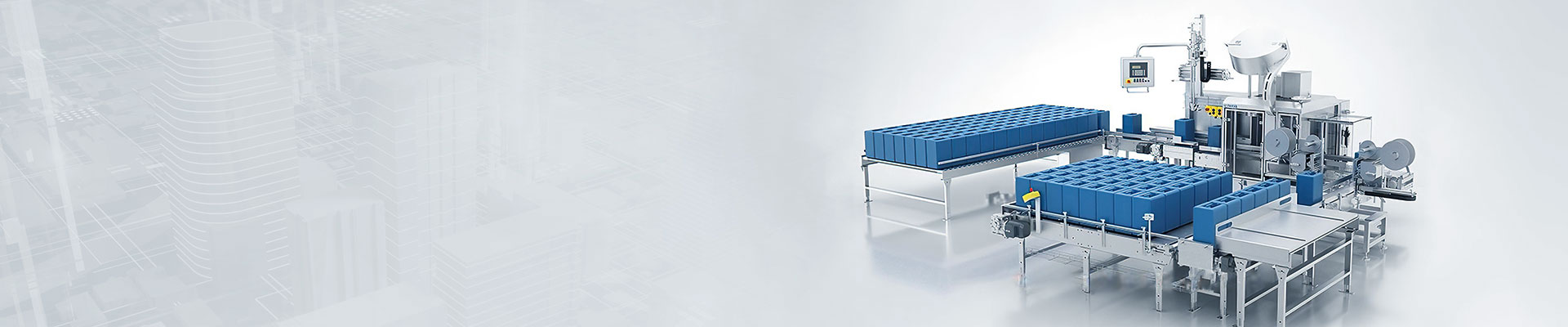
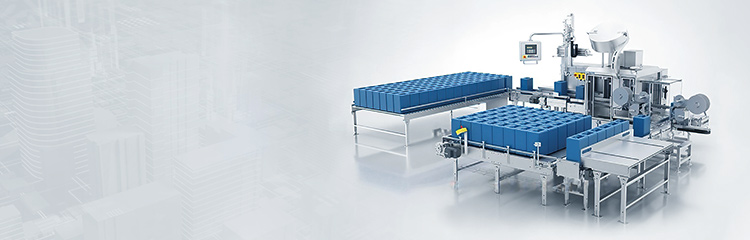
Powder dosage system can be integrated with existing conveyor weighing systems for warehouse and package picking terminals. TLX Advanced Edition helps you to provide dosage control for revenue, optimize inventory control, save costs and improve operational processes. Meanwhile the configuration control, i.e. data acquisition, uses high-end configuration software as a host computer, through which commands are issued to manage the automation equipment and processes. Through digital and analog inputs and outputs to control various types of batching or production processes, the design should follow the principle of easy integration with industrial control and easy expansion of its functions.

The constant flow control of the automatic Batching system adopts PID regulation, and the flow metering control is a combination of metering deviation and frequency conversion speed regulation. According to the control system automatically put all kinds of materials into the Weighing system batching according to the pre-set proportion automatically, the weighing system completes the formula of each material automatically adding by itself. After each batching is completed by the climbing elevator to the mixer, after mixing after turning automatically out of the material or reversing the material out of the climbing elevator to the latter material warehouse, from the storage silo to supply the packaging scales for automatic weighing and packaging for the finished product through the conveyor sewing packages after the finished product into the warehouse.
After the material is scanned by barcode, the storage hopper to be refilled will automatically run to the refilling platform, and after stopping, the automatic door opening mechanism will open the refilling door automatically, and then the material will be transported to the refilling platform through the material transportation belt, and then the operator can unpack the refilling. Before the production starts, the operator puts a plastic bag on the dosing basket, and then sends the formula to be produced through the management computer, and then the system starts to run automatically. At this time, the hopper will automatically run according to the recipe set process to the operating position to stop, the operator to start dosing. Then the dosage basket will run to the operation position in turn, and the operator will repeat the above dosage process. In the process of dosage, the feeding system will judge whether the weighing is qualified or not according to the weighing value set in the computer and the allowable error value, only after the weighing is qualified will the dosage basket be automatically transferred to the next working position. After adding one kind of material according to the process recipe, the system hopper drive device starts to find the next hopper that needs to be dosed and automatically runs it to the operation position, and then operates according to the above mentioned operation. Until all the materials of the process recipe produced are finished, the system will alert the operator to pick up the materials.
The load cell or weighing module collects the weighing data with high accuracy and the weighing instrument provides a complete control solution with integrated weighing display. Storage of compositional parameters. Data acquisition and processing. Loading and unloading. A single instrument can meet the requirements of the user to control the production. The weight signal from the load cell is mainly collected, filtered and processed internally and then transmitted to the PLC, which completes the other control parts.