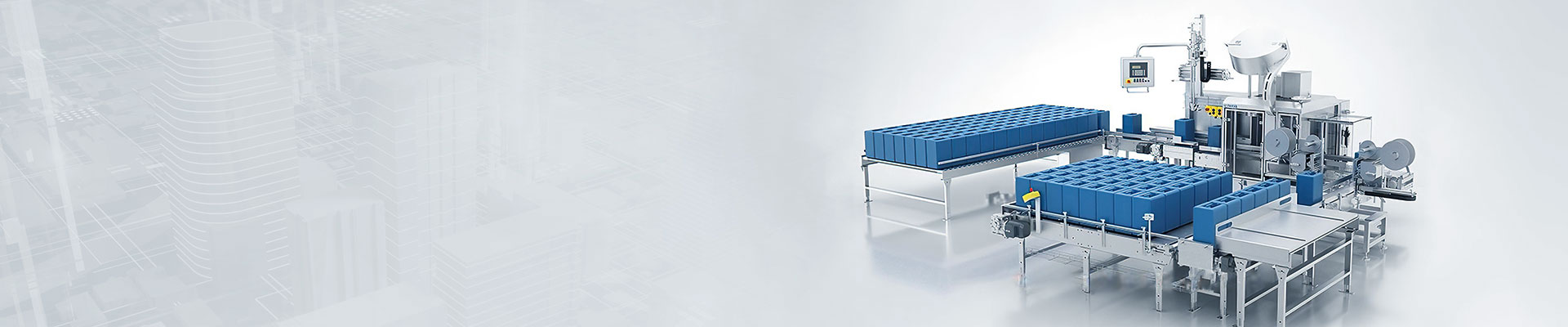
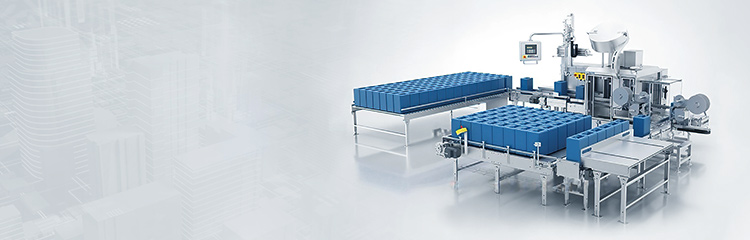
The automatic batching system is developed with the central processing system as the core, each weighing controller controls one weighing scale, which directly controls the batching process and accomplishes the tasks of data collection, processing, storage and display, fault detection and alarm, data communication, etc. The automatic batching system can be used for the real-time display of the batching process and the data communication. Real-time display of the dosage process, data storage and report printing, and directly involved in the control of the feeding and discharging action of each scale. The control system is a multi-channel data acquisition unit, installed in the production site, responsible for the data acquisition and local display of the weighing signals and liquid level signals, and sends the acquired data to the host computer for processing through the serial bus.

The automatic Dosage system is mainly based on weighing instruments, PLC as auxiliary control system, computer human-machine interface to display the proportioning parameters (formula) and monitor and record the real-time data. In automatic control mode, clicking the "Start" button of automatic dosage in the front process screen or the "Start" button of the front control cabinet, the weighing control instrument will open the dosage valve of the dosage scale according to the set recipe. If the system detects that the dosage valve of a scale is not closed, an alarm occurs and the scale enters the pause state. Each scale has an advance according to the dosage scale speed, when the control instrument detects that the material weight reaches the set value, it will subtract the advance and the control instrument will close the dosage valve. The advance amount can be corrected by human or automatically, so that the control instrument can control the dosage scale to reach the set target value every time the dosage accuracy.
Automatic dosage is to put the weighed raw materials into the reaction kettle in a certain order, and at the same time turn on the stirring and heating. This control process is accomplished by temperature control meter and PLC. The temperature control meter controls the upper temperature limit and the heating is controlled by PLC. There are two kinds of control methods for automatic batching: fixed order and programmable. In the fixed-order mode, the order of discharging all kinds of raw materials is fixed and cannot be changed. In programmable mode, the feeding order of all kinds of raw materials can be set artificially on the human-machine interface according to the formula.
