guarantee that the weighing hopper is free to move without affecting the measurement.
4. Selection of self-control valve. Based on the characteristics of the material, and the requirements of the pipeline connection method, choose the pneumatic diaphragm switching valve (also known as diaphragm valve) is more appropriate, the diaphragm should be used PDF material diaphragm. This weighing and batching machine adopts Baode company 2 pneumatic diaphragm switching valve, the use of 18 months without internal leakage phenomenon, it is recommended to choose.
5. Auxiliary organizations. Breathing pipeline, because the material is through the automatic flow plus to realize the weighing, which needs to have with the atmosphere connected to the breathing pipeline. Trimethyl has been cool chlorine exposure in the air will absorb water deterioration, based on this reason, we in the breathing pipeline installed in the breathing tank, in the breathing tank with a desiccant silica gel to solve this problem. Cleaning pipeline, weighing and batching machine is easy to cause scale on the inner wall of tank and pipeline after long-term use, if dismantling and cleaning will be very time-consuming and laborious, and re-installation will affect the measuring accuracy of weighing and batching machine. In order to solve this problem, we have installed a cleaning pipeline. On-line cleaning, through the vacuum quickly blow dry the tank and pipeline, without affecting the production schedule.
Second, simple dosing process
Step 1: The operator will pump the Trimethyl Chloride into the storage tank through vacuum loading, and check the equipment before weighing in strict accordance with the operating procedures. Step 2: Input the required dosage quantity through the accumulator (this parameter is seldom changed because the quantity required for each batch is exactly the same). Step 3: Command to start weighing is given via the touch screen. Step 4: Trimethyl has been cool chlorine began to add flow, until the amount added is less than the total amount of 100g rough addition valve closed, fine addition valve continues to add the remaining 100g flow (fine addition time is about 60s). Step 5: Timing by PLC timer for 60s, i.e., the material is left to stand for 60s, and the deviation between the displayed value and the set value is less than 20g, weighing is completed. Step 6: By opening the lower material valve, the material will flow into the buffer tank until the accumulator is zero and then wait for 30s, close the lower material self-control valve. According to the process requirements of the material manually into the process reaction tank can be.
Third, weighing and batching machine control system
The control system of weighing and batching machine is mainly composed of weighing module, weighing totalizer and PLC touch operation screen.
1. Weighing module: automatic weighing and batching machine uses four cantilever beam weighing module, because the cantilever beam sensing is the most used weighing module in the world today, so many manufacturers have a lot of choice. We choose Hodinger cantilever beam weighing module, in the choice of weighing module as long as attention to the matching problem can be.
2. Weighing Instrument: The weighing controller is a dynamic weighing instrument that accepts the weight signal from the weighing module on the quantitative weighing hopper during the dynamic weighing process. In addition to displaying the weight of the material as the basic function, it also has the functions of 4-20MA analog output, weighing total amount setting, residual difference setting, upper and lower limit alarms, communication interface, and multiple relay contacts, etc. All the weighing displays on the market nowadays have the function of displaying the weight of the material, which is the most important function in the weighing process. Now on the market all the weighing display accumulator can meet our process requirements, only METTLER-TOLEDO a company has a variety of instruments to choose from.
3. Selection of PIC: The batching process of weighing and batching machine is controlled by PLC. As we have a set of SIEMENSS-7300 control system in the whole production workshop, in order to save investment and convenient management and maintenance, we just add AIDO and DI points in the original PROFIBUS process station and realize communication with CPU through PROFIBUS protocol to achieve the control function. The central control room is far away from the site, the site does not have the conditions for the installation of the host computer, in order to solve this problem, we installed a SIEMENS touch screen OP37 on the site to complete the operation and human-machine interface work.
4. Configuration of power supply: there are many high-power power equipment in the production site because of the lack of soft start, their start-up on the power grid has a greater impact on the weighing module is easy to burn, so the addition of purified power supply is very necessary.
Fourth, weighing mixer calibration
Weighing mixer belongs to the non-standard equipment, there is no molding of the calibration procedures, we are based on the process characteristics of the production of semi-combined resistance, and according to the calibration procedures of the electronic scales, the development of its own characteristics in line with the calibration procedures, the calibration cycle was selected for 60 days. After 18 months in 10 times of calibration all qualified, fully demonstrated that the dosage weighing to meet the design requirements.
Fifth, the mass flow meter and non-standard automatic weighing batching machine than
Mass flow meter is also used in the material quality measurement. It has its own advantages and disadvantages with non-standard automatic weighing and batching machine.
Advantages: mass flow meter than non-standard automatic batching system is much easier to install, almost do not need any space, as long as directly installed in the pipeline can be. And non-standard automatic batching machine needs a lot of installation space, each about 4M * 4M, more parts and components installed, the installation process is complex, debugging work is also more cumbersome, its installation and debugging cycle is dozens of times the quality of the flowmeter. Mass flowmeter than non-standard automatic weighing and batching machine routine maintenance is much simpler, the mass flowmeter almost do not need routine maintenance, weighing before the inspection content is also relatively small. The non-standard automatic weighing and batching machine daily maintenance content up to dozens of items, such as: regular cleaning of the weighing hopper and pipeline, regular platform for anti-corrosion treatment, regular replacement of the weighing module, regular replacement of the drying meter and so on. Non-standard automatic weighing and batching machine weighing before checking content is also more, the operator to grasp the difficulty.
Disadvantages: the quality of the mass flow meter is mostly produced by foreign companies, such as ABB, E+H, ROSEMOUNT, etc., the price is more expensive and non-standard automatic weighing and batching machine is made by our own technicians using domestic parts and components made of cheaper prices. Mass flow meter can not be adapted to the complexity of the nature of the fluid material similar to the trimethyl has been cool chlorine, even in the mass flow meter of the internal special treatment is very difficult. Mass flow meters are very difficult to calibrate while non-standard automatic weighing and batching machines can be calibrated with standard weights. The maintenance cost of mass flowmeter is very high, once need maintenance must be carried out abroad, time-consuming, laborious and affect the production, and non-standard automatic weighing and batching machine is our own products can be repaired at any time, time-saving, labor-saving does not affect the production, the maintenance cost is very low.
Practice has proved: our self-developed non-standard automatic weighing and batching machine has reached the design requirements. The quality of the product and yield indicators are stable, the incidence of respiratory diseases among employees has plummeted, and the emission of pollutants into the atmosphere is almost zero. In short, the use of non-standard metering batching machine quality, environmental protection and safety of the three benefits are very significant.