Post batching control is based on the flow detection of base powder scale. The control host detects the flow of base powder scale through RS-485 communication and gives the control current of pump and pump according to the ratio value.PLC outputs 4~20mA to control the pump and pump frequency converter to make and set the quantitative flow change of discharging and discharging, and the ratio control is PID regulation control. The flow of auxiliary material scale is collected to the control host through RS-485 communication. The host computer calculates the corresponding tracking flow rate according to the process requirements and passes it to PLC, which gives 4-20mA control current to control the frequency converter of the auxiliary material scale, so that the corresponding dosage flow rate can be controlled in the tracking flow rate in the most range. Pre-mixer, conveying screw machine, distributing screw machine and have on-site start-stop button, through the remote control conversion, connected to the central control room, can be realized through the start-stop button equipment start-stop control, but also can be manipulated after the human-machine interface with the process of the start-stop button, through the control of the PLC to achieve start-stop.
At the beginning of the mixer, if a discharge valve is not closed, or the system does not detect a signal to close the discharge valve, the system will sound an alarm, suspend the dosage scale process of the weighing instrument, and make the running indicator light flash. When the alarm occurs, the automatic discharging will not be carried out, until the fault is eliminated or the cause of the alarm does not affect the discharging, press the reset button and then press the "Discharge" button, then the discharging will be continued.
When automatic discharging starts, the system firstly checks whether each kind of raw material switching is in place, if the switching is not in place or the switching is not consistent, the alarm system will start to alarm and the automatic discharging can not be carried out. Through the check, that can be discharged, press the reset button, and then press the "discharge" button, then start discharging.
If the dosage kettle has been allocated to the raw material pulp is not released, but still to the kettle discharge, generating alarm signals, automatic discharge can not be started. After checking and confirming that the material can be discharged, press the reset button, and then press the "Discharge" button, the automatic discharging will start.
During the process of dosage scale, due to the emergency need to stop the dosage scale, press the self-locking "Dosage Scale Emergency Stop" button, all the feed valves of each scale will be closed, and the dosage scale will be stopped. To restart the scale, turn the "Emergency Stop" button and press the "Start" button to restart the scale. In case of automatic discharging, press the "Discharge Emergency Stop" button, the system will close all discharge valves and stop discharging, mixing and conveying.
The human-machine interface of the master station and the slave station adopts the configuration software of Configuration King and the communication program developed by VB, which consists of pre-matching process, post-matching process, pre-matching formula, parameter setting, history curve and alarm information, etc. The main menu of the system consists of a series of buttons. The main menu of the system consists of a series of buttons. When the mouse rests on the menu buttons, the buttons are raised, and different buttons can be clicked to enter different screens. There are two main types of function screens for operation, one is the display operation screen, i.e. display data (display mode is digital, curve, historical trend, etc.), function soft switches and soft buttons for operators to operate, etc.; the other is the process screen, which displays the process arrangement of the equipment, the process flow and the corresponding test data.
Pre-dispensing process pre-dispensing process flow interface can be displayed in real time before the instantaneous flow of the dosage scale, the proportion of the formula, the dosage scale dosage status, material level and valve closure signals, kettle temperature, motor current and so on. There are other operations on the interface, such as automatic/manual control buttons, single and continuous switching buttons of automatic dosage scale, material buttons and reset buttons.
The interface of the post-dispensing process flow can display the flow rate, accumulated value and weight of the base powder scale and auxiliary material scale in real time, and display the load of the base powder scale, the current of the pre-mixer, the state of the unloader, the instantaneous flow rate of the non-ionic and the instantaneous flow rate, and so on. The interface can also carry out some button control operations, such as running and stopping of the loss-in-weight scale, frequency adjustment, manual and automatic conversion, as well as the setting of the proportion of several materials.
The parameter setting interface displays the instantaneous weight of the former dosage scale, the material level, the use status of the former dosage scale and the dosage sequence of various materials. The interface of former dosage formula is some management of former dosage formula, which can choose any kind of formula that has been set up, or modify the formula that has already been proposed, or newly propose the formula. The report interface can complete the production records of the batching process in the molding workshop, including the pre-batching report and post-batching report of each shift. Pre-matching report records the weight, time and kettle number of each material, while post-matching report records the amount of positive and negative products produced in each shift, the total amount of positive and negative products produced every day, and you can view the situation of the 3 shifts every day at any time through the time box. The instantaneous weight of the former dosage scale can be viewed from the history curve interface. The alarm interface can display the valve closing and the alarm signals such as discharging timeout, discharging timeout and so on